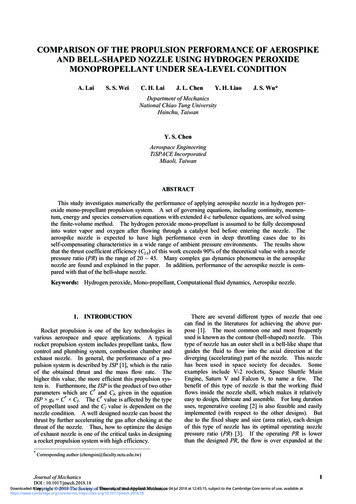
Transcription
COMPARISON OF THE PROPULSION PERFORMANCE OF AEROSPIKEAND BELL-SHAPED NOZZLE USING HYDROGEN PEROXIDEMONOPROPELLANT UNDER SEA-LEVEL CONDITIONA. LaiS. S. WeiC. H. LaiJ. L. ChenY. H. LiaoJ. S. Wu*Department of MechanicsNational Chiao Tung UniversityHsinchu, TaiwanY. S. ChenAerospace EngineeringTiSPACE IncorporatedMiaoli, TaiwanABSTRACTThis study investigates numerically the performance of applying aerospike nozzle in a hydrogen peroxide mono-propellant propulsion system. A set of governing equations, including continuity, momentum, energy and species conservation equations with extended k-ε turbulence equations, are solved usingthe finite-volume method. The hydrogen peroxide mono-propellant is assumed to be fully decomposedinto water vapor and oxygen after flowing through a catalyst bed before entering the nozzle. Theaerospike nozzle is expected to have high performance even in deep throttling cases due to itsself-compensating characteristics in a wide range of ambient pressure environments. The results showthat the thrust coefficient efficiency (Cf,η) of this work exceeds 90% of the theoretical value with a nozzlepressure ratio (PR) in the range of 20 45. Many complex gas dynamics phenomena in the aerospikenozzle are found and explained in the paper. In addition, performance of the aerospike nozzle is compared with that of the bell-shape nozzle.Keywords: Hydrogen peroxide, Mono-propellant, Computational fluid dynamics, Aerospike nozzle.1.INTRODUCTIONRocket propulsion is one of the key technologies invarious aerospace and space applications. A typicalrocket propulsion system includes propellant tanks, flowcontrol and plumbing system, combustion chamber andexhaust nozzle. In general, the performance of a propulsion system is described by ISP [1], which is the ratioof the obtained thrust and the mass flow rate. Thehigher this value, the more efficient this propulsion system is. Furthermore, the ISP is the product of two otherparameters which are C* and Cf, given in the equationISP g0 C* Cf. The C* value is affected by the typeof propellant used and the Cf value is dependent on thenozzle condition. A well designed nozzle can boost thethrust by further accelerating the gas after choking at thethroat of the nozzle. Thus, how to optimize the designof exhaust nozzle is one of the critical tasks in designinga rocket propulsion system with high efficiency.*There are several different types of nozzle that onecan find in the literatures for achieving the above purpose [1]. The most common one and most frequentlyused is known as the contour (bell-shaped) nozzle. Thistype of nozzle has an outer shell in a bell-like shape thatguides the fluid to flow into the axial direction at thediverging (accelerating) part of the nozzle. This nozzlehas been used in space society for decades. Someexamples include V-2 rockets, Space Shuttle MainEngine, Saturn V and Falcon 9, to name a few. Thebenefit of this type of nozzle is that the working fluidflows inside the nozzle shell, which makes it relativelyeasy to design, fabricate and assemble. For long durationuses, regenerative cooling [2] is also feasible and easilyimplemented (with respect to the other designs). Butdue to the fixed shape and size (area ratio), each designof this type of nozzle has its optimal operating nozzlepressure ratio (PR) [3]. If the operating PR is lowerthan the designed PR, the flow is over expanded at theCorresponding author (chongsin@faculty.nctu.edu.tw)Journal of MechanicsDOI : 10.1017/jmech.2018.18Downloaded fromhttps://www.cambridge.org/core.University of MassachusettsAmherst, on 04 Jul 2018 at 12:45:15, subject to the Cambridge Core terms of use, available atCopyright 2018 The Society of Theoreticaland Applied Mechanicshttps://www.cambridge.org/core/terms. https://doi.org/10.1017/jmech.2018.181
