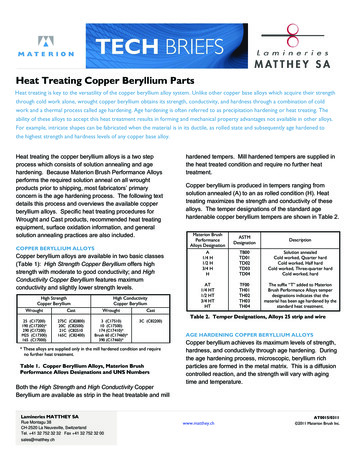
Transcription
Heat Treating Copper Beryllium PartsHeat treating is key to the versatility of the copper beryllium alloy system. Unlike other copper base alloys which acquire their strengththrough cold work alone, wrought copper beryllium obtains its strength, conductivity, and hardness through a combination of coldwork and a thermal process called age hardening. Age hardening is often referred to as precipitation hardening or heat treating. Theability of these alloys to accept this heat treatment results in forming and mechanical property advantages not available in other alloys.For example, intricate shapes can be fabricated when the material is in its ductile, as rolled state and subsequently age hardened tothe highest strength and hardness levels of any copper base alloy.Heat treating the copper beryllium alloys is a two stepprocess which consists of solution annealing and agehardening. Because Materion Brush Performance Alloysperforms the required solution anneal on all wroughtproducts prior to shipping, most fabricators’ primaryconcern is the age hardening process. The following textdetails this process and overviews the available copperberyllium alloys. Specific heat treating procedures forWrought and Cast products, recommended heat treatingequipment, surface oxidation information, and generalsolution annealing practices are also included.COPPER BERYLLIUM ALLOYSCopper beryllium alloys are available in two basic classes(Table 1): High Strength Copper Beryllium offers highstrength with moderate to good conductivity; and HighConductivity Copper Beryllium features maximumconductivity and slightly lower strength levels.High StrengthCopper BerylliumWroughtCast25 (C17200)190 (C17200)*290 (C17200)M25 (C17300)165 00)High ConductivityCopper BerylliumWroughtCast3 (C17510)10 (C17500)174 (C17410)*Brush 60 (C17460)*390 (C17460)*3C (C82200)* These alloys are supplied only in the mill hardened condition and requireno further heat treatment.Table 1. Copper Beryllium Alloys, Materion BrushPerformance Alloys Designations and UNS NumbersBoth the High Strength and High Conductivity CopperBeryllium are available as strip in the heat treatable and millhardened tempers. Mill hardened tempers are supplied inthe heat treated condition and require no further heattreatment.Copper beryllium is produced in tempers ranging fromsolution annealed (A) to an as rolled condition (H). Heattreating maximizes the strength and conductivity of thesealloys. The temper designations of the standard agehardenable copper beryllium tempers are shown in Table 2.Materion BrushPerformanceAlloys DesignationA1/4 H1/2 H3/4 HHAT1/4 HT1/2 HT3/4 4Solution annealedCold worked, Quarter hardCold worked, Half hardCold worked, Three-quarter hardCold worked, hardTF00TH01TH02TH03TH04The suffix “T” added to MaterionBrush Performance Alloys temperdesignations indicates that thematerial has been age hardened by thestandard heat treatment.Table 2. Temper Designations, Alloys 25 strip and wireAGE HARDENING COPPER BERYLLIUM ALLOYSCopper beryllium achieves its maximum levels of strength,hardness, and conductivity through age hardening. Duringthe age hardening process, microscopic, beryllium richparticles are formed in the metal matrix. This is a diffusioncontrolled reaction, and the strength will vary with agingtime and temperature.Lamineries MATTHEY SARue Montagu 38CH-2520 La Neuveville, SwitzerlandTel. 41 32 752 32 32 Fax 41 32 752 32 00ASTMDesignationwww.matthey.chAT0015/0311 2011 Materion Brush Inc.
