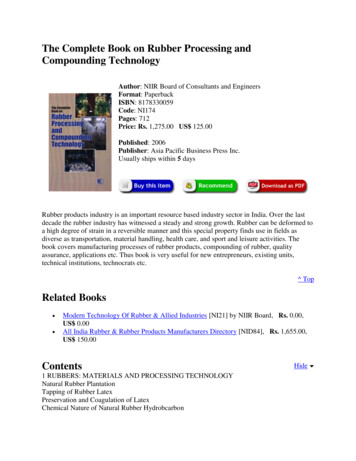
Transcription
The Complete Book on Rubber Processing andCompounding TechnologyAuthor: NIIR Board of Consultants and EngineersFormat: PaperbackISBN: 8178330059Code: NI174Pages: 712Price: Rs. 1,275.00 US 125.00Published: 2006Publisher: Asia Pacific Business Press Inc.Usually ships within 5 daysRubber products industry is an important resource based industry sector in India. Over the lastdecade the rubber industry has witnessed a steady and strong growth. Rubber can be deformed toa high degree of strain in a reversible manner and this special property finds use in fields asdiverse as transportation, material handling, health care, and sport and leisure activities. Thebook covers manufacturing processes of rubber products, compounding of rubber, qualityassurance, applications etc. Thus book is very useful for new entrepreneurs, existing units,technical institutions, technocrats etc. TopRelated Books Modern Technology Of Rubber & Allied Industries [NI21] by NIIR Board, Rs. 0.00,US 0.00All India Rubber & Rubber Products Manufacturers Directory [NID84], Rs. 1,655.00,US 150.00Contents1 RUBBERS: MATERIALS AND PROCESSING TECHNOLOGYNatural Rubber PlantationTapping of Rubber LatexPreservation and Coagulation of LatexChemical Nature of Natural Rubber HydrobcarbonHide
Hydrogenated RubberCyclized RubberChlorinated RubberRubbers from Stereo-regular Polymerization of Isoprene and ButadieneStyrene-Butadiene Rubber (SBR)Polychloroprene Rubber (CR)Nitrile Rubber (NBR)Butyl Rubber (IIR)Ethylene-Propylene-Diene Terpolymer (EPDM)Polysulphide Rubber (PSR)Polyacrylic Rubber or Acrylate Rubber (ACR)Fluorocarbon Rubber (FKM)IntroductionMastication and MixingOpen MillInternal MixersReclaimed tivatorsTyresBelting and HosesCellular Rubber ProductsMiscellaneous Applications of RubberPassenger TyreTube Compound for Car tyresConveyor BeltsInsulation Compound for CablesShoe Soles2 MIXING TECHNOLOGY OF RUBBERTwo-roll MillsInternal Batch MixersContinuous MixersAdvantages of continuous mixingDisadvantages of continuous mixingDevelopment of the Banbury MixerOperating VariablesRam PressureRotor SpeedBatch SizeCoolant TemperatureUnit Operations in MixingSingle-Pass Versus Multiple-Pass MixingTypes of Mix Cycle
Late Oil AdditionUpside-down MixingSandwich MixesAnalysis of Changes to the Mix ProcedureAcceleration of First-pass CompoundMill Mixing of Speciality CompoundsAcceleration in Line with Internal MixingTesting of Raw MaterialsElastomers as Raw MaterialsFillersPlasticisers and Process OilsSmall IngredientsControl of CompositionTracking the Mix CycleCompound TestingBasic SPC ChartingRheometer Data and its MeaningMixing Control SoftwarePeptisers in Natural RubberEffects of TemperatureEffects of TimeEffects of Use LevelEffects of Other AdditivesPeptisers in SBRPeptisers in Sulphur-containing PolymersAdditives to Increase ViscosityPreventing Unwanted Chemical ReactionsFiller TreatmentsBin Storage ProblemsInspection of Banbury MixersInspection at the Mezzanine LevelSide CoolingRotor CoolingRotors and BearingsRotor Bearing LubricationDust StopsDrop Door and LatchHydraulic SystemGrease SystemDust Stop LubricationDrive GearsCouplingsInspection of the Banbury PlatformRam and CylinderHeating WeightPiston Rod
Weight Pin AssemblyHopper DoorAir Line FilterHopper OperationMixer Maintenance and LubricationEach time the mixer is startedOnce per shiftOnce per dayOnce per weekOnce per monthEvery six monthsAnticipating Required ServiceDust Stop MaintenanceSSA Dust StopsAssemblyLappingRunningBanbury Mixer — Hydraulic Dust StopsAssemblyRun-inLappingProductionFlushingEPDM Expansion Joint CoverExpansion Joint Intermediate LayerTraffic Counter Treadle CoverSBR/IR Belt CoverEPDM Low Voltage Electrical ConnectorPeroxide-cured Black-filled EPDM CompoundsEPDM Concrete Pipe GasketInjection-moulded NBR GasketCR/SBR BlendLow Durometer CR/SBR BlendNon-black CR for Injection MouldingHard Rubber Industrial WheelHigh Durometer NBR MasterbatchNBR/PVC Cable JacketNBR/PVC/SBR BlendButyl MasterbatchButyl Masterbatch, Heat InteractedChlorobutyl/NR BlendCSM CORD JacketNon-black Millable UrethaneSome Major ChangesTempered WaterPower-controlled Mixing
Energy ConservationComposition of EPDM ElastomersVariables in EPM and EPDM ElastomersAverage Molecular WeightMolecular Weight DistributionEthylene/Propylene RatioType of DieneDiene LevelHow Processing Relates to Structure and RheologyPractical Guidelines for Mixing EP ElastomersUsing Internal MixersPolymer Composition and FormFiller/Oil Levels and TypesCure SystemsProcessing AidsMixing ProcessMixing InstructionsFill FactorMixing TemperatureMachine ParametersRam PressureCoolant TemperatureAutomationMachine ConditionDownstream Processing EquipmentUsing Two-roll MillsSummaryReworkPhase MixingNatural Rubber Viscosity ReductionMeasurement of Mixing EfficiencySpecial ConsiderationsRaw MaterialsTypical FormulationsInternal MixingMill MixingSummaryAccounting MethodsFarrel Continuous MixerOperating Principles of the FCMCommercial Applications for the FCMFarrel Mixing Venting Extruder (MVX)Designing the RotorAnalysis of Dispersive Mixing3 TECHNIQUES OF VULCANIZATIONPressureless Vulcanization
Rubber MouldingFactors of MoudingMouldinCompression MouldingTransfer MouldingInjection MouldingHelicureBuffed Tread CrumbIncineration and Pyrolysis of TyresReclaimed Rubber4 RUBBER VULCANIZATIONPhysical Property TestsFree Sulphur DeterminationSolvent-swell MethodMooney-Rivlin Equilibrium ModulusDifferential Scanning CalorimetryDetermination of Spring ConstantSulphur VulcanizationPeroxide CrosslinkingResin VulcanizationElectron Beam VulcanizationNitroso CompoundsMetal Oxides5 RUBBER COMPOUNDINGGeneral Compounding PrinciplesTensile StrengthTear ResistanceThe Crescent Tear TestThe Hardness of RubberSetAbrasion ResistanceFlex Cracking ResistanceResilienceHeat Build-upTemperature ResistanceTyresRetreading MaterialsConveyor Belting, Transmission Belting and HoseFootwearRubber RollerMedical Applications‘O’ rings and SealsRubber BlendsMaster BatchesChoice of RubberFillers
Vulcanizing RetardersSofteners and PlasticizersRubber CrumbFacticeProcessing AidsSpecial Purpose AdditivesUnvulcanized compound propertiesVulcanized compound properties6 RUBBER RECLAIMING7 MANUFACTURE OF RUBBER PRODUCTSClassificationComponentsTyre BuildingParts of a Conveyor BeltCover rubberManufacturing ProcessFinished belt testingPVC BeltingSteel Cord BeltingDesign of HosesHose ManufactureBraided/spiralled hosesTesting of HoseConstructionsV-Belt ManufactureMain Types of Power Transmission BeltsPreparation of IngredientsStability of Latex CompoundsManufacture of Latex ProductsFoaming and GellingVulcanizationClassification and TerminologyFabric Lined Water-proof ShoesCanvas ShoesMicro-cellular SolingManufacturing procedureTypes of Mountings8 LATEX AND FOAM RUBBERSelection of Raw MaterialsPreparation of Raw MaterialsCompounding and Design
MaturationProcessing and shapingDipped GoodsLatex ThreadVulcanisationHot Air CureHot Water VulcanisationAutoclave VulcanisationRadiation VulcanisationUltrasonic Wave CuringTesting of Rubber ProductsPacking and MarketingConclusions and RecommendationsManufacture of Latex FoamDunlop ProcessMechanism of GellingCompoundingFoaming and GellingConstruction of MouldsCuringWashingDryingFinishingCommon Defects in Foam MakingShrinkageFoam CollapseSettingComplete Distortion of the FoamProtein estimation protocolConlusion9 SILICONE RUBBERElectronics and Electrical IndustriesSilicone Rubbers to Mimic FleshSilicone PolymersSilicone Rubber ElastomersReinforcing FillersSemireinforcing or Extending FillersAdditivesCuring Dispersion Coating of Fabric
Heavy-duty HoseBondingBonding Unvulcanised Silicone RubberBonding Vulcanised Silicone RubberPost-bakingCondensation Cure—One-componentCondensation Cure—Two-componentAddition Cure10 POLYBUTADIENE AND POLYISOPRENEPolyisopreneCyclopolyisopreneGel and BranchingPolybutadieneIsopreneButadiene11 STYRENE BUTADIENE RUBBER (SBR)Raw MaterialsProduction of Hydrocarbon RubberManufacture of Emulsion SBRVinyl Content and BlockinessMolecular Weight and BranchingManufacture of Solution SBRProperty ControlBranchingBlendingPropertiesTg MeasurementMolecular-weight MeasurementDynamic Mechanical MeasurementsApplications of SBR12 RECLAIMED RUBBERWhole Tyre ReclaimDrab and Coloured ReclaimsButyl ReclaimScrap-rubber PreparationReclaimed RubberDigester ProcessReclaimator ProcessPan ProcessEngelke ProcessTesting and Evaluations of Reclaimed RubberMillroom OperationsSpecial Strengths Through ReclaimingFurther Advantages of Reclaiming - ApplicationsMajor Uses of Reclaimed Rubber
Automobile floor matSemi-pneumatic tyreButyl inner sation of Reclaimed Waste Latex Rubber (WLR)13 NITRILE AND POLYACRYLIC RUBBERUses of Nitrile RubberMixing and ProcessingLatest DevelopmentsCompositionRaw Polymer CharacteristicsPhysical CharacteristicsHeat, Fluid, Low-temperature ResistanceApplicationsCure SystemsReinforcing AgentsPlasticiscrsProcess d Storage StabilityVulcanisationBonding CharacteristicsSolution CharacteristicsBlendsFuture Developments14 RUBBER NATURALAgricultureExploitationLatex CompositionTypes and GradesProductionLatex ConcentrateProcessingChemistryPhysical PropertiesEconomic AspectsApplications15 HARD RUBBEREboniteHard Resin Rubbers16 RECYCLING OF RUBBERS
Reclaiming TechnologySurface TreatmentGrinding and Pulverization TechnologyMicrowave MethodUltrasonic MethodGeneral RemarksUse in New TiresRubber/Recycled Rubber BlendsThermoplastic-Recycled Rubber BlendE. Concrete Modified by Recycled RubberAsphalt Modified by Recycled RubberUse of Crumb Rubber in Soil TopSample ChaptersHide(Following is an extract of the content from the book)Mixing Technology of RubberINTRODUCTIONThis chapter deals broadly with the art and science of mixing rubber. Those unfamiliar with thenuts-and-bolts aspect of the industry may all too readily attribute artistic (or even magical)practice to the exotic ingredients and process techniques involved in manufacturing rubberarticles. Others who have experienced the frustration when a composition does not quite meet arequired physical property, lacks an anticipated attribute, or processes unsatisfactorily for noapparent reason, only to uncover remedies that are as difficult to explain as the symptoms, theywill understand the phrase 'art and science'. These occurrences do not detract from the scientificachievements that have driven the art of mixing to its current level of sophistication.The goal in mixing is to provide compositions having useful properties and suitableprocessability with as high a level of consistency as possible. The terms useful and suitable aredetermined by the application, for example, what is suitable for a sink stopper might not besuitable for an O-ring. In almost all applications there are criteria for the attributes thatcharacterise whether a composition is suitably mixed; the criteria may vary, but they existnonetheless. It is almost always the case that these criteria must be met with optimum efficiency,i.e., with the maximum output per expenditure of capital and energy.In order to understand the reasons for the techniques and types of machinery employed inmixing, one must have some familiarity with raw materials, their physical forms, functions in thecompound, and behaviour during processing. Several basic categories of ingredients are usuallydistinguished.
(a) Rubber or polymer-bales, clips, pellets or powder(b) Fillers-powder, pellets Reinforcing-carbonExtending - clay, calcium carbonate, talc(c) Plasticisers and lubricants-fluids, oils, waxes, process oil, ester plasticisers, processing aids,waxes, proprietary blends, stearic acid.(d) Miscellaneous additives-powder, pellets, fluids Antioxidants, antiozonantsColourantsRelease agents(e) Vulcanising agents and accelerators SulphurPeroxidesSpecial ingredientsA knowledge of physical characteristics and forms leads to a certain amount of guidanceregarding the most suitable type of mixer. For example, the knowledge that liquid additives needto be mixed into a liquid polymer would direct the technologist to certain types of equipment.But selection of the optimum mixer is not always possible, primarily because of economicfactors. The organisation must often make do with what happens to be available; the ingenuity ofthe compounder lies in his or her ability to achieve specific results with the equipment on hand.On the other hand, given some degree of choice a more appropriate machine is usually availableto improve mixing characteristics and, therefore, final properties. Early in the history of rubercompounding, almost simultaneously with Goodyear's discovery of sulphur vulcanisation it wasfound that kneading or softening the elastomer was useful in increasing its receptivity toincorporation of powders. This is the basis of mixing-masticating the elastomer to make itreceptive to other ingredients, yet retaining sufficient stiffness to ensure adequete dispersion.(The more difficult an ingredient is to disperse, the higher the viscosity required during mixing )This balance of mastication without undue shear softening can be achieved through severalmeans.1. Mixing with close temperature control.2. Use of a specific sequence for adding materials.3. In some cases, remixing after cooling (two-pass mixing).These three considerations apply to mixing with all the most common types of equipment: tworoll mills, internal batch mixers, continuous mixers, extruders or combinations thereof.
MIXING MACHINERY FOR RUBBERTwo-roll MillsEvery mixer must provide two basic functions, both equally important-acceptable dispersion(intensive or dispersive mixing) and high uniformity (extensive or distributive mixing). Theequipment used
Farrel Continuous Mixer Operating Principles of the FCM Commercial Applications for the FCM Farrel Mixing Venting Extruder (MVX) Designing the Rotor Analysis of Dispersive Mixing 3 TECHNIQUES OF VULCANIZATION Pressureless Vulcanization .