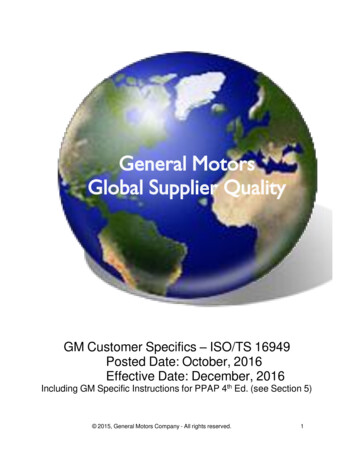
Transcription
General MotorsGlobal Supplier QualityGM Customer Specifics – ISO/TS 16949Posted Date: October, 2016Effective Date: December, 2016Including GM Specific Instructions for PPAP 4th Ed. (see Section 5) 2015, General Motors Company - All rights reserved.1
PrefaceGeneral Motors Customer Specific Requirements - ISO/TS16949Including GM Specific Instructions for PPAP 4th Ed. (see Section 5)NOTE: A revision history to the November 2014 Edition is also provided. However, it is theorganization’s responsibility to review and apply the requirements of this document. 2015, General Motors Company - All rights reserved.2
Table of ContentsRevision History .71.0 Scope 122.0 References . .123.0 Definitions . .13Accredited Laboratory - 3.1. . 13Active Part – 3 . . . 13Aftermarket Part(s) – 3.3 . . . . . 13Consulting – 3.4 . . . . . . 13Customer – 3.5 . .,., . . . . 13Ergonomics – 3.6 . . .13Initial Process Study – 3.7 . .14PPM (Parts Per Million – 3.8 . . .14S-IpB (Severtiy Incidents per Billion – 3.9 .14Quality Indices – 3.10 . . .14Organization – 3.11 . . . .15Service Parts – 3.12 . . . .15Suppliers – 3.13 . . .15Value-added Production Parts – 3.14 154. 0 Requirements . . 16ISO TS 16949:2009 (Third Edition) June 2009 -Related Requirements - 4.1 . . 16Management of production tooling – 4.1.1 . 16 2015, General Motors Company - All rights reserved.3
Records Retention – 4.1.2 . 16Electronic Communication – 4.1.3 . 16Shipment Notification System – 4.1.4 . . .16Special Characteristics – 4.1.5 . . .16Design Changes – 4.1.6 . . 16Official Language Version – 4.1.7 . .17Part Approval Process – 4.1.8 . . .17Customer Satisfaction – 4.1.9 . 17Internal Auditor Qualifications – 4.1.10 . .17Supplier Quality Management System Development – 4.1.11 .17Customer Acceptance of 2nd Party Audits and Criteria for Approval4.1.11.1 .18Supplier Development of Specially Designated Small Suppliers4.1.11.2 . .18Heat Treating Processes – 4.1.12 .19Plating Processes – 4.1.13 .19Coating Processes – 4.1.14 .19Plastic Molding Processes – 4.1.15 . 20Solder Processes – 4.1.16 20BIQS Essential Requirements – 4.1.17 thru 4.1.28 21-25Verification Station/Final Inspection /CARE / GP12 – 4.1.29 .25General Motors – Specific Requirements – 4.2 .25Third Party Registration Requirements – 4.2.1 . 25General Procedures and Other Requirements – 4.2.2 .26 2015, General Motors Company - All rights reserved.4
IS0/TS 16949:2009 Applicability – 4.2.3 . 26UPC Labeling for Commercial Service Applications – 4.2.4 .27Layout Inspection and Functional Test – 4.2.5 .27Customer Signature on Control Plan – 4.2.6 27Certification Body Notification and Certification Status – “New Business Hold –Quality” – 4.2.7 .27Controlled Shipping Level II (CSII) – Notice to Certification Body – 4.2.8 .28Management Review 4.2.9 .285.0 PPAP – GM Specific Instructions 29Applicability – 5.1 (including Service Parts note) .29Requirements for Approval – 5.2 , 29PSW Form – 5.2.1 . .29Acceptance Approval Report – 5.2.2 . 29Sample Production Parts – 5.2.3 .30Control Plans – 5.2.4 30Design Records – 5.2.5 . 30Design Failure Mode and Effects Analysis - 5.2.6 31Material/Performance Test Results – 5.2.7 .31International Material Data System (IMDS) 5.2.7.1. 31Customer Notification of Supplier - Initiated Changes – 5.2.8 .32Submission Levels – 5.2.9 .32Part Submission Status – 5.3 . 32Approved 5.3.1 . . 32 2015, General Motors Company - All rights reserved.5
Saleable PPAP – 5.3.2 .32Examples of Saleable PPAP - 5.3.2.1 . 33Non-Saleable PPAP – 5.3.3 33Examples of Non-Saleable PPAP – 5.3.3.1 .33Rejected PPAP - 5.3.4. .34SQMS Action Plan - 5.5. . .34 2015, General Motors Company - All rights reserved.6
Revision History - March 2006 to current editionDateSectionRevisionMarch 20063.8 PPM Parts PerMillionMethod of calculating PPM explained.March 20064.1.5 SpecialCharacteristicsNote added: GMW 15049 replacesGM 1805 QN for all global programsbeginning with 2009 MY and all otherprograms beginning in 2010.March 20064.1.12 HeatTreatingProcessesJune 20064.1.12 HeatTreatingProcessesNote 1 revised: Implementation is 90days following the effective date of therelease of CQI-9 Special Process:Heat Treat System Assessment(HTSA). Based on the release date ofCQI-9, the effective date ofimplementation is August 1, 2006Note 3 added: Implementationeffectiveness should be based onevidence that the organization has aprocess in place that includeselements such as auditors identified,schedule for self-assessment in placeincluding schedule adherence, supplierdevelopment process identified forapplicable suppliers, monitoring ofprogress, defined corrective actionprocess and record-keeping. 2015, General Motors Company - All rights reserved.7