Recommended or standard age hardening time andtemperature combinations have been determined for eachcopper beryllium alloy. These standard times andtemperatures allow parts to reach peak strength in two tothree hours, without the risk of strength decrease due toextended temperature exposure. As an example, the Alloy25 response curves in Figure 1 indicate how low, standard,and high aging temperatures affect both peak propertiesand the time required for the alloy to reach peak strength.In Figure 1, at the low temperature of 550 F (290 C), thestrength of Alloy 25 increases slowly, and peak strength isnot reached until approximately 30 hours. At the standardtemperature of 600 F (315 C), Brush Alloy 25 exhibitsvirtually no change in strength after three hours ofexposure. At 700 F (370 C), peak strength is reached in30 minutes and declines almost immediately. In short, asaging temperature increases, the time necessary to reachpeak strength decreases, as does maximum obtainablestrength. This response is similar for all copper berylliumalloys, but at different standard temperatures.Peak Tensile Strength225Tensile Strength200500 F / 260 C175700 F / 370 C125Overaging at 700 F / 370 C Underaging at 700 F / 370Long Time, Easy to Control C - Short Time, PreciseControl RequiredTime (Hours)100750.01.02.03.04.0Allowable variances in age hardening time are dependenton furnace temperature and final property requirements. Topeak age at the standard temperature, furnace time istypically controlled to 30 minutes. For high temperatureaging, however, more precise time control is required toavoid overaging. For example, the aging time of Alloy 25 at700 F (370 C) must be controlled to 3 minutes to holdpeak properties. Similarly, underaging requires tight controlof the process variables because of the sharp initialincrease of the aging response curve. In the standard agehardening cycle, heating and cooling rates are not critical.However, to assure that aging time does not begin untilparts reach temperature, a thermocouple can be placed onthe parts to determine when desired temperature has beenachieved.Standard age hardening times and temperatures for theHigh Strength Copper Beryllium alloys and the HighConductivity Copper Beryllium alloys are detailed in thefollowing sections.HIGH STRENGTH WROUGHT COPPER BERYLLIUM(ALLOYS 25, M25, AND 165)600 F / 315 C150is stored for significant lengths of time.5.0Age hardening temperatures for high strength wroughtcopper beryllium varies from 500 F (260 C) to 700 F(370 C). The time required to reach peak properties at thelower temperature is longer than at the higher temperature.The standard age hardening treatment is 600 F (315 C) fortwo to three hours; two hours for cold worked alloys andthree hours for annealed alloys. Figure 2 shows the effectof time and temperature on the mechanical properties ofAlloy 25 1/2H temper.Figure 1. Alloy 25 – Response to Age Hardening HeatTreatment for three temperaturesCopper beryllium can be age hardened to varying degreesof strength. The term peak aged refers to copper berylliumaged to maximum strength. Alloys not aged to maximumstrength are underaged, and alloys aged beyond maximumstrength are overaged. Underaging copper berylliumincreases toughness, uniform elongation, and fatiguestrength. Overaging increases the alloy’s electrical andthermal conductivity’s and dimensional stability. Copperberyllium never ages at room temperature, even if materialHIGH STRENGTH CAST BERYLLIUM COPPER ALLOYS(ALLOYS 275C, 20C, 21C, AND 165C)The standard age hardening cycle for the high strengthcasting alloys, both annealed and as cast, is three hours at625-650 F (320-340 C). However, to develop the higheststrength for the as cast products, a separate solutionanneal should precede the age hardening.Lamineries MATTHEY SARue Montagu 38CH-2520 La Neuveville, SwitzerlandTel. 41 32 752 32 32 Fax 41 32 752 32 00sales@matthey.chwww.matthey.chAT0015/0311 2011 Materion Brush Inc.
