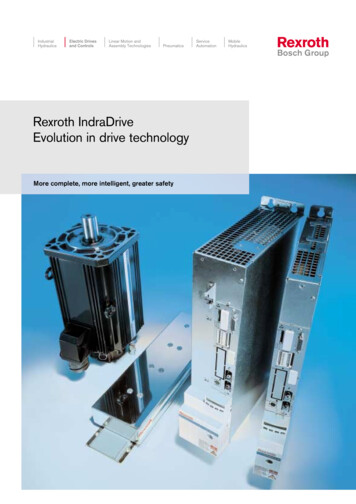
Transcription
Rexroth IndraDriveEvolution in drive technologyMore complete, more intelligent, greater safety
2IndraDrive from RexrothMore complete, more intelligent, greater safetyHow can something be "morecomplete" than "complete", youare probably wondering. Fact is,our IndraDrive sets new standards in drive engineering thatare best described by the apparent contradiction in terms: Itoffers greater safety in use, ismore intelligent in its functions,and really does come "morecomplete" with software andhardware than all past generations of drive systems.Whatever branch of industryyou call your own, in IndraDriveyou will find a complete, intelli-With the IndraDrivegeneration of drives,Rexroth sets yet another milestone in thedevelopment ofmodern automationcomponents for moreflexibility, productivityand precisionIndraDrive is theapplication-optimizeddrive solution withintegrated safetytechnology, PLC andhigh-dynamic motorsgent and above all future-proofsolution to your automation tasks.The flexible combination ofcompact converters or modularinverters with high-dynamiclinear and rotary motors makesIndraDrive predestined forintelligent single-axis as well ascomplex multiple-axis applications.IndraDrive offers a host ofapplication advantages, forexample: Safety on Board conformingto EN 954-1, category 3, for"Safe Stop" and "Safe Motion" a wide power range from 1 kWto 110 kW openness for internationalinterfaces integrated Motion Controlwith PLC conforming toIEC 61131-3 highest performance and precision scalable power and functionality fast initial startup power regenerating anddirect connection to mainssupply from 380 V to 480 V integrated mains contactorand braking resistor
3Convincing in performance and functionalitySafety on BoardFast and easy initial startupSafety technology certified as complying with EN 954-1, category 3,makes sure that people are protected even from moving axes. Unlikeconventional safety concepts, thistechnology works without powercontactors in the mains or motorsupply lines and without additional speed monitors.The DriveTop startup assistant guides you reliably and quickly throughthe startup routine.Integrated Motion Control withPLC conforming to IEC 61131-3Motion Control with PLC conforming to IEC 61131-3 can be integrated as an optional feature that isfully committed to open standards.This makes it easier to implementcustomer know-how, and the costsof higher-level control systems andpersonnel training courses can besaved.Integrated technology functionsTechnology functions can be parameterized on the basis of the drivePLC to perform the most diverseprocess-oriented tasks. The userneeds no programming know-howwhatsoever for this work.Open interfacesInternationally recognized interfaces are available for communicatingwith higher-level machine controlsystems: SERCOS interface, PROFIBUS-DP, INTERBUS, CANopen,DeviceNet, analogue and parallel.AutomationPrinting and paper convertingmachinesA unique platformWe have developed two versions ofIndraDrive in order to better meetyour individual requirements: with a compact converter systemfor power ratings up to 110 kW with a modular inverter systemfor up to 75 kWParticularly economical drive solutions can be assembled from thecommon control units and thecombination of versions.Conveying and storagetechnologyGlass processing machinesHandling and assemblysystemsA complete range of motorsThe newly developed generation ofIndraDyn motors meets all requirements in modern factory automation through a combination ofmodel diversity and unique performance: synchronous and asynchronousservo motors of far greater compactness with higher power servo motors for potentiallyexplosive areas – conforming toATEX and UL/CSA linear and torque motors forinnovative direct drive concepts synchronous and asynchronousmotors for high-speed applications, e.g. motor spindlesWoodworking machinesPlastics processing machinesTextile machinesConverting technologyPackaging and foodprocessing machinesMachine tools
4Standardized for all applicationsConverters from 1,5 kWto 11 kW – the mostcompact in their class,ideal for single-axisapplicationsIndraDrive is based on a uniform hardware platform thatsets new standards with its unique continuity, flexibility andfuture adaptability.All control components – fromthe simple frequency converterto the high-end servo drive withintegrated Motion Control –are combinable with allIndraDrive C converters andIndraDrive M inverters.Power unitsControl unitsControl units are available in differentversions:Basicwith sufficient performance and functionality for standard applicationsAdvancedfor applications requiring the highestperformance and interface flexibilityConverters from 15 kWto 110 kW – can becombined with modularinverters to create economical and compactdrive solutionsModular inverters upto 75 kW – ideal formultiple-axis applicationsA further example of continuityand flexibility: Indradrive Cconverters can be combinedwith IndraDrive M inverters tocreate extremely compact andeconomical drive packages.
