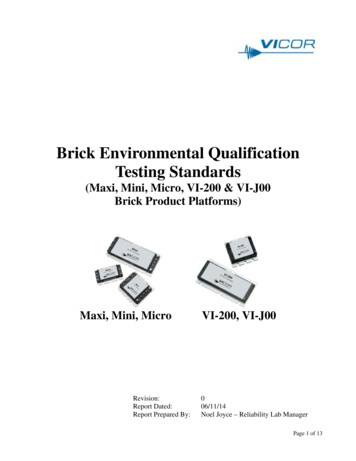
Transcription
Brick Environmental QualificationTesting Standards(Maxi, Mini, Micro, VI-200 & VI-J00Brick Product Platforms)Maxi, Mini, MicroRevision:Report Dated:Report Prepared By:VI-200, VI-J00006/11/14Noel Joyce – Reliability Lab ManagerPage 1 of 13
Table of Contents1. Purpose . 32. Executive Summary . 33. Environmental Test Conditions. 43.1.3.2.3.3.3.4.3.5.3.6.HIGH TEMPERATURE OPERATING BIAS TEST (HTOB) . 4TEMPERATURE CYCLING (TC) TEST . 5TEMPERATURE HUMIDITY BIAS (THB) . 6LOW TEMPERATURE STORAGE TEST ( LTS) . 7HIGH TEMPERATURE STORAGE TEST ( HTS) . 7HIGHLY ACCELERATED LIFE TEST (HALT) . 83.6.1.HALT Test Detail . 83.7.RANDOM VIBRATION TESTING (OPERATING)-. 113.8.MECHANICAL SHOCK (OPERATING)- . 113.9.SALT FOG . 113.10.HUMIDITY TEST . 123.12.THROUGH-HOLE SOLDERABILITY . 123.13.ESD CLASSIFICATION TESTING. . 123.14.ACCELERATION . 123.15.ALTITUDE. 123.16.EXPLOSIVE ATMOSPHERE. 134. Product Requirements . 135. Testing Requirements . 13Page 2 of 13
1. PurposeThis report outlines environmental testing which were performed to qualify Vicor Brick (Maxi, Mini,Micro, VI-200 and VI-J00) product platforms.2. Executive SummaryVicor Brick products are considered qualified to the following environmental testing standards.Representative samples from each product family were tested to the standards referenced below. Aspart of Vicor’s Ongoing Reliability Monitoring (ORM) program representative samples of Brickproducts are tested to verify continued compliance to the standards referenced below.TABLE 1Reference StandardApplicable Grade(C,T,H or M)High Temperature OperatingBias/Life (HTOB/HTOL)JESD22-A108DAll GradesTemperature Cycling Test (TCT)JESD22-A104DAll GradesTemperature Humidity Bias(THB)JESD22-A101CAll GradesHigh Temperature Storage (HTS)Low Temperature Storage (LTS)Random VibrationMechanical ShockHighly Accelerated Life Test(HALT)Salt STD-810FInternal Vicor ProcedureDP-0265MIL-STD-810FMIL-STD-810FAll GradesAll GradesIndustrial-Military GradesIndustrial-Military GradesMIL-STD-810FIndustrial-Military GradesMIL-STD-202GJEDEC JS-001-2012JESD22-C101EAll GradesAll GradesAll GradesAccelerationMIL-STD-810FIndustrial-Military GradesAltitudeMIL-STD-810FIndustrial-Military GradesExplosive AtmosphereMIL-STD-810FIndustrial-Military GradesTesting ActivityHumiditySolderabilityESD Human Body ModelESD Charged Device ModelAll GradesIndustrial-Military GradesIndustrial-Military GradesPage 3 of 13
3. Environmental Test Conditions.3.1. High Temperature Operating Bias Test (HTOB)HTOB Test CriteriaInput Voltage:Nominal Line Typical. Applied Voltage is within productspecifications.Operating Temperature:Maximum Operating temperature /- 5 CTest Duration:1000 hours.Test monitoring:Product temperature, output voltage and currentmonitored throughout the test.Output Conditions:Full Load.Functional Verification:Pre and post functional testing performed.Applicable standard:JESD22-A108D.Qty Tested:Minimum 10.Page 4 of 13
3.2. Temperature Cycling (TC) TestTemperature Cycling (TC) Test CriteriaTemperature extremes:125ºC to –55ºC (Industrial and Military Grades)125ºC to –40ºC (All other Grades)Dwell:5 minute dwell at each temperature extreme.Temp Transition rate:8ºC per minute.Test Duration:1000 cyclesSample Size:Minimum 15 unitsFunctional Verification:Pre and post ATE testing as well as ATE testing at the250 cycles.Applicable standard:JESD22-A104DPage 5 of 13
3.3. Temperature Humidity Bias (THB)THB Test ConditionsInput Voltage:Nominal Input Voltage.Output Conditions:Minimum loadTemperature:85ºC, 85%RHTest Duration:1000 hrs.Test Monitoring:Continuous Monitoring. Full functional ATE testing every250 hrsQuantity Tested:Minimum quantity of 10.Applicable standard: JESD22-A101CPage 6 of 13
3.4. Low Temperature Storage Test ( LTS)Test Temperature:-65ºC, Non Biased.Test Duration:1000 HoursSample Size:3 unitsFunctional Verification:Pre and post ATE testing as well as ATE testing at the250 hour test points.Applicable standard:JESD22–A1193.5. High Temperature Storage Test ( HTS)Test Temperature:125ºC, Non Biased.Test Duration:1000 HoursSample Size:13 unitsFunctional Verification:Pre and post ATE testing as well as ATE testing at the250 hour test points.Applicable standard:JESD22-A103-DPage 7 of 13
3.6. Highly Accelerated Life Test (HALT)3.6.1. HALT Test DetailTest Standard: Internal Vicor specification DP-0265HALT test equipment:Model:QualMark Typhoon 2.0 calibration.Equipment Limitations:Maximum air temperature of 200ºCMinimum air temperature of – 100ºCMaximum vibration level of 75 GrmsVibration type:Omni-axis vibration system.Typical setup sample.Product is mounted in a manner which mimics a customer application.Page 8 of 13
Test Conditions:a.Low Temp – Product low temperature operation specification verified,followed by reducing temperature to minimum operating temperature ofchamber to induce failure.b.High Temp - Product maximum operating temperature specificationverified, followed by increasing temperature to product shutdown orproduct failure.Page 9 of 13
c.Rapid Thermal Cycling – 5 rapid temperature cycles from maximum tominimum operating temperature under full load.Sample Profiled.Random Vibration Test – Sample product exposed to increasing levelsof vibration to point of failure to establish destruct point, remainingsamples exposed to a vibration level 25% less than destruct point.Sample Profilee.Combined Stresses Test - Product temperature cycled under load for 5cycles with increasing vibration levels to test structural integrity ofpackage.f.Vibration Destruct limits. Product samples vibrated to point of failure.Page 10 of 13
3.7. Random Vibration Testing (Operating)-A total of 3 samples are exposed to the test environment noted below at an external testlaboratory. All units are ATE tested pre and post exposure to vibration test.Units are also inspected for any signs of damage with no anomalies noted.Test standard:MIL-STD-810FTest Conditions:Method 514.5, Procedure I, Category 14, helicopter AH-6J Main Rotorwith overall level of 5.6grms, 4 hrs per axis.3.8. Mechanical Shock (Operating)-A total of 3 samples are exposed to the test environment noted below. All units are tested preand post exposure to shock testing.Units are also inspected for any signs of damage.Test Standard:MIL-STD-810FTest Conditions:Method 516.5, Procedure I, Functional shock 40G, total of 18 shocks.Product mounted on an evaluation board.3.9. Salt FogA total of 3 samples are exposed to the test environment noted below at an external testlaboratory. Units are also inspected for any signs of damage.Test Standard:MIL-STD-810FTest Conditions:Method 509.4.Page 11 of 13
3.10. Humidity TestA total of 10 samples are exposed to the test environment noted below.Test Standard:MIL-STD-810FTest Conditions:Method 507.4, 95% Relative Humidity.3.12. Through-Hole SolderabilityThree devices are tested in-house to the referenced standard.Test standard:MIL-STD-202GTest Conditions:Method 208H 8hr aging.3.13. ESD Classification Testing.Human Body Model (JEDEC JS-001-2012 Table 2B) Units meet class 1C– Qty 6Charged Device Model (JESD22-C101E) Units meet Class II - Qty 63.14. AccelerationThree devices are tested to the referenced standard at an external test laboratory.Test standard:MIL-STD-810FTest Method:Method 513.5, Procedure II, 2-7g, 6 directions.3.15. AltitudeThree devices are tested to the referenced standard at an external test laboratory.Test standard:MIL-STD-810FTest Method:Method 500.4, Procedure I and II, Conditions, 40k feet and 70k.Page 12 of 13
3.16. Explosive AtmosphereOne device is tested to the referenced standard at an external test laboratory.Test standard:Test Method:MIL-STD-810FMethod 511.4, Procedure I, Operational.4. Product RequirementsAll products which undergo testing are manufactured using the standard process.5. Testing RequirementsAll products are tested at the scheduled intervals as outlined in the test datasheets or as dictated bythe test standard specific to the individual test.Definition of Electrical Failure: Components that are no longer generating valid output voltageare considered hard failures. These components must be evaluated to root cause. Changes inelectrical performance (parameters outside acceptable tolerance limits of specification) or electricalfailures caused by thermal transitions require that Vicor perform an evaluation.Corrective Action – All product failures must be fully investigated, determining root cause andassigning corrective actions as deemed appropriate.Page 13 of 13
Functional Verification: Pre and post ATE testing as well as ATE testing at the 250 hour test points. Applicable standard: JESD22-A119 3.5. High Temperature Storage Test ( HTS) Test Temperature: 125ºC, Non Biased. Test Duration: 1000 Hours Sample Size: 13 units Functional Verification: Pre and post ATE testing as well as ATE testing at the