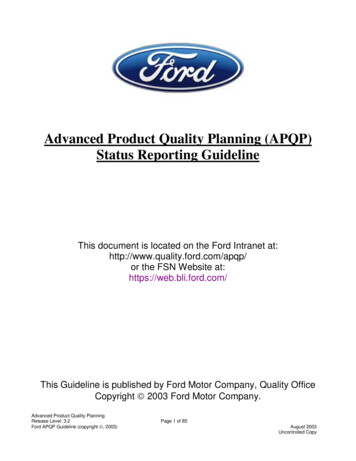
Transcription
Advanced Product Quality Planning (APQP)Status Reporting GuidelineThis document is located on the Ford Intranet at:http://www.quality.ford.com/apqp/or the FSN Website at:https://web.bli.ford.com/This Guideline is published by Ford Motor Company, Quality OfficeCopyright 2003 Ford Motor Company.Advanced Product Quality PlanningRelease Level: 3.2Ford APQP Guideline (copyright , 2003)Page 1 of 85August 2003Uncontrolled Copy
All rights reservedForewordFord Motor Company launched an Advanced Product Quality Planning Status ReportingGuideline (APQP) Fast Start Initiative in December 1994. A cross-functional APQP team wasformed to review the existing FAO Procedures and target best practices. The 1994 version ofthis document was created at that time, to be in line with the AIAG Advanced Product QualityPlanning and Control Plan Manual.Since that time, the external suppliers to Ford Motor Company, and internal suppliers withinFord have used the FAO APQP Status Reporting Guideline to monitor their own systems withregard to APQP.A cross-functional team was formed in 1999/2000, which continues today to periodically reviewthis manual and update it accordingly to current best practices, and FPDS processes. Thismanual contains references (at the time of publishing) to the FPDS Process Sheets. All of thishas been done to clarify further the appropriateness of the APQP process, and its direct tie tothe existing systems/process Ford currently has in place.Furthermore, it is intended that the updated APQP process and FPDS timing information willassist the external supply base in understanding the differences between their own timingrequirements, and those which need to be met by the entire Vehicle Program in the delivery ofa new vehicle.This Guideline documents the Ford APQP evaluation and status reporting process. It does notreplace the AIAG Advanced Product Quality Planning and Control Plan Reference Manual asthe basis for quality planning.Questions regarding this process, please contact the following:Supplier APQP concerns: NAT - Ranga Rajan (313) 33-75383 NAC - Debra Keller (313) 32-31735New Model Programs: Craig Fike (313) 32-21765PTO Program Launches: Internal Make Parts/Internal Suppliers – Larry Berard (313) 32-29256(note: PT internal suppliers refer to PTP 07-137)Stamping Business Unit Program Launches (SBU): Jesse Jou (313) 39-03246APQP Guideline changes: Steve Opaleski (313) 32-20941Advanced Product Quality PlanningRelease Level: 3.2Ford APQP Guideline (copyright , 2003)Page 2 of 85August 2003Uncontrolled Copy
Table of ContentsFOREWORD .2APQP FUNDAMENTALS .5APQP Process Flow Map.6Fundamentals of the APQP Process .7APQP REPORTING PROCESS .10APQP Status Reporting Process Flow Chart.11APQP Status Report .12APQP Status Report Form.13Filling Out the Status Report Form.14Quality of Event Checklists .15Risk Assessment.15APQP TIMING .17Ford / Supplier Systems "V" Model .18APQP Generic Program Timing Gantt Chart .19APQP ELEMENTS .21Sourcing Decision .22Customer Input Requirements .23Craftsmanship .24Design Failure Mode and Effects Analysis (DFMEA) .25Design / Manufacturing Reviews.27Design Verification Plan & Report (DVP&R).28Sub-Contractor APQP Status.29Facilities / Tools / Gauges.30Prototype Build Control Plan .32Prototype Builds .33Drawings & Specifications.34Team Feasibility Commitment.36Manufacturing Process Flow.37Process Failure Mode and Effects Analysis (PFMEA).38Measurement System Evaluation .40Pre-Launch Control Plan.41Operator Process Instructions.42Packaging Specifications .43Production Trial Run .44Production Control Plan .46Preliminary Process Capability .47Production Validation Testing .48Part Submission Warrant (PSW).50Advanced Product Quality PlanningRelease Level: 3.2Ford APQP Guideline (copyright , 2003)Page 3 of 85August 2003Uncontrolled Copy
