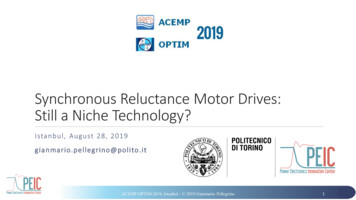
Transcription
Synchronous Reluctance Motor Drives:Still a Niche Technology?Istanbul, August 28, 2019gi a n mar io.pel legr ino@poli to .itACEMP OPTIM 2019, Istanbul - 2019 Gianmario Pellegrino1
Outline Introduction Politecnico di Torino and the Power Electronics Innovation Center (PEIC) The Synchronous Reluctance Motor Background: history of the SyR motor technology Where we Stand Today’s Challenges SyR-e: Synchronous Reluctance Evolution ConclusionACEMP OPTIM 2019, Istanbul - 2019 Gianmario Pellegrino2
Politecnico di TorinoGalileo Ferraris(1847 – 1897)Founded in 1859, as Technical School for EngineersPolitecnico di Torino since 1906Home to Galileo Ferraris, pioneer of electricalengineering. He was a professor here, and a Senator ofthe former Reign of Italy35000 students, 700 PhD students850 Faculty members, 890 Administrative Technical staffBudget (2018): 250 M (55% State, 12% student fees, 30% projects)Tuition fee:1000 - 2000 / yearACEMP OPTIM 2019, Istanbul - 2019 Gianmario Pellegrino3
PEIC: The Power Electronics Innovation CenterInter-Departmental Center dedicated to PowerElectronics, from Si wafer to final applications,founded in 2017http://www.peic.polito.it/20 faculty members, 2 technicians, 25 PhD studentsKey lines of application: Transportationelectrification, Energy, IndustryCapability of delivering TRL4 demonstrators,support to higher-TRL prototypingHome to SLED 2019, September 9-10 2019https://attend.ieee.org/sled-2019/ACEMP OPTIM 2019, Istanbul - 2019 Gianmario Pellegrino4
PEIC: The Power Electronics Innovation CenterInter-Departmental Center dedicated to PowerElectronics, from Si wafer to final applications,founded in 2017http://www.peic.polito.it/20 faculty members, 2 technicians, 25 PhD studentsKey lines of application: Transportationelectrification, Energy, IndustryCapability of delivering TRL4 demonstrators,support to higher-TRL prototypingHome to SLED 2019, September 9-10 2019https://attend.ieee.org/sled-2019/ACEMP OPTIM 2019, Istanbul - 2019 Gianmario Pellegrino5
The Synchronous Reluctance Motor TechnologyACEMP OPTIM 2019, Istanbul - 2019 Gianmario Pellegrino6
Background: Synchronous Reluctance TorqueExcitation oflow reluctance rotor axisExcitation ofhigh reluctance rotor axisReluctance motors operate according to the principle of magnetic reluctance .The rotor consisting of air and iron has the least possible magnetic reluctance in one directionand the highest possible reluctance in the direction perpendicular to that. Because the systemalways moves toward the lowest magnetic reluctance, rotational movement results.Source: “Dynamic Energy Efficiency”, in Advance 1/2015, April 2015, Siemens AGACEMP OPTIM 2019, Istanbul - 2019 Gianmario Pellegrino7
Advantages of SyR Motors1. Standard distributed-winding stator2. Rotor simplicity- no windings substantial loss reduction, ease of manufacturing- no PMs cost reduction, no de-magnetization, no back-emf voltage when uncontrolled- low moment of inertia Dynamic performanceVs Asynchronous Motors:- smaller frame size per continuous torque or higher efficiency- faster speed dynamicsVs PM Synchronous Motors:- lower cost of production (no PM cost, ease of manufacturing)- higher transient overload capability (no demag)ACEMP OPTIM 2019, Istanbul - 2019 Gianmario PellegrinoSource: new.abb.com8
Advantages of SyR Motors1. Standard distributed-winding stator2. Rotor simplicity- no windings substantial loss reduction, ease of manufacturing- no PMs cost reduction, no de-magnetization, no back-emf voltage when uncontrolled- low moment of inertia Dynamic performanceVs Asynchronous Motors:- smaller frame size per continuous torque or higher efficiency- faster speed dynamicsVs PM Synchronous Motors:- lower cost of production (no PM cost, ease of manufacturing)- higher transient overload capability (no demag)ACEMP OPTIM 2019, Istanbul - 2019 Gianmario PellegrinoSource: new.abb.com9
