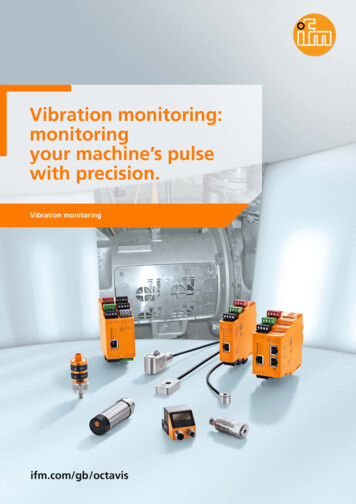
Transcription
Vibration monitoring:monitoringyour machine’s pulsewith precision.Vibration monitoringifm.com/gb/octavis
Systems forvibration monitoring.The optimum solutionfor every Machine protectionProcess monitoringSystem setupProduct overview2
For industrialapplicationsMonitoring of overall vibration accordingto ISO 10816.Detecting resulting damage at an earlystage, avoiding consequential damageand increasing life spans.4- 5Early detection of potential faults andtheir causes on the basis of individualvibration characteristics and otherinfluencing factors.6- 7Avoid damage to machine components,tools or workpieces via permanentmonitoring and very short response times.The integration into the PLC makes itpossible to adjust the vibration monitoringto the process of the machine or the plant.8- 9The ifm group of companies: our owndevelopment and production with highquality standard.The detection and integrated evaluationof vibration signals serves as a basis for theseamless integration of online conditionmonitoring into manufacturer-independentautomation and control systems.10 - 123
Trend monitoring:detecting impending damageat an early stage to avoidconsequential costs.Simple:monitoring of the overallstatus of the machineStandardised:compliant to ISO 10816Vibration monitoringSafe:protection against machinedamageFlexible:easy integration in theapplicationReliable:longer uptimeUnbalanceLoosenessMachine protection and remotemaintenance.The monitoring of wind power gearboxes or pumps in the water supplyconcerning wear and stress makes itpossible for the operator to organiseefficient maintenance.Alarm outputs serve to protect thesystem, to trigger remote maintenanceand to facilitate targeted anlysis.BeltVibration velocityMisalignmentAlarmWarningTimeTrending of the machine vibrationsto ISO 108164
What vibration reveals about machinehealth.Even if in peak condition, all machinesgenerate vibrations during operation.However, due to unbalance, misalignmentor looseness, these vibrations will increaseto a level that will have a negative effecton the functionality and service life of themachine. The ISO 10816 standard definesVibration velocityVibration accelerationVibration monitoringprecise vibration limit values for industrialCondition monitoringmachines that can be used to assess themachine condition from new to critical.With ifm's product portfolio, the vibrationbehaviour can be monitored precisely andaccording to your requirements. Even onlyslightly increased vibration velocities willbe detected and signalled. This is howimpending defects can be detected andComponent protectionContaminationTooth faultsRolling element lanceBeltremedied at an early stage to avoid expensive damage and downtime.1 kHz10 kHzFrequency rangeWireless vibrationsensor type VWBasic vibrationsensor type VKBattery-poweredvibration sensorfor intermittentmeasurement ofthe overall vibration of simplemachines. Requiresa suitable gateway.Switching outputand transmitterfunction. Responsedelay avoids triggering at start-up.Basic vibrationtransmitter type VTSimple transmitterfunction, 4.20 mA.Intelligentvibration sensorstype VVIntelligentvibration sensorstype VNAccelerationsensorsVSA / VSP typeDiagnosticelectronicstype VSEEfficient conditionmonitoring forsimple machinesvia IO-Link.Detects and analyses various processvalues internallyfor early damagedetection.4-digit alphanumeric displaywith colourchange, historymemory withreal-time clock,analogue andswitching outputor 2 switchingoutputs.Robust acceleration sensors typeVSA or VSP (orintrinsically safeVSP0xA) forconnection to theVSE diagnosticelectronics.4-channeldiagnostic modulewith additionalprocess valueinputs, integratedhistory memory,networkingpossible.Monitor vibration velocityThe vibration sensors VK / VT / VWmonitor online the overall vibrationcondition of machines and plantsaccording to ISO 10816. The sensormeasures the rms vibration velocityon a non-rotating component surfaceand triggers an alarm if the machinevibrations are too strong.Simple sensor setting:ifm.com/gb/setting-guide5
Acting rather than reacting:increase availability,reduce maintenance costs,assure quality.Safe:permanent condition monitoringof critical machinesAnticipate:machine diagnosis for earlydamage detection and avoidanceof serious consequential damageCondition monitoringOptimise:maintenance actions can beplannedLong service life:make optimum use of theresidual life of componentsEconomical:make production processes transparent – meet TCO (total cost ofownership) conceptsPrecise:Counters detect values suchas exposure time and machineuptime and support productionbased on key indicators.Monitor up to 4 measurement points.LoosenessMisalignmentRolling elementbearingUnbalanceWith the sensor type VSA / VSP machinevibrations can also be measured atinaccessible places.Up to 4 measuring points can bemonitored and documented with thediagnostic electronics type VSE. TheEthernet and fieldbus interfaces simplifynetworking and remote diagnostics.FrictionImpactDetect vibration and shocks at anearly stageTooth faultsCavitation6BeltContaminationUndetected unbalance, misalignmentor bearing damage lead to unexpectedfailures and shorter service lives. TheVV sensor detects the main indicatorsof impending machine damage.Triggered raw data acquisition (BLOB)enables further analyses.
