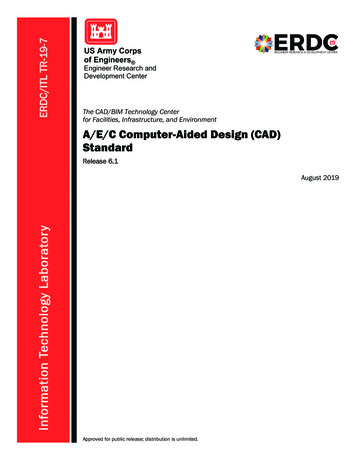
Transcription
ERDC/ITL TR-19-7The CAD/BIM Technology Centerfor Facilities, Infrastructure, and EnvironmentA/E/C Computer-Aided Design (CAD)StandardRelease 6.1Information Technology LaboratoryAugust 2019Approved for public release; distribution is unlimited.
The U.S. Army Engineer Research and Development Center (ERDC) solvesthe nation’s toughest engineering and environmental challenges. ERDC developsinnovative solutions in civil and military engineering, geospatial sciences, waterresources, and environmental sciences for the Army, the Department of Defense,civilian agencies, and our nation’s public good. Find out more at www.erdc.usace.army.mil.To search for other technical reports published by ERDC, visit the ERDC online libraryat http://acwc.sdp.sirsi.net/client/default.
The CAD/BIM Technology Centerfor Facilities, Infrastructure, andEnvironmentA/E/C Computer-Aided Design (CAD)StandardRelease 6.1U.S. Army Engineer Research and Development Center (ERDC)Information Technology Laboratory (ITL)3909 Halls Ferry RoadVicksburg, MS 39180-6199Final ReportApproved for public release; distribution is unlimited.Prepared forUnderHeadquarters, U.S. Army Corps of EngineersWashington, DC 20314-1000Work UnitERDC/ITL TR-19-7August 2019
ERDC/ITL TR-19-7AbstractThe A/E/C Computer-Aided Design (CAD) Standard has been developedby the CAD/Building Information Modeling (BIM) Technology Center forFacilities, Infrastructure, and Environment to eliminate redundant CADstandardization efforts within the Department of Defense (DoD) and theFederal Government. This manual is part of an initiative to develop anonproprietary CAD standard that incorporates existing industry,national, and international standards and to develop data standards thataddress the entire life cycle of facilities within the DoD.The material addressed in the A/E/C CAD Standard include level/layerassignments, electronic file naming, and standard symbology. TheCAD/BIM Center's primary goal is to develop a CAD standard that isgeneric enough to operate under various CAD software packages (such asBentley's MicroStation and Autodesk's AutoCAD) while incorporatingexisting industry standards when possible.DISCLAIMER: The contents of this report are not to be used for advertising, publication, or promotional purposes.Citation of trade names does not constitute an official endorsement or approval of the use of such commercial products.All product names and trademarks cited are the property of their respective owners. The findings of this report are not tobe construed as an official Department of the Army position unless so designated by other authorized documents.DESTROY THIS REPORT WHEN NO LONGER NEEDED. DO NOT RETURN IT TO THE ORIGINATOR.ii
ERDC/ITL TR-19-7ContentsAbstract . iiFigures and Tables . vPreface. viAcronyms and Abbreviations. vii1Introduction . 11.11.21.31.41.51.61.71.81.92Background . 1United States National CAD Standard . 2Objectives . 2Approach . 3Scope . 3Target systems. 3Design applications and other applications . 3Coordination with design agent . 4Additions/revisions. 4Drawing File Organization . 52.1Design area . 52.1.1 Available drawing area . 52.1.2 File accuracy (units) . 52.1.3 International Feet versus Survey Feet . 52.1.4 Origin (global origin) . 62.2Design, drawing, and sheet models . 62.2.1 Model files and sheet files . 72.2.2 Border model files . 82.2.3 Reference files (XREF). 82.2.4 Raster references . 92.32.4Drawing sheet assembly–use of Design Model and Sheet Model (1:1 border sheet) . 9Electronic drawing file naming conventions . 102.4.1 Project code . 102.4.2 Model file naming convention. 112.4.3 Sheet file naming convention . 182.4.4 Adding a drawing sheet. 252.53Coordination between sheet file name and sheet identifier . 25Graphic Concepts . 273.1Presentation graphics . 273.1.1 Line widths . 273.1.2 Line types/styles. 283.1.3 Line color . 283.1.4 Plotting . 293.1.5 Screening. 29iii
ERDC/ITL TR-19-73.24Text . 31Level/Layer Assignments . 324.14.2Level/Layer naming convention . 32Model files . 354.2.1 Level/layer assignment tables . 354.2.1 General levels/layers . 355Standard Symbology . 375.15.2Introduction . 37Symbology resources . 375.2.1 Cells/blocks. 375.2.2 Line styles . 385.36Downloadable resources . 38Conclusion . 39References . 40Appendix A: Model File Level/Layer Assignment Tables . 42Report Documentation Pageiv