DateSectionRevisionMarch 20064.2.2.10 KeyCharacteristicDesignationSystem (KCDS)(GM 1805 QN)4.2.8 CertificationBody Notificationand CertificationStatus – NewBusiness Hold –QualityNote added: GMW 15049 replacesGM 1805 QN for all global programsbeginning with 2009 MY and all otherprograms beginning in 2010.March 20064.2.8 CertificationBody Notificationand CertificationStatus – NewBusiness Hold –QualityNote 4 added: When an organizationis placed in CSII after a recertificationsite audit but before the certificate forrecertification is issued:1. The Certification Body shall issuea major nonconformance against theorganization which shall be closed outin accord with the 90 dayrequirement.2. The Certification Body shall issuethe new certificate in accord with theIATF Rules with this majornonconformance open.June 20064.1.12 HeatTreatingProcessesNote 1 revised to include: Based on therelease date of CQI-9, the effective dateof implementation is August 1, 2006.June 20063.8 PPM Partsper MillionPPM clarified: PPM for a GM supplyorganization is impacted when both of thefollowing conditions exist:March 2006Note 3 added: When an organizationis placed in NBH after a recertificationsite audit but before the certificate forrecertification is issued:1. The Certification Body shall issuethe certificate in accord with the IATFRules.2. The Certification Body shall thenplace the new certificate in immediatesuspension with the rules for liftingsuch suspension appropriatelyapplied.1.Quality PRR is written with 2015, General Motors Company - All rights reserved.8
DateSectionRevision quantity discrepant andTherearereceiptsforreferenced part and dunsnumber within the previoustwelve months.PPM for a supplier manufacturingduns is calculated monthly usingthe following formula:2.Total all the “estimated quantitynonconforming” for all partnumbers for that locationNote:Actualquantitynonconforming is used forsupplier initiated PRR’s.Divide by total receipts for thatlocationMultiply by 1,000,000.3.August 20064.1.2 RecordsRetentionMay 20071 Scope2 References3.10 Organization3.12 Suppliers4.1.7 OfficialLanguage Version4.1.11.1CustomerAcceptance ofQS-9000:19984.2.1 Third- PartyRegistrationRequirements3.1 AccreditedLaboratoryMay 2007Note revised: The customer or procuringdivision may specify alternative recordretention periods applicable todesignated holders of GM BusinessRecords.QS-9000 references and applicabilityremoved. QS-9000 expired December15, 2006.NOTE: 4.1.11.1 and 4.1.11.2 reflect newheading titles based on removal ofCustomer Acceptance of QS-9000:1998(formerly 4.1.11.1),Clarified and updated to reflect ISO17011 having replaced Guide 58. 2015, General Motors Company - All rights reserved.9
DateSectionRevisionMay 20075.2.1 PSW FormNote revised as follows . . . FinalGM 1829, GM 1411, AAR(s) etc.,(as required) shall be attached tothe correct sample . . .May 20075.2.7 Material /Performance TestResults5.2.7. 1InternationalMaterial DataSystem (IMDS)5.3.2 SaleablePPAPExtensive revision to verbiage ofnumbers 1. 2. 3; includingresponsibilities and processNote: Links to additional informationaddedMay 20075.4 Driver CodesMay 20075.4 Driver CodesSeptember20074.1.12 HeatTreatingProcesses4.1.13 PlatingProcesses4.1.14 CoatingProcesses1. Scope#3 – Link to Driver Code Matrixadded#4 – Link to Driver Code MatrixdeletedRevised to include CQI-9 2ndEdition, Heat Treat SystemAssessment (HTSA)Added to include CQI-11, PlatingSystem Assessment (PSA)Added to include CQI-12, CoatingSystem Assessment (CSA)NOTE for clarification added2. ReferencesUpdated list of documents published4.2.2 GeneralProcedures4.2.3 ISO/TS16949:2009Applicability /Note4.2.25.2.1GeneralDocumentClarificationMay 2007May er2008September2008September2008Oct. 2010Oct. 2010Oct. 2010#2 – grammar correctionsClarificationUpdated listPart 4 revisedUpdated editions of ISO/TS16949,TS Rules, ISO 9001; Updated Tableof Contents; Updated References;Updated GP procedures. 2015, General Motors Company - All rights reserved.10