The most efficient way to avoidunplanned downtimeWith condition-based monitoring, imminent machine damage can be detectedat an early stage. This enables predictivemaintenance planning, which in turnallows for consistent product quality andthe associated efficient use of resources.VibrationDiagnostic electronicsdetect and evaluate vibration data. Thisis how the current machine status istransmitted to the controller or the ITinfrastructure as a status value and, ifnecessary, as a warning or alarm signal.Counter functions also facilitate the calculation of component lifetimes influencedby the frequency and intensity of impacts,NoiseComponent stateFrictionHeatVibration monitoringForecast complexityThe vibration products from ifm reliablytemperature or speed.SmokeMonthsWeeksDaysFailureMinutesPrevention timeIntelligentvibration sensorstype VNIntelligentvibration sensorstype VVAccelerationsensors typeVSA / VSP / VSMIntrinsically safeacceleration sensortype VSP0xADiagnosticelectronicstype VSEOn board display,history storage fordocumentation, forrotatingmachines 120 rpm.Detection of numerous vibrationparameters withoptional raw dataacquisition (BLOB)for extended analyses as well as integrated machineuptime detectionbased on thevibration values.Different types,also for mountingin difficult toaccess areas.Various measuringranges withvoltage output(100 mV/g) orcurrent loop(0.10 mA).Connection tothe VSE diagnosticelectronics.For the measurement of vibrationin hazardous areas.Connection tothe VSE diagnosticelectronics installedoutside the ATEXzone via a barrier.4-channel diagnostic module withadditional processvalue inputs,integrated historymemory, networking possible.Vibration diagnosis on a mixing tool.Unplanned standstills of criticalmachines cause huge cost. Permanentcondition monitoring of the wholeplant makes it possible to act withforesight and to optimise the process.Our solution for conditionmonitoring of machines.ifm.com/gb/condition-monitoring7
Measuring forces:minimise scrap andconsequential damageto machine tools.Dynamic:monitoring of dynamic forces,e.g. in milling processesFast:Machine protection / process monitoringresponse times of 1 msSafe:machine, tools and workpiecesare protected against expensiveconsequential damagePreventive:early condition monitoringavoids unplanned failuresIntegrated:direct connection to the machinecontrol via a fieldbus interfaceDetect unusual vibrations.The micromechanical accelerationsensor type VSA is screwed into thehousing of the spindle and detectseven the most subtle changes of thevibration behaviour. The sensor withstands even fast movements and highforces without problems.Protectionof machinecomponentsWorkpieceprotectionTool protectionT3T2Photo source: DMG / MORI SEIKIwww.dmgmoriseiki.com8T1
standstills.diagnostic of the spindle's vibration behav-Incorrect settings and process parametersiour, collisions or excessive cutting forcesas well as incorrectly selected or defectivewill be detected within a millisecond andtools can quickly have far-reaching conse-a corresponding switching signal will bequences: The spindle and workpiece mayoutput.crash, the spindle may be permanentlyThe integration of the vibration monitor-overloaded, or the manufacturing qualitying via the fieldbus interface into themay be insufficient or the workpiece maymachine control ensures optimumbe damaged. The resulting unplannedevaluation adapted to the current operat-downtimes and increased rejects reduceing status. For example, individual alarmplant efficiency and cause unnecessarythresholds can be defined for differentcosts.tools. This ensures that the machine willThese costs are unnecessary becauseshut down reliably or change to a safedamage to the machine tool and work-state before serious damage or downtimepiece can be efficiently prevented.will occur.Dynamic forcesThrough permanent monitoring andCrash historywithout alarmAlarmWarning1 msMachine protection:spindle collision detectable in 1 msCondition indicatorMonitor spindle vibration, avoidTimeAlarmTimeTrending in a stamping processAlarmWarningAccelerationsensors typeVSA / VSMDiagnosticelectronicstype VSEDiagnosticelectronics typeVSE15xTrouble-free operation in the eventof fast movementor influence ofhigh forces. Integrated self-test forpermanent safety.Frequencyselective monitoring, history memorywith real-timeclock, counterfunction, networkcapability TCP/IP.Frequencyselective monitoring, history memorywith real timeclock, counterfunction, networkcapability TCP/IP,interface for themost commonfieldbusesAlarmWarningProcess cycleAdaptive limit value considerationAvoid consequential damageto machine tools.Changes in the cutting forces as causedby blunt tooling or swarf jam will bedetected on the basis of the changedvibration characteristics. Each tool canbe assigned individual tolerance limitse.g. a warning and switch-off thresholdDamage to the workpiece is reliablyprevented.9
Systems forvibration monitoring.Suitable productsfor all applications.Wirelessvibration sensorsFor intermittent monitoringof the overall vibrationcondition of machines andequipment according toISO 10816.Basicvibration sensorsand transmittersFor permanent monitoringof the overall vibrationcondition of machines andequipment according toISO 10816.Intelligentvibration sensorsFor measuring the overallvibration according to ISO 10816or as a condition monitoringsolution for simple machines.VNVibration sensorwith IO-LinkEnables real-time monitoringof the four categories ofmachine failure: impact, fatigue,friction and temperature.VVDiagnostic electronics4-channel diagnostic systemfor the evaluation of dynamicsignals, with additionalanalogue inputs.Acceleration sensorsProvide the measuredmachine body sound as araw signal for downstreamvibration monitoring ordiagnostics.VWVTVKVSEVSE 15xVSAVSPVSMSoftware: VES & APA toolAccessories10Software for parameter setting and onlinedata monitoring of the intelligent vibrationsensors and diagnostic electronics.
For industrialapplicationsmALE4.20To connect the vibration diagnostics tohigher-level systems (SCADA, MES, AOPC server software VOSDs(vBr-Rm oaMon dS)ito banrin dgN altrenCodinguntersCondition monitoring capabilities)Physical interfacesAccessories /connection technologyA wide product range of connection technology(e.g. sockets, Y-cables) and adapters makes it easyto implement the sensors.moneo:IIoT platformwww.moneo.ifm11
Nothing convincesmore than practice:successful use ofvibration diagnostics.Application reportsScaniaSmart lock in EefdeThe Swedish vehicle manufacturerScania is one of the world’s largestmanufacturers of utility vehicles. Theplant in Stockholm produces, amongother things, powerful engines fortrucks and buses.Vibration sensors are monitoring theautomated production.World Class Maintenance – The higheststandards in all corporate sectors leadto an improvement of all processes.These guidelines are also followedfor the waterway infrastructure in theNetherlands. On board: vibrationsensors from ifmGKN Aerospace.The Swedish company GKN Aerospacefrom Trollhättan produces highprecision parts for aircraft engines andfor aerospace industries. The machinetools have sensors that ensure maximum transparency and highest productquality.Would you liketo learn more?
Systems forvibration monitoring.From sensor to ERP.NarrowBand-IoT,2G GSMio-key AIKKQ level sensorVV vibration sensorOPC server software VOSNetwork (LAN)FieldbusFieldbusPLCAnalogue andswitching signalsIO-LinkOperating andparameter settingsoftware VES004AL masterVibrationswitchVKDiagnostic electronics VSE10x / VSE0xx / VSE15xVSPSVflowmeterGatewayfor wirelessVW pterJN22xxinclinationsensorSpeed monitorDP2122Acceleration sensorsVV vibrationsensorZener barrier ZB0633ATEXInductive sensorVSP0xA*The gateway for wireless vibration sensors and the wireless VW vibration sensor are excluded from the 5-year warranty.
Go ifmonline!Browse, select, order in the ifmwebshopIdentification systemsSensors formotion controlCondition monitoringsystemsIndustrial imagingSystems formobile machinesSafety technologyConnectiontechnologyProcess sensorsSoftwareIndustrialcommunicationPower suppliesIO-LinkAccessoriesWPosition sensorssyearsonctifm electronic gmbhFriedrichstraße 145128 EssenTel. 49 / 201 / 24 22-0Fax 49 / 201 / 24 22-1200E-mail info@ifm.comRANTYARif m p r o duifm article no. 78003835 We reserve the right to make technical alterations without prior notice. · Printed in Germany on non-chlorine bleached paper. 12/20ifm.com
VSE diagnostic electronics. Diagnostic electronics type VSE 4-channel diagnostic module with additional process value inputs, integrated history memory, networking possible. Wireless vibration sensor type VW Battery-powered vibration sensor for intermittent measurement of the overall vibra-tion of simple machines. Requires a suitable gateway.