Advantages of SyR Motors1. Standard distributed-winding stator2. Rotor simplicity- no windings substantial loss reduction, ease of manufacturing- no PMs cost reduction, no de-magnetization, no back-emf voltage when uncontrolled- low moment of inertia Dynamic performanceVs Asynchronous Motors:- smaller frame size per continuous torque or higher efficiency- faster speed dynamicsVs PM Synchronous Motors:- lower cost of production (no PM cost, ease of manufacturing)- higher transient overload capability (no risk for demagnetization)ACEMP OPTIM 2019, Istanbul - 2019 Gianmario PellegrinoSource: new.abb.com10
Control: Mandatory AspectsMTPA OperationSensorless Control (no encoder)The high efficiency at partial load is obtained viaMaximum Torque per Ampere operationThis keeps the variable speed SyR motor drivecost competitive respect to the asynchronouscounterpart (exception: servo applications;ACEMP OPTIM 2019, Istanbul - 2019 Gianmario Pellegrino11
Well Known DisadvantagesLow Power Factor and High Torque Ripple- low PF- high torque rippleNeed for precise Motor Commissioning (also said non standard control)- respect of MTPA law- stable Sensorless ControlHigh Speed Applications2- rotor ribs scale with 𝑛𝑛𝑚𝑚𝑚𝑚𝑚𝑚Low Speed Applications- high number of poles harmed by increase of p.u. excitation currentACEMP OPTIM 2019, Istanbul - 2019 Gianmario Pellegrino12
Well Known DisadvantagesLow Power Factor and High Torque Ripple- low PFWe will discuss each point later on- high torque rippleNon-standard control, need for precise Motor Commissioning- respect of MTPA law- stable Sensorless ControlHigh Speed Applications2- rotor ribs scale with 𝑛𝑛𝑚𝑚𝑚𝑚𝑚𝑚Low Speed Applications- high number of poles harmed by increase of p.u. excitation currentACEMP OPTIM 2019, Istanbul - 2019 Gianmario Pellegrino13
History of the Synchronous Reluctance Motor TechnologyACEMP OPTIM 2019, Istanbul - 2019 Gianmario Pellegrino14
1923: The Idea of Flux BarriersKostko, J.K., "Polyphase reaction synchronous motors,“American Institute of Electrical Engineers, Journal of the, 1923ACEMP OPTIM 2019, Istanbul - 2019 Gianmario Pellegrino15
1972: The Synduction MotorFirst exemplar for both variable speed(constant V/f) or direct online applicationCast aluminium cage in the rotor, designoptimized for best trade-off between a highpull-out torque (low 𝐿𝐿𝑞𝑞 ) and a low criticalfrequency of oscillation (high 𝐿𝐿𝑞𝑞 )Adoption limited to special applications, suchas textile industry (multiple motors driven withthe same converter, at same speed)Honsinger, V.B., “Synchronous reluctance motor”, US3652885, 1972 (Allis Chalmers, Ohio)Honsinger, V. B., "Inherently Stable Reluctance Motors Having Improved Performance," in IEEE Transactions onPower Apparatus and Systems, vol. PAS-91, no. 4, pp. 1544-1554, July 1972ACEMP OPTIM 2019, Istanbul - 2019 Gianmario Pellegrino16
1990s: Variable Speed DrivesWith the advent of modern power electronicsand vector control, the SyR Motor solutionbecame widely studied and developed(Flux Barriers) flux barriers Vs axially laminated (ALA) Motor design rules saliency maximization torque ripple minimization(ALA) Vector control schemes First sensorless control schemes[*][**][*] Kolehmainen, J. (2010). Synchronous reluctance motor with form blocked rotor. IEEE Transactions on Energy Conversion[**] Vagati, A. (1998) "Synchronous reluctance electrical motor having a low torque-ripple design." U.S. Patent No. 5,818,140ACEMP OPTIM 2019, Istanbul - 2019 Gianmario Pellegrino17
