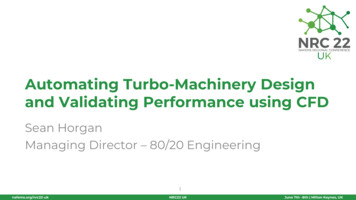
Transcription
Automating Turbo-Machinery Designand Validating Performance using CFDSean HorganManaging Director – 80/20 Engineering1nafems.org/nrc22-ukNRC22 UKJune 7th –8th Milton Keynes, UK
AGENDA – ‘NAFEMS UK – 7th June 2022’ Brief Company Overview – 80/20 Engineering Ltd Automated Turbo-Machinery Design Case Study from Amarinth Pumps The Amarinth Design Process Case Study from Selwood Pumps Selwood’s Competing Performance Requirements Conclusions2nafems.org/nrc22-ukNRC22 UKJune 7th –8th Milton Keynes, UK
80/20 Engineering LtdOverview3nafems.org/nrc22-ukNRC22 UKJune 7th –8th Milton Keynes, UK
80/20 Engineering (Formed in 2010) The Value 80/20 Engineering delivers: Design Engineers need to evaluate many concepts quickly andeasily, so need a real alternative to traditional physical testing CFD/CAE tools for Product Development Some Flow/Thermal/Structural applications are very complex innature and often companies just don’t possess the resourcesand/or competencies to perform in-house simulation . High Level Simulation Consultancy4
8020CFD SolutionsCFturbo‘Turbo-Machinery DesignSoftware’‘Automated ShapeOptimization Software’Simerics-MP (PumpLinx)CAESES‘CFD Analysis for allFluid Machinery’5nafems.org/nrc22-ukNRC22 UKJune 7th –8th Milton Keynes, UK
Some of our CustomersQinetiQ - Delivering Customer Focused Solutions6nafems.org/nrc22-ukNRC22 UKJune 7th –8th Milton Keynes, UK
Automating Turbo-Machinery DesignOverview7nafems.org/nrc22-ukNRC22 UKJune 7th –8th Milton Keynes, UK
The Process of Turbo-Machinery Design GENERAL Willi Bohl, Wolfgang ElmendorfStrömungsmaschinen 1 2Vogel-Verlag, 2008Werner FisterFluidenergiemaschinen Bd. 1 und 2Springer-Verlag, 1984 und 1986Wolfgang KalideEnergieumwandlung in Kraft- und ArbeitsmaschinenHanser-Verlag, 1989Carl Pfleiderer, Hartwig PetermannStrömungsmaschinenSpringer-Verlag, 1991Joachim RaabeHydraulische Maschinen und AnlagenVDI-Verlag, 1989Arnold Whitfield, Nicholas C. BainesDesign of Radial TurbomachinesLongman Scientific & Technical, 1990 PUMPS Johann F. GülichKreiselpumpenSpringer-Verlag, 1999Kurt Holzenberger, Klaus JungKreiselpumpen LexikonKSB AG, 1989Val S. Lobanoff, Robert R. RossCentrifugal Pumps, Design & ApplicationGulf Professional Publishing, 1992Michael SchwanseStrömungsmechanische Auslegung und Nachrechnung von radialen und diagonalenKreiselpumpenlaufrädernDissertation, TU Dresden, 1990A. J. StepanoffCentrifugal and Axial Flow PumpsJohn Wiley & Sons, 1957 PUMPS (Continued ) John TuzsonCentrifugal pump designJohn Wiley & Sons, 2000Walter WagnerKreiselpumpen und KreiselpumpenanlagenVogel-Verlag, 1994Gotthard WillKreiselpumpenin: Taschenbuch Maschinenbau, Band 5hrsg. von Hans-Joachim Kleinert, Verlag Technik Berlin, 1989 FANS Leonhard Bommes, Jürgen Fricke, Reinhard GrundmannVentilatorenVulkan-Verlag, 2003Bruno EckVentilatorenSpringer-Verlag, 1991Thomas CarolusVentilatorenTeubner-Verlag, 2003Hans Werner RothOptimierung von Trommelläufer-VentilatorenDissertation, Universität Karlsruhe, 1980 R.A. WallisAxial flow fans and ductsJohn Wiley&Sons, 19838nafems.org/nrc22-ukNRC22 UKJune 7th –8th Milton Keynes, UK
The Process of Turbo-Machinery Design TURBINES COMPRESSORS Ronald H. AungierTurbine AerodynamicsASME Press, 2006Hany Moustapha, Mark Zelesky, Nicholas C. Baines, Davide JapikseAxial and Radial TurbinesConcepts NREC, 2003 Ronald H. AungierCentrifugal CompressorsASME Press, 2000Ronald H. AungierAxial-flow CompressorsASME Press, 2003Klaus H. LüdtkeProcess Centrifugal CompressorsSpringer-Verlag, 2004Bruno Eckert, Erwin SchnellAxial- und RadialkompressorenSpringer-Verlag, 1980Davide JapikseCentrifugal Compressors Design and PerformanceConcepts ETI, 1996N. A. CumpstyCompressor