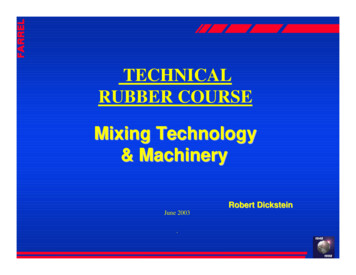
Transcription
TECHNICALRUBBER COURSEMixing Technology& MachineryRobert DicksteinJune 2003.Main
Topics Commonly used Rubber Compounding machinery Basic mixing theory Intermeshing and tangential batch mixers Practical Aspects of Batch mixer operationMain
Main
Primary Compounding rst Rubbercompoundingmachine(not generally aprimary mixerthey are usedas a post mixerforming device)-Very versatileBroad range of shear capabilityaccepts all feed formsgood for short production runs- difficult to control- difficult to automate- batch to batch variation ( due toweighments, feeding ,&heat & shearhistory)- dirty operation- safety considerations- low output- varying power demand- labor intensiveBATCH MIXERSMost commonRubbercompoundingMachinery-accepts all feed formshigh outputcan be automatedgood for short production runslong life expectancybroad range of shear capability- varying power demand- batch to batch variation(mixer control & weighments)- post mixer variable product heat history- capital intensive- need post mixer forming- can be labor intensiveCONTINUOUSMIXERSSpecialtyapplications- high output- energy efficient- ease of process optimization- easily automated- uniform product shear & heathistory- need free flowing feed (particulaterubber)- require sophisticated weigh & feedsystems- not applicable for short runs- difficult to clean- capital intensive- need post mixer formingTWIN -- need free flowing feed(particulaterubber)- require sophisticated weigh & feedsystems- not applicable for short runs- difficult to clean- capital intensive- configuration changes requiredMainenergy efficientease of process optimizationeasily automatedgeometry optimized for useuniform product shear & heathistory
Compounding’s Quality ObjectiveQUALITY PRODUCTPRODUCT POTENTIALWHEN PROPERLY FABRICATED THEPART MUST MEET ALL PHYSICALREQUIREMENTSMainPROCESSABILITYTHE PRODUCT MIX MUST EASILYBE FORMED INTO THE FINALPRODUCT SHAPE
Process ery
The Mixing ProcessMain
Raw MaterialsTypical Material Concerns Polymer type age, uniformity & purity MW & MWD entanglements thermal &oxidative characteristics homogenization of single or multiple polymers(phase morphological concerns-compatibly) environmental and geometric affect of polymers filler type( extending,reinforcing,& reactive fillers) age,uniformity, purity,reactivity particle size and particle size distribution requirement to breakdown agglomerates or pellets the possible forming of agglomerates requirements for efficient filler/polymer interaction type of plasticizers ,protective additives,reactive chemicals age,uniformity, purity,reactivity lubricating affects of liquid and melting additives threshold temperature affects for incorporation maximum temperature limitationsMain
TYPES OF MIXINGREACTIVEMainDISPERSIVEHigh shearDISTRIBUTIVE
Batch Mixing TechnologyMain
Basic Components of The Batch MixerAIR or HYDRAULICCYLINDER(ram actuator)HOPPERHOPPER COVERASSEMBLYRAMCHAMBERROTORS(Tangential or Intermeshing)Mixer motor drive& reduction setMainBatch dischargingmechanismDROP DOORTHERMOCOUPLE INDROP DOOR OR END FRAME(indicated mix temperature)
Batch MixingTechnologiesIntermeshingIntermix “Mark 5”MainTangentialBanbury F series “ST”
Machinery in ApplicationAREAS O F APPLICATIO N% O F INTERM IX BATCH M IXERS INAPPLICATIO N% O F BANBURY BATCHM IXERS IN APPLICATIO NTIRE CO M PO UNDS557TECH NICAL RUBBER G O O DSie,SEALS,H O SE , AND CUSTO MM IXING7923W IRE AND CABLE7334613FLO O RINGPLASTICS CO M PO UNDINGMain