Technology Development TimelineSource: Google ScholarACEMP OPTIM 2019, Istanbul - 2019 Gianmario Pellegrino18
The Roaring NinetiesSource: Google ScholarACEMP OPTIM 2019, Istanbul - 2019 Gianmario Pellegrino19
Milestones: 19911991Lipo, T. A. "Synchronous reluctance machines - a viable alternative for ac drives?“ Electric Machines and Power Systems 19.6(1991): 659-671Xu, L., Xu, X., Lipo, T. A., Novotny, D. W. (1991). “Vector control of a synchronous reluctance motor including saturation andiron loss”, IEEE Transactions on Industry Applications, 27(5), 977-985.ACEMP OPTIM 2019, Istanbul - 2019 Gianmario Pellegrino20
Milestones: 19921992Vagati, A., Franceschini, G., Marongiu, I., & Troglia, G. P. (1992, October). “Design criteria of high performance synchronousreluctance motors”, In Conference Record of the 1992 IEEE Industry Applications Society Annual Meeting (pp. 66-73). IEEE.ACEMP OPTIM 2019, Istanbul - 2019 Gianmario Pellegrino21
Milestones: 19931993Staton, D. A., Miller, T. J. E., & Wood, S. E. (1993, July). “Maximising the saliency ratio of the synchronous reluctance motor”,In IEE Proceedings B (Electric Power Applications) (Vol. 140, No. 4, pp. 249-259). IET Digital Library.Betz, R. E., Lagerquist, R., Jovanovic, M., Miller, T. J., & Middleton, R. H. (1993). “Control of synchronous reluctance machines”,IEEE Transactions on Industry Applications, 29(6), 1110-1122.ACEMP OPTIM 2019, Istanbul - 2019 Gianmario Pellegrino22
Milestones: 19941994Matsuo, T., & Lipo, T. A. (1994). “Rotor design optimization of synchronous reluctance machine”, IEEE Transactions on EnergyConversion, 9(2), 359-365.Lagerquist, R., Boldea, I., & Miller, T. J. (1994). “Sensorless-control of the synchronous reluctance motor”, IEEE Transactions onIndustry Applications, 30(3), 673-682.Boldea, I., Fu, Z. X., & Nasar, S. A. (1994). “Performance evaluation of axially-laminated anisotropic (ALA) rotor reluctancesynchronous motors”, IEEE transactions on industry applications, 30(4), 977-985.ACEMP OPTIM 2019, Istanbul - 2019 Gianmario Pellegrino23
Milestones:19961996Kamper, M. J., Van der Merwe, F. S., & Williamson, S. (1996), “Direct finite element design optimisation of the cagelessreluctance synchronous machine”, IEEE Transactions on Energy Conversion, 11(3), 547-555.ACEMP OPTIM 2019, Istanbul - 2019 Gianmario Pellegrino24
Milestones: 19981998Vagati, A., Pastorelli, M., Francheschini, G., & Petrache, S. C. (1998), “Design of low-torque-ripple synchronous reluctancemotors”, IEEE Transactions on Industry Applications, 34(4), 758-765.ACEMP OPTIM 2019, Istanbul - 2019 Gianmario Pellegrino25
Milestones: 19991999Ha, J. I., Kang, S. J., & Sul, S. K. (1999). Position-controlled synchronous reluctance motor without rotational transducer. IEEEtransactions on Industry Applications, 35(6), 1393-1398.Consoli, A., Russo, F., Scarcella, G., & Testa, A. (1999). Low-and zero-speed sensorless control of synchronous reluctancemotors. IEEE Transactions on Industry Applications, 35(5), 1050-1057.ACEMP OPTIM 2019, Istanbul - 2019 Gianmario Pellegrino26
Milestones: 20002000Vagati, A., Pastorelli, M., Scapino, F., & Franceschini, G. (2000). Impact of cross saturation in synchronous reluctance motors ofthe transverse-laminated type. IEEE Transactions on Industry Applications, 36(4), 1039-1046.ACEMP OPTIM 2019, Istanbul - 2019 Gianmario Pellegrino27
Bottom LineBy 2000, the technology was ready, includingmotor design, vector control and sensorlesscontrol aspectsHowever, the interest on SyR motors did notramp again until 2013 – 2014Enabling opportunities:- New regulations on electric motors effy- Price volatility of rare-earth PMsACEMP OPTIM 2019, Istanbul - 2019 Gianmario Pellegrino28