ERDC/ITL TR-19-7Figures and TablesFiguresFigure 2-1. Sheet file composition using Design Model and Sheet Model. 10Figure 2-2. Model file naming convention. . 12Figure 2-3. Sheet file naming convention. . 19Figure 2-4. Supplemental drawing designator. . 25Figure 2-5. Typical border sheet title block with sheet identification block. . 26Figure 3-1. Predominant line types/styles. . 28Figure 4-1. Typical levels/layers contained in a sheet file. . 32Figure 4-2. Sheet- and model-specific information. . 33Figure 4-3. Level/layer naming format. . 34Figure 4-4. Model file level/layer assignment table. 35TablesTable 2-1. Discipline designators. . 12Table 2-2. Model file types. . 13Table 2-3. Sheet file discipline designators. . 19Table 2-4. Sheet type designators. . 24Table 3-1. Comparison of line widths. . 27Table 3-2. Basic colors. . 29Table 3-3. Screened colors. . 30Table 4-1. Status (Phase) codes. . 36v
ERDC/ITL TR-19-7PrefaceThis study was conducted for HQ USACE. The technical monitor wasJason Fairchild, Headquarters, U.S. Army Corps of Engineers.The work was performed by the CAD/BIM Technology Center of theSoftware Engineering and Informatics Division (SEID), U.S. ArmyEngineer Research and Development Center, Information TechnologyLaboratory (ERDC-ITL). At the time of publication, Mr. Edward L. Huellwas Chief, CEERD-IS-C; Mr. Ken Pathak was Chief, CEERD-IS; andDr. Robert M. Wallace, was the Technical Director, CEERD-IZ-T. TheDeputy Director of ERDC-ITL was Ms. Patti Duett and the Director of ITLwas Dr. David A. Horner.The CAD/BIM Technology Center acknowledges the support of the USACECAD/BIM Community of Practice (CoP), especially Mr. Jason Fairchild,Headquarters, U.S. Army Corps of Engineers. Special thanks go toMr. Roger Fujan, U.S. Army Engineer District, Walla Walla; Mr. GeraldPiotrowski, U.S. Army Engineer District, Louisville; Mr. Carl Broyles,U.S. Army Engineer District, Kansas City, and Mr. Brian Baker, U.S. ArmyEngineer District, Pittsburgh for serving on a committee that assisted inreviewing/evaluating recommended changes to the standard.COL Ivan P. Beckman was Commander of ERDC, and Dr. David W.Pittman was the Director.vi
ERDC/ITL TR-19-7viiAcronyms and AbbreviationsAcronymMeaningAIAAmerican Institute of ArchitectsBIMBuilding Information ModelingCADComputer-Aided DesignCADDComputer-Aided Design and DraftingCSIConstruction Specifications InstituteDoDDepartment of DefenseERDCEngineer Research and Development CenterFAQFrequently Asked QuestionsfpFloor planftfootGSAGeneral Services AdministrationininchITLInformation Technology LaboratorymmeterNAVFACNaval Facilities Engineering CommandNCSNational CAD StandardNIBSNational Institute of Building SciencesO&Moperations and maintenanceRGBred-green-blueSEIDSoftware Engineering and Informatics DivisionSMACNAUDSSheet Metal and Air Conditioning Contractors’ NationalAssociationUniform Drawing SystemUSACEU.S. Army Corps of EngineersxdExisting/Demolition planxrefReference files2DTwo-dimensional3DThree-dimensional
ERDC/ITL TR-19-71Introduction1.1BackgroundThe A/E/C Computer-Aided Design (CAD) Standard has been developedby the CAD/ Building Information Modeling (BIM) Technology Center(hereafter referred to as the Center) for Facilities, Infrastructure, andEnvironment to eliminate redundant standardization efforts within theDepartment of Defense (DoD) and the Federal Government. This manualis part of an initiative to develop a nonproprietary CAD standard thatincorporates existing industry, national, and international standards andto develop data standards that address the entire life-cycle of facilitieswithin the DoD. This report supersedes A/E/C CAD Standard, Release 6.0(ERDC/ITL TR-12-6).The immediate benefits of CAD standards are the following:Consistent CAD products for customers Uniform requirements for A-E deliverables Sharing of products and expertise. Recognizing such potential benefits, each of the DoD agenciesindependently initiated efforts to establish CAD standards in the late1980s. In 1989, the Air Force Logistics Command released theArchitectural and Engineering Services for Computer-Aided Design andDrafting (CADD) Implementation within Air Force Logistics Command.Headquarters, U.S. Army Corps of Engineers (USACE), in 1990 publishedEngineer Manual 1110-1-1807, Standards Manual for U.S. Army Corps ofEngineers Computer-Aided Design and Drafting (CADD) Systems. In1993, the Naval Facilities Engineering Command (NAVFAC) distributedits Policy and Procedures for Electronic Deliverables of FacilitiesComputer-Aided Design and Drafting (CADD) Systems.To consolidate these efforts into a single standard, the Center was taskedto develop standards for the A/E/C disciplines. This manual presents theCenter’s continuing effort at standardizing CAD requirements for A/E/Cdesign and construction documents.1