Areas of mixer applicationIntermix &Banbury -medium viscosity formulations-general rubber goodsIntermix Banbury -specialty rubber goods(low temperature compounding )-extreme quality applications-high volume applications-easy to mix formulations-sticky materials reactive mixing applications (high viscosity) single step mixing applications multiple step mixing applications(especially final mix of highviscosity compounds)Main
Selected Items of ComparisonMechanicalINTERMESHING ROTOR DESIGNTANGENTIAL ROTOR DESIGN Ram actuation(HYDRAULIC OR PNEUMATIC) Hopper door Ram or weight design Mixer sides Mixer rotor end plates Mixer rotors Drop door design Drop door latch mechanism Dust stopsMainMain1
Hydraulic hopper ActuationPotential Benefits Eliminates compressed airrequirements Efficient application of highbatch pressure Potential Increase of processrepeatability due to theelimination of the variations inthe plant air supply Potential reduction in plantoperating expenses it allows position control andvariation of pressure on thebatch during the mixing cycleMain
Batch & Cylinder PressureCYLINDER AIR PRESSURE- air pressure applied to thepiston in the cylinder forcingthe weight downBATCH or RAM PRESSURE- pressure applied by thebottom of the weighton the batchMain
Batch & Cylinder PressureCylinder Vs Batch Pressure(F-270 - 22 inch diameter air cylinder)70BatchPSI605040302010010203040506070Air cylinder PSIMain8090100
Batch & Cylinder Pressure(hydraulic system for F-270 mixer)Main
“BATCH” AND “CYLINDER”PRESSUREPSI T(PSI ABOVE PISTON)BATCH PSI f (PSI T - PSI B) x AREA PISTONAREA WEIGHTMIXER AIR CYLINDER PERFORMANCE(assume area of piston area of weight)( Batch pressurization time)PSI B90( PSI BELOW PISTON)80PSI(CYLINDER)70AIR PRESSURE ABOVE PISTONIN CYLINDER60BATCH PSI50( EFFECTIVE PRESSUREON BATCH)40RESIDUEPSIAIR PRESSUREBELOW PISTON BLOCKAGESLOW PRESSURIZATIONBATCH30PRESSURIZATIONIN CYLINDER201000152030TIME (SECONDS)Main405060
“BATCH” AND “CYLINDER”PRESSUREPSI T(PSI ABOVE PISTON)BATCH PSI f (PSI T - PSI B) x AREA PISTONAREA WEIGHTMIXER AIR CYLINDER PERFORMANCEIncreased pressurization timePSI BLegendPSI(top)PSI(B)PSI (B res.)PSI (EFF.-1)PSI (EFF-res)90( PSI BELOW PISTON)80PSI(CYLINDER)7060BATCH PSI50( EFFECTIVE PRESSUREON BATCH)40RESIDUEPSISLOW PRESSURIZATION BLOCKAGEFAST30PRESSURIZATION201000152030TIME (SECONDS)Main405060
Selecting aHydraulic or Pneumaticactuated ramTopics to be addressed TangentialVs Intermeshing rotor mixer Consistency of air pressure to mixer Quality & quantity of supplied air Operating cost Environmental considerations System Maintenance costs Capitol investment Knowledge of system operating characteristicsMain
Selected Items of ComparisonMechanical TANGENTIAL ROTOR DESIGNRam actuationHopper doorRam or weight designMixer sidesMixer rotor end platesMixer rotorsDrop door designDrop door latch mechanismDust stopsMainMainINTERMESHING ROTOR DESIGN1
Intermix full down weight positionThe ram when full down is anextension of the body bore( the bottom becomes a working surface)Main
Banbury full down weight positionThe ram full down position iselevated.The Elevated Positionis necessary for efficient ventingand material flow within themixing chamberMain
