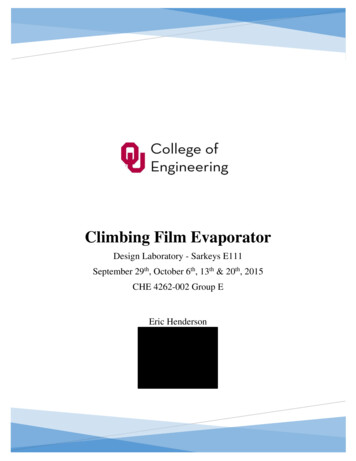
Transcription
Climbing Film EvaporatorDesign Laboratory - Sarkeys E111September 29th, October 6th, 13th & 20th, 2015CHE 4262-002 Group EEric HendersonNadezda MamedovaAndy SchultzXiaorong Zhang
Table of ContentsExecutive Summary (Nadezda Mamedova) . . 2Introduction (Nadezda Mamedova) . . . .3Theory (Nadezda Mamedova) . . . .4Design Plan (Eric Henderson) . . . 6Experimental Plan (Andy Schultz) . . . . . . .8Apparatus (Andy Schultz) . . . . .10Experimental Results (Xiaorong Zhang) . . . 12Scaled Up Design (Andy Schultz) . . . 14Process Flow Diagram (Nadezda Mamedova) . . . . 18Design Comparison (Andy Schultz). . . . .20References . .21Appendices . . . .22Appendix I: Data Tables (Eric Henderson). . . .22Appendix II: Results Calculations (Eric Henderson) 27Appendix III: Error Calculations (Nadezda Mamedova) . 31Appendix IV: Scaled Up Design Calculations (Eric Henderson) . 341
Executive Summary – Nadezda MamedovaPurpose: The purpose of the experiment was to determine operating conditions of a climbingfilm evaporator that can recover triethylene glycol from a stream that contains 30 wt%triethylene glycol. The desired concentration of the exit stream is at 88 wt% triethylene glycol. Itis required that 90,000 gallons of inlet liquid be processed per day.How information was obtained: Our engineers had four laboratory days to operate a climbing filmevaporator over a range of vacuum pressures to determine which pressure was the most costefficient as well as which operating conditions could process the required inlet flow.Key findings: We determined that in order to be cost efficient and handle the required inlet flow,we require two climbing film evaporators operated at 20 inHg vacuum. The total cost of installationand operation for a year is 2,718,483.00. The most expensive requirement is 2.8*107 kg of steamper year.Disclaimers and Recommendations: This experiment was performed under the assumption that thevacuum and system pressures were in equilibrium. We used this assumption to calculate a goaltemperature at which the desired exit composition would be reached. We recommend testing theexit product composition to determine the accuracy of this assumption. Due to time constraints,our data gathered was not all started at the same temperature. If more time is allowed, werecommend running the experiment from the same temperature and atmospheric pressure to allowfor better comparisons.2
Introduction – Nadezda MamedovaOur engineers are expanding our company by adding in a climbing film evaporator that canremove water from a stream of triethylene glycol and recycle the glycol back into a previousprocess. The entering stream is at a concentration of 70 wt. % water, and our goal is to have anoutlet stream of no more than 12 wt. % water. The process requires ninety thousand gallons ofmixture to be processed per day.Climbing film evaporators, also known as rising film or vertical long tube evaporators, are usedin industry for effluent treatment, polymer production, food production, pharmaceuticals, andsolvent recovery.1 The liquid being evaporated is fed from the bottom into long tubes and isheated with steam condensing on the outside of the tubes, bringing the liquid inside to a boil. Theproduced vapors press the liquid against the walls of the tubes. The vapor has a higher velocitywhich forces the liquid against the tube wall to rise. This gives the process its name.23
Theory – Nadezda MamedovaA variety of evaporators are used in industry. Our engineers will focus on the climbing filmevaporator operated in batch mode. The evaporator will also be operated under vacuum. Thebenefit of this is that it allows for operation at lower temperatures. The mixture of triethyleneglycol and water enter the bottom of a thin wall glass calandria tubes wherein the mixture isheated to boiling. The water vapor carrying the triethylene glycol climbs the evaporator andenters a cyclone separator. Here the triethylene glycol condenses and is returned to theevaporator while the water is collected separately.Bourgois and LeMaguer found that the dimensionless volumetric vapor flux may be used todetermine the most efficient point of operation. The dimensionless vapor flux,, is given by[1]Where: vapor density liquid density gravitational constant inside diameter of the tubeOperation efficiency increases with increasinguntil 2.5. At this point steamconsumption is at a minimum and the steam temperature and vacuum pressure are optimal.When the value ofis greater than 2.5 the steam consumption needed to produce product at agiven concentration greatly increases asincreases, and the process becomes inefficient.To account for economic efficiency we considered a scale up factor, R. R was determined fromthe amount of liquid needing to be processed and the amount our pilot equipment could process.4