APPENDIX SECTION .52APPENDIX A:APQP ROLES & RESPONSIBILITIES .53VO – PD APQP Lead/Support Responsibilities – Relationship Table .54Powertrain Roles and Responsibilities Matrix .55Powertrain Program Review Process .56STA Roles & Responsibilities.57EXTERNAL SUPPLIERS .67APPENDIX B:RELATED FORMS .69APPENDIX C:GLOSSARY OF TERMS .72APPENDIX D:REFERENCES AND WEBSITES .79APPENDIX E:CHANGE INDEX .84Advanced Product Quality PlanningRelease Level: 3.2Ford APQP Guideline (copyright , 2003)Page 4 of 85August 2003Uncontrolled Copy
APQP FundamentalsAdvanced Product Quality PlanningRelease Level: 3.2Ford APQP Guideline (copyright , 2003)Page 5 of 85August 2003Uncontrolled Copy
APQP Process Flow MapAPQP PROCESS FL0WC R A F T S M A N S H IPD R A W IN G S /S P E C IF IC A T IO N SS O U R C IN GD E C IS IO NP -D ia g r a mD E S IG N /M A N U F A C T U R IN GR E V IE W SF a ilu r e M o d e s & E r r o rS ta te sC U S T O M E R IN P U TR E Q U IR E M E N T STEA MF E A S IB IL IT YC O M M IT M E N T(a ffe c t a ll A P Q Pe le m e n ts )S p e c ific a tio n s &T a rg e ts(V D S /S D S /C D S )D e s ig n in g o f th eV e h ic le / S y s te m /S u b s y s te m /C om ponentD E S IG N F A IL U R EM O D E EFFE C TA N A L Y S IS (D F M E A )F E E D IN F O R M A T IO NFO R W A R DF E E D IN F O R M A T IO NB A C KD E S IG NV E R IF IC A T IO NP L A N (D V P )D R A W IN G S /S P E C IF IC A T IO N S (P a p e r/ E le c tr o n ic )F A C IL IT IE S /TO O LS/G A U G ESM A N U F A C T U R IN GPR O C ESS FLO WM EA S U R EM EN TSY STEME V A L U A T IO N(D im e n s io n a lC o n tro l)O P ER A TO RPR O C ESSIN S T R U C T IO N S(P ro c e s sD e fin itio n )PR O C ESSF A IL U R E M O D EEFFEC TA N A L Y S IS(P F M E A )PR O TO TY PEB U IL D C O N T R O LPLA NPR O TO TY PEB U IL DP R E -L A U N C HC O N TR O L PLA NP R O D U C T IO N T R IA LR U NO P ER A TO RPR O C ESSIN S T R U C T IO N S( V e r if ic a tio n &T r a in in g )P R E L IM IN A R YPR O C ESSC A P A B IL IT YP R O D U C T IO NC O N TR O LPLA NP R O D U C T IO NV A L ID A T IO NT E S T IN GPA R TS U B M IS S IO NW A R R A N T (P S W )Advanced Product Quality PlanningRelease Level: 3.2Ford APQP Guideline (copyright , 2003)Page 6 of 85August 2003Uncontrolled CopyTIME
Fundamentals of the APQP ProcessAdvanced Product Quality Planning (APQP)Advanced Product Quality Planning (APQP) is a structured method for defining andexecuting the actions necessary to ensure a product satisfies the customer. APQP isprogram and supplier-led and is required of all system, subsystem and componentmanufacturing locations. This includes both internal and external suppliers to Ford.The Goal of APQPThe goal of APQP is to facilitate communication between all persons and activitiesinvolved in a program and ensure that all required steps are completed on time, with ahigh quality-of-event, at acceptable cost and quality levels.The Purpose of APQPThe purpose of this status reporting guideline is to establish:! Common APQP expectations for the internal and external suppliers to FordMotor Company! Common APQP process metrics! A common program status reporting format! Roles and responsibilities for APQP elements! A better understanding of how the APQP elements relate to the Ford ProductDevelopment System (FPDS), specific FPDS milestones, and their timingThe Approach of APQPThis status reporting guideline describes 23 key APQP disciplines. Ford MotorCompany expectations are defined for these key disciplines in definitions, and detailedchecklists. The status for these disciplines is summarized using metrics described inthe Reporting section.This status reporting guideline is written from a supplier standpoint. A supplier is aninternal or external supplier of materials, components, subsystems, systems, designs orprocesses that will be delivered to a customer. A customer is the recipient of thesupplier's product or process. Besides customers, every supplier will havesubcontractors. A subcontractor is the provider of material or parts to a supplier.The Applicability of APQPAPQP status reporting is a requirement of all internal and external suppliers to Ford(including Ford Product Development). APQP must be done for new programs/partsand major part changes as appropriate. In addition, Product Development Teams are tomonitor the status of internal and external engineering and process developmentdisciplines and assess the "Quality-of-Event" as well as the timing and completion ofeach of the 23 elements.Advanced Product Quality PlanningRelease Level: 3.2Ford APQP Guideline (copyright , 2003)Page 7 of 85August 2003Uncontrolled Copy
