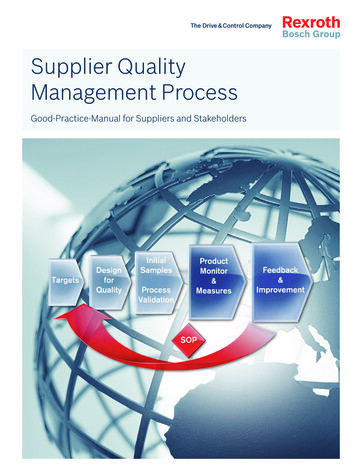
Transcription
Supplier QualityManagement ProcessGood-Practice-Manual for Suppliers and Stakeholders
2PrefaceQuality is a key ingredient for success for the Rexroth brand.This is because in the industries that we supply, customers and theirend users have high expectations of our products.Our target is to satisfy the expectations of our custo-This Good-Practice-Manual describes comprehensiblymers with “Best-in-Class” quality!the most important aspects of this quality framework.First, the manual provides information on our “SupplierThe early involvement of suppliers and the intensiveQuality Management Process” (SQM), and, second, youcooperation already during the Product Engineeringwill find guidelines to which we expect compliance fromProcess (PEP) before the series production plays anour suppliers and employees to the same degree.important role in order to achieve outstanding qualityin the entire value stream for products and processes.We have defined the nature of reliable processesbetween Bosch Rexroth and its suppliers and whatFor several years we embarked on the path in a qualitymethods must be adopted to guarantee long-lastingpartnership with suppliers which is based on openquality.communication. For this reason we are confidentthat we remain jointly successful on the market. ThisSuppliers in our quality partnership understand this andis also shown due to the exemplary developed keythey actively practice the process for implementationperformance indicators of suppliers, who already workand continuous improvement.according to the new processes intensively.„Number-One-in-Quality“ requires courage, disciplineand consistency from all of us.DC/PUDC/PUQHead of PurchasingHead of Purchasing Quality ManagementLutz BergManfred Zerbe
3AimThis Good-Practice Manual defines the tasks for the co operation between Bosch Rexroth and its suppliers in03AimApplication areaResponsibilityShort description04SQM process description and details06Typical customer requirements07Quality expectations for our suppliers08Overview GPc09-23Description GPc24Matrix of responsibilities andprocess activities26Appendix GPc 6:Supplier Quality Plan (SQP)28Appendix GPc 7:Check list Specificationup-to-date & complete29Appendix GPc 8/9:Check list TSR and feasibilityconfirmation supplier30Other valid documents31-33Glossaryrespect to quality assurance for products (products, rawmaterials and trade goods) and from the selection of suitable suppliers to the monitoring and improvement in theseries production.Application areaThe Good-Practice Manual is applied to projectsand processes in the supply management between BoschRexroth AG, its subsidiaries, and the respective suppliers.ResponsibilityPurchasing quality management is responsible for the content and management of this manual.All Bosch Rexroth business units contribute to the development and improvement of this manual.Short descriptionThe Bosch Rexroth Supplier Quality Management Processdescribes the following procedures: Selection of suppliers and their qualification Quality development & engineering with suppliers andquality performance contracts Initial sample inspection and parts approval Series production, series delivery and changemanagement Key performance evaluation and targeting process, aswell as in case of deviations from Bosch Rexroth requirements Feedback on all phases of process and continuousimprovement
4SQM Process Description and DetailsDCCD 08016-41DCCD 08016-43Supplier selectionContracting & parts releaseDCCD 08016-42Qualification, enabling and development of suppliersPlanning &Engineering &Parts &PreparationContracting*Process ApprovalSupplier approvedfor RfQTechnicalSourcing ReviewFeasibility ConfirmationSupplier Key Product Characteristics GPc 3 Certificate CheckingParts release: Lessons learned GPc 5 Q-System accepted (QAA) Initial sample inspection Supplier Quality Plan SQP GPc 6 Supplier evaluation(ISIR Point CIP) GPc 12 Specification up-to-date & Requirement profile product, Installation testcomplete GPc 7material(fit, form, function) TSR GPc 8 Q-Targets: Feasibility Confirmation GPc 9- incidents/mio pProcess release: Contracting- ppm System validation FMEA- initial sample recursions Product Process Approval Inspection plan GPc 10(PPAP on customer request) Design validatedGPc 16 Ramp-up (Run@Rate forQB0QB1QB2QB3automotive industry oncustomer request) GPc 20
5Internal central departmentdirectives (DCCD) outline allDCCD 08016-44phases of the ProcurementFirst standard deliveries, Purchasing after SOPProcess. The main goal is tomost effectively support development activities and continuous product improvementthroughout the life-cycle of theproduct.DCCD 08016-45Key performance indicators & policy deploymentSOPProduct Monitoring &Feedback &MeasuresImprovementProduct ProcessApprovalConformityassuredTo optimize cooperation with Parts inspection Process auditsuppliers, important delive- SPC Supplier Developmentrables are described as Good Target and key performance AwardsPractices. The focus of these Quality Programs“GPc’s” is prevention throughtracking (Incidents/mio p,ppm, PUE ppm, initial sample(Q focus program, supplierjoint reviews with suppliers.recursions) GPc 17 and 18learning factory)They are continuously revised Change request (ECR) GPc 23 SRM (Supplier RelationshipManagement)and updated, if necessary. CIP Claims management Process improvement reviewGPc 218D-Reports incl. assessments Early warning systems (Q-Alert)QB4QB5QBs are linked to ProductEngineering Process PEP*Based on the project targets andcustomer requirements
6Typical Customer Requirements Zero-defect target Safety stock, ability to supply and capacity consent Validation of key product characteristics PEP in reconciliation with customer (e.g. PPAP) Ship-to-line concepts Close control of processes at supplier Processing of complaints according to 8D method Take over external failure costs Management System (e.g. ISO 9001) Efficient escalation processes
7Quality expectations for our suppliersIncoming Inspection Optimized quality assurance measures and inspections at supplier Avoid double-work without compromising quality Target: Ship-to-stock / Ship-to-line If failures occur: 8D with root cause analysis (technical/managerial)Initial Samples Initial samples are perfect – avoid recursions Supplier self-declaration of part conformity (warrant): confirmation,all requirements fulfilled Use part family releases instead of single ISIR No need for DC to confirm dimensions submitted by a supplier (establish trust)Capability and Audits Self-driven measures for continuous improvement and control plans 8D failure cluster analysis Process capabilities, process reviews, sustainable failure prevention Use 3rd party audits to improve your processesWe expect that our suppliers take initiative!
8Overview Good Practices “GPc”Key Product CharacteristicsGPc 3Lessons Learned Similar Products and ProjectsGPc 5Supplier Quality Plan (SQP) – Quality Planning during ProcurementGPc 6Specification up-to-date & completeGPc 7Technical Sourcing Review (TSR)GPc 8Feasibility Confirmation of SupplierGPc 9Inspection planningGPc 10Initial sample inspectionGPc 12Production Process Approval – (PPAP on customer request)GPc 16Key Performance Indication and Policy Deployment – out of preventive Quality AssuranceGPc 17Key Performance Indication and Policy Deployment – after SOPGPc 18Safe Launch: Risk Management for New Suppliers, Material/TechnologiesGPc 20Auditing of suppliersGPc 21Sub-Supplier Quality ManagementGPc 22ECR in PurchasingGPc 23Note: GPc available in SOCOS at 07416-XXX (http://inside.bosch.com/alias/dc/gpc-manual-EN)
9GPc 3Key Product CharacteristicsTask OwnerDevelopment1. DescriptionProduct characteristics or production process parameter which effect safety, compliance ofofficial regulations, correct fit, form, function or further processing are “Key Product Characteristics”. These are identified by R&D Department. Suppliers considers these in his manufacturingprocesses.2. ResultKey Product Characteristics are documented and clearly marked in drawings or specifications asreference for validation and part release (e.g. critical characteristics).3. Area of applicationDrawing related parts and components. SQP Scope 2 & 34. Due dateDefinition prior to RfQ. Verification of the process control measures to insure KPC‘s during ISIR,FMEA or process audit resp. process approval (GPc 16).5. Possible inputPossible input:Responsible for input: Check list DCGP 3Project Purchasing, Development,Purchasing Quality Up-to-date drawings (incl. Key ProductCharacteristics), parts lists, materialspecificationsDevelopment Specifications under consideration ofstandards and regulationsDevelopment Lessons learned, complaint book ofsimilar products (end of line, 0-km, field)Project Purchasing, Supplier Product characteristicsDevelopment, Supplier Critical failure mode from D-FMEADevelopmentReference:6. Method Potential Key Product Characteristics are identified and documented by development atDesign FMEA Technical purchasing provides the supplier drawings incl. Key Product Characteristics as wellas failure mode and impacts (from Design FMEA) as part of RfQ Supplier verifies feasibility of process control Supplier conducts Process FMEA Supplier implements appropriate measures to ensure Key Product Characteristics into manufacturing process after discussion with Bosch Rexroth (generally project purchasing) Supplier verifies consideration of KPC s during ISIR and Process Approval (GPc 16), contracting and parts releaseOther valid regulations CDQ0306 DCCD 08016-43 DCCD 08914-1 DCCD 08914-2
