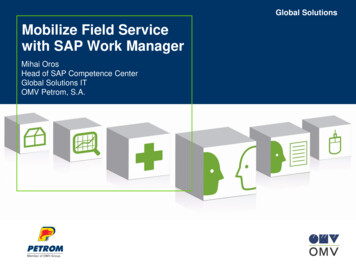
Transcription
Global SolutionsMobilize Field Servicewith SAP Work ManagerMihai OrosHead of SAP Competence CenterGlobal Solutions ITOMV Petrom, S.A.
ContentsOMV at a glanceWhere did we start?What did we do?Where are we now?Key take away
OMV at a glance
OMV at a glance Key figures:
OMV Business Segments
E&P: explores, discovers and producesoil and gas worldwide
SAP Competence Center highest priority is tosafeguard the stable operation of SAP IT solutionsPart of Global Solutions IT -the internal Shared Service Center for OMVGroup Approx. 110 employees in Vienna and Bucharest Main tasks: Optimize the efficiency of SAP operations Support the implementation of new business requirements
Supporting more than 9.000 sap users in morethan 14 countries SAP Products in use:SAP ECC 6.0IS-OilIS-RetailSAP ERP HCMESS/MSSSAP SRMSAP APOSAP NetWeaverBWSAPBusinessObjectssolutionsSAP solutions forGRCSAP NetWeaverPortalSAP SolutionManagerSAP WorkManager
Where did we start?
Situation before the projectOMV Petrom Exploration & Production Maintenance business unit inRomania is using standard Plant Maintenance (SAP ERP) to manageapprox. 200.000 work orders per year.Maintainable facilities Flow lines & pipelines: 25,000 km Productive oil wells: 7000 Productive gas wells: 600 Water injection wells: 700 Gathering stations: 600 Gas processing units: 30 Tank farms: 50 Compressor stations: 100
Process Pain points Planners prepare & provide working package to technicians via paperTechnicians execute works and write details ofexecuted work on paper work package ( fault codes /catalogue, summary of executed work; split of activitytimings; corrective notification if needed)Paper is reviewed by Quality InspectorTechnicians return work package to planners within2 to 3 days after work completionWork package provided is most of the timeincomplete, resulting in false data analysis resultingin ineffective actions taken to improve maintenanceactivities
What did we do?
Simplifying Work Order ProcessWhy? Avoid printing papers, physical hand-over of documentation, phonecommunications, a lot of travel time for the different actors involved, that inthe current process lead to delays and alignment disruptionsWhat? Implementation of a State of the Art Mobile application for plantmanagement (SAP ERP) and Field Service that will easily allow the fieldworkers and quality inspectors to access SAP data (Work Orders,Notifications, Contracts, Master Data ) and remotely record Services,Activities and Materials ConsumptionHow? Assure the on-line and also off-line access to the relevant SAP PM data forthe field workers for: Instant data entry Location-independent Improved data quality through prevention of transfer errors
Where are we now?
Assignment of workorderAccess of work orderinformationTechnicaldocumentation andwork time confirmationTechnical acceptance Work orders are assigned to Quality Inspectors by responsibleplanner and the orders are put in daily schedule
Assignment of workorderAccess of work orderinformationTechnicaldocumentation andwork time confirmation On the work place the QualityInspector starts the work order usinghis laptop without connectivityTechnical acceptance
Assignment of workorderAccess of work orderinformationTechnicaldocumentation andwork time confirmationTechnical acceptance After the work is released, Quality Inspector creates timeconfirmation, completes the notification and documents executedactivities.
Assignment of workorderAccess of work orderinformationTechnicaldocumentation andwork time confirmationTechnical acceptance All the information regarding the job is transferred to SAP PM inreal time (when connectivity is available) so the work order couldbe verified by planner and closed in time
Key take away
Project TimelinesSAP Work Manager solution was successfullyimplemented with minor enhancements in a veryshort span of 5 weeks from the workshops to theGo-Live leveraging Atos Deployment Solutionsfor Mobility.
Key take away1Stick to the standard Allows quick project duration Immediate benefits available Atos standard solution available2Keep it simple Ease the usage for technicians Decrease implementation effort Lower effort for operations3Step by step Continuous improvement – phasedapproach Learning by doing (real field experience)
SAP Work Manager solution was successfully implemented with minor enhancements in a very short span of 5 weeks from the workshops to the G