Bottom LineBy 2000, the technology was ready, includingmotor design, vector control and sensorlesscontrol aspectsHowever, the interest on SyR motors did notramp again until 2013 – 2014Enabling opportunities:- New regulations on electric motors effy- Price volatility of rare-earth metalsACEMP OPTIM 2019, Istanbul - 2019 Gianmario Pellegrino29
Improve the EfficiencyNote: efficiency classes IE2, IE3 defined according to IEC 60034-30 standardACEMP OPTIM 2019, Istanbul - 2019 Gianmario Pellegrino30
Reduce the Rare-Earth Magnet ContentJune 2011ACEMP OPTIM 2019, Istanbul - 2019 Gianmario Pellegrino31
Consequent Boom of the SyR Motor TechnologyIE3 compulsoryIE2 andrare-earth peakSource: Google ScholarACEMP OPTIM 2019, Istanbul - 2019 Gianmario Pellegrino32
Main Players on the Market (2019)ABBIE4 SynRM range - High output SynRM range (M3AL/M3BL), 5.5–315 kW, Frames: 132–315SiemensSimotics GP – Simotics SD (VSD4000), IES2 (EN 50598), 0.55 – 48 kWFrames: 80 - 200KSB: REEL SuPremE, IE4/IE5, 0.55 . 450 kWOemer: QSR SincroSPE, IE4, 0.3 . 500 kWBonfiglioli: BSR Series, IES2 (IEC 61800-9-2), 0.3 . 18.5 kWRegal Beloit (Genteq HERMETIC): 0.5 . 150 kW probably incompleteSource: new.abb.comSource: Google ScholarACEMP OPTIM 2019, Istanbul - 2019 Gianmario Pellegrino33
SyR motor technology: where we standACEMP OPTIM 2019, Istanbul - 2019 Gianmario Pellegrino34
Review of Known DisadvantagesLow Power Factor and High Torque Ripple- low PF- high torque rippleNon-standard control, need for precise Motor Commissioning- respect of MTPA law- stable Sensorless ControlHigh Speed Applications2- rotor ribs scale with 𝑛𝑛𝑚𝑚𝑚𝑚𝑚𝑚Low Speed Applications- high number of poles harmed by increase of p.u. excitation currentACEMP OPTIM 2019, Istanbul - 2019 Gianmario Pellegrino35
About the Low Power FactorLow Power Factor and High Torque Ripple- low PF: related to the rotor ribs width𝑐𝑐𝑐𝑐𝑐𝑐 𝜑𝜑𝑛𝑛 0.79Pellegrino, G., Armando, E., Guglielmi, P., & Vagati, A. (2009), “A 250kWtransverse-laminated Synchronous Reluctance motor”, In 2009 13thEuropean Conference on Power Electronics and Applications. IEEE.𝑐𝑐𝑐𝑐𝑐𝑐 𝜑𝜑𝑛𝑛 0.87ACEMP OPTIM 2019, Istanbul - 2019 Gianmario Pellegrino36
Torque RippleLow Power Factor and High Torque Ripple- low PFPellegrino, G., Cupertino, F., & Gerada, C. (2014), “Automatic design ofsynchronous reluctance motors focusing on barrier shape optimization”,IEEE Transactions on Industry Applications, 51(2), 1465-1474.- high torque ripple: rules for minimization (e.g. 𝒏𝒏𝒓𝒓 𝒏𝒏𝒔𝒔 𝟒𝟒) skewing, same as Asynchronous Motor Numeric optimization is widely adoptedACEMP OPTIM 2019, Istanbul - 2019 Gianmario Pellegrino37
Motor Identification and ControlLow Power Factor and High Torque Ripple- low PFMeasured characteristics of 1.1 kW ABB SyR Motor (M3AL 90LA4)MTPA was off-line evaluated by flux maps manipulationIncremental saliency defines the area of feasibility of high-frequencyresponse based sensorless control- high torque rippleNon-standard control, need for precise Motor Commissioning- respect of MTPA lawFlux Maps- stable Sensorless Controla) Experimental Flux Maps of ABB M3AL 90LA4, 1.1 kW SyR Motor; b) MTPA trajectory (red) and incremental saliency contoursACEMP OPTIM 2019, Istanbul - 2019 Gianmario Pellegrino38
High-speed ScalabilityLow Power Factor and High Torque Ripple- low PFFerrari, S.; Pellegrino, G.; Bonisoli, Elvio (2016) “Magnetic and structuralco-design of synchronous reluctance electric machines in an open-sourceframework”, International Journal Of Mechanics And Control,Levrotto&Bella, pp. 8, 2016, Vol. 17, ISSN: 1590-8844- high torque rippleNeed for precise Motor Commissioning- respect of MTPA law- stable Sensorless ControlHigh Speed Applications- rotor ribs scale with 𝒏𝒏𝟐𝟐𝒎𝒎𝒎𝒎𝒎𝒎 T and PF dropTorque reduction as the ribs size is increased to withstand a larger max speedACEMP OPTIM 2019, Istanbul - 2019 Gianmario Pellegrino39