aerodynamicsKrieger publishing, 2004Ernst LindnerTurboverdichterin: Taschenbuch Maschinenbau, Band 5hrsg. von Hans-Joachim Kleinert, Verlag Technik Berlin, 1989Arthur J. WennerstromDesign of highly loaded axial-flow fans and compressorsConcepts ETI, 2000Members of the staff of Lewis Research CenterAerodynamic design of axial-flow compressorsNASA SP-36, Washington, D.C. 1965P. de HallerDas Verhalten von Tragflügelgittern in Axialverdichtern und im WindkanalBrennstoff-Wärme-Kraft, Band 5, Heft 10, 1953Michael Casey and Chris RobinsonA method to estimate the performance map of a centrifugal compressor stageProceedings of the ASME Turbo Expo 2011, ASME GT2011- 45502 O. E. BaljeA study on design Criteria and matching of Turbomachines: Part A - Similarity Relations andDesign Criteria of TurbinesJournal of Engineering for Power, January 1962, p. 83-102 Further literatureJohn D. Stanitz, Vasily D. PrianA rapid approximate method for the determining velocity distribution on impeller blades ofcentrifugal compressorsNACA Technical note 2421; July 1951John David Anderson, R. Grundmann, E. DickComputational Fluid Dynamics: An IntroductionSpringer-Verlag, 1996Redlich, O., Kwong, J.N.S.On the Thermodynamics of Solutions. V. An Equation of State. Fugacities of GaseousSolutions,Chemical Reviews. 44, No. 1, pp. 233–244, 1949Aungier, R.H.A Fast, Accurate Real Gas Equation of State for Fluid Dynamic Analysis Applications,Journal of Fluids Engineering, Vol. 117, pp. 277-281, 1995Soave, G.Equilibrium constants from a modified Redlich-Kwong equation of state.,Chemical Engineering Science. 27, No. 6, pp. 1197–1203, 1972Peng, D.Y., Robinson, D.B.A New Two-Constant Equation of State,Industrial and Engineering Chemistry: Fundamentals, Vol. 15: pp. 59–64, 1976Von Backström, Th. W.A unified correlation for slip factor in centrifugal impellersJournal of Turbomachinery, 2006; 128(1):1-10.Mason, E.A., u. S. C. SaxenaApproximate formulae for the thermal conductivity of gas mixturesPhys. Fluids 1 (1958), 361 Jakob AckeretZum Entwurf dicht stehender SchaufelgitterSchweizer Bauzeitung 120 (1942), S. 103-1089nafems.org/nrc22-ukNRC22 UKJune 7th –8th Milton Keynes, UK
Automating Turbo-Machinery DesignDriving Design Parameters Design point data:(1) Flow rate:pumps, ventilators: volume flow Qcompressors:mass flow m or volume flow Q (referring to total state on suction side)turbines:mass flow m(2) Energy transmission:pumps:head H or pressure difference Δptventilators:pressure difference Δptcompressors:total pressure ratio πt or total pressure difference Δpt or specific work Yturbines:total pressure ratio πtt or specific work Y or Machine-Mach-number M1 orInlet peripheral speed u1 or Inlet diameter d1 or total-to-static pressure ratio πts(3) Rotational Speed (RPM) Direction of impeller rotation: seen toward hub backside; for 3D model only Casing efficiency: includes losses of all none rotating components (stators, volute); used for overall efficiency calculation inconnection with the impeller efficiency (for information only) Fluid properties: density only for incompressible fluid; perfect gas or simple real gas model with compressibility factor forcompressible fluids; some default fluids available – can be customized Inflow definition: Inflow swirl as flow angle α, swirl number δr or swirl energy δY;additional state properties for compressible fluids10nafems.org/nrc22-ukNRC22 UKJune 7th –8th Milton Keynes, UK
A Design in 3D, that can be manufactured efficiently, isthe goal11nafems.org/nrc22-ukNRC22 UKJune 7th –8th Milton Keynes, UK
A Turbo-Machine must also meet the SystemPerformance Curve Objectives12nafems.org/nrc22-ukNRC22 UKJune 7th –8th Milton Keynes, UK