HIGH CONDUCTIVITY WROUGHT ALLOYS (ALLOYS 3AND 10) AND HIGH CONDUCTIVITY CAST ALLOY 3CThe standard age hardening cycle for both the wrought andcast high conductivity alloys is 900 F (480 C) for two tothree hours; two hours for the cold rolled alloys and threehours for the cast and annealed wrought alloys. The highconductivity alloys are noted for their excellent electricaland thermal conductivity’s. They obtain their moderatestrength through age hardening, but at a highertemperature than the high strength alloys.Because their mechanical properties change only slightlywith time, few high conductivity applications benefit fromeither underaging or overaging. As an example, the heattreating curves for Alloy 3 demonstrate the affects of agingon the mechanical properties (see Figure 3).AGE HARDENING EQUIPMENTRecirculating Air FurnacesRecirculating air furnaces, with temperature controlled to 15 F ( 10 C), are recommended for the standard agehardening of copper beryllium parts. These furnaces aredesigned to accommodate both large and small batches ofparts, and are ideal for reels of stamped parts aged oncarrier strips. However, care must be exercised whenaging large batches of parts. Because of their sheerthermal mass, large batches of parts will not have all partsat temperature for the same length of time. As a result,underaging or short aging cycles of large batches of partsshould be avoided.Strand Aging FurnacesStrand aging furnaces, using a protective atmosphere asthe heating medium, are suitable for processing largequantities of material in coil form. This process is generallyused by metal producers, and performed in long furnaceswhere material can be uncoiled into the furnace, passedthrough heating and cooling zones, and upcoiled uponexiting the furnace. The advantages of this type of furnaceinclude good time and temperature control, better part topart uniformity and the ability to control special cycles forunderaging or high temperature/short time aging andselectively hardening a portion of a part.Salt BathsAlso recommended for age hardening wrought products aresalt baths. Salt baths offer rapid and uniform heating, andare recommended at any temperature in the hardeningrange. They are particularly advantageous for short time,high temperature aging.Vacuum FurnacesVacuum aging of copper beryllium parts can be donesuccessfully, but caution must be exercised. Becausevacuum furnace heating is by radiation only, it is difficult touniformly heat large loads of parts. Parts on the outside ofthe load are subject to more direct radiation than those onthe inside, as a result, the temperature gradient produces avariation in properties after heat treatment. To assureuniform heating, load size should be limited and parts mustbe shielded from the heating coils.Alternatively, vacuum furnaces, backfilled with an inert gassuch as argon or nitrogen, can be used. Again, parts mustbe shielded unless the furnace is equipped with arecirculating fan.SURFACE OXIDEDuring aging, the copper beryllium alloys develop a surfaceoxide composed of beryllium and, depending on the alloyand furnace atmosphere, copper oxides. These oxide filmsvary in thickness and composition and are oftentransparent.Surface oxidation of beryllium during age hardening cannotbe suppressed, even in a pure hydrogen atmosphere or ahard vacuum. However, some atmospheres can minimizethe copper oxidation. For instance, a low dew point (-40 F/40 C) atmosphere of approximately 5 percent hydrogen innitrogen will minimize oxidation and economically aid inheat transfer. Air atmospheres contribute the most tosurface oxide and reducing atmospheres the least.Although oxide films are not detrimental to the base alloy,they should be removed if parts are to be plated, brazed, orsoldered. For specific information on cleaning copperberyllium, consult the Materion Brush Performance AlloysTechBrief, “Cleaning Copper Beryllium”.SOLUTION ANNEALINGTo elicit an effective age hardening response, copperberyllium must be solution annealed and quenched prior toaging. In addition to preparing the alloy for age hardening,annealing softens the alloy for further cold work andregulates grain size. Materion Brush Performance Alloysperforms this required anneal on all wrought products at themill. Therefore, customers usually do not need to annealLamineries MATTHEY SARue Montagu 38CH-2520 La Neuveville, SwitzerlandTel. 41 32 752 32 32 Fax 41 32 752 32 00sales@matthey.chwww.matthey.chAT0015/0311 2011 Materion Brush Inc.