TeamsThe first step in the Advanced Product Quality Planning Process is to assignresponsibility to a cross-functional team. Effective product quality planningrequires the involvement from all areas within a corporation. The team includesrepresentatives from engineering, manufacturing, material control, purchasing,quality, sales, field service, subcontractors, and customers as appropriate.ElementsThis Status Reporting Guideline describes 23 key APQP disciplines, identified asFord APQP elements. Please note that there is a slight difference in the 23elements in this updated version. These elements, when summarized andreported, communicate the status of different levels of a program.Of the 23 Ford APQP elements, 19 are requirements of the AIAG AdvancedProduct Quality Planning and Control Plan manual. The four additional elementsmeet unique Ford requirements for APQP status reporting and communicationbetween supplier and customer.The 19 industry standard elements are: Design FMEADesign Verification Plan &ReportPrototype Build Control PlanManufacturing Process FlowChartProcess FMEAPre-Launch Control PlanOperation ProcessInstructionsProduction Control PlanDesign & Mfg. Review(s) Facilities / Tools / GaugesThe four Ford unique elements are: Sourcing DecisionCustomer Input RequirementsAdvanced Product Quality PlanningRelease Level: 3.2Ford APQP Guideline (copyright , 2003) Prototype BuildsDrawings and SpecificationsTeam FeasibilityCommitmentMeasurement SystemsEvaluationPackaging SpecificationsProduction Trial RunPreliminary ProcessCapability StudyProduction Validation TestingProduction Part Approval(PSW)Subcontractor APQP StatusCraftsmanshipPage 8 of 85August 2003Uncontrolled Copy
APQP FlowThe chart on page 6 of this section is an overall summary of the APQP process.It is intended to show that APQP is NOT just a feed forward process, but it alsoincludes feeding information back, updating documents in an iterative fashion,and using information and lessons learned from a program for future programs.The APQP Process includes five main functions:1. Planning of the APQP elements2. Execution of the APQP elements3. Monitoring the "Quality-of-Event" of the execution of the elements, as well asthe timing, by the team in-between FPDS milestones4. Issues Resolution5. Status Reporting (minimum at FPDS milestones)RolesThe roles matrix in Appendix A defines the lead and support roles for VehicleOperations and Product Development. Under the VO/PD matrix, the APQPStatus Reporting is as follows: Vehicle Operations Program Launch Managerreports the status on VO Internal Suppliers, and Product Development TeamLeaders will report on the D & R Engineers' status. Powertrain will report bothInternal & External P/T Suppliers (see Powertrain R & R matrix for further detail).STA will report status on External Suppliers as described in their R & R matrix.This Roles and Responsibilities matrix can be used to derive other tables specificto each organization's requirements for element responsibility and statusreporting.ResponsibilitiesResponsibilities for the activities are identified in the checklist, and references toFPDS process sheets are in the element descriptions. A Quality-of-Eventchecklist is provided for each element to assist in understanding the Expectationsfor each element. Rating history, FPDS timing requirements, and Expectationsdue at certain points in the program are described.Advanced Product Quality PlanningRelease Level: 3.2Ford APQP Guideline (copyright , 2003)Page 9 of 85August 2003Uncontrolled Copy
APQP ReportingProcessAdvanced Product Quality PlanningRelease Level: 3.2Ford APQP Guideline (copyright , 2003)Page 10 of 85August 2003Uncontrolled Copy
Advanced Product Quality PlanningRelease Level: 3.2Ford APQP Guideline (copyright , 2003)Page 11 of 85August 2003Uncontrolled Copy