Selected Items of ComparisonMechanical TANGENTIAL ROTOR DESIGNRam actuationHopper doorRam or weight designMixer rotorsMixer rotor end platesMixer sidesDrop door designDrop door latch mechanismDust stopsMainMainINTERMESHING ROTOR DESIGN1
Intermix Dispersive and Distributive MixingDispersive MixingDistributiveMixingMain
Intermix rotor designs(increased fill factor and shear flow)NR 5MainNR 2
Mixing Action “Banbury ”DistributiveDispersiveEven speed or friction operationMain
F-Series Banbury Mixers(tangential mixers)Even speed RotorAlignmentsMain
F-Series Banbury Mixers(tangential mixers)F series Banbury rotor typesST / SN4T4 wing / SKWFTMain2 wing
Feeding EfficiencyIntermix Vs. Banbury Main
Selected Items of ComparisonMechanical TANGENTIAL ROTOR DESIGNRam actuationHopper doorRam or weight designMixer rotorsMixer rotor end platesMixer sidesDrop door designDrop door latch mechanismDust stopsMainMainINTERMESHING ROTOR DESIGN1
Drop door designs of theIntermix Vs. Banbury a full extension of the bodybore for maximum shear workand heat transferIntermix MainContoured to be an extension ofthe body bore and relieved to permitmaterial transferBanbury
Mixer Metal TemperatureTemperature Control- Maximum Productivity- Optimum QualityHeat TransferMainOptimum Material Flow(Stick-Slip)
Intermix Chamber Water Cooled CavitiesTEMPERATURE CONTROLLEDWEIGHT STANDARDHIGH EFFICIENCYTEMPERATURE CONTROLLEDSIDESHIGH EFFICIENCYTEMPERATURE CONTROLLEDROTORSTEMPERATURE CONTROLLEDROTOR END PLATES STANDARDTEMPERATURE CONTROLLEDDOOR TOPMain
Intermix Rotor CoolingEnhanced spiral cooling passages over whole length of rotor bodyEnhanced cooling of NogMain
NR5 Rotor Spiral CoolingMain
Banbury Mixer Heating / Cooling“OPTIONAL” CORED WEIGHTFOR TEMPERATURE CONTROLHIGH EFFICIENCYTIP COOLED ST ROTORS“OPTIONAL” TEMPERATURECONTROLLED ROTOR ENDPLATES AND DUST STOPSMainHIGH EFFICIENCYTEMPERATURE CONTREOLLEDSIDESTEMPERATURECONTROLLEDDOOR TOP
Banbury Rotor Cooling(Tip Cooled Design)conventional rotor coolingMainST rotor cooling
Typical Ram Action and Power DemandBanbury Ram Actionand Power DemandIntermix Ram Actionand Power DemandMixerpowerMainMixerPower
PRIMARY VARIABLES AFFECTING BATCH MIXERS MainMaincompound formulationbatch weight / fill factormixing steps and proceduresmixer applied batch pressuremixer rpmmixer temper ( metal temperature control )compound component considerationsenvironmental effects1
Batch Size CalculationBATCH SIZE(THEORETICAL)batch wt. (net mixer volume)(density compd.)(fill factor)Fill factor (Intermix) 0.85 (fill factor(Banbury))MainMain1
BANBURY MixerNet Chamber Volume& Rotor Type(liters)NET MIXER VOLUME “ LITERS “Mainrotor type2 wing4wing ST Br- 16001.6-rotor type2 wing4 wing4 wing ST 57257F-370----414414F-620---652704
Intermix MixerNet Chamber Volume (nr-5) rotors(liters)Net Mixer volume “liters”Machine size K-0NR-2 rotors 1.64NR-5 rotors 1.82MainK-155.5K-2 K-2A18442049K-48291K-5126140K-6 K-6A K-7185 231 330205 257 330K-8436484K-10783870
Intermix Vs Banbury Batch Weight & fill FactorBanbury ST equipped mixer @ 50 psi batch pressureIntermix NR5 equipped mixer @ 75 psi batch pressure160140120ML 4@100 60.650.70.75FILL FACTORMain0.80.850.9
BANBURY BATCH WEIGHT & FILL FACTORAPPLIED BATCHPRESSUREMain
BANBURY Batch Pressure & ViscosityAPPLIEDBATCHPRESSURE( PSI )Main
Optimum fill factor(Banbury)% FILL VS PRODUCT VISCOSITY5048PRODUCTMOONEYML4464442PROPRIETARYNR SINGLE STEPMIX105 C DISCHARGE25 RPM25 PSI BATCHMain6769% FILL7480