5Scalable for your individual applicationThe basic packages already includeall essential functionalities forstandard applications, such aspositioning block mode, positioncontrol, and speed and torque control.Extension packages are also available, e.g. for electronic axis synchronization, cam switches, error compensation, main spindle functionsor Motion Control with drive PLCconforming to IEC 61131-3.Complex process functions areimplemented by means of application-oriented technology packages.Programming is easy and requiresno special programming knowhow.The technology packages can alsobe used within the freely programmable PLC.Motion Control with PLCconforming to IEC 61131-3Process-orientedtechnology packagesProcess-orientedtechnology packagesError compensationMain spindleMain spindleCam groupSynchronizationSynchronizationOpen loop basicpackagesOpen loop basicpackagesBASICADVANCED
6Fast initial startup and easy operationwith DriveTopThe DriveTop startup assistant makes it easier in many ways for you to start up your machine.Parameters areentered in standardunits of measurementsPositioning data areentered with graphicassistanceIntegrated four-channel oscilloscopeStartup assistantAutotuning functionDriveTop guides the startupoperator in interactive mode.The system automatically asksfor the relevant data accordingto the mode of operation. Allvalues are entered in standardunits of measurement (e.g. mm,inch) in order to cut time-consuming conversion calculations.The values entered stand indirect relationship to themechanical components. Theycan be selected from a largeselection of positioning modeswhich are presented in graphicform. All the data can be savedin a file. Data blocks can beuploaded and downloadedthrough an RS232 interface orfield bus.All controllers in IndraDrive arealready pre-set and tuned to theconnected motor in question.The autotuning function can beused for controller optimizationif adaptations need to be madeto the machine.Four-channel oscilloscopeEasy optimization ofcontrol circuit settingsA four-channel oscilloscope isavailable for checking the control equipment settings in theplant, for troubleshooting andfor preventive maintenance. Allmeasurements and their relatedsettings are available for documentation in the form of aprint-out or data file.Offline modeThe plant-relevant operatingmodes and their correspondingparameters can be set in advancein offline mode.Adapting DriveTop to yourmachineDriveTop is easy to adapt to yourapplication or machine. Duringstartup you then need to provideonly data that is relevant for theselected application.