APQP Status ReportThe Ford APQP Status Report summarizes the program status using the 23 Ford APQPelements. It summarizes the information and provides an assessment at thecomponent/subsystem level, the system/organization level(s), and finally the programlevel. The individual issues at each level are to be documented and tracked, as well asraised to management for assistance in solving/closing if they cannot be handled at theworking level.Please note the different levels of reporting, and the summarizing process as shown onpage11. Submit the Status Report to the customer at all major program reviews (e.g. FPDSMilestones).Customers or suppliers shall conduct more frequent status reviews as needed.The customer shall provide a list of all scheduled program status review dates to thesupplier.Submit supporting documentation upon customer request.The subsystem team completes the status report for its product, with componentsupplier status summarized on the Subcontractor APQP status line. The subsystemteams submit the report to their customer, the system team.The system/organization team will then complete the status report for their product, withtheir subsystem supplier status summarized onto the Subcontractor APQP status line.The system teams submit the data to their customer, the vehicle team.Ratings and AssessmentG/Y/R StatusGreen-Yellow-Red status communicates the progress toward the successful completionof an APQP Element by the program need date. Program need date is the last possibledate an element can be completed and not adversely affect quality or timing of theprogram. The “GYR Status” column of the report shows the assessment for eachelement.Definitions/Risk factors for Green, Yellow, and Red are listed in the table below.DEFINITIONSRisk/Status AssessmentRiskHighColorDefinitionRedTarget dates and/or deliverables are at risk. A recovery work plan is notavailable and/or implemented, or the work plan does not achieve programtargets.Moderate Yellow Target dates and/or deliverables are at risk, but a resourced recoverywork plan has been developed to achieve program targets, and has beenapproved by the appropriate Management Team.NoneGreen Target dates and deliverables are on track and meeting objectives.Advanced Product Quality PlanningRelease Level: 3.2Ford APQP Guideline (copyright , 2003)Page 12 of 85August 2003Uncontrolled Copy
APQP Status Report FormAdvanced Product Quality PlanningStatus ReportSupplier/Org:Location:Supplier Code:1Contact Name/Tel:4Program:Model Year:FPDS Milestone:Review Date:23FPDS MILESTONEAPQP ELEMENT6789101112 SI SC PH PA (ST) PR (CP) CC LR LS (J1)yyyy/mm/dd1. Sourcing DecisionPart Name:Part Number:Notice Level:User y/mm/ddyyyy/mm/ddyyyy/mm/ddyyyy/mm/ddyyyy/mm/dd FS yyyy/mm/ddyyyy/mm/dd132. Customer Input Requirements3. Craftsmanship4. Design FMEA5. Design/Manufacturing Review(s)6. Design Verification Plan & Report7. Subcontractor PSW Status8. Facilities, Tools & Gages9. Prototype Build Control Plan10. Prototype Build(s)11. Drawings & Specifications12. Team Feasibility Commitment13. Manufacturing Process Flowchart14. Process FMEA15. Measurement Systems Evaluation16. Pre-Launch Control Plan17. Operator Process Instructions18. Packaging Specifications19. Production Trial Run20. Production Control Plan21. Preliminary Process Capability Study22. Production Validation Testing23. Part Submission Warrant (PSW)OVERALL APQP STATUS RATING (GYR)1415161718Element / Activity#ActivityIssue(s) for Red/Yellow Elements(summarize the concern & resulting risk)Corrective Action / Resolution Plan(e.g. revise timing, allocate rAdvanced Product Quality PlanningRelease Level: 3.2Ford APQP Guideline (copyright , 2003)Page 13 of 85August 2003Uncontrolled Copy