10GPc 5Lessons LearnedSimilar Products and ProjectsTask OwnerProject Purchasing1. DescriptionAnalysis of all internal or external defects and weak points based on a complaint list includingpossible counter measures. Implementation of counter measures in new processes.2. ResultProduction and logistics are able to address existing and potential failures through preventiveaction. Feedback for new developments and continuous improvement for existing parts is communicated to development and manufacturing planning.3. Area of applicationDrawing related parts and components, SQP Scope 2 & 34. Due dateAt Technical Sourcing Review (QB2), latest before series tool release or Process FMEA.5. Possible inputPossible input:Responsible for input: Defects and weak points at manufacturingprocess (QAM)Manufacturing/Assembly Process FMEA or auditsManufacturing/AssemblyPUQ Techn. Service Complaint list (internal & external)Quality, Supplier, Purch. Q-Mgmt.,Manufacturing/Assembly 8D ReportManufacturing/Assembly,Purchasing Quality Mgmt. Work instructions for productionManufacturing/Assembly, internal Inspection planInternal, Supplier Parts validation resultsDevelopmentReference:6. Method Analysis of main faults in production (manufacturing/assembly) Possible failures and corrective actions from QAM or 8D Report to be considered Complaint list of faults and corrective actions to be completed Checking current production status by means of additional parts sampling is also possible Process FMEA to be completed Prepare a ‘Lessons learned check list’ for external use Transfer to supplier for consideration in his process planning and confirmation of feasibility(GPc 9) Lessons learned to be part of supplier employee training and work instructions Inspection plan to be updated Supplier implements counter measures latest before Process Approval (GPc 16)Other valid regulations CDQ0517 DCCD 08958 DCCD 08016-43
11GPc 6Supplier Quality Plan (SQP) –Quality Planning during ProcurementTask OwnerProject Purchasing1. DescriptionTime table of sourcing process including all quality related deliverables and responsibilities. Monitoringof deviation. The SQP has to be in line with the overall project schedule.2. ResultAll necessary actions until SOP are known and scheduled. Responsibilities are defined. Bindingresource planning.3. Area of applicationFor all parts (drawing related parts and components, catalogue and company standard parts).SQP Scope 1 - 34. Due dateDraft after project start (QB1). Detailed SQP after TSR (Technical Sourcing Review), beforeinitial sample order.5. Possible InputPossible input:Responsible for input:Reference: SQP master documentProject PurchasingAppendix GPc 6 Project schedulesProject Leader Up-to-date drawings (incl. Key ProductCharacteristics), Bills of Material (BOM),material specificationsDevelopment Decision of SQP Scope 1 - 3Project Purchasing & Development Technical requirements, specifications(incl. prototype tests)Development, Project Leader Validation plan / approval planDevelopment, Project Leader Responsibilities of project team membersProject Leader LPACommodity Purchasing6. Method Project Purchasing, PUQ Technical Services and development decide SQP Scopefor components DIN, standard parts and assemblies (all single parts released) are SQP Scope 1 In case of SQP Scope 3 collaboration of PUQ Technical Services is required (contracting) Adopt SQP master document based on sourcing process details such as specifications,validation plan, LPA results and parts release Propose back scheduling based on project / sub-project plan Propose responsible person for each task in SQP Overall resource planning and request for additional capacity if required Responsible persons to confirm task deadlines of SQP (incl. supplier) Monitor and update SQP Set up action plan in case of deviations from project planOther valid regulations DCCD 08016-43Key ProductCharacteristicsGPc 3Lessons LearnedGPc 5Inspection PlanningGPc 10Initial SampleInspectionGPc 12Safe LaunchGPc 20Spec. up-to-date& completeGPc 7Technical SourcingReview (TSR)GPc 8FeasibilityConfirma tion ofSupplier
SRM (Supplier Relationship Management) Claims management 8D-Reports incl. assessments Early warning systems (Q-Alert) Process audit Supplier Development Awards Quality Programs (Q focus program, supplier learning factory) Change request (ECR) GPc 23 CIP Process improvement review GPc 21 QBs are linked to Product Engineering Process PEP DCCD 08016-43 Contracting & parts release