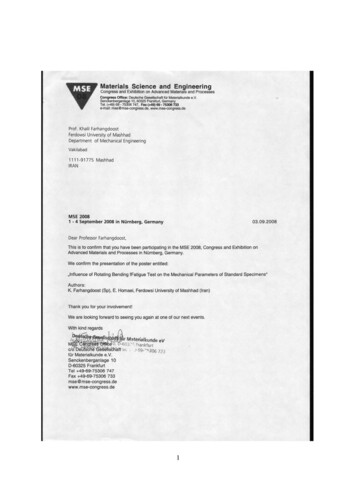
Transcription
1
2
Influence of rotating bending fatigue test on the mechanical parameters ofstandard specimensKhalil Farhangdoost1,*, Ehsan Homaei21,2Department of Mechanical EngineeringFerdowsi University of Mashad91775-1111, MashadIran*farhang@um.ac.irAbstract:The aim of this paper is determining the rate of fatigue damage due to applying rotating bendingfatigue test on standard specimens. The influence of rotating bending fatigue tests areinvestigated on the mechanical parameters- yield strength, ultimate strength, percentage of areareduction and the percentage of elongation- on standard specimens. Different fatigue loads areapplied to the specimens on which fatigue test was run in such a way that no specimen reached toits fracture cycle. Then, tensile test was done on the specimens and the mechanical parameterswere determined for each specimen. Then, the data was compared with the data obtained from thespecimen on which no fatigue test was run and the tensile test was carried out on it directly.Results show that, in comparison to the other mechanical parameters, ultimate strength is moresensitive to the fatigue test that can be a reliable criterion for fatigue damage.concept of fatigue damage has been thoughtto be the weakening or losing of the strengthof a material due to irreversible slip incrystals or plastic strain cycling. In fact, ithas been experimentally verified that thevalue of the residual fracture ductility offatigued specimens is lower than that of thevirgin state, and the decrease in fractureductility becomes predominant as thenumber of cycles approaches fracture cycle[6].Mechanical,metallurgicalandenvironmental variables can influence thefatigue resistance of a structural component[2]. If the stresses due to fatigue loads arehigh enough, they will lead to failure of thecomponent, even though the maximumstress is lower than the static strength of thematerial. Failure occurs when the crack hasso weakened the local material that the1. IntroductionFatigue is important as a mode offailure, the phenomenon of fatigue has beenstudied extensively for more than onehundred years [1]. It is an importantparameter to be considered in the behaviorof mechanical components subjected toconstant and variable amplitude loading [2].Fatigue is primary cause for 80–90% of allengineering failure [3]. Formation of slipbands induces strain localization. Thedevelopment of slip bands may result insubstantial defect creation in localizedregions [4]. The evaluation of residual life ofmaterials loaded cyclically is of greatpractical importance. This requires nondestructive tools that enable one to assesschanges in the material state since thebeginning of service [5]. One historical3
remaining cross section of the componentcannot withstand the imposed mechanicalload [7].Rotating bending fatigue tests are themost usual way to investigate the fatiguebehavior of a material or a component and,due to their speeds, they have also beenwidely used in research on short crackgrowth rates. Rotating bending fatigue testsrepresent perhaps the most simple way toinvestigate the fatigue behavior of materialsor components. The successful applicationof rotating bending fatigue tests is due todifferent factors: the high load cycling rates;the simple testing procedure; and the lowcost for use and maintenance. The speed ofrotating bending fatigue tests is aconsequence of the peculiar configuration ofthe test rig: a vertical load is transformedinto a bending moment on a specimenrotating at high velocity [8].In this paper changes on yieldstrength, ultimate strength, percentage ofarea reduction and the percentage ofelongation on standard specimens due torotating bending fatigue tests are studied andthe sensitivity of these parameters tochanges in number of cycles and fatigue loadare investigated. Setup of the fatigue testingmachine and environmental variables for allof the tests are same.stress values in every cycle. For an elasticmaterial, we have:σ 32Mπd 3(1)Where σ is the maximum surfacestress; M