ry2014Section 3.9Updated the editions of TS Rules.Table of contents, Reference Docsin Section 2, GP Procedures.Definition of Severity incidents perBillion (S-IpB) addedJanuary2015 Section 4.1Added 4.1.15, Plastic Molding selfassessment using AIAG CQI-23January2015Section 4.1January2015Section 5Posted:May 2015Section 4.1.2Section 4.1.16Section 4.1.29Section 5.2.1Section 5.2.5Section 5.2.7.1Added 4.1.16 thru 4.1.27 BIQSessential requirements includingguidance on application andcompliance: LOOK AT/LOOK FORNote added on Service PPAPapplication; Removed GM 1411Worksheet and instructions. Usersshould use GM Supply Power link.Revised record retentionAdded 4.1.16, Solder ProcessesMolding Assessment using AIAGCQI-17Added 4.1.29 BIQS EssentialrequirementsRevised PSW part numberrequirementsRevised marked drawing statusUpdate to IMDS requirementsEffective:July 2015October2016Section 4.1.2Section 4.2.2Section 4.2.9Section 4.2.10Section 4.2.11Section 5.2.1Section 5.2.7Section 5.3Section 5.4Section 5.5Revised record retention to reflectGM15920.Updated General Procedures andOther Requirements to the properGM 1927 document names.Added BIQS/QSB revocationnotification.Added BIQS/QSB certificationrequirement.Moved Management Review to4.2.11.Updated GQTS to SQMS and GM1411 Worksheet to SQMS ActionPlan where appropriate.Removed “Driver Codes” section 5.4and all references.Addition of the English language 2015, General Motors Company - All rights reserved.being mandatory for SQMS ActionPlans.11
1.ScopeISO/TS 16949:2009, Second Edition, June 15, 2009, “Quality management systems – Particularrequirements for the application of ISO 9001:2008 for automotive production and relevant service partorganizations,” and this document define General Motors fundamental quality system requirements fororganizations where automotive customer-specified parts, for production and/or service aremanufactured. Third party certification to ISO/TS 16949 shall meet the following conditions: The certification scope must include both ISO/TS 16949 and the accompanying ISO/TS 16949GM-Customer Specific Requirements, The certification must be conducted in compliance with the IATF recognized automotivecertification scheme by a certification body currently contracted and recognized by an IATFOversight office.All ISO/TS 16949:2009 requirements including the requirements of this document shall be addressed inthe organization’s quality management system.2.References2.1Chrysler, Ford Motor, General Motors Production Part Approval Process PPAP, FourthEdition, March 2006.2.2Chrysler, Ford Motor, General Motors Statistical Process Control (SPC),Second Edition, July 2005.2.3Chrysler, Ford Motor, General Motors Advanced Product Quality Planning and Control Plan,APQP Second Edition July 2008. Chrysler, Ford Motor, General Motors MeasurementSystems Analysis, MSA Fourth Edition, June 20102.4Chrysler, Ford Motor, General Motors Potential Failure Mode and Effects Analysis, FMEAFourth Edition, July 2008.2.6Automotive Certification Scheme for ISO/TS 16949:, Rules for Achieving IATFRecognition, Fourth Edition for ISO/TS 16949: November 20132.7ISO/TS 16949:2009, 3rd Edition, June 20092.8Minimum Automotive Quality Management System Requirements for Sub-tierSuppliers, April 2013The list above contains the most current editions. However, the latest edition or most current versionof the reference documents listed applies unless otherwise specified by the GM ProcuringDivision. Copies of PPAP, APQP, FMEA, MSA, SPC, ISO/TS 16949 Rules, , and ISO/TS 16949:2009and other related manuals are available from AIAG at www.AIAG.org. Copies of ISO documents areavailable from the American National Standards Institute (ANSI) at webstore.ansi.org.Certain documents listed above are requirements documents and are described as such insection 4 of this document. Section 5 of this document contains the GM PPAP SpecificInstructions. PPAP is a requirements document. 2015, General Motors Company - All rights reserved.12
3.DefinitionsWhere inconsistent terminology exists between ISO/TS 16949:2009 and this document, this documentshall take precedence. Otherwise the definitions from ISO/TS 16949:2009 apply to this document.3.1Accredited LaboratoryAn accredited laboratory is one that has been independently evaluated for technical competence. Thecriteria for evaluation are based on ISO/IEC 17025, or national equivalent. Accreditation is performed byqualified agencies (public or private) operating in accordance with ISO/IEC 17011.NOTE: The above definition also applies to the reference manuals in Section 2 of this documentand currently in effect.3.2Active PartAn active part is one currently being supplied to the customer for original equipment or serviceapplications. The part remains active until tooling scrap authorization is given by the appropriatecustomer activity. For parts with no customer-owned tooling or situations where multiple parts are madefrom the same tool, written confirmation from the customer Purchasing activity is required to deactivate apart.NOTE: For bulk material, “active part” refers to the bulk material contracted, not the parts thatare subsequently produced from that material.3.3Aftermarket PartsAftermarket parts are replacement