The Solution is Turbo-Machinery Design Software3D modelTurbo-MachineryDesign Software thatfits into the existingdesign process13nafems.org/nrc22-ukNRC22 UKJune 7th –8th Milton Keynes, UK
Computer Aided Engineering (CAE) Design ValidationCFD/FEA SimulationGrid generationSimerics-MP, ANSYS, FineTurbo,PumpLinx, STAR CCM , CFdesign,OpenFOAM ICEM-CFD, TurboGrid,Pointwise, AutoGrid, Gambit Dimensioning,DesignTMDS ProductOptimizationinteractivley or automaticallyCADProductMeasurementCatia, SolidWorks, NX,CREO/ProE, Inventor, BladeModeler,SolidEdge.Rapid Prototyping,Validation14nafems.org/nrc22-ukNRC22 UKJune 7th –8th Milton Keynes, UK
CFD Tools in use within Turbo-MachineryTurbo-MachineryDesign SoftwareGrid generationCFD simulationANSYSICEM-CFD, TurboGridCFX, FluentPointwisePointwise/ Gridgen any solver ANSYSG/Turbo, GambitFluentNumecaAutoGrid, IGGFINE/TurboSiemensSTAR CCM SimericsSimerics-MP (PumpLinx)ADSKADSK CFD (CFdesign)OpenFOAM15nafems.org/nrc22-ukNRC22 UKJune 7th –8th Milton Keynes, UK
The Amarinth Design ProcessAmarinth Pumps Ltd16nafems.org/nrc22-ukNRC22 UKJune 7th –8th Milton Keynes, UK
Amarinth Pumps Centrifugal Pump Manufacturer – Woodbridge, SuffolkFocus on Chemical Process, Oil & Gas, harsh environmentsBespoke Pump Design RequirementsInnovation and Agility are seen as a competitive advantage17nafems.org/nrc22-ukNRC22 UKJune 7th –8th Milton Keynes, UK
The Amarinth Be-Spoke Design Process Proposed 2D Profiles from Amarinth’s experience Imported into TMDS The Meridional Blade Profile is then designed with TMDS with additionalinputs of flow, head and impeller speed The full 3D Impeller is then produced so that all functional requirements aremet such as the inlet area between vanes, blade angle distribution andmeridional area progression18nafems.org/nrc22-ukNRC22 UKJune 7th –8th Milton Keynes, UK
The Amarinth CFD Verification Process Low NPSH, Stable Performance Curves and capable of operating as low shear are all typical requirements forAmarinth’s Pumps. Therefore an initial CFD Analysis is carried out on a single passage to verify Impeller’s performance This process is applicable to both the Single and Double Entry Pumps being designed19nafems.org/nrc22-ukNRC22 UKJune 7th –8th Milton Keynes, UK
The Amarinth Design Exploration Workflow With a contract secured full 3DPump assemblies are createdincluding the volutes for furtherCFD Analyses prior to manufacture. The full 3D geometries areexported to 3rd party meshing toolsto enable the CFD work. By changing the parameters youcan quickly regenerate thegeometry and reanalyse.20nafems.org/nrc22-ukNRC22 UKJune 7th –8th Milton Keynes, UK
Selwood’s Competing PerformanceRequirementSelwood Pumps Ltd21nafems.org/nrc22-ukNRC22 UKJune 7th –8th Milton Keynes, UK
Selwood Pumps Leaders in Pump Rental Solutions and Manufacture – ChandlersFord, Hampshire Pump Sets for water, environmental and construction industries Needed to reduce reliance on external pump design expertise New Pump ranges needed with better performance whilst retainingsolids handling capability22nafems.org/nrc22-ukNRC22 UKJune 7th –8th Milton Keynes, UK
Pressure Head and Solids Handling Same Turbo-Machinery Design SoftwareUsed Complete 3D Pump Assembly Designedvirtually Pressure Head requirement satisfied bycalling for restriction to Solids Handlingperformance. Integrated CFD capability needed toovercome conflict23nafems.org/nrc22-ukNRC22 UKJune 7th –8th Milton Keynes, UK
Pressure Head and Solids Handling Additional Manufacturing Constraints ofHub and Impeller Diameter imposed Volute Design included a specified outletpipe diameter Idealized Full 3D Design created usingautomated tools24nafems.org/nrc22-ukNRC22 UKJune 7th –8th Milton Keynes, UK