prior to age hardening. Furthermore, solution annealing willcause expansion and distortion of machined parts, and cancause generation of hazardous oxides on the surface.If solution annealing is required, it is a high temperaturesoak: 1450 F (790 C) for the high strength alloys and1650 F (900 C) for the high conductivity alloys. Annealingmust be carefully controlled as excess time or temperaturemay cause grain growth. Solution annealing should beimmediately followed by a water quench. As a precaution,large quantities of metal should not be annealed withoutfirst conducting a furnace simulation test. Thin sections,such as fine wire, require an annealing time of about 3-5minutes. Fifteen minutes to one hour is required for thinwalled tube and small castings. Heavy sections (aboveabout one inch) usually require 1-3 hours. A heat up timeof one hour per inch of thickness must be added to thesoak time.Because most salts will attack copper beryllium attemperatures in the solution annealing range, solutionannealing should not be performed in a salt bath.When peak aging copper beryllium castings andweldments, the customer must always solution anneal priorto age hardening. However, if peak properties are notrequired, castings can be age hardened from the as castcondition without the solution anneal.MILL HARDENED ALLOYSIn applications not requiring severe forming, fabricators caneliminate the heat treating and cleaning of the heattreatable alloys by specifying mill hardened copperberyllium. Materion Brush Performance Alloys performs aspecial heat treatment on mill hardened product whichdelivers maximum formability at desired strength levels.High Strength Mill Hardened AlloysThe high strength copper beryllium mill hardened alloys areBrush Alloy 190 and 290. Both alloys fall within the C17200designation and are available in several tempers. Alloy 290provides improved formability at a given strength level.High Conductivity Mill Hardened AlloysThe high conductivity mill hardened copper beryllium alloysare Brush Alloys 3, 10, 174, Brush 60 , BrushForm 47,390 , and 390E. The mechanical properties of millhardened Alloys 3 and 10 are equivalent to the peak agedproperties of the AT or HT age hardenable tempers. Highconductivity Alloys 174, Brush 60, BrushForm 47, 390 and390E are available only in mill hardened tempers. Consultthe “Guide to Materion Brush High Performance Alloys” foradditional data on all mill hardened tempers.SAFE HANDLING OF COPPER BERYLLIUMPlease refer to the Materion Corporation publications“Safety Facts 6 - Safety Practices for Heat Treating CopperBeryllium Parts”, and “Safety Facts 105 - ProcessingCopper Beryllium Alloys.”Handling copper beryllium in solid form poses no specialhealth risk. Like many industrial materials, berylliumcontaining materials may pose a health risk ifrecommended safe handling practices are not followed.Inhalation of airborne beryllium may cause a serious lungdisorder in susceptible individuals. The OccupationalSafety and Health Administration (OSHA) has setmandatory limits on occupational respiratory exposures.Read and follow the guidance in the Material Safety DataSheet (MSDS) before working with this material. Foradditional information on safe handling practices ortechnical data on copper beryllium, contact Materion BrushPerformance Alloys, Technical Service Department at 1800-375-4205.BrushForm , Brush 60 , and Alloy 390 are registeredtrademarks of Materion Brush Inc.Lamineries MATTHEY SARue Montagu 38CH-2520 La Neuveville, SwitzerlandTel. 41 32 752 32 32 Fax 41 32 752 32 00sales@matthey.chwww.matthey.chAT0015/0311 2011 Materion Brush Inc.
Alloy 25 ½ HAlloys 3 A and 10 A900800800 F / 425 CStrength (ksi)1000752.03.04.012001100700 F / 370 C1000500 F / 260 C125900800800 F / 425 C1000.01.02.05.0750700850 F / 455 C650900 F / 480 C85600950 F / 510 C75550500450Time (Hours)550.05.01.02.04003.04.05.03 A Elongation25 1/2 H Elongation15%Elongation500 F / 260 C20%Elongation4.03 A Yield Strength30%25%3.0655004.02.0956003.01.0105700Time (Hours)755000.01300600 F / 315 C5507514001751506506005.025 1/2 H Yield Stre ngth20070095Strength (ksi)1.0950 F / 510 CTime (Hours)5000.0750105600Time (Hours)80085700100Strength (ksi)Strength (MPa)1100Strength (MPa)Strength (ksi)700 F / 370 C150850900 F / 480 C1151200175500 F / 260 C850 F / 455 C1300600 F / 315 C1253 A Tensile Strength125Strength (MPa)1400Strength (MPa)25 1/2 H Tensile Strength200800 F / 425 C10%25%20%700 F / 370 C850 F / 455 C 900 F / 480 C 950 F / 510 C5%600 F / 315 CTime (Hours)Time 0853 A Hardness25 1/2 H Hardness235340700 F / 370 C75310500 F / 26028070250800 F / 42522065Hardness (DPH)Hardness (HR15N)370Microhardness(DPH)400900 F / 480 C22081205160Time (Hours)0.01.02.03.01304.019077Time (Hours)175750.02.03.04.05.0Figure 3. Alloys 3 A and 10 A Aging Response CurvesLamineries MATTHEY SAsales@matthey.ch1.05.0Figure 2. Alloy 25 ½ H Aging Response CurvesRue Montagu 38CH-2520 La Neuveville, SwitzerlandTel. 41 32 752 32 32 Fax 41 32 752 32 0079950 F / 510 C1906083850 F / 455 CHardness (HR30T)600 F / 31580www.matthey.chAT0015/0311 2011 Materion Brush Inc.
Heat Treating Copper Beryllium Parts Heat treating is key to the versatility of the copper beryllium alloy system. Unlike other copper base alloys which acquire their strength through cold work alone, wrought copper beryllium obtains its strength, conductivity, and hardness through a combination of cold .