Filling Out the Status Report FormThe following section describes how to fill in each of the fields on the Status Report.Refer to the status report example on the previous page for the number in each field.1. Org/SupplierEnter your organization or your company name. If you are delivering the product to anotherdepartment within the manufacturing facility, a department number or group name may beentered here.2. LocationEnter the location of the facility manufacturing the system/subsystem or component ifapplicable.3. Supplier CodeEnter the UCCS code for the manufacturing facility if applicable.4. Contact Name/Telephone NumberIdentify Program Manager and phone number.5. ProgramEnter the name of the program.6. Model YearEnter the Model Year of the program.7. FPDS Milestone/Team EventEnter the current FPDS Milestone / Team Event that you will be reporting on.8. Review DateEnter the date of the review of this report.9. Part NameEnter the name of the part being reviewed (if applicable).10. Part NumberEnter the part number of the part being reviewed (if applicable).11. Notice LevelEnter the notice level of the part being reviewed (if applicable).12. User PlantEnter the plant(s) where this vehicle / engine / transmission will be built.Advanced Product Quality PlanningRelease Level: 3.2Ford APQP Guideline (copyright , 2003)Page 14 of 85August 2003Uncontrolled Copy
Filling Out the Status Report Form (cont.)13. G/Y/R StatusEnter status for the 23 Elements14. Element / ActivityEnter your home Element Number for which the issue is being reported and the Activityreporting on the issue.15. Issue(s) for Red/Yellow ElementsSummarize the concern and resulting risk here.16. Corrective Action / Resolution PlanEnter a summary of the corrective action for the issue being addressed and the resolutionplan to correct the issue (an 8D that is tracking the issue may be referenced here).17. TimingEnter the Open date for the issue, and when it is resolved, enter the closing date.18. ResponsibilityEnter the name of the Ford Motor Company and/or the Supplier person responsible forfollow-up on this issue.Quality of Event ChecklistsIn Appendix B, is an example of a completed Quality-of-Event Checklist along with thewebsite location of the Excel file that contains the 23 Element Checklists. Thesechecklists cover the basic requirements for successful completion of the elements, butmay not be inclusive. These checklists are to be used as a guideline in assessing yourstatus. The Element expectations on these checklists have been grouped for Milestonereporting following the FPDS process. The boxed areas should be completed by theappropriate milestone. For next milestone report requirements, update the previousmilestone boxed areas as needed. The APQP Status Report Form is linked to thechecklists and the Information Worksheet for ease of reporting.Risk AssessmentEvery APQP team should conduct a risk assessment as soon as possible after formingthe team. The purpose of the risk assessment is to determine what elements in theAPQP process a supplier, organization, or program team must complete. ReferenceAppendix B, for an example of a risk assessment form.Advanced Product Quality PlanningRelease Level: 3.2Ford APQP Guideline (copyright , 2003)Page 15 of 85August 2003Uncontrolled Copy
Risk Assessment (cont.)Elements to be evaluated in the Risk Assessment include:1) Quality History High warranty or Things Gone Wrong (TGWs)on current model or surrogate product Frequent Quality Rejects (QRs) and/or campaigns at the receiving plant (Assy& Stmp. Plants, Supplier Plants, etc.) Similar component or system was the cause of a recall action2) Supplier Profile New supplier or new manufacturing location Product or manufacturing technology is new to the supplier manufacturinglocation Supplier's historic launch performance is poor Supplier resources are stretched due to significant amount of new business Supplier location is not Q1 or is a Q1 revoked-supplier3) Engineering Profile New design Manufacturing techniques are new to the industry Similar products are subject to numerous design changes that threatenprogram timing High product or process complexity Product is strategically important due to high visibility or functionalperformance4). Performance versus Targets Design goals (weight, materials, functional performance, etc.) will be difficultto achieve Reliability goals will be difficult to achieve