[2]Where:R Scale up factorQrequired Amount of liquid required for processing (90,000 Gallons)QExperimental Amount of liquid our laboratory could processThis R factor was carried out to determine other scaled up calculations and cost of the process.5
Design Plan – Eric HendersonDuring the operation of a climbing film apparatus, the continued use of steam becomes veryexpensive; therefore, an attempt to minimize this use of steam will be made. A systemtemperature at a given pressure will be related to steam flow rate to produce a 88% triethyleneglycol separation using figures from the DOW Chemical Triethylene Glycol manual (figurebelow).4 This system temperature will be found by utilizing the Antoine equation in Excel’sSolver. The Antoine constants are obtained by interpolation of 80% and 90% values in Figure 5in this lab’s manual (Vapor Pressures of Aqueous Triethylene Glycol Solutions at VariousTemperatures) to produce constants for 88% triethylene glycol separation.Figure 1: Vapor Pressures of Aqueous Triethylene Glycol Solutions at Various Temperatures4Using these experimental data (triethylene glycol flow, column pressure, steam temperature,dehydrated triethylene glycol temperature, and condensed water volume), various relationshipsbetween data can be calculated to estimate process cost. For example, once a strong relationshipbetween triethylene glycol separation, temperature, and pressure has been established, a steamcost comparison ( /kg) will be analyzed by using data from Table 8.4 (Costs of Some CommonChemicals).5By taking the costs into consideration, the optimum steam flow rate will be related to vapor flux(Equation 1) and feed flow rate to determine the economically optimum scale up plant size.Equipment sizes will be predicted from using Figure 2, with the notion that the production6
requirement of 90k gal/day of process mixture must be met. Analysis of these costs will alsorequire a raw materials cost estimation from Table 8.3, and ultimately, the total costsexamination by Table 8.2.5Figure 2: Purchased Costs for Evaporators and Vaporizers5It must be assumed that calculated values for this experiment can be applied to any apparatuslocation. That is to say, values such as correction factors for various geological locations do notneed to be used. Furthermore, an accurate exemplification for the current market value costs canbe assumed to be corrected under evaluation techniques from present worth calculations.Although correction factors are assumed to not apply, scale up factors must still be calculatedonce the optimal steam pressure and vacuum pressure are found. The scale up factor calculatedfrom Equation 2 (from Theory) will be used when sizing the equipment and total steamconsumption from the pilot plant to the commercial plant. On the other hand, the size of thetubes in the evaporator does not need to be scaled up since the heat transfer will not change.However, an increased number of tubes in the evaporator would be optimal for the commercialprocess.The optimal steam pressure and vacuum pressure are found by experimental trials in which thedesired composition is achieved by the lowest steam consumption under a constant vacuumpressure. These values will be used in the cost analysis, along with the amount of cooling waterin the condenser. The amount of cooling water in the condenser is found from the heat necessaryto condense the vapor from the cyclone separator.7
Experimental Plan – Andrew SchultzIn this experiment, the group will analyze the separation of water from triethylene glycol (TEG)via steam evaporation in a column. Several variables will be manipulated throughout theexperiment to evaluate the optimal conditions which yield the best separation of the twosubstances. Variables of importance include: steam flow, saturated triethylene glycol flow,column pressure, steam temperature, dehydrated triethylene glycol temperature, and condensedwater volume. The operating parameters for each are given below in Table 1.VARIABLEOPERATING RANGEUNITSSteam Flow Rate0 – 90mL/minSaturated TEG Flow Rate0 – 90mL/minVacuum Pressure0 – 30psiTable 1: Operating ranges of independent experimental variables.Throughout the experiment, the independent variables which the group will manipulate includesteam flow, saturated triethylene glycol mix flow, and