is the bending moment at the crosssection under consideration and d is thecritical diameter of the specimen. Fatiguetesting was carried out on a rotating bendingfatigue testing machine (Roell Amseler,UBM 200) of capacity 6 NM (Newtonmeter), at a frequency of 50 Hz and at roomtemperature. The sample was subjected toalternate cycles of tensile and compressivestresses as it is simultaneously bent androtated.2.2 MaterialThe specimens are made of Ck45, Nothermal operations are done on thesematerials. This medium carbon high tensilesteel is suitable for medium stressed parts inmachinery and industrial tools. Chemicalcomposition of this material is given in table1.Table 1. Chemical composition of Ck45 steelRunCSiSPMnFE1.4289 .124 .036 .028 .609 98.772.4332 .133 .032 .02 .628 98.75Avg.4310 .128 .034 .024 .619 98.762. Experimental MethodThe test specimens are prepared onthe basis of the instruction of fatigue testinginstrument in accordance with the prescribedstandard DIN 50113 (fig. 1). The bars weremachined to form fatigue test specimens.After turning, the portion of the specimenhaving continuous radius was polished to geta mirror-finish. This was done to avoid themost likely influence of surface roughnesson fatigue strength.2.1 Rotating bending fatigue test machineRotating bending fatigue test is asimple method of determining fatigueproperties by applying known bendingmoments to rotating round specimens. Thespecimen has a continuous radius such thatthe maximum bending stresses are constantat all cross sections. The stress at a point onthe surface of a rotating bending specimenvaries sinusoid ally between numericallyequal maximum tensile and compressive4
are determined for each specimen. The dataare shown in table 290.4410291.9203Fig. 1. Shape of standard specimen2.3 Procedure of experimentsDifferent fatigue loads are applied tothe specimens on which fatigue test is run insuch a way that no specimen reaches to itsfracture cycle, in other words, any specimenon which a certain load is applied isremoved from fatigue test process beforefailure happens. For example, if we findfrom S-N diagram that the specimen isfractured because of bending load of 500MPa after 100000 cycles, it is removed fromtesting process after 50000 cycles fordetermining the rate of fatigue damage. S-Ndiagram is shown in figure 2.Table 2. experimental dataNLUY(cycle) mm (MPa) (MPa)508.33 883.60 792.99508.5 881.53 818.191009.25 899.89 780.612008.94 959.33 914.295008.87 941.32 868.282009.89 898.74 831.954009.61 879.11 728.236009.79 906.97 840.694009.19 890.80 771.756009.32 907.28 866.518008.99 895.59 713.045009914.04 833.617507.38 909.75 848.099007.11 935.08 27.3528.7330.1432.7025.5324.32σ is stress due to fatigue load, N isnumber of cycles that must be multiply with1000, L is percent of elongation, U isultimate strength, Y is yield strength and Ais percent of area reduction.Then, the data is compared with thedata obtained from a virgin specimen (thespecimen on which no fatigue test is doneand the tensile test is carried out on itdirectly). The data for virgin specimen areshown in table 3.S-NTable 3. Experimental data for virgin specimen6.4L0(mm)10.10y -0.250x 9.18746.2U0 (MPa)899.61Y0 (MPa)747.89A031.88Ln(S)6L0, U0, Y0 and A0 are themechanical parameters for the virginspecimen.5.85.65.45.211121314153. Results and DiscussionNote the considerable amount ofscatter in fatigue life. The existence ofscatter in fatigue test results is common anddeserving of considerable attention, sinceengineering design decisions must be basedon recognition of the statistical character ofLn(N)Fig. 2. S-N diagram for Ck45 from rotatingbending fatigue testThen, tensile test is done on thespecimens and the mechanical parameters5