Quality goals (warranty, TGWs, scrap rates, rework rates, etc.) will be difficultto achieve Program timing is compressed Cost targets are aggressive5). AdjustmentsIf any of the concerns listed above are present, the customer may require all APQPelements to be completed and reported. If the program is considered to be low risk, thesupplier may skip certain APQP elements. For example, if the product is carryover withminor changes, existing control plans may be used, and packaging evaluations may notbe required. The customer must agree in writing to all deviations from the APQPprocess. If the customer and the supplier agree that an element/expectation is notrequired, the supplier should write "NA" for not applicable in the correspondingMilestone column on the Quality-of-Event Checklists.Advanced Product Quality PlanningRelease Level: 3.2Ford APQP Guideline (copyright , 2003)Page 16 of 85August 2003Uncontrolled Copy
APQP TimingAdvanced Product Quality PlanningRelease Level: 3.2Ford APQP Guideline (copyright , 2003)Page 17 of 85August 2003Uncontrolled Copy
Ford / Supplier Systems "V" ModelC u s to m e r F o c u sC u s to m e rM u s t / W a n ts KO C u s to m e rS a tis fa c tio nC u s to m e r E x p e rie n c e a n d F e e d b a c kF o rd(S u p p lie r's(S u p p lie r'sIn te rn a l) F o rd S I In te rn a l) J1 J1 J1 G e n e ric S y s te m s E n g in e e rin gV e h ic le L e v e l In p u ts S I F o rdP ro g ra m T im in gR e la tio n s h ip to S u p p lie rT im in g J1 "V " M o d el S I R e la tio n s h ip to P ro g ra m a n d S u p p lie r T im in gT h e T o ta l F o rd P ro g ra m T im in g isd e te rm in e d , a n d p ro v id e d to th eT ie r 1 a n d T ie r 2 S u p p lie rs .V e h ic le L e v e lR e q u ire m e n ts (V D S )It is v e ry im p o rta n t to u n d e rs ta n dth a t th e T ie r 1 a n d T ie r 2s u p p lie rs a re b ro u g h t o n a td iffe re n t tim e s , w ith tig h te rp ro c e s s tim in g re q u ire m e n ts .S u p p lie rs m u s t b e a b le to p e rfo rma ll o f th e n e c e s s a ry e le m e n tso f A P Q P a n d th e p ro g ra m , w ith inth is tim in g .S y s te m /S u b s y s te m L e v e l (S D S )T o o lin g &T h e ir o w n in te rn a l J o b # 1 m u s to c c u r b e fo re th e a c tu a l J o b # 1 o fth e p ro g ra m , a n d th e y m u s t b a c ku p th e ir tim in g fro m th e a c tu a lP ro g ra m J o b # 1 to a s s u re th e ya re a b le to d e liv e r o n tim e .T ie r 2 S u p p lie rT o o lin g & T ie r 1 S u p p lie rF o rd T o ta l P ro g ra m T im in gIt is th e re fo re e v e n m o re c ritic a lth a t a ll d e s ig n a n d q u a lityd is c ip lin e s a re p la n n e d fo r, a n dfo llo w e d , v e ry e a rly o n , to p re v e n tla te e n g in e e rin g c h a n g e s . IfN O T , th e y a re N O T a b le tore c o v e r in m a n y c a s e s .P a rt/C o m p o n e n t F a b ric a tio n /V e rific a tio nP a rt /C o m p o n e n t D e s ig n(C o m p o n e n t D e s ig n S p e c - C D S )T o ta l P ro g ra m F P D S M ile s to n e sT ie r 1 S u p p lie r M ile s to n e sT ie r 2 S u p p lie r M ile s to n e s S I S tra te g icIn te n t CC C h a n g e C u to ffS y s te m s O rie n te d v ie w o f A P Q PAdvanced Product Quality PlanningRelease Level: 3.2Ford APQP Guideline (copyright , 2003)(C P )C o n firm a tio nP ro to ty p e J1 Job #1M a n u fa c tu rin g a n d D e liv e ry O rie n te d v ie w o f A P Q PPage 18 of 85August 2003Uncontrolled Copy
APQP Generic Program Timing Gantt ChartAPQP Generic Program Timing Gantt ChartMonths Before Job #1 (MBJ1)All new vehicle: S6New Exterior, modified lower struc: S5New Exterior, c/o lower structure: S4Moderate Freshening: S3Minor Freshening: S2Trim: S1ElementFPDS MilestonesFERPSWRequirement(Approx. 17Months1PP 484.5
Ford APQP Guideline (copyright , 2003) August 2003 Uncontrolled Copy APQP Status Report The Ford APQP Status Report summarizes the program status using the 23 Ford APQP elements. It summarizes the information and provides an assessment at the component/subsystem level, the system/organization level(s), and finally the program level.