“RPI” DATA(Banbury Data)1Aram position Vs timesmall batch weightMain1Bram position Vs time optimumbatch weight1Cram position Vs timelarge batch weight
Typical Ram Action and Power DemandBanbury Ram Actionand Power DemandIntermix Ram Actionand Power DemandMixerpowerMainMixerPower
“RPI” SYSTEMsignal conditionerRECORDERMain
Mix Topography &Process OptimizationINDICATED MIX TEMPERATUREMIXER POWERRAM POSITIONMain
Banbury Mixer RPM &Mix timeMain
Mixer RPM & 868482303540455560F-270 MIXER RPMMain65707580
Mixer RPM,TCU settings &Mooney Viscosity100Mixer rpm, Mixer temperature, MooneyViscosity, & Cycle time9090808070Legendcycle time 100% 10 minutesMooney 0-90 ML4std deviation 100% /- 66.770% of fullscale6070 F mixer5050404090 F mixer30302020140 F mixer10100283D mixer 2 wing rotor100 lb. #4SS Natural43 PSI batch pressureuniform feed @ approx. 10 Lb.chunks70 F feed temperaturedischarge @ 285 -300FMain605684mixer rpm0112mooneyML 4
Mix Cycle and MixerRPMMIX CYCLE FUNCTION DISTRIBUTION(POLYMER)loading4%low speed breakdown16%( TO PREVENTcooling60%STICKING ONTHE MILL)( FILLERS)Legendloadinglow speed breakdownhigh speed mixingram bumpcoolingMainram bump1%high speed mixing20%
Mixer Metal TemperatureTemperature Control- Maximum Productivity- Optimum QualityHeat TransferMainOptimum Material Flow(Stick-Slip)
Metal Temperature & Interfacialfriction effectsMain
SBR mixing,TCU settings& mix efficiencyMain
Mixing Action “Banbury ”DistributiveDispersiveEven speed or friction operationMain
ST Rotor PerformanceCure Uniformity and Rotor TemperatureTread Compound - Final MixF-270 4wSTmixer body @49 C (120 F)mixer door @ 27 C (81 F)fill factor @ 75%batch Pressure @ 4.1 bar (60 psi)mixer @ 30 rpm70 sec rm dn mix timerotor water @ 71 C (160 F)rotor water @ 60 C (140 F)Mainrotor water @ 49 C (120 F)
Temperature Control Unit“TCU”Main
Banbury Water Flow Rates( for maximum heat transfer)Main
Banbury TCU settings(starting points)Main
COMPONENT CONSIDERATIONS“Feed Form”(kW)(NR)(410)(298)(336)LBS. (50.9Kg)(298)PSI(261)(224)(32 ‘C)(121 (4.55)AVERAGE WEIGH OF RUBBER FEED UNIT - LBS.(KG)Main(45.5)
COMPONENT CONSIDERATIONS“environmental effects”NAT,L RUBBER MASTICATION10080* TEMPERATUREAVG POWER* HUMIDITYMOONEY REDUCTIION RATE% ofscalerange6040MIX TIMELegend--scale rangemix time 0-10 min.avg kw 0-200mooney reduction rate 0-10 M/min.200-10(14 F)4(40 F)21(70 F)RUBBER FEED TEMPERATURE DEGREES CENTIGRADEMain32(90 F)
Mixing Parameters, Steps and Procedures“The Art of Mixing Rubber”I MIXING STEPSIII MIXER OPERATING PARAMETERSSINGLE STEP MIX- conventional single step- upside down single step- process specific single stepMULTIPLE STEP MIX- premastication (optional )- masterbatch-simple single step mix-process specific single step mix- remill (optional )- final mix- % fill(batch weight)- temper- ram pressure-mixer speedII MIXING PROCEDURES- order of additions- number of additions- number of ram cleanings (brushes)- discharging procedures- rpm and batch pressure settings- means of controlMainCYCLE CONTROL-time- indicated temperature- energy (kwh)- torque (power hp or kw )
Mixe
CONTINUOUS MIXERS Specialty applications - high output - energy efficient - ease of process optimization - easily automated - uniform product shear & heat history - need free flowing feed (particulate rubber) - require sophisticated weigh & feed systems - not applicable for short runs - difficult to clean - capital intensive - need post mixer forming TWIN SCREW EXTRUDERS Newer technology .