parts not procured or released by OEM for service part applicationswhich may or may not be produced to original equipment specifications.3.4ConsultingFor the purposes of TS16949:2009, consulting is the provision of training, documentation development,or assistance with implementation of quality systems to a specific customer. If these activities are opento the public, advertised, and not customer specific, they are considered training rather than consulting.Other products, processes or services may be offered directly or indirectly, provided they do notcompromise confidentiality or the objectivity or impartiality of its certification process or decisions. Referto the most current version of Automotive Certification Scheme for ISO/TS 16949 Rules, (Currently inthe 4th Edition). Also see ISO/IEC 17021.3.5CustomerReferences to “customer” in ISO/TS 16949:2009 and this document shall be interpreted as the ProcuringDivision of General Motors for suppliers pursuing third party registration to ISO/TS 16949:2009 to satisfyGeneral Motors sourcing requirements third party quality system assessment registration.3.6ErgonomicsErgonomics is the evaluation of the design of a product or process to assure compatibility with thecapabilities of human beings. Analysis of motion refers to capabilities of people with respect to tasks(e.g. lifting, twisting, reaching) to prevent or relieve problems of strain, stress, excessive fatigue, etc.Factors involved include anatomical dimensions of the worker, placement of products to be workedupon, placement of buttons/switches, physical loads imposed on the worker, and environmental effectssuch as noise, vibration, lighting and space. 2015, General Motors Company - All rights reserved.13
3.7Initial Process StudyInitial Process Studies are short-term studies conducted to obtain early information on the performanceof new or revised processes relative to internal or customer requirements. In many cases, preliminarystudies should be conducted at several points in the evolution of new processes (e.g. at the equipmentor tooling subcontractor’s plant, after installation at the supplier’s plant). These studies should be basedon as many measures as possible. When utilizing X-Bar and R charts, at least twenty-five subgroups(minimum of four pieces per sub-group) are required to obtain sufficient data for decision-making.When this amount of data is not available, control charts should be started with whatever data isavailable, or contact the authorized customer representative to develop a suitable plan. See also theProduction Part Approval Process (PPAP) in Section 5.NOTE: Initial Process Studies. The purpose of the initial process study is to understand theprocess variation, not just to achieve a specific index value. When historical data are availableor enough initial data exist to plot a control chart (at least 100 individual samples), Cpk can becalculated when the process is stable. Otherwise, for processes with known and predictablespecial causes and output meeting specifications, Ppk should be used. When not enough dataare available ( 100 samples) or there are unknown sources of variation, contact the authorizedcustomer representative to develop a suitable plan.3.8PPM (Parts per Million)PPM for a GM supply organization is impacted when both of the following conditions exist: Quality PRR is written with quantity discrepant andThere are receipts for referenced part and duns number within the previous twelve months.PPM for a supplier manufacturing duns is calculated monthly using the following formula:3.91Total all the “estimated quantity nonconforming” for all part numbers for that locationNote: Actual quantity nonconforming is used for supplier initiated PRR’s.23Divide by total receipts for that locationMultiply by 1,000,000.S-IpB (Severity Incidents per Billion)S-IpB for a GM supply organization is impacted when both of the following conditions exist: Quality PRR is written with a documented impact towards the GM final customer, GMmanufacturing plant and GM product (vehicle, powertrain or component).There are receipts for referenced part and duns number within the previous six months.S-IpB for a supplier manufacturing duns is calculated monthly using the following formula:1. Each Quality PRR receives a weight factor based on the documented impact towards theGM final customer, manufacturing plant and product2. Total all the weight factors
PPM for a supplier manufacturing duns is calculated monthly using the following formula: 2. Total all the “estimated quantity nonconforming” for all part numbers for that location Note: Actual quantity nonconforming is used f