7Stay on the safe sideThe protection of persons fromuncontrolled machine movements has absolute priority inall applications. With IndraDrivefrom Rexroth, the pioneer ofdrive-integrated safety technology, you are on the safe side.We have integrated diverse safety functions directly in the drive– without detour through acontrol system. Reliability isthus increased, while monitoring components are saved andwiring effort is reduced.Maximum safety and highestdrive dynamicsConvincing advantagesSafety category 3 – alreadycertified in the driveExploit these advantages anduse the integrated safety functions of our drives to provideeffective protection for man andmachine: high reliability through integrated, certified safety functions very fast reaction times( 2 ms) when the internalmonitors respond non-time-critical selection ofsafety functions, e.g. by thePLC fewer measurement systemsor indicating devices required reduced certification costs forthe customer use of any higher-level controlsystems shorter startup times, fastertroubleshootingRedundant software and hardware components in the drivemake it all possible. The noncontact monitoring of all setlimit values enables very shortresponse times of less than 2 ms.Once a fault is detected, all thedrives are automatically stopped– depending on which stopcategory is selected (0, 1 or 2) –and immediate two-channeldisconnection from mains.as the pioneers in this field. Theresults of our ongoing furtherdevelopment work are safetyfunctions that are convincinglyimplemented and certified ascomplying with EN 954-1, category 3: "Safe Stop" "Safe Operational Stop" "Safely Reduced Speed" "Safely Limited Increment" "Safely Limited AbsolutePosition" "Safe Direction of Rotation" “Safe Closing of Safety Door”Ever since we first introduceddrives with Safety on Boardtechnology to the market backin 1999 we have been regarded2IndraDrive safety technology from RexrothConventional safety technology800Movement of axis in mm after an Emergency StopSafety increased 400-foldIn the time it takes anoperator in a protected area with conventional enabling torespond to an error, alinear axis with a ballscrew spindle willhave already covereda distance of 100 to200 mm, and a linearmotor a distance of400 to 800 mm.IndraDrive safetytechnology detectsthe error within 2 msand the axis moves adistance of no morethan 2 mm.
8Basic or AdvancedAlways optimum performance and functionalityBASICOpen LoopClosed LoopADVANCEDOpen LoopClosed LoopBasic packages"Open loop" basic functionsMotor control with U/f curve,incl. slip compensation, I x R compensation and stall protectionAutomatic control circuit adjustmentCurrent and torque limitingSpeed ramp generatorFlying restart after power failurePositioning by limit switchesOscilloscope function"Closed loop" basic functionsPosition, speed and torque controlDrive-controlled positioningDrive-internal interpolationPositioning block modeAdjustable reaction to errorsElectronic type plateBrake controlPosition, current and torque limitingMoving to fixed stopAutomatic control circuit adjustmentAutomatic commutation adjustmentPath switching point with ON and OFF switching thresholdSetting the coordinate system––Error compensationEasy backlash compensationAxis error correctionQuadrant error correctionFrictional torque compensationTouch probe with fast stop––––––––1Parameter set changeoverincluding gear changeField-oriented controlVector control, without encoder up to 2000 HzSpindle positioning modeDrive-controlled swiveling for gear �––2Extension packagesMain spindle functionsSynchronizationSpeed synchronizationAngle synchronizationMeasuring wheel modeReal and virtual leading axisCam plate (tabular value)Cam plate (analytical value)Touch probe with time measurementTouch probe with synchronization ��1––––––coming soon–2Cam groupDynamic cam groupDrive PLCMotion ControlFreely programmable in compliance with IEC 61131-3Programming system for AWL, ST, AS, CFC, KOP, FUP(online change, debugging, offline simulation)Integrated logic controlSingle-axis Motion Control4 user tasks (periodic, unsolicited or event-controlled)System librariesMotion library based on PLC openSupport of customer librariesProcess-oriented technology packagescoming soon