ERDC/ITL TR-19-71.2United States National CAD Standard In 1995, the combined resources of the Center, the American Institute ofArchitects (AIA), the Construction Specifications Institute (CSI), theUnited States Coast Guard, the Sheet Metal and Air ConditioningContractors National Association (SMACNA), the General ServicesAdministration (GSA), and the National Institute of Building Sciences(NIBS) Facility Information Council began an effort to develop a singleCAD standard for the United States. Working together, these organizationsagreed to develop an integrated set of documents that collectively wouldrepresent the United States National CAD Standard (NCS).The two main NCS documents referenced within the A/E/C CAD Standardare the following:Uniform Drawing SystemThe Construction Specifications Institute110 South Union Street, Suite 100Alexandria, VA 22314-3351AIA CAD Layer GuidelinesThe American Institute of Architects1735 New York Avenue, NWWashington, DC 20006-5292Each of these documents is available as part of the NCS. Additionalinformation on the NCS, as well as how to purchase a copy, can beobtained fromNational Institute of Building Sciences1090 Vermont Avenue NW, Suite 700Washington, DC 20005-4905http://www.nibs.org1.3ObjectivesThe objective of the A/E/C Standards is to ensure design intent isconsistently, efficiently, and effectively transmitted through theconstruction phase to operations and maintenance (O&M) and back todesign for future work.2
ERDC/ITL TR-19-71.4ApproachThe approach chosen to respond to A/E/C community comments andfeedback entailed reviewing the concerns and recommendations. If thecomment was from a purely personal preference standpoint, it wasdisregarded. If the comment made a valid point, a workaround wasdetermined on how to best resolve the issue while still maintaining theintent of industry standards. A Frequently Asked Questions (FAQ) pagewas established to document the interim solutions. This documentupdates the A/E/C Standards to incorporate those solutions.1.5ScopeThis manual provides guidance and procedures for preparing CADproducts within the DoD. Chapters 2–5 of this manual address topics suchas presentation graphics, level/layer assignments, electronic file naming,and standard symbology. Appendix A contains tables on model filelevel/layer names.1.6Target systemsThis standard does not target any specific CAD system or software, butdoes specifically target CAD workflows. To ensure successful translationsamong CAD applications, certain system-specific characteristics wereconsidered and the standard adjusted accordingly. During the preparationof the standard, several baseline decisions were made:The standard must be applicable to the latest release of commerciallyavailable CAD packages. AutoCAD and MicroStation were chosenbased on their prevalence within the DoD. The standard is based on CAD applications that utilize layer/levelnames and reference files. The standard requires every final plotted drawing sheet to have its ownseparate electronic drawing file. 1.7Design applications and other applicationsNumerous design applications have been developed to run on top of basicCAD engines. These applications can be used by designers to generategraphics inside CAD files. Most notable are design software packages forCIM and BIM.3
ERDC/ITL TR-19-7Document management systems that contain attributes or metadata forindividual files and have such features as title block integration arebecoming standard tools for management of electronic files. Use of thesesystems to store searchable metadata for files is encouraged.1.8Coordination with design agentWith all the complexity and options currently available in the world ofCAD, it becomes important to coordinate fundamental aspects of designwork. The previously mentioned issues of basic platform, designapplications, and document management are three of the issues that canaffect the success of a project and the future usefulness of the finaldocuments. As such, each project should have at its initiation discussionsand agreements on such issues as these. Each software package being usedshould be approved, and a determination made on how many of the supporting electronic files should be provided to the customer as a part of theend product.1.9Additions/revisionsThis Standard is intended to be neither static nor all inclusive, and thus,will be updated as appropriate. Suggestions for improvements are stronglyencouraged so that subsequent updates will reflect the input and needs ofCAD users.Recommendations or suggested additions should be sent to the following:U.S. Army Engineer Research and Development CenterATTN: CEERD-IS-C/CAD/BIM Technology Center3909 Halls Ferry RoadVicksburg, MS 39180-6199or by e-mail to CADBIM@usace.army.mil.4