nozzle exit, which results in thrust lost and possiblestructural problem [4]; and if the operating PR ishigher than the designed PR, the flow is under expanded at the nozzle exit, which also causes thrust lost.Both aforementioned cases result in thrust lost with amagnitude depending on the difference between theoptimal and operating PR.Another type of nozzle which has been seldom used inthe rocket propulsion system is the aerospike (a.k.a.plugged) nozzle [5]. This type of nozzle has a spike atthe center of the nozzle which guides the fluid to accelerate in the axial direction. The benefit of this type ofnozzle is that the flow will expand to the ambient condition automatically. This leads to optimal expansion andproduce maximal obtainable thrust in a wide range ofambient conditions. Some of the examples are the X-33of Lockheed Martine, VentureStar, and some projects ofEnvironmental Aeroscience Corporation (EAC). Yetthere are several issues that a user must overcome inorder to implement this type of nozzle. These include:1) The hot gas encloses the “spike” during operation,which causes a challenging material problem sincefinding a material with such a small volume at the tipthat can withstand the heat of the exhaust gas is verydifficult; 2) The “spike” has to be held in place from theinterior of the engine which can cause difficulty andcoupling during design, and 3) For long duration operations, it is difficult to implement the regenerative coolingstrategy often used in the bell-shaped nozzle.Despite of the issues stated above, these challengescan be well waived by using mono-propellant hydrogenperoxide, even though its ISP is comparably low. It mayfind some specific application such as attitude controlthruster of rocket and others such as levitating platform[6] using multiple thrusters without thrust vectoringcontrol. For the material melting problem, the exhaustgas temperature of 1,023 K for using, e.g., 90% H2O2, isrelatively low (compared with bi-propellant enginesabout 3,000 K) and metals such as steel can work well inthis condition. The fixture used in holding the “spike”in place can be connected directly to the catalyst bed inthe reacting zone of the engine which makes the implementation much easier. And finally, regenerative coolingis not required in this case since the temperature is not acritical issue at 1,023 K.This work tries to design a mono-propellant aerospikeengine using H2O2. A typical throttling method is bycontrolling the propellant injected to the engine. Thiswill cause the chamber pressure to vary and so do the PR.Therefore, this work numerically investigates the propulsion performance of an aerospike nozzle for a 90%mono-propellant H2O2 engine under the effect of different PRs at sea level. Finally, a comparison of thebell-shaped and aerospike was conducted.performance are not included. For example, the reactingefficiency in the reacting zone of the engine is assumedto be perfect.2.1 Numerical MethodThe numerical tool used in this work is the all-speedUNIC-UNS code [9] that has a capability to solve a setof physical governing equations which include the massconservation Eq. (1), momentum conservations Eq. (2),energy conservation Eq. (3) and species conservation Eq.(4) using pressure-based cell-centered finite volumemethod. To model the turbulence of the described flowfield, the extended turbulence k-ε model Eq. (5, 6) [10] isused. For the equation of state, the HBMS (Hirschfelder,Beuler, McGee and Sutton) model Eq. (7, 8) [11] is usedto describe the relationship between pressure, densityand enthalpy. To analyze the nozzle flow fields, theproblems are solved numerically using the time marchingscheme. UNIC-UNS is a pressure-based multiphysicssolver. Details of the numerical discretization and solutionalgorithm can be found in [9] and are not described here.Only the governing equations are summarized as followsfor reference. ( u j ) 0 t x j ( ui ) ( ui u j ) t x j x j(2) 1 V 2 [()] t 2 x j x j K t u j 2 uk k uj x j C p h xk 3 xk P Qr t (3) t ( i ) ( i u j ) D t x j x j i x i (4) j t k ( k ) ( ku j ) u x t x j x j k j ( ) ( ) ( u j ) t x j x j2. RESEARCH METHODSPr 2 P gi xi K t e ( h) ( hu j ) t x j x j C p h x j This work first validates the current numerical tool bycomparing with previous studies related to aerospikenozzle [7, 8]. Since the main focus of this article is theeffect of the nozzle, other factors that may affect the u x j(1)4j 1H H0 ZcRT c0 t x j 2 C1 C2 C3 k 6 T B rj 2(5)iji 2r(6)(7)i 1 P P 2P 1 (8) T T r d r Z c c r r Tr rJournal of MechanicsDownloaded from https://www.cambridge.org/core. University of Massachusetts Amherst, on 04 Jul 2018 at 12:45:15, subject to the Cambridge Core terms of use, available athttps://www.cambridge.org/core/terms. https://doi.org/10.1017/jmech.2018.18