9IndraDrive control units differ inperformance and configuration.Thanks to this flexibility it is possible to select the best suited andhence most economical version foreach application:Advanced control units offer thehighest performance and can beequipped with the most diversecontrol, communication and encoder interfaces as well as additionaloptions for safety technology, forexample. Digital and analogueinputs and outputs are already permanently integrated – along with arelay output – for communicationwith higher-level control systems.Advanced control units have a levelof performance to satisfy even thehighest requirements imposed oncontrol quality.Basic control units are the economical solution for standard applications. Basic control units withfixed configurations can be usedfor applications which impose lowrequirements on interface flexibility.They are available with SERCOSinterface, PROFIBUS and analogueinterfaces, as well as with an encoderinterface for IndraDyn S motors.Configurable Basic control components in single-axis as well as double-axis versions are also availablefor standard applications requiringadditional option modules.All control units are equipped witha standard display. A graphicscapable comfort display is alsoSingle-axisBASICDouble-axisBASICfixed rationCommand communicationOption slot 1Option slot 2Option slot 3Option safetyOption display–––Control communication interfacesSERCOS ue interfaceParallel interfaceMulti-encoder interfacesIndraDyn S motors incl. Hiperface and 1VssMHD, MKD and MKE motorsEnDat 2.1 incl. 1Vss Z0 and 5 V TTLEndat 2.2Safety options compliant with EN 954-1Drive lockProtection from unintended restartingSafety technologyin compliance with Safety Category 3"Safe Stop" and "Safe Operational Stop""Safely Reduced Speed" (RPM)"Safe Direction of Rotation""Safely Limited Absolute Position""Safe Closing of Safety Door "–––––/coming sooncoming sooncoming soon–Further optionsAnalogue I/O extensionEncoder emulationDigital I/O extensionCross communication––coming sooncoming soonSoftware moduleMMC (MultiMediaCard)DisplayStandardone line, four buttonsComfortfour lines, graphics-capable, four buttonsavailable as an option. The configurable control units can be equipped with a MultiMediaCard (MMC)for changing devices without a PCor, for example, for use as anextended program memory for theintegrated PLC.Standard featuresOptioncoming soon
10IndraDrive C – Converters of compact formatParticularly economical solutionsfor both single-axis and multipleaxis applications with up to 11 kWrated motor power are possibleusing this series of space-savingconverters. Already integrated inthe compact design are a supplyunit, a braking resistor, link circuitcapacitors and axis inverters. Thelink circuit connection permitsenergy compensation for multipleaxis applications. Installation incompact 300-mm control cabinetsis possible.IndraDrive -W0070Rated current (S1)A eff4,2112028Maximum current (400 ms)A eff12285470Typical rated motor powerkW1,547,5*11*Connection voltageof power unit3 x 200 V . 500 V AC 10 %Connection voltageof control unit24 V DC /- 20 % or autonomous voltage supply from the link circuit0 . 3000 HzOutput frequencyBraking resistorContinuous braking powerkWMaximum braking power (0,5 s) kWWidth x Height x Depth50 . 60 Hz 2 nal0,050,150,35/0,360,5/5,5410182665 x 295 x 26565 x 350 x 265105 x 350 x 265105 x 350 x 265*Data with external choke
11IndraDrive C – Converters for highest powersThese compact converters cover theentire range from 15 kW to 110 kWrated motor power and are ideal for400-mm control cabinets. Theycome on request with braking transistor, braking resistor and line filter– optimally scaled for your driveapplication. And together withIndraDrive M inverters they provideyou with a particularly economicaland compact drive system for multiple-axis operations.HWDIndraDrive 210HCS03.1-W0350Rated current (S1)A eff406295145210Maximum current (400 ms)A eff6390147213350Typical rated motor powerkW18304575110Connection voltageof power unit3 x 200 V . 500 V AC 10 %Connection voltageof control unitAutonomous voltage supply from the link circuit; external 24 V DC ( 20%) stand-by supply available as optionOutput frequency0 . 2500 Hz (fp 4 kHz)External braking resistor,minimum valueContinuous braking power50 . 60 Hz 2 %kWMaximum braking power t 2 skWWidth x Height x Depthmm0 . 3000 Hz (fp 16 kHz)181371,93,5915233855304474110180125 x 440 x 309225 x 440 x 309225 x 440 x 309350 x 440 x 309coming soon*All data with external choke