Low-speed ApplicationsLow Power Factor and High Torque Ripple- low PFBoazzo, B., Vagati, A., Pellegrino, G., Armando, E., Guglielmi, P. (2014).Multipolar ferrite-assisted synchronous reluctance machines: A generaldesign approach. IEEE Transactions on Industrial Electronics, 62(2), 832845.- high torque rippleNeed for precise Motor Commissioning- respect of MTPA law- stable Sensorless ControlHigh Speed Applications2- rotor ribs scale with 𝑛𝑛𝑚𝑚𝑚𝑚𝑚𝑚Low Speed Applications14-pole, ferrite assisted SyR motor prototype, for direct drive application- high number of poles harmed by p.u. excitation currentp.u. airgap grows PM assistance adjusts the Power FactorACEMP OPTIM 2019, Istanbul - 2019 Gianmario Pellegrino40
Today ’s ChallengesACEMP OPTIM 2019, Istanbul - 2019 Gianmario Pellegrino41
Today’s ChallengesMotor DesignKeysDevelop trustable design tools Balanced use of magnetic FEA Saturated steel propertiesFind the reliable minimum width of rotor ribs Structural FEA in the loop Fatigue test campaignsHave a vector controlled test-rig Flux maps identification for designvalidationMTPA Law and Sensorless ControlKeysKnow the motor parameters Download from Motor Database On-site Sensorless self-commissioningACEMP OPTIM 2019, Istanbul - 2019 Gianmario Pellegrino42
Challenge 1: Motor Design ProceduresMotor DesignKeysDevelop trustable design tools Balanced use of magnetic FEA Saturated steel propertiesFind the reliable minimum width of rotor ribs Structural FEA in the loop Fatigue test campaignsHave a vector controlled test-rig Flux maps identification for designvalidationMTPA Law and Sensorless ControlKeysKnow the motor parameters Download from Motor Database On-site Sensorless self-commissioningACEMP OPTIM 2019, Istanbul - 2019 Gianmario Pellegrino43
Challenge 2: Standardize Motor IdentificationMotor DesignDevelop trustable design toolsKeys E., Boglietti, A., Bojoi, R., “Electrical drives measurements andArmando,testing: Past, Present and Future”, Tutorial at ECCE 2018, Portland, USA Balanced use of magnetic FEA Saturated steel propertiesFind the reliable minimum width of rotor ribs Structural FEA Fatigue test campaignsHave a vector controlled test-rig Flux maps identification for designvalidationMTPA Law and Sensorless ControlKeysKnow the motor parameters Download from Motor Database On-site Sensorless self-commissioningACEMP OPTIM 2019, Istanbul - 2019 Gianmario Pellegrino44
Challenge 3: Plug-and-play ControlMotor DesignKeysDevelop trustable design tools Balanced use of magnetic FEA Saturated steel propertiesFind the reliable minimum width of rotor ribs Structural FEA Fatigue test campaignsHave a vector controlled test-rig Flux maps identification for designvalidationMTPA Law and Sensorless ControlKeysKnow the motor parameters Download from Motor Database On-site Sensorless self-commissioninga) Explored points in the 𝑖𝑖𝑑𝑑 , 𝑖𝑖𝑞𝑞 plane;b) Obtained current vs flux curves (fit)Pescetto, P., Pellegrino, G. (2018). Automatic Tuning for SensorlessCommissioning of Synchronous Reluctance Machines Augmented WithHigh-Frequency Voltage Injection. IEEE Transactions on IndustryApplications, 54(5), 4485-4493.ACEMP OPTIM 2019, Istanbul - 2019 Gianmario Pellegrino45
SyR-e: Synchronous Reluctance EMP OPTIM 2019, Istanbul - 2019 Gianmario Pellegrino46