the fatigue process. The origins of testscatter are manifold. They include variationsin testing environment, preparation of thespecimen surface, alignment of the testmachine, and a number of metallurgicalvariables. With regard to the testingapparatus, the least amount of scatter isproduced by rotating bending machines,since misalignment is less critical than inaxial loading machine [9].By dividing percent of elongationoutcomes from experimental data to thepercent of elongation resulted from thevirgin specimen data (L/L0), we obtain nondimentional values and fit the least meansquare curve from each three points relatedto the same fatigue load and differentnumber of cycles (fig. 3).1.2fatigue load1.06291.9203 MPa328.7336 MPaU/U01.04373.8140 MPa1.02429.9308 MPa291.9203 MPa1328.7336 MPa373.8140 MPa0.98429.0938 MPa0.960200 400600 800 1000number of cycles(1000 cycles)Fig. 4. Fatigue effect on ultimate tensile strengthBy dividing yield strength outcomesfrom experimental data to the yield strengthresulted from the virgin specimen data(Y/Y0), we obtain non-dimentional valuesand fit the least mean square curve fromeach three points related to the same fatigueload and different number of cycles (fig. 5).fatigue load1.11L/L01.08291.9203 MPa1.25328.7336 MPa1.2291.9203 MPa1.15328.7336 MPafatigue load373.8140 MPa429.0938 MPa0.9Y/Y0291.9203 MPa0.8328.7336 MPa373.8140 MPa1.1429.0938 MPa1.05291.9203 MPa1328.7336 MPa373.8140 MPa0.7429.0938 MPa0.6373.8140 MPa0.950200400600800429.0938 MPa10000.9number of cycles(1000 cycles)0Fig. 3. Fatigue effect on percent of elongation2004006008001000number of cycles(1000 cycles)Fig. 5. Fatigue effect on yield strengthBy dividing ultimate tensile strengthoutcomes from experimental data to theultimate tensile strength resulted from thevirgin specimen data (U/U0), we obtain nondimentional values and fit the least meansquare curve from each three points relatedto the same fatigue load and differentnumber of cycles (fig. 4).By dividing percent of area reductionoutcomes from experimental data to thepercent of area reduction resulted from thevirgin specimen data (A/A0), we obtain nondimentional values and fit the least meansquare curve from each three points relatedto the same fatigue load and differentnumber of cycles (fig. 6).6
1.2area reduction and elongation are decreased.Generally, cyclic hardening occurs.fatigue load291.9203 MPa1A/A0328.7336 MPa0.8References[1] H. Oh, Journal of Materials ProcessingTechnology, 62, pp. 37-41, January 1995.[2] M.A.S. Torres and H.J.C. Voorwald,International Journal of Fatigue, 24, pp.877–886, October 2001.[3] R. Sadeler, Y. Totik, M. Gavgalı and I.Kaymaz, Journal of Materials and Design,25, pp. 439–445, December 2003.[4] M. Nagumo, H. Shimura, T. Chaya, H.Hayashi and I. Ochiai, Journal of MaterialsScience and Engineering A, 348, pp. 192200, September 2002.[5] M. Soultan, X. Kleber, J. Chicois and A.Vincent, Journal of NDT&E International,39, pp. 493–498, March 2006.[6] Y. Murakamia and K.J. Miller,International Journal of Fatigue, 27, pp.991–1005, October 2004.[7] M. Naeem, R. Singh and D. Probert,International Journal of Fatigue, 21, pp.831–847, March 1999.[8] S. Beretta and P. Clerici, InternationalJournal of Fatigue, 19, pp. 457-460, May1997.[9] R.W. Hertzberg, Deformation andfracture mechanics of engineering materials,John Wiley & Sons, New York, USA 1996.373.8140 MPa429.0938 MPa0.6291.9203 MPa328.7336 MPa0.4373.8140 MPa429.0938 MPa0.20200400600800 1000number of cycles(1000 cycles)Fig. 6. Fatigue effect on percent of areareductionCertain engineering alloys willcyclically strain harden and others willsoften. Manson et al. observed that thatpropensity for cyclic hardening or softeningdepends on the ratio of monotonic ultimatestrength to 0.2% offset yield strength. Whenσ ult / σ ys 1.4 , the material will harden, butwhen σ ult / σ ys 1.2 , softening will occur.For ratios between 1.2 and 1.4, forecastingbecomes difficult, though a large change inproperties is not expected. Therefore,initially hard and strong materials willgenerally cyclically strain soften, andinitially soft materials will harden. Manson’srules make use of monotonic properties todetermine whether cyclic hardening orsoftening will occur.Generally, in this research, theultimate tensile strength and the yieldstrength of the material increased and thematerial is hardened and in accordance, thepercent of area reduction and elongