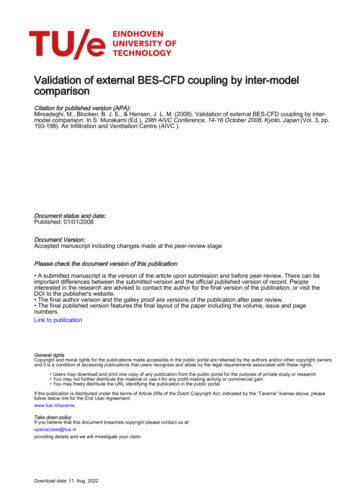
Transcription
Validation of external BES-CFD coupling by inter-modelcomparisonCitation for published version (APA):Mirsadeghi, M., Blocken, B. J. E., & Hensen, J. L. M. (2008). Validation of external BES-CFD coupling by intermodel comparison. In S. Murakami (Ed.), 29th AIVC Conference, 14-16 October 2008, Kyoto, Japan (Vol. 3, pp.193-198). Air Infiltration and Ventilation Centre (AIVC ).Document status and date:Published: 01/01/2008Document Version:Accepted manuscript including changes made at the peer-review stagePlease check the document version of this publication: A submitted manuscript is the version of the article upon submission and before peer-review. There can beimportant differences between the submitted version and the official published version of record. Peopleinterested in the research are advised to contact the author for the final version of the publication, or visit theDOI to the publisher's website. The final author version and the galley proof are versions of the publication after peer review. The final published version features the final layout of the paper including the volume, issue and pagenumbers.Link to publicationGeneral rightsCopyright and moral rights for the publications made accessible in the public portal are retained by the authors and/or other copyright ownersand it is a condition of accessing publications that users recognise and abide by the legal requirements associated with these rights. Users may download and print one copy of any publication from the public portal for the purpose of private study or research. You may not further distribute the material or use it for any profit-making activity or commercial gain You may freely distribute the URL identifying the publication in the public portal.If the publication is distributed under the terms of Article 25fa of the Dutch Copyright Act, indicated by the “Taverne” license above, pleasefollow below link for the End User Agreement:www.tue.nl/taverneTake down policyIf you believe that this document breaches copyright please contact us at:openaccess@tue.nlproviding details and we will investigate your claim.Download date: 11. Aug. 2022
Mirsadeghi, M., Blocken, B.J.E. & Hensen, J.L.M. (2008).Validation of external BES-CFD coupling by inter-model comparison.In MURAKAMI, S (Ed.), 29th AIVC Conference, 14-16 October 2008, (3, pp. 193-198).Kyoto: Air Infiltration and Ventilation CenterValidation of external BES-CFD coupling by inter-model comparisonM. Mirsadeghi, B. Blocken, J.L.M. HensenBuilding Physics and Systems, Technische Universiteit Eindhoven, the NetherlandsABSTRACTConflation of computational fluid dynamics(CFD) and building energy simulation (BES)has been used in recent years in order toimprove the estimation of surface coefficientsfor studies on thermal comfort, mold growthand other performance aspects of a building.BES can provide more realistic boundaryconditions for CFD, while CFD can providehigher resolution modelling of flow patternswithin air volumes and convective heat transfercoefficients (CHTC) for BES. BES and CFDcan be internally or externally coupled. Internalcoupling is the traditional way of expandingsoftware by which the code is expanded byadding new modules and it entails a lot of effortin terms of debugging, maintenance etc. On theother hand, by external coupling differentexisting numerical packages work together,using the latest advances already implementedin them.This paper focuses on the validation of anewly developed prototype performing theexternal coupling of BES and CFD. Thevalidation procedure involves an inter-modelcomparison between a conjugate heat transfermodel and the prototype.1. INTRODUCTIONIntegration of BES tools with CFD by usinginternal coupling has been investigated forindoor air climate with different degrees ofcomplexity (Negrao, 1995; Zhai, 2003;Beausoleil-Morrison, 2000). By this approach aCFD module is developed within a BESenvironment. Due to this coupling strategy, thefinal numerical package might suffer fromcertain limitations in the long run. On the otherhand, developing and maintaining one singlepackage to include all geometrical and physicaldomains is expensive and includes: thebackground research, development of a pilotprogram, improvement of the software etc.(Maver and Ellis, 1982).A solution which has been adopted recentlyis run-time external coupling of distributedapplications. By this approach the existingnumerical packages for specific geometrical orphysical domains work together and exchangedata at predefined or calculated time steps. Ithas been recognized and justified that the finaldistributed simulation environment is moreflexible, practical and powerful than the sum ofthe individual software programs (Hensen,2002).In the past, there were some attempts tovalidate external coupling between ESP-r (BES)and FLUENT (CFD) by using experimental dataand inter-model comparisons for room airtemperature and surface coefficients (Djunaedy,2005). Because of uncertainties associated withexperimental data and the discrepanciesobserved in the other validation technique forCHTC, a new inter-model comparisonprocedure is proposed. In this inter-modelcomparison, a CFD conjugate heat transfersimulation is used to assess the performance ofexternal BES-CFD coupling, focusing on thevalidation of the external coupling for averageair temperature, surface temperature and CHTC.The conjugate heat transfer model performs thecoupled simulation of solid and fluid domaincompletely within CFD. In BES-CFD coupling,
CFD is only applied for the fluid domain andthen the transfer coefficients are passed to BESwhich is mainly responsible for the soliddomain.This paper is structured as follows. First themethodology and the model description areexplained. Then the different steps necessary forthe conjugate heat transfer simulations for acubic cavity in CFD are described. Next, anexternal BES-CFD coupling for the same case ispresented. After, the response of the BES-CFDmodel and of the conjugate heat transfer modelto a 20 K step change in surface temperature arecompared to each other. Finally, a discussionand the conclusions of the work are presented.2. METHODOLOGYFigure 1 shows a schematic view of the intermodel comparison procedure. At the left handside the external BES-CFD coupling prototypeis shown. As it can be seen in this figure, theloose coupling strategy has been applied. In thisstrategy, two or more sets of equations aresolved separately and exchange data at eachpredefined or calculated time step. The internalsurface temperatures which are calculated byBES are passed to CFD at each time step. Thenthe calculated convective heat transfercoefficients (CHTC) from the converged CFDsolution is passed to BES for the next time stepcalculation. There is no iteration processbetween the two programs to get an agreementon the values at each time step.model or the CFD stand-alone model in thispaper. In other words, the boundary condition ofthe CFD model in the prototype is moved fromthe inside to the outside of the walls, and thusforming a single set of equations to be solved ateach time step (i.e. strong coupling).In order to perform the inter-modelcomparison, an effort has been put into makingall the CFD settings the same in the prototypeand in the CFD stand-alone simulations. Theyboth use also the same model and boundaryconditions which are explained in the followingsections.As indicated in Figure 1, there are two sets ofresults from the prototype and one set of resultfrom the CFD stand-alone which will becompared in the last section of the paper.3. DESCRIPTION OF THE MODELThe geometry of the model is inspired from(Tian and Karayiannis, 2000) in whichexperimental data for natural convection flow inan air filled cavity has been presented. Theseexperimental data are used to validate one of thesteps in developing the CFD stand-alone modelwhich will be explained in the next section. Forreducing the computational time, the length ofthe cavity was chosen 75 cm. Therefore thevolume of the cavity is half of that of the cavityused in the mentioned paper.Figure 1: Inter-model comparison procedure.Figure 2: Geometry of the cavity. Wall thickness 8(cm).At the right hand side of Figure 1, the fluidand solid domain which are solved separately inthe prototype, are both modeled and solvedwithin CFD including the radiation model toform what is called the conjugate heat transferThe boundary conditions are applied at theexterior wall surfaces. As indicated in Figure 2,the south wall is kept at 30 C and a 20 C stepchange at the surface temperature of the northwall is applied. The rest of the walls are
adiabatic. The construction used for all walls is8 (cm) concrete with the thermo-physicalproperties stated in Table 1.Table 1: Thermal properties of concreteThermal conductivity [W m-1 C-1]1.4Specific heat capacity [kJ/kg C-1]653Density [kg m-3]21004. CFD SIMULATIONSThe CFD commercial software FLUENT 6.3.26was selected to be used for all the simulationsthroughout this study.In order to obtain an optimum 3D grid for theCFD stand-alone simulation, three major stepshad to be done:First, a set of 2D simulations of just thecavity with zero wall thickness were performedand validated by experimental data provided by(Tian and Karayiannis, 2000). They measuredthe temperature and velocity field in an air filledcavity with the width and height of 75 (cm) anda depth of 150 (cm). Grid sensitivity analysis onthe 2D simulations was performed beforemoving to 3D simulation.Second, based on the optimum 2D grid andits validation, the maximum time step and theminimum number of iteration per time steprequired for the transient simulation wasobtained through sensitivity analysis.Finally, based on the settings obtained in theprevious steps, the 3D grid including the wallswas build for the final conjugate heat transfersimulation.1.58 109 which is the indication of a turbulentnatural convection flow.Figure 3 shows a typical result obtained fromthe finest mesh which is in good agreement withexperimental data (Figure 4). In these figures, Xand Y are dimensionless coordinates and L isthe width of the cavity. The same results wereobtained from 30 30 (coarsest) grid whichconforms with the work done by (Omri andGalanis, 2007). Therefore the computationaldomain with the grid size of 30 30 was chosenfor the next step. Note that the y value was lessthan unity for this case.Figure 3: Temperature distribution at different heightsobtained from 2D simulations.4.1. 2D simulations2D CFD simulations were performed on a nonuniform rectangular grid. Four different gridsizesof30 30,50 50,100 100 and 150 150 were tested. Theresiduals, variables and y value were monitoredand checked. The k-ω model was chosen formodelling the turbulence and enhanced walltreatmentwasapplied.Boussinesqapproximation was considered while solving themomentum equation. To account for theradiation exchange between surfaces in thecavity, the S2S radiation model available inFLUENT was chosen. The correspondingRayleigh number in the experiment was equal toFigure 4: Temperature distribution measured by (Tian andKarayiannis, 2000).
4.2. Best settings for 2D transient simulationHaving the grid ready from the previous step, aset of transient CFD simulations wereperformed in order to investigate the sensitivityof the residuals and the variables to the size oftime step and the number of iterations requiredper time step. The boundary conditions are thesame as described in section 3. Time stepslarger than 2 seconds caused some oscillation inthe prediction of temperature distribution andalso in convergence. In Figure 5, the differencebetween the predicted average CHTC on thesouth wall and that of the reference case can beobserved. The reference case is the one with 100iterations per time step which leads to residualslower than 10-6.As it can be seen from the Figure 5, thedifference between the reference and the casewith 10 iterations per time step is notremarkable. Furthermore, since the primaryfocus of this study is the validation of thecoupling, the accuracy of the case with 10iterations per time steps lies within anacceptable range for this purpose.surface temperatures and convective heattransfer coefficients were extracted. Theseresults are compared to those of BES-CFDcoupling in section 6.5. BES-CFD COUPLINGA loose coupling strategy was implementedbetween an open source building performancesimulation software (ESP-r) and the commercialCFD package FLUENT. The 3D grid obtainedin CFD stand-alone section excluding the wallswas used to calculate the fluid domain (Figure7).Figure 6: 3D computational grid for the CFD stand-alonemodel.Figure 5: The impact of different iterations per time stepon the predicted average CHTC on the south wall.4.3. 3D simulationThe 3D grid including the walls (solid domain)was made based on the previous steps (Figure6). In ESP-r, the 1D heat conduction equation issolved by the control volume method while theheat transfer mechanism in the solid domain inthe present CFD model is 3D. In order to makethis 3D effect less important, the corners of thecube were eliminated. The CFD simulation wasrun with the boundary conditions and thesettings described in sections 2 and 3,respectively. The average cavity temperature,Figure 7: 3D computational grid for BES-CFD coupling.In Figure 8, the variation of Rayleigh numberversus time in the cavity has been plotted afterthe temperature jump at the exterior northsurface. Due to the presence of turbulence in thecavity, the coupling mechanism shown in Figure9 was considered. In this coupling, at each timestep the internal surface temperatures areextracted from BES and passed to FLUENT. InFLUENT, we first perform a steady statesimulation with a one-order-lower Rayleigh
109Rayleigh numbernumber and then a transient simulation with thereal Rayleigh number. Then the CHTCscalculated by FLUENT are passed to ESP-r forthe next time step.The coupling was performed for one hourwith the time step equal to 1 minute. Runningthe coupling with the same time step as CFDstand-alone would increase the computationaltime dramatically to 600 days which is notefficient. Then the coupling was terminated andESP-r was run for more 2 hours in a stand-alonemode. The results are compared and presentedin the next section.for internal CHTC (Alamdari and Hammond,1982) is applied. As it can be observed fromFigure 10, there is 1 C difference between theresults for this simple geometry while usingempirical correlation.0.40.3Figure 10: Evolution of average temperature in differentcases.0.20.100246810ΔT between the cold and hot wall ( C)Figure 8: Rayleigh number variation in the co-simulation.Figure 11: Comparison of average surface temperature forthe north wall.Figure 9: Coupling mechanism for the BES-CFDprototype.6. RESULTS AND DISCUSSIONIn order to evaluate the performance of theexternal coupling, the results from section 4 and5 are presented and compared to each other. Theaverage cavity temperature from the BES-CFDcoupling is compared with that of CFD standalone and BES stand-alone in Figure 10.During the first hour of simulation the intermodel comparison of average temperature are ingood agreement. At the end of the fist hour,CFD is switched off and BES is used to predictthe average temperature. While using BESstand-alone, the empirical correlation equationFigure 11 shows the average surfacetemperature for the north wall. In CFD standalone, the 3D heat transfer in the solid whichleads to a temperature distribution at the surfaceof the wall may contribute to the sooner jumpbefore 0.2 (s) in the average surfacetemperature. The temperature contours areplotted for a typical time step in Figure 12. Incontrast, in BES-CFD coupling there is notemperature distribution at the surfaces since thesurface temperature is calculated from a 1Dconduction equation in BES and passed to CFDas a uniform boundary condition at each timestep. Figure 13 illustrates the comparison ofCHTC for the north wall. The differencebetween the two curves originates from thedifference between the time step chosen and
also 1D and 3D heat transfer in the solid domainin BES-CFD coupling and CFD stand-alone,respectively. Surface discretization in BES canenhance the conformity of curves in Figure 11and Figure 13 and play an important role whenstudying mold growth and condensation.38.33738.238.1Figure 12: Contours of temperature at the north wall(inside face).Average CHTC forthe north wall (W/m2K)32.521.51CFDstand alone0.5coupling000.20.40.6Time (hours)The authors would like to appreciate thefinancial support from “Institute for thePromotion of Innovation by Science andTechnology in Flanders” (IWT-Vlaanderen) aspart of the SBO-project IWT 050154 “Heat, Airand Moisture Performance Engineering: a wholebuilding approach”.9. REFERENCES38.4388. ACKNOWLEDGEMENT0.81Figure 13: Comparison of average CHTC for the northwall.7. CONCLUSIONSAn inter-model comparison between BES-CFDcoupling and CFD stand-alone was performed.The comparison led to the following remarks: The external coupling is validated byapplying this approach. For such a simple geometry, 1 C differencewas observed if there is no CFD involved inthe simulation. For complex geometry thisdifference might be more remarkable,highlighting the impact of coupling CFDwith BES. The discrepancies in CHTC and surfacetemperature curves signifies the need forsurface discretization in BES tools whilefocusing on certain performance indicatorssuch as condensation and mold growth.Alamdari, F., Hammond, G. P. (1982) Improved DataCorrelations for Buoyancy-Driven Convection inRooms Building Services Eng. Res. and Tech. 4(3)106-12Beausoleil-Morrison, I. (2000). The Adaptive Coupling ofHeat and Air Flow Modelling Within DynamicWhole-Building Simulation, PhD Thesis, EnergySystems Research Unit, Department of MechanicalEngineering, University of Strathclyde, Glasgow, UK.Djunaedy, E. (2005). External coupling between buildingenergy simulation and computational fluid dynamics,PhD thesis, Technische Universiteit Eindhoven,Eindhoven, the Netherlands.Hensen, J. L. M. (2002). Simulation for performancebased building and systems design: some issues andsolution directions, in Proc. of 6th Int. Conf. onDesign and Decision Support Systems in Architectureand Urban Planning, Netherlands.Maver, T. W., Ellis, J. (1982). Implementation of anenergy model within a multi-disciplinary practice,Proceedings of the CAD82, Brighton, UK.Negrao, C. O. R. (1995). Conflation of ComputationalFluid Dynamics and Building Thermal Simulation,PhD Thesis, Energy Systems Research Unit,Department of Mechanical Engineering, University ofStrathclyde, Glasgow, UK.Omri, M. Galanis, N. (2007) Numerical analysis ofturbulent buoyant flows in enclosures: Influence ofgrid and boundary conditions. International Journal ofThermal Sciences 46, 727–738Tian, Y.S. Karayiannis, T.G. (2000) Low turbulencenatural convection in an air filled square Cavity Part I:the thermal and fuid fow fields. International Journalof Heat and Mass Transfer 43, 849–866Zhai, Z. (2003). Developing an integrated design tool bycouplingbuildingenergysimulationandcomputational fluid dynamics, PhD thesis,Department of Architecture, Massachusetts Institute ofTechnology.
comparison, a CFD conjugate heat transfer simulation is used to assess the performance of external BES-CFD coupling, focusing on the validation of the external coupling for average air temperature, surface temperature and CHTC. The conjugate heat transfer model performs the coupled simulation of solid and fluid domain completely within CFD.