vacuum pressure. The group willdetermine the flow rates for the steam and saturated TEG. These flow rates will be measured byrotameters located on the operating panel and will remain constant throughout the experiment.The group will manipulate the pressure inside the column via a vacuum pump. The separation ofwater and TEG will then be evaluated at various vacuum pressures.As the pressure inside the column is manipulated, each new system pressure will be used tocalculate the theoretical (goal) temperature that triethylene glycol must reach to obtain thedesired dehydration. The temperature of the steam flowing into the system is an importantparameter to monitor as it is the initial temperature of the system. The measured (dependent)goal temperature is the final temperature of the system at a given vacuum pressure. The volumeof condensed water is also an important dependent variable that the group will measure. Thevolume of water collected over a period of time as determined by the group will indicate theeffectiveness of separation at a given vacuum pressure.8
The group will conduct the experiment over the next three laboratory periods according to Table2 below. The order of evaluation for each vacuum pressure will be cycled during each laboratoryperiod to evaluate the effect of the temperature of the column being higher than ambientconditions after the first experiment of each day. This will allow the group to identify andevaluate the differences, if any, of starting an experiment at ambient conditions versus a systemat higher than ambient KMeasure condensed water volume for vacuum pressures at 19, 20, 21, 22psi. Evaluate time taken to achieve goal temperature.Measure condensed water volume for vacuum pressures at 20, 21, 22, 19psi. Evaluate time taken to achieve goal temperature.Measure condensed water volume for vacuum pressures at 21, 22, 19, 20psi. Evaluate time taken to achieve goal temperature.Table 2: Schedule of experiments to be performed on remaining experimental laboratory days.Due to the limitations of the laboratory, specifically the vacuum pump, the range of vacuumpressures at which the group was able to conduct the experiment were limited. This may be afactor when the group determines the optimum operating vacuum pressure to separate waterfrom triethylene glycol to the desired dehydration set point. You also changed the steampressure.9
Apparatus – Andrew SchultzMajor equipment available in the laboratory for pilot tests for this experiment include anevaporator, separator, condenser, batch reactor, vacuum pump, and recycle pump. The watertriethylene glycol (H20/TEG) mixture is pumped from a storage tank into a shell and tube heatexchanger. The H20/TEG mixture enters tube side at the bottom of the exchanger while steamenters shell side at the top. As the steam condense around the tubes, the process fluid inside thetubes is heated until water begins to vaporize. As the water vaporizes, the TEG is pushed to theoutside of the tubes and up the column, hence the namesake climbing film evaporator.6 Thewater vapor and TEG then enter a vertical separator wherein the heavier liquid TEG flows to thebottom of the separator into a recycle loop while the water vapor flows out of the top of theseparator to the condenser. Inside the column, the water vapor condenses downward into a batchreactor. The condensed water is collected and measured via an outlet stream from the bottom ofthe reactor. This volume is indicative of the efficiency of the system under the operationalvacuum pressure conditions – that is, the more water that is collected, the more water that isseparated from the TEG. Thus, the more efficient the system is at the specified operatingconditions. The vacuum recycle pumps facilitate the movement of the process throughout thesystem. Rewrite last sentence to clarify.Important operating variables for this experiment include the vacuum pressure of the system,vacuum pump water flow, and steam pressure entering the evaporator. The group activelymanipulated the vacuum pressure throughout the experiment in order to evaluate the efficiencyof water evaporation from a water-triethylene glycol mixture. This procedure was predicated onthe idea that the boiling point of fluids decrease at higher vacuum pressures. In order to createthe vacuum inside the system, a fluid stream was necessary to cycle through the vacuum pump.A water stream
Climbing Film Evaporator Design Laboratory - Sarkeys E111 September 29th, October 6th, 13th & 20th, 2015 CHE 4262-002 Group E Eric Henderson Nadezda Mamedova Andy Schultz Xiaorong Zhang