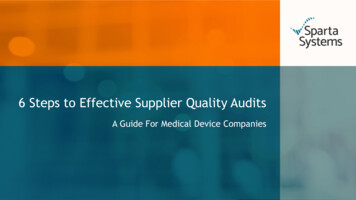
Transcription
6 Steps to Effective Supplier Quality AuditsA Guide For Medical Device Companies1
Table of Contents3Why Supplier Quality Audits Matter4Manual vs. Automated Supplier Audits5Six Steps to Effective Supplier Quality Audits12Medical Device Company Benefits14Conclusion2
Why Supplier Quality Audits MatterRecent issues impacting consumer safety have requiredorganizations to re-examine the way they approach theirquality management practices. Medical Device companiesare increasing their efforts to inspect and audit the qualityof their own operations both internally and throughout thesupply chain network of partners and suppliers.FDA initiated productrecalls rose 69.5%from 2007 to 2012*Audits evaluate processes, systems, product and materials,people or other corporate operations. Audits can be runinternally, by partners, customers, regulatory agencies, orthird parties.* Source: FDA Enforcement Statistics Summary3
Manual vs. Automated Supplier AuditsDuring external audits with suppliers, the auditor documents information before, during and after the audit. Documentation isneeded to both record the results of the specific audit and support future tracing and trending efforts. Manually capturing resultscause inefficiencies, inconsistencies and redundancies. An organized approach to audit management allows companies to leveragetechnology that enables holistic end-to-end automation across their entire supply chain auditing process and their globalorganization.ManualAutomated Ineffective supplier communications Integration for a closed-loop process Siloed processes/Disconnected systems Consistent templates Incomplete or inaccessibledocumentation Data management to protect company’sinterest agreements with suppliers Inconsistent audit results Reduce time and cost per audit21% Lack of oversight4
Six Steps to Effective Supplier Quality chedulePlan5
Step 1: PlanProper planning results in an audit that flows smoothly and logically,minimizing backtracking and repeat visits that take time and effortwithout adding value. An audit management system can aid withsupplier planning processes that include:1 Assigning appropriate auditors to lead and assist with the auditingeffort Specifying which processes and sub processes will be audited, aswell as the results from the previous audit;2 Assign Auditors Define audit scope andobjectives and review previousaudit results with supplier Defining the supplier’s audit scope, objectives and agenda; Determining which audit template to use; Developing a chronology of the audit from start to finish;3 Build the audit template Determining the types of resources and documents needed from thesupplier’s process owner.6
Step 2: Schedule Handle all calendar andworkload aspects of thesupplier audit, and incorporatethe strategic use of reminderand tracking systems Manage multiple auditssimultaneously Balance workload and conflictsAn automated audit system can simplify the process of schedulingaudit dates, manage resource conflicts, including automatic remindersto initiate and assign audits to ensure that tasks don’t fall through thecracks.Automated scheduling is particularly useful when multiple supplieraudits are occurring at the same time because it eliminates personnelconflicts.Robust reports can subsequently be produced that allow keystakeholders to achieve a macro view of audit activity across thesupply chain, understand auditor utilization, and identify properworkload balancing and conflicts. Communicate schedule toauditors7
Step 3: Perform AuditAudit management systems help the lead auditor manage the overall supplier auditprocess, including gathering required data; recording audit findings and objectiveevidence for each question; issuing action items to address discrepancies; managingand communicating any changes to the supplier audit plan; communicating progress toall stakeholders; and ensuring that the schedule stays on track.Auditors can electronically document audit results whether they have internetconnectivity or not — at a customer site, on an airplane, or at their desk. This allowsauditors to document everything once (including all of the classifications managementneeds for future tracking and trending), and eliminates the copy/paste challengescommon in audits. This capability is enabled by modern lightweight technology thatallows auditors to conduct work while disconnected from the internet. This approachis a complete departure from legacy work methods like MS Excel, which are looselycontrolled and emulate the manual processes audit management systems are strivingto replace.Benefits of a properlyexecuted supplier auditRecommendations andCAPAs often ariseDocument findings andobjective evidenceIdentify and addressdiscrepanciesManage and communicateany needed changesKeep schedule on trackand document auditresults8
Step 4: ReportOnce the appropriate criteria are evaluated,auditors can generate a formatted report thatincludes the written audit observations of goodpractices, and risks and problems identified.This report forms the basis of the discussionabout the audit results and findings.An audit management system providesreporting capabilities that also generate trendsand metrics against data gathered acrossreports. In systems that track multiple auditinggroups, risk and prioritization can be rolled upand used to determine prioritization ofresources across groups, not just on a siloedbasis within each group.Reports that are written and organized wellallow both the manufacturer and supplier tounderstand and benefit from the audit processProvide a formal audit report withappropriate trends and metrics analysisSignificant attention should be given to thequantity and type of data collected, reportformatting, and diversity of readershipEffective communication is key9
Step 5: Action TasksAction tasksmust be assignedpriorityLack of followthrough createsmajor deficiencyand liabilityEffectively andefficiently manage aCAPA processAddressDiscrepanciesThe supplier must respond to audit findings by their respective due dates. The response must include a probe into the root cause, aproposed corrective action and a completion date. An integrated CAPA management solution is highly recommended to effectivelyand efficiently manage the CAPA process based on the priority, criticality and the risk factor of the finding. For supplier audits, theoffline capabilities now allow auditors to email the audit findings directly to the supplier. The supplier can respond electronically,which helps ensure that the response fulfills the expectations of the organization’s quality system.10
Step 6: Supplier Close OutThis final step is to assure nothinghas been overlooked, guaranteeingaudit integrityEnsure all action itemsare addressedEnsure responses arecapturedEnsure appropriate signoffs are receivedA supplier audit can be completed and closed-out once all the action items are addressed, and the responses andappropriate sign-offs are received. A final audit report can be generated to document the audit for inspection, or theaudit management system can be used as the official system of record.11
Medical Device Company Benefits1Verify whether the correct SOP is being followedAvoid2Check for supplier quality agreement complianceHuman Injury3Alert the company of any supplier deficiencies4Help identify and correct minor issues before major issuesdevelopLegal LiabilityFinancial LossPublic RelationsDisasterBenefits for a medical device company to build an audit process include the opportunity to create a consistent format. When itsends in different auditing groups such as accounting, IT systems, HR, engineering, or materials, each of those groups can accessthe shared supplier information. This streamlines all audits with multiple suppliers by eliminating duplication of effort andvariability of outcome. Audit steps and reporting formats require a uniform and consistent appearance, making everyone’s jobeasier, faster, and more efficient. Audits help identify and correct minor issues before major issues develop, leading to proactiveresolution.This can mean the difference between a simple supplier process correction versus human injury, legal liability, financial loss, andthe associated public relations disaster.12
Medical Device Partner/Supplier Benefits1Audit data sharing and standardizations can reduce the stafftime and expense associated with multiple audits2Strengthen supplier reputation via a history of auditcooperation and successful results3Help suppliers better understand strengths and areas ofopportunityStrengthens thepartner-supplierrelationshipMedical Device companies and suppliers mutually benefit from the auditing process. Suppliers can incorporate insights and findingsinto processes and thereby become best-in-class. This strengthens the partner-supplier relationship and enhances the supplier’sstanding in the marketplace.Audits involve inspections of data, processes, metrics, and onsite equipment across the supply chain. Effectively addressing riskareas, assuring regulatory compliance, reducing costs, and enhancing visibility are the four main reasons to establish a global auditprocess. The global audit process maximizes the benefit throughout the organization and critical suppliers are better managedwithin this close working relationship.13
ConclusionA centralized and automated audit management solution enablesstrong collaboration with partners and suppliers across themedical device value chain. Automated solutions improveauditors’ productivity, provide more accurate results, and make iteasier to identify trends across the global organization, thus,helping to improve operational processes and controls throughoutthe supply chain.As a result of this integrated end-to-end solution, enterprises reapthe benefits of lower audit costs, greater productivity, and lessoperational risk, which ultimately leads to better product quality.Supply Chain Challenges Efficiency Product Quality Regulatory Compliance Safety Cost Containment Quality Assurance Public RelationsAudit SolutionsRaise performance levels andstrengthen relationships whileimproving patient-care quality forMedical Device companies andtheir suppliers14
ResourcesTo learn more about audit management, please visitwww.spartasystems.com or check out the following resources:Whitepaper: Automated Audit ManagementWhitepaper: Conducting Effective Internal AuditsDatasheet: Audit Management15
Back PageFounded in 1994, Sparta Systems is the world’s premier provider of cloud and on-premise quality management software. We offer thesolutions, analytics, and expertise that speed up quality and compliance. Companies in life sciences, consumer products, discretemanufacturing and more, rely on Sparta.1.888.261.5948 1.609.807.5100 sales@spartasystems.com www.spartasystems.com16
Benefits for a medical device company to build an audit process include the opportunity to create a consistent format. When it sends in different auditing groups such as accounting, IT systems, HR, engineering, or materials, each of those groups can access the shared supplier information. This streamlines all audits with multiple suppliers by eliminating duplication of effort and