ERDC/ITL TR-19-72Drawing File Organization2.1Design area2.1.1 Available drawing areaThe two most extensively used CAD applications within the DoD,AutoCAD and MicroStation, both provide for a drawing area with nearlyinfinite range in each positive and negative axis (x,y,z).2.1.2 File accuracy (units)CAD systems allow the designer to work in real-world units. The mostcommon units are feet:inches, survey feet:hundredths (or thousandths) offeet, and meters:millimeters.MicroStation’s approach to file accuracy allows the user to set the workingunits (i.e., real-world units) as the following:Master Units The largest unit that may be referred to when workingin the design file (e.g., feet, meters) Sub Units Subdivisions of Master Units (e.g., inches, millimeters). In AutoCAD, the basic drawing unit for any file is the distance betweentwo fixed Cartesian coordinates. For example, the distance betweencoordinates (1,1,1) and (1,1,2) is one drawing unit. A drawing unit cancorrespond to any measurement (e.g., foot, inch, meter, mile, fathom).AutoCAD users may enter the Units display option to set the desireddrawing units.The Units command of AutoCAD does not have a direct metric systemsetup. For metric designs, the recommended procedure is to choose theDecimal option in the Drawing Units dialog box. This will allow eachdrawing unit to represent decimal meters, millimeters, and so forth, at thediscretion of the user.2.1.3 International Feet versus Survey FeetMany sites have to contend with the initial question as to whether aparticular project is designed using International Feet or Survey Feet. Insome states, it is specified by statute that units of measure for grid5
ERDC/ITL TR-19-7coordinates have to be either International Feet or Survey Feet. The twounits are defined as follows:International Feet: 1 foot (ft) 0.3048000 meters (m) U.S. Survey Feet: 1 ft 0.3048006 m. Looking at this comparison, the difference between the two (0.0000006 m)may seem insignificant; however, ultimately this difference may causecoordinate values to be off by several feet, resulting in inaccurate designfiles. In MicroStation, the units.def file does contain a definition for SurveyFeet (usually stored in c:\ProgramFiles\Bentley\Workspace\System\data), but it is disabled by defaultin some earlier versions. To enable, scroll down the units.def file to thesection English units (based on U.S. Survey Foot) and delete the # infront of #sf,ft, which will allow for the selection of Survey Feet from theWorking Units box the next time MicroStation is started.Note: If a drawing has already been created using International Feet,changing the Master Units to Survey Feet will not automatically scale allelements in the drawing to Survey Feet.2.1.4 Origin (global origin)Positioned within every electronic drawing file is an origin (“global origin”in MicroStation and “origin” in AutoCAD). The origin of a drawing file isimportant because it serves as the point of reference from which all otherelements are located. Origins are typically defined in a drawing file by theCartesian coordinate system of x, y, and z.The benefit of standardizing the location of the origin of a drawing is mostnotable in the use of reference files (see section Reference Files (XREF) inChapter 2). A standardized origin is also helpful when translating filesbetween CAD applications. The recommended global origin for twodimensional (2D) files in both AutoCAD and MicroStation drawings is x 0 and y 0. When three-dimensional (3D) files are used, the z-originshould be set to allow for elevations below 0.2.2Design, drawing, and sheet modelsInside each CAD file can exist Design/Drawing Models (or Model Spacefor AutoCAD users) and Sheet Models (or Layout for AutoCAD users).6