An Initial Design – Results Animation25nafems.org/nrc22-ukNRC22 UKJune 7th –8th Milton Keynes, UK
Pressure Head and Solids Handling Initial Design of Pump validated to deliver sufficient pressure head using Integrated CFDMinimal Cavitation presentMinimum Gaps between the Impeller blades too narrow25 design iterations tested ‘virtually’ within 2 weeks to resolve the conflict26nafems.org/nrc22-ukNRC22 UKJune 7th –8th Milton Keynes, UK
Pressure Head and Solids Handling Design Variables Modified Blade thickness, Impeller size, Wrapangle, Leading edge, Larger fillets,Improved volute cutwater, Shorterblades, Altered hub27nafems.org/nrc22-ukNRC22 UKJune 7th –8th Milton Keynes, UK
CFD SummaryDesign VariantHead (m)Power (kw)EfficiencyEarly Design36.0716.8772.8Thicker Blades, Smaller Impeller32.6915.1473.5Smaller Wrap Angle33.2815.6672.3Smaller Impeller Diameter31.7714.6873.7Reduce Impeller Diameter and Wrap Angle32.5214.9674.0Moving Leading Edge Outward29.5614.2770.5Reduce Impeller Diameter32.9515.1773.9Large Impeller Fillets, Improve Volute Cutwater32.1814.8673.7Previous with Reduced Impeller outlet width31.5114.5473.8Previous with Reduced Impeller diameter to 242.5mm32.8414.9474.8Previous with Reduced Impeller diameter to 240mm32.5214.8774.2Reduced Impeller diameter 240mm and reduced blades28.313.273.028nafems.org/nrc22-ukNRC22 UKJune 7th –8th Milton Keynes, UK
Performance Validation To validate the design, a full pumpassembly was simulated and tested Additional simulations were run tocalculate the NPSH performance Hydraulic Forces acting in Radialand Axial directions extracted forBearing selection29nafems.org/nrc22-ukNRC22 UKJune 7th –8th Milton Keynes, UK
40Performance Validation35 Pressure Head versus Flow-Rate Power and EfficiencyPressure Head r (kW)510400805030Efficiency (%)5012100Flow Rate150200(m3/hour)620410200050100150Flow Rate (m3/hour)nafems.org/nrc22-uk20025030NRC22 UKJune 7th –8th Milton Keynes, UK250
Design Point -125 m3/hr31nafems.org/nrc22-ukNRC22 UKJune 7th –8th Milton Keynes, UK
Design Point -125 m3/hrAnimation of Impeller with Pressures and Velocities on ParticlesNovember, 2017nafems.org/nrc22-uk32NRC22 UKJune 7th –8th Milton Keynes, UK
Performance Validation1800 Radial and Axial Forces on theImpeller for Structural Analysisand Bearing selectionRadial Force .00Flow RateAxial Force (Newtons)Average Radial Force150010005000-500 0200.00150.00200.00250.00(m3/hour)Maximum Radial Force250.00Flow Rate (m3/hour)Average Axial ForceMaximum Axial Force33nafems.org/nrc22-ukNRC22 UKJune 7th –8th Milton Keynes, UK
Design Point -125 m3/hr34nafems.org/nrc22-ukNRC22 UKJune 7th –8th Milton Keynes, UK
Automating Turbo-Machinery DesignConclusions The Implementation of TMDS needs to be able suit user preference CFD Integration within the TMDS enables more innovation and fasterturnaround Tremendous opportunity remains to reduce the islands of automation foundwithin industry Using Engineering Software tools needs to bring advantage over physicaltesting and prototyping – 80/20 Rule The key is flexibility and the user interaction of the software35nafems.org/nrc22-ukNRC22 UKJune 7th –8th Milton Keynes, UK
Sean Horgan, Director – 80/20 Engineering Ltdsean.horgan@8020ngineering.comTel: 44(0) 1494 216080Direct: 44 (0) 01494 325014Mobile: 44 (0) 7879 432669www.8020Engineering.comThank You!36nafems.org/nrc22-ukNRC22 UKJune 7th –8th Milton Keynes, UK
CFD Tools in use within Turbo-Machinery Grid generation CFD simulation ANSYS CFX, Fluent Pointwise any solver ANSYS Fluent Numeca FINE/Turbo STAR CCM Simerics-MP (PumpLinx) ADSK CFD (CFdesign) OpenFOAM ICEM-CFD, TurboGrid Pointwise/ Gridgen G/Turbo, Gambit AutoGrid, IGG Siemens Simerics ADSK Turbo-Machinery Design Software 15