12IndraDrive M – Modular invertersParticularly economical multipleaxis solutions with up to 75 kWcan be implemented with the slimline single-axis devices (HMS) anddouble-axis devices (HMD) of theIndraDrive M inverter system. Thedevices are optimized for highmaximum currents from 20 A to210 A and ensure that your machining processes perform with maximum dynamics. Supply units withpower regenerating are also available.IndraDrive 1.1N-W0036Rated current (S1)A eff10181220Maximum current (400 ms)A eff20362036Connection voltage275 V . 750 V DC0 . 3000 HzOutput frequencyWidth x Height x Depthmm50 x 440 x 30975 x 440 x 30950 x 440 x 30950 x 440 x .1N-W0210A eff284290140Maximum current (400 ms) A eff5470150210150 x 440 x 309200 x 440 x 309IndraDrive MRated current (S1)Connection voltage275 V . 750 V DC0 . 3000 HzOutput frequencyWidth x Height x Depthmm75 x 440 x 309100 x 440 x 309
13IndraDrive M – Modular supply unitsFor the modular system ofIndraDrive M inverters you have achoice of supply units with or without power regenerating, dependingon the power requirement andapplication. Wiring in the controlcabinet is minimized by integratedcomponents such as mains contactors and braking resistors, and bydirect connection to a mains voltage from 380 V to 480 V. Optionalline filters suppress conductedinterference, even without an additional transformer.IndraDrive MHDWVoltage supply without power regeneratingVoltage supply with power regeneratingHMV01.1E-W0030 HMV01.1E-W0075 HMV01.1E-W0120 HMV01.1R-W0018 HMV01.1R-W0045 HMV01.1R-W0065Link circuit power with throttlekW30751201845Link circuit power without throttlekW184572–––Maximum link circuit powerkW4511218045112162Connection voltage3 x 380 V . 480 V AC6550 . 60 HzControl voltageexternal 24 V DCMains contactorintegratedBraking resistorinternalContinuous braking powerkW1,522,50,40,40,4Maximum braking powerkW36901303690130Energy consumptionkWs10025050080100150150 x 440 x 309200 x 440 x 309350 x 440 x 309175 x 440 x 309250 x 440 x 309350 x 440 x 309Width x Height x Depth
14A range of motors to satisfy all wishesIndraDrive offers you a complete range of synchronous and asynchronous motors fortranslatory and rotary movements. The outstanding characteristic of this range is itsunique diversity of motor types, models and power ratings.Servo motorsfor standard applicationsServo motorsfor the highest requirementsServo motorsfor potentially explosive areas Rated torque from 0,4 Nm to72 Nm Rated torque from 1,2 Nm to240 Nm Rated torque from 0,9 Nm to48 Nm Natural convection and surfaceventilation Natural convection, surface ventilation and liquid cooling Natural convection Rated speed up to 9.000 min-1 Rated speed up to 9.000 min-1 Resolver with data memory formotor parameters Rated speed up to 7.500 min-1 Resolver with data memory formotor parameters Absolute encoder (option) High-resolution single- andmulti-turn absolute encoderswith data memory for motorparameters Holding brake (option) Holding brake (option) High-resolution single- andmulti-turn absolute encoderswith data memory for motorparameters IP68 (option) Holding brake (option) ATEX-conform version UL/CSA version (option)
15Servo motorsfor high drive powersLinear motorsfor the highest dynamicsKit motors for newmachine conceptsHigh-torque motorsfor high torques Drive range up to 93 kW Feeding force up to 22.000 N Rated torque up to875 Nm Maximum torque up to4.700 Nm Surface ventilation or liquidcooling Speed up to 600 m/min Rated speed up to6.500 min-1 Maximum speed up to1.200 min-1 Liquid cooling (thermalencapsulation) Liquid cooling (thermalencapsulation) High-resolution single- andmulti-turn absolute encoderswith data memory formotor parameters Incremental encoder(option) Holding brake (option) Liquid cooling (thermalencapsulation)
Bosch Rexroth AGElectric Drives and ControlsP.O. Box 13 5797803 LohrBgm.-Dr.-Nebel-Str. 297816 LohrGermanyPhone 49 93 52/40-0Fax 49 93 52/40-48 85www.boschrexroth.comPresented by:The data shown are for general information only.Please contact your local sales office for up-to-date information.A1 - HW - Copyright reserved!Subject to revisions!Printed in Germany71 039 EN/03-03
IndraDrive is based on a uni-form hardware platform that sets new standards with its u-nique continuity,flexibility and future adaptability. All control components - from the simple frequency converter to the high-end servo drive with integrated Motion Control - are combinable with all IndraDrive C converters and IndraDrive M inverters.