ERDC/ITL TR-19-72.2.1 Model files and sheet filesTwo distinct types of CAD files are addressed in this standard: model filesand sheet files.2.2.1.1 Model filesNote: This model files section contains definitions for both DesignModels and Drawing Models.A model file contains the physical components of a building (e.g., columns,walls, windows, ductwork, piping). Model files are drawn at full scale andtypically represent plans, elevations, sections, etc. Model files can begenerated either by placing graphics, or from BIM modelextractions/views. Model files are used as components in creating plottedsheet files. The information contained within a model file for a disciplinemay be referenced by other disciplines to create the particular model filesor sheet files for that discipline.A model file can be considered a work in progress. For instance, amechanical engineer may reference the architect’s floor plan model file tobegin development of the HVAC ductwork layout model file. Meanwhile,the architect can continue developing the floor plan to meet new requirements. Any changes to the floor plan would be immediately accessible tothe mechanical engineer. The viewing of real-time updates eliminates agreat deal of frustration for other disciplines because it allows foron-the-spot rather than after-the-fact modifications.Design Models are models that are developed, or possibly assembled priorto creation of the Sheet Model (see section 2.3, Drawing Sheet Assembly).Design Models contain graphic information in a model file format. Forexample, it may contain the entire Architectural Floor Plan model file for abuilding. It is this model file that is used as a reference for creatingindividual sheet files. Adding annotation to the Design Model should beavoided (annotation should be placed in the Drawing Model).A Drawing Model is a 2D view/representation with annotation of a 3DDesign Model. Drawing Models include items such as plans, sections,elevations, and details referenced to the Sheet Model.7
ERDC/ITL TR-19-72.2.1.2 Sheet filesA sheet file is synonymous with a plotted CAD drawing file. A sheet file is aselected view or portion of referenced model file(s) within a 1:1 bordersheet. The addition of sheet-specific information (e.g., text, dimensions,symbols) completes the construction of the document. In other words, asheet file is a ready-to-plot CAD file. A design model inside the sheet filecontains the model information assembled as it would be displayed on asheet. This model would have real-world spatial alignment and would beused as the primary model for graphical information to be displayed andpresented in the sheet model.A useful generalization for differentiating between model files and sheetfiles is stated in Module 1 Drawing Set Organization of the UniformDrawing System (UDS) (NIBS 2014): “Model files are always referencedby other files, while sheet files are never referenced by other files.”A Sheet Model shows the presentation of model file graphics as they wouldappear on an individual sheet. This assembly area would containreferenced files, one of which would be the border sheet.2.2.2 Border model filesBorders are model files referenced by all disciplines to create sheet files.This model file contains border linework, the title block, andproject-specific symbols and text. Each discipline shall use the sameborder (for more information on Borders, see the A/E/C GraphicsStandard).2.2.3 Reference files (XREF)Reference files (external references or XREF) enable designers to sharedrawing information electronically, eliminating the need to exchangehard-copy drawings among the design disciplines.With the use of reference files, the structural engineer need not wait forthe architect to complete the architectural floor plans before beginning thestructural framing plan model file.Referencing electronic drawing information makes any changes made laterby the architect apparent to the structural designer. This real-time access8
ERDC/ITL TR-19-7to the work of others ensures accuracy and consistency within a set ofdrawings and helps promote concurrent design efforts. No longer does onediscipline have to wait until another discipline is nearly finished beforethey begin their drawings.Note: Never bind references.Note: Each reference file shall have a unique, logical name/referencedescribing what is being referenced (e.g., Floor 1 Plan, Site Plan – Area A).2.2.4 Raster referencesFor interoperability, the only raster file types allowed to be referenced areTIF, JPG, and PDF. Raster file names shall conform to the model filenaming convention with a model file type of “IG” (e.g., *CIGXXXX.ti
The A/E/C Computer-Aided Design (CAD) Standard has been developed by the CAD/Building Information Modeling (BIM) Technology Center for Facilities, Infrastructure, and Environment to eliminate redundant CAD standardization efforts within the Department of Defense (DoD) and the Federal Gove