Table 1 Test conditions used in this study for case validation.Table 2 Boundary conditions used in this study.Boundary typevelocitythermalPRPc (bar)Pa (bar)Inlet66.01.01515.01.0External(ambient)Fixed total pressure to PaFixed ent Pressure Simulation ChamberNon-dimensional Pressure on Cone-shaped Plugged Surface0.50.3(P-Pa)/PcPlugInletLFig. 1LegendSymbol DataSourcePR 6Tomota et al., 1996PR 15Tomota et al., 1996PR 340 Tomota et al., 1996PR 6Present workPR 15Present workPR 340 Present work0.4Cowlx/L -1Fixed total pressure to Pc Room temperature0.20.10x/L 0-0.1Schematic diagram of the experimental setupTomita et al. [7].-0.2-1-0.8-0.6-0.4-0.20x/L2.2Code Validation for Aerospike NozzleTo validate the code for the similar physical problems,we simulated the same PRs in the experimental andnumerical studies of Tomita et al. [7] and Ito et al. [8]with the pressure values shown in Table 1, respectively.Figure 1 illustrates the sketch of the geometry ofaerospike nozzle used by Tomita et al., which consists ofa cowl, a cone-shaped plug that builds the nozzle systemand an external chamber that can simulate the desired“ambient” or external pressure of the nozzle system.The working gas is compressed air. The respectivenumerical boundary settings are described in Table 2.This experiment investigated many cases includingnozzle pressure ratios (PR Pc/Pa) of 6, 15 and 340.Figure 2 shows the comparison of non-dimensionalsurface pressure, (P-Pa)/Pc, along the axial position xfrom the nozzle tip for different PRs between the presentnumerical study and Tomita et al. Note x/L is anon-dimensional parameter defined as the ratio of axialposition from the nozzle tip to the distance between nozzle tip and the throat. The results show that the pressurevariations between the experiments and the current studyare generally in reasonable agreement even though thedeviations are larger for lower PR. For the case of PR340, a smooth decaying curve similar to exponential lineis observed due to pure supersonic expansion from thenozzle throat to the nozzle tip. For the case of PR 6 and15, a negative value of (P-Pa)/Pc is observed which indicates the presence of strong compression (or shock)waves along the surface. Normally, these waves will beaccompanied by oblique shocks which is also observedin this work. The generation of shock waves is extremely dependent on the geometrical condition and willaffect the pressure on the nozzle surface. Due to thereason that other than the major dimensions given in theFig. 2Non-dimensional pressure along the nozzle surface as a function of non-dimensional distancefrom the tip for PR of 6, 15 and 340.reference, we made a reasonable guess on the non-stateddimensions. Therefore, the (P-Pa)/Pc of the case withlower PR slightly deviates from those of Tomita et al.[7].Figure 3 to Fig. 5 show the corresponding Machnumber, pressure and temperature contours for PR of 6,15 and 340, respectively. In the case of PR 6, we cansee a train of compression and expansion waves (3 sets)that interacts throughout the exhaust flow above the nozzlesurface causing the increasing and decreasing of Machnumber, pressure and temperature values Figs. 3(a), (b)and (c). As the flow goes downstream, the intensity ofthe expansion and shock wave decreases, therefore thevariation of these three also decreases. Similar phenomenais also observed in Fig. 4 for the case of PR 15 but thenumber of expansion and compression waves decreasesto one since the PR is larger than the previous case. Afterthe nozzle, a slightly stronger expansion is observed,then followed by a strong compression wave that initiates from x -36 and causes the flow to detached fromthe plug surface. A negative (P-Pa)/Pc is also observedat this point in Fig. 2 (x/L -0.7). This compressionwave is accompanied by a decrease in Mach numberobserved in Fig. 4(a) and slight increase of temperaturein Fig. 4(c). In Fig. 5 for the case of PR 340, a pureexpansion is observed on the nozzle surface and the firstshock initiates near the tip of the nozzle where the flowfrom the other half of the nozzle starts to interact with itscounterpart. Due to the pressure compensation characteristic of the aerospike nozzle, the width of the exhaustJournal of MechanicsDownloaded from https://www.cambridge.org/core. University of Massachusetts Amherst, on 04 Jul 2018 at 12:45:15, subject to the Cambridge Core terms of use, available athttps://www.cambridge.org/core/terms. https://doi.org/10.1017/jmech.2018.183
100M21.510.50R (mm)806040200-50050100150200X (mm)(a)50P (atm)6420.90.70.50.3R (mm)403020100-60-40-200X (mm)(b)20406050Temp (K)290270250230210190170150R (mm)403020100-60-40-200X (mm)(c)204060Fig. 3 (a) Mach number (b) pressure and (c) temperature contour of PR 6 for the case of Tomita et al. [7].100M32.521.510.50R (mm)806040200-50050100150200X (mm)(a)50P (atm)141086420.90.70.50.3R (mm)403020100-60-40-200X (mm)(b)20406050Temp (K)250240230220210200190180170160150R (mm)403020100-60-40-200X (mm)(c)204060Fig. 4 (a) Mach number (b) pressure and (c) temperature contour of PR 15 for the case of Tomita et al. [7].4Journal of MechanicsDownloaded from https://www.cambridge.org/core. University of Massachusetts Amherst, on 04 Jul 2018 at 12:45:15, subject to the Cambridge Core terms of use, available athttps://www.cambridge.org/core/terms. https://doi.org/10.1017/jmech.2018.18
100M876543210R (mm)806040200-50050100150200X (mm)(a)50P (atm)107410.70.40.10.070.040.01R (mm)403020100-60-40-200X (mm)(b)20406050Temp (K)300270240210180150120906030R (mm)403020100-60-40-200X (mm)(c)204060Fig. 5 (a) Mach number (b) pressure and (c) temperature contour of PR 340 for the case of Tomita et al. [7].Sensor Ports(Pressure Transducers, ospikeNozzleNozzleLipFig. 6 Schematic diagram of H2O2 monopropellant engine.plume increases as PR increases. All these Mach number patterns are the same as those of Ito et al. [8].With the above comparisons with previous experimental and numerical studies of aerospike nozzle, weconclude that the numerical tool used in this work issufficient to model the aerospike nozzle.3. RESULTS AND DISCUSSIONThis study proposes an aerospike nozzle that can beattached to an H2O2 catalyst bed for a monopropellantpropulsion system application. A schematic diagram isshown in Fig. 6. This reactor is designed to operate atmaximum chamber pressure (Pc) of 45 atm while theambient pressure (Pa) of 1 atm (PR about 45). In thisstudy, we would like understand the effect of variouschamber pressures on the performance of the aerospikenozzle and compare with the conventional bell-shapednozzle.The computational domain is defined in the regionbehind the catalyst bed where almost all H2O2 hasdecomposed into H2O and O2 (assumed). The domainof interest is modeled using a 2-D axisymmetric methodJournal of MechanicsDownloaded from https://www.cambridge.org/core. University of Massachusetts Amherst, on 04 Jul 2018 at 12:45:15, subject to the Cambridge Core terms of use, available athttps://www.cambridge.org/core/terms. https://doi.org/10.1017/jmech.2018.185
100R (mm)806040Throat (X 0, 43.3 deg.)Contoured Surface2000Fig. 750100X (mm)150200Schematic diagram of the computational domain. Red line: inflow with fixed total pressure and temperatureconditions, purple/brown line: wall with no-slip and adiabatic conditions, orange line: far-field condition, greenline: supersonic outflow condition, blue line: axisymmetric axis.Table 3 Parameters used in the designed aerospike nozzle.NameLip (cowl) diameterLip (throat) widthInlet outer diameterInlet inner diameterThroat angleLip (primary nozzle) lengthThroat areaPrimary nozzle areaInitial nozzle ratioOverall nozzle ratioFar-field diameterOutlet distance from throatwhere the axis of rotation is the centerline of the propulsion system. A schematic diagram of the computationaldomain with rough dimension is shown in Fig. 7 withboundary conditions color coded and related detaileddimensions are summarized in Table 3. The inlet isindicated in red line, which is the interface of the catalystbed and aerospike nozzle. At this boundary, a fixed totalpressure and a total temperature were applied. The speciesflowing into the nozzle was defined as H2O: O2 0.5765:0.4235 wt% (equivalent to 90% of H2O2(aq) solution).The inlet total pressure ranged from 5 to 45 atm for thecase study and the total temperature was 1,023 K, whichis the adiabatic decomposition temperature of this solution.For the nozzle wall (purple lines), no-slip and adiabaticboundary conditions were applied. In this boundary, thesimulated surface pressure applied to the wall was usedto calculate the force and ISP of the propulsion system.The brown lines represent the outer-casing of the propulsionsystem for guiding the hot gas flow. At this boundary,no-slip and adiabatic boundary conditions were applied.Note that the pressure acting on this surface was theeffect of external environment and would result in the6Dimension33.54 (mm)2.93 (mm)61.00 (mm)22.50 (mm)43.3 (deg.)2.00 (mm)289.10 (mm2)504.76 (mm2) 1.746 3.056200 (mm)225 (mm)drag force of the vehicle. This force was not consideredin calculating the performance of the nozzle. The orangeline indicates the far-field boundary condition, along whichthe total pressure is set to 1 atm. The green line is thesupersonic flow outlet. The blue line is the axisymmetriccenterline of the computational domain.3.1Grid TestsTo ensure that the resolution of the grid is sufficient, aseries of grid test was performed. The case chosen forthe grid test was the case with chamber pressure (Pc) of30 atm. Four different mesh resolutions were used withcell numbers of 37 k, 62 k, 125 k and 192 k respectively.Figure 8 shows a typical time history of simulated massflow rate, thrust and ISP history curve with a chamberpressure of 30 atm. The results show that a steady stateof these parameters is reached after 0.002 s. Nevertheless, the external flow field (stream trace) is stable onlyafter 0.006 s (though the performance of the nozzle isindependent of the evolution of the external flow after acertain instant of time). Therefore, all these cases wereJournal of MechanicsDownloaded from https://www.cambridge.org/core. University of Massachusetts Amherst, on 04 Jul 2018 at 12:45:15, subject to the Cambridge Core terms of use, available athttps://www.cambridge.org/core/terms. https://doi.org/10.1017/jmech.2018.18
Aerospike, 90% H2O2 @ 30 atm, 1023 K-1000-12001.21751.11501125-11001.3Mass-Flow (kg/sec)ISP (sec)Mass-Flow (kg/sec)Fx (N)200ISP (sec)-9001.4-1300-1400-1500-1600Fx 020.0030.004Time (sec)0.005-2100Fig. 8 Time history of thrust, mass flow rate and ISP.Aerospike Axi-Sym 2D90% H2O2 @ 30 atm, 1023 K125 k .80.60.40.2R (mm)100500050100150200250X (mm)Fig. 9 Stream trace and Mach number contour of aerospike nozzle at 30 atm with 125 k cells. (PR 30)calculated up to the physical time of 0.006 s for comparison purpose. Figure 9 shows the stream trace withMach number contour for the case of 125 k cells. Wecan observe that there is a clear barrier between theambient air and the exhaust flow. A strong entrainmentof the ambient air is also observed near this barrier.The pressure contour is shown in Fig. 10. In this case,the flow experience a smooth expansion from the throatto the tip of the plug. To make sure that the resolutionis enough, some calculated properties are summarized inTable 4. The error of mass flow rate (ṁ), relative to thecase of 192 k cells, has a maximum value of 1.37% inthe case of 37 k cells and less than 1% for the cases of62 k and 125 k cells. For the integrated propulsiveforce (F), the maximum error occurs in the case of 62 kcells with the value of 0.59%. In these four cases, themaximum error of ISPvac is found for the case of 37 kcells with a value of -1.23%.In addition to the grid test, we also tested whether thedownstream “far field” distance is sufficiently far enoughso that it will not affect the computational results. Inthis study, we used a grid resolution similar to the case of125 k, but extended the “x” boundary 1.5 times and “R”boundary 2.0 times the original setup. Figure 11 andFig. 12 shows the results of Mach number and Pressurecontour using 177 k cells are essentially the same asJournal of MechanicsDownloaded from https://www.cambridge.org/core. University of Massachusetts Amherst, on 04 Jul 2018 at 12:45:15, subject to the Cambridge Core terms of use, available athttps://www.cambridge.org/core/terms. https://doi.org/10.1017/jmech.2018.187
Aerospike Axi-Sym 2D90% H2O2 @ 30 atm, 1023 K125 k cellsP (atm)3020109876543210.90.80.70.60.50.40.30.20.1R (mm)100500050100150200250X (mm)Fig. 10 Pressure contour of aerospike nozzle at 30 atm with 125 k cells. (PR 30)Table 4 Grid test result of aerospike nozzle case of 30 atm chamber pressure. (PR 30)Case* Mass Flow (kg/s)*C (m/s)ṁ (Pc*At)/ṁ(error, %)37 k62 k125 k177 k192 41.370.970.800.79-------* Force (N)F1359.721365.921362.821362.781357.96Cf,vac (-) 43-------(error, %)ISPvac (s) F/ṁ(error, %)* time averaged value from t 0.004 to 0.006error (value (192 k) – value (case))/value(192 k) 100%Aerospike Axi-Sym 2D90% H2O2 @ 30 atm, 1023 K177 k cells 1.210.80.60.40.2R (mm)100500050100150200250X (mm)Fig. 11 Stream trace and Mach number contour of aerospike nozzle at 30 atm with 177 k cells. (PR 30)8Journal of MechanicsDownloaded from https://www.cambridge.org/core. University of Massachusetts Amherst, on 04 Jul 2018 at 12:45:15, subject to the Cambridge Core terms of use, available athttps://www.cambridge.org/core/terms. https://doi.org/10.1017/jmech.2018.18
Aerospike Axi-Sym 2D90% H2O2 @ 30 atm, 1023 K177 k cells (extended)P (atm)3020109876543210.90.80.70.60.50.40.30.20.1R (mm)100500050100150200250X (mm)Fig. 12 Pressure contour of aerospike nozzle at 30 atm with 177 k cells. (PR 30)Table 5 Results of aerospike nozzle at various operating chamber pressures.Case5 atm15 atm20 atm25 atm30 atm35 atm40 atm45 atmPR (-)515202530354045* ṁ (kg/s)0.160.480.640.800.961.121.281.44* F 046.59ISPvac 4ISPground ISPη0.630.870.900.920.930.940.950.96C .76Cf,vac (-)1.651.531.531.531.531.531.531.53Cf,ground (-)1.061.341.401.431.451.461.481.49** time averaged value from t 0.004 to 0.006those of Fig. 9 and Fig. 10. Corresponding derivedpropulsion properties in this case are also included inTable 4. Based on the above numerical experiments,we have decided to use 125 k cells for the all the casespresented next unless otherwise specified, consideringthe computational time and accuracy of the simulation.3.2 Aerospike Nozzle Case StudyNext, we try to investigate the effect of throttling onthe propulsion performance. For this study, differentchamber pressures (Pc) were used to simulate level ofthrottling. The pressures used are 5, 15, 20, 25, 30, 35,40 and 45 atm. The Mach number and pressure contourof PR 15 to 45 are very similar to Fig. 9 and Fig. 10.The calculated propulsion related properties are summarized in Table 5. Due to the choking condition at thethroat of the nozzle, the mass flow rate and corresponding integrated thrust are both proportional to the chamberpressure as expected. The ISPvac was found to be nearlyconstant with a value of 144.5 s, except for an ex-tremely high value for the case of 5 atm, which will beexplained later. The ground ISP (ISPground) was alsoevaluated by subtracting the back pressure from the integrated force as ISPground (F – Pa*Ae)/ṁ, where Ae is thenozzle exit area. Since the back pressure is 1 atm in thecurrent study, the ISPground decreases with decreasingchamber pressure. The ISPground and the correspondingISP efficiency (ISPη ISPground/ISPvac) of the studiedaerospike nozzle ranges from 100 to 138 s and from 63%to 96%, respectively. Thrust coefficient (Cf,vac) is defined by the ratio of overall force obtained by the nozzle(F) and the pressure force at the throat (Pc*At). Undervacuum condition, Cf,vac is only a function of the nozzleconfiguration. In this study, the aerospike nozzle shapewas fixed; therefore, the Cf,vac is a constant value 1.53.But for Cf,ground, the effect of the back pressure shall bededucted. Therefore, Cf,ground is also a function ofchamber pressure. In these cases, the minimum value is1.06 at 5 atm and maximum value is 1.49 at 45 atm.The Mach number and pressure contours of PR 5 areshown in Fig. 13 and Fig. 14 respectively. In this case,Journal of MechanicsDownloaded from https://www.cambridge.org/core. University of Massachusetts Amherst, on 04 Jul 2018 at 12:45:15, subject to the Cambridge Core terms of use, available athttps://www.cambridge.org/core/terms. https://doi.org/10.1017/jmech.2018.189
Aerospike Axi-Sym 2D90% H2O2 @ 5 atm, 1023 K125 k .30.20.1R (mm)100500050100150200250X (mm)Fig. 13 Stream trace and Mach number contour of aerospike nozzle at 5 atm with 125 k cells. (PR 5)Aerospike Axi-Sym 2D90% H2O2 @ 5 atm, 1023 K125 k cellsP (atm)4.543.532.521.510.90.80.70.6R (mm)100500050100150200250X (mm)Fig. 14 Pressure contour of aerospike nozzle at 5 atm with 125 k cells. (PR 5)the PR is too low that compression and oblique shocksoccurs at the plug surface. Therefore, the ISPvac is relatively higher than those of the other cases.3.3Bell-Shaped Nozzle Case StudyTo investigate the difference between aerospike andbell-shaped nozzles, we conducted a similar setup withcontoured bell-shaped nozzle. Table 6 summarizes thedimensions used in designing the bell-shaped nozzle.The bell-shaped nozzle cases also underwent a series ofgrid test and the errors of the results were analyzed.The simulations were set to run for 0.006 s. Since thebell-shaped nozzle has a fixed expansion ratio. Theratio used in this study is chosen to be 4, which is thecase of inviscid supersonic expansion when the chamberpressure is 30 atm. To summarize, there are three caseswith different grid densities and one extended computational domain, namely 39 k, 126 k, 196 k and 174 k10Table 6 Parameters used in the designed bell-shapednozzle.NameThroat diameterExit diameterInlet diameterThroat areaExit areaNozzle (expansion) ratioFar-field diameterOutlet distance from throatDimension19 (mm)38 (mm)28.35 (mm)283.53 (mm2)1134.11 (mm2)4200 (mm)200 (mm)(extended) respectively, which are similar to those ofaerospike case study. Table 7 summarizes the result ofmass flow rate (ṁ), thrust (F), ISPvac, C* and Cf,vac. TheJournal of MechanicsDownloaded from https://www.cambridge.org/core. University of Massachusetts Amherst, on 04 Jul 2018 at 12:45:15, subject to the Cambridge Core terms of use, available athttps://www.cambridge.org/core/terms. https://doi.org/10.1017/jmech.2018.18
Table 7 Grid test result of bell-shaped nozzle case at 30 atm. (PR 30)Case* Mass Flow (kg/s)C* (m/s)(error, %)* Force (N)Cf,vac (-)(error, %)ISPvac (s)(error, %)ṁ (Pc*At)/ṁF F/(Pc*At) F/ṁ39 k0.92934.400.0661260.781.46-0.073139.52-0.14126 k174 k196 139.64139.65139.71-0.046-0.042------* time averaged value from t 0.004 to 0.006error (value (196 k) – value (case))/value(196 k) 100%150Bell Shaped Aerospike Axi-Sym 2D90% H2O2 @ 30 atm, 1023 K126 k .80.60.40.2R (mm)100500050100150200250X (mm)Fig. 15 Stream trace and Mach number contour of bell-shaped nozzle at 30 atm with 126 k cells. (PR 30)150Bell Shaped Axi-Sym 2D90% H2O2 @ 5 atm, 1023 K126 k cellsM2.82.62.42.221.81.61.41.210.80.60.40.2R (mm)100500050100150200250X (mm)Fig. 16 Stream trace and Mach number contour of bell-shaped nozzle at 5 atm with 126 k cells. (PR 5)errors of these cases are all less than 0.15% which is essentially no difference. To minimize controversy forcomparison, the case chosen for further study is 126 kcells one.After the grid test, various chamber pressure conditions, similar to those of aerospike, were investigated.Figure 15 shows the stream traces and Mach numbercontour for the case of 30 atm chamber pressure. Pureexpansion was observed in the divergent part of the nozzle and a clear Mach disk appeared at x 75. As expected, both the mass flow rate and thrust are proportional to the chamber pressure except for the case of 5atm. For the case of 5 atm, the expansion ratio of 4which is too large for this low PR case. Correspondingresults of stream traces and Mach number contour isshown in Fig. 16, in wh
sion performance of an aerospike nozzle for a 90% mono-propellant H2O2 engine under the effect of differ-ent PRs at sea level. Finally, a comparison of the bell-shaped and aerospike was conducted. 2. RESEARCH METHODS This work first validates the current numerical tool by comparing with previous studies related to aerospike nozzle [7, 8].