What is SyR-eSyR-e: Synchronous Reluctance – evolution is a design tool for synchronous e-machinesLaunched on September 2014 in occasion of a Tutorial presented at ECCE - Pittsburg,from a collaboration between Politecnico di Torino and Politecnico di Bari, in ItalyIt runs under Matlab (or GNU Octave), using FEMM as a client for magneto-static FEASyR-e is downloadable at https://sourceforge.net/projects/syr-e/, under the APACHE License, Version 2.0. FEMM is at www.femm.infoACEMP OPTIM 2019, Istanbul - 2019 Gianmario Pellegrino47
GUISyR-e has a Graphical User Interface (GUI) built in Matlab, for ease of data/command inputDesign examples are provided: mot 01.fem, mot 01.mat(default initial design) RAWP.fem, RAWP.mat(demo)ACEMP OPTIM 2019, Istanbul - 2019 Gianmario Pellegrino48
What SyR-e can doThe key feature of SyR-e is the capability of parametric FEA modelling and fast simulationMoreover, SyR-e includes: Design Equations (x,b plane approach) FEAfix: fixing the equations with few selected FEA runsOptimization of selected design goals using MODESimplified copper temperature and centrifugal stress modelsScripts for advanced manipulation of FEA output (flux maps, effy maps)Exporting capability to other CAD environments (Autocad, Infolytica, MotorCAD)Save MachineACEMP OPTIM 2019, Istanbul - 2019 Gianmario PellegrinoPost Processing\Start49
Machine TypesSynchronous Reluctance and PM-assisted Synchronous Reluctance machines: circular barriers angled barriers (called SEG) fluid barriersInterior PM rotors (V-type IPM), Surface-mounted PM machines (SPM)Distributed and concentrated winding statorconfigurations, multi-three-phaseCircular barriersSEG barriersSurface-mounted PMSMACEMP OPTIM 2019, Istanbul - 2019 Gianmario PellegrinoConcentrated Windings50
syrmDesign(x,b): Design EquationsTorque and power-factor contoursare evaluated via design equationsas a function of the two keyparameters: 𝑥𝑥 (rotor/stator split) 𝑏𝑏 (iron/copper split)ACEMP OPTIM 2019, Istanbul - 2019 Gianmario Pellegrino51
Example of Resultsx 0.55, b 0.55x 0.68, b 0.55Any point of the plane corresponds to onemachine design: torque and PF havedifferent trendsLeft to right (𝑥𝑥 up): rotor gets bigger, slots get smallerUp to down (𝑏𝑏 down): Iron paths width decreasesAll the designs have the same peak flux density(stator back iron and rotor flux carriers)x 0.68, b 0.42Stator teeth size can be calibrated separately via thededicated parameter 𝑘𝑘𝑡𝑡ACEMP OPTIM 2019, Istanbul - 2019 Gianmario Pellegrino52
FEAfix: FEA-augmented Design EquationsMain design inputs costraintsFerrari, S., & Pellegrino, G. (2018). FEA-Augmented Design Equations forSynchronous Reluctance Machines. In 2018 IEEE Energy ConversionCongress and Exposition (ECCE) (pp. 5395-5402). IEEE.Design equationsTorque(x,b) and PF(x,b)1 FEMM runFEAfix1Selected designx,b 0.68, 0.55a) Torque contours; b) Power Factor ContoursACEMP OPTIM 2019, Istanbul - 2019 Gianmario Pellegrino53
Flux Barriers ShiftRecently added feature for building motorswith asymmetric poles, and selectivelyeliminating torque ripple harmonicsFerrari, S., Pellegrino, G., Davoli, M., Bianchini, C. (2018). Reduction ofTorque Ripple in Synchronous Reluctance Machines through Flux BarrierShift. In 2018 XIII International Conference on Electrical Machines (ICEM)(pp. 2290-2296). IEEE.ACEMP OPTIM 2019, Istanbul - 2019 Gianmario Pellegrino54
Design OptimizationCupertino, F., Pellegrino, G., & Gerada, C. (2014). Design of synchronousreluctance motors with multiobjective optimization algorithms. IEEETransactions on Industry Applications, 50(6), 3617-3627.The Optimization tab commandsMODE (Multi-Objective DifferentialEvolution) optimizationKey input fields: Population size and # of generations Inputs are selectable Goals are selectableFast FEA evaluation: 5 rotor positions per candidate,random current phase angle duringoptimization Accurate re-evaluation of the Paretooptimal designs (30 rotor positions)ACEMP OPTIM 2019, Istanbul - 2019 Gianmario Pellegrino55
Copper Temperature EstimateThe inputs are: Copper loss Target copper temperatureSyR-e evaluates: Estimated copper temperature Phase current i0 1 p.u. andresistance (given the number of turns)A thermal network estimates thecopper temperature given thehousing temperatureTarget and estimated temperaturemust be equalACEMP OPTIM 2019, Istanbul - 2019 Gianmario Pellegrino56
Structural co-designThe overspeed input fielddetermines the size of theadditional radial ribs included forrotor integrityThis under the assumption thateach rib supports all thecentrifugal load downstream of therespective layer, and imposing astress limit equal to the yieldstrength of the selected siliconsteel (e.g. 285 MPa for M600-50A)This feature is on-line duringdesign optimizationACEMP OPTIM 2019, Istanbul - 2019 Gianmario Pellegrino57
Automatic or User-defined WindingKOIL designs the winding distribution into slots automatically, given the slot/pole/phase numberExample: p 3 (pole pairs), q 2 (slots/pole/phase)Takes advantage of odd-periodic symmetry conditions one rotor pole and 6 stator slotsOptionally, bigger portions of the machine can be modelled, for example for modifying thewinding set manually (e.g. all 36 slots)36 slots6 slotsThe user can edit the winding schemeACEMP OPTIM 2019, Istanbul - 2019 Gianmario Pellegrino58
FEA Evaluated Flux MapsIn a similar manner, output mapsare produced: dq flux maps Torque and torque ripple mapsd axis flux linkageq axis flux linkageTorquePk-pk Torque ripplePhase angle 1000 is an internal code to launch the flux map featureACEMP OPTIM 2019, Istanbul - 2019 Gianmario Pellegrino59
Magnetic Curves Manipulation (syreManipulateMM)Out of the control GUI, additional scripts are availablefor flux maps manipulation: Torque and torque factor [Nm/A] vs current MTPA and MTPV Torque and power vs speed profilesId, Iq control LUTs[Nm] vs [A]ACEMP OPTIM 2019, Istanbul - 2019 Gianmario Pellegrino60
ConclusionThe literature on SyR motors and drives is rich and well established: key concepts were known asearly as in the early 2000s. This technology has advantages and disadvantages, expectedlyHowever, it is consistently gaining momentum as Super Premium efficiency (IE4) solution forvariable speed drives. There is potential also as servomotor and direct-on-line, constant speedapplications.Most of all, what is missing is engineering and standardizationA wider diffusion will be possible if the tight connection between motor design and (sensorless)control design aspects will be better formalized and standardizedKey points are machine testing standards, including test bed and self-commissioning proceduresSyR-e is online, to contribute to this processACEMP OPTIM 2019, Istanbul - 2019 Gianmario Pellegrino61
Thank you!QUESTIONS, PLEASEgi a n mar io.pel legr ino@poli to .itACEMP OPTIM 2019, Istanbul - 2019 Gianmario Pellegrino62
References (1/3)1)2)3)Kostko, J.K., "Polyphase reaction synchronous motors,“ American Institute of Electrical Engineers, Journal of the, 1923Honsinger, V.B., “Synchronous reluctance motor”, US3652885, 1972Honsinger, V. B., "Inherently Stable Reluctance Motors Having Improved Performance," in IEEE Transactions on Power Apparatus and Systems,vol. PAS-91, no. 4, pp. 1544-1554, July 19724) Kolehmainen, J. (2010). Synchronous reluctance motor with form blocked rotor. IEEE Transactions on Energy Conversion5) Vagati, A. (1998) "Synchronous reluctance electrical motor having a low torque-ripple design." U.S. Patent No. 5,818,1406) Lipo, T. A. "Synchronous reluctance machines - a viable alternative for ac drives?“ Electric Machines and Power Systems 19.6 (1991): 659-6717) Xu, L., Xu, X., Lipo, T. A., Novotny, D. W. (1991). “Vector control of a synchronous reluctance motor including saturation and iron loss”, IEEETransactions on Industry Applications, 27(5), 977-985.8) Vagati, A., Franceschini, G., Marongiu, I., & Troglia, G. P. (1992). “Design criteria of high-performance synchronous reluctance motors”,In Conference Record of the 1992 IEEE Industry Applications Society Annual Meeting (pp. 66-73). IEEE.9) Staton, D. A., Miller, T. J. E., & Wood, S. E. (1993, July). “Maximising the saliency ratio of the synchronous reluctance motor”, In IEE Proceedings B(Electric Power Applications) (Vol. 140, No. 4, pp. 249-259). IET Digital Library.10) Betz, R. E., Lagerquist, R., Jovanovic, M., Miller, T. J., & Middleton, R. H. (1993). “Control of synchronous reluctance machines”, IEEE Transactionson Industry Applications, 29(6), 1110-1122.11) Matsuo, T., & Lipo, T. A. (1994). “Rotor design optimization of synchronous reluctance machine”, IEEE Transactions on Energy Conversion, 9(2),359-365.ACEMP OPTIM 2019, Istanbul - 2019 Gianmario Pellegrino63
References (2/3)12) Lagerquist, R., Boldea, I., & Miller, T. J. (1994). “Sensorless-control of the synchronous reluctance motor”, IEEE Transactions on IndustryApplications, 30(3), 673-682.13) Boldea, I., Fu, Z. X., & Nasar, S. A. (1994). “Performance evaluation of axially-laminated anisotropic (ALA) rotor reluctance synchronous motors”,IEEE transactions on industry applications, 30(4), 977-985. Kamper, M. J., Van der Merwe, F. S., & Williamson, S. (1996), “Direct finite elementdesign optimisation of the cageless reluctance synchronous machine”, IEEE Transactions on Energy Conversion, 11(3), 547-555.14) Kamper, M. J., Van der Merwe, F. S., & Williamson, S. (1996), “Direct finite element design optimisation of the cageless reluctance synchronousmachine”, IEEE Transactions on Energy Conversion, 11(3), 547-555.15) Vagati, A., Pastorelli, M., Francheschini, G., & Petrache, S. C. (1998), “Design of low-torque-ripple synchronous reluctance motors”, IEEETransactions on Industry Applications, 34(4), 758-765.16) Ha, J. I., Kang, S. J., & Sul, S. K. (1999). Position-controlled synchronous reluctance motor without rotational transducer. IEEE transactions onIndustry Applications, 35(6), 1393-1398.17) Consoli, A., Russo, F., Scarcella, G., & Testa, A. (1999). Low-and zero-speed sensorless control of synchronous reluctance motors. IEEETransactions on Industry Applications, 35(5), 1050-1057.18) Vagati, A., Pastorelli, M., Scapino, F., & Franceschini, G. (2000). Impact of cross saturation in synchronous reluctance motors of thetransverse-laminated type. IEEE Transactions on Industry Applications, 36(4), 1039-1046. Pellegrino, G., Armando, E., Guglielmi, P., &Vagati, A. (2009), “A 250kW transverse-laminated Synchronous Reluctance motor”, In 2009 13th European Conference on PowerElectronics and Applications. IEEE.ACEMP OPTIM 2019, Istanbul - 2019 Gianmario Pellegrino64
References (3/3)19) Pellegrino, G., Cupertino, F., & Gerada, C. (2014), “Automatic design of synchronous reluctance motors focusing on barrier shape optimization”,IEEE Transactions on Industry Applications, 51(2), 1465-1474.20) Pellegrino, G., Cupertino, F., & Gerada, C. (2014), “Automatic design of synchronous reluctance motors focusing on barrier shape optimization”,IEEE Transactions on Industry Applications, 51(2), 1465-1474.21) Ferrari, S.; Pellegrino, G.; Bonisoli, Elvio (2016) “Magnetic and structural co-design of synchronous reluctance electric machin
Synchronous reluctance motor with form blocked rotor. IEEE Transactions on Energy Conversion [**] Vagati, A. (1998) "Synchronous reluctance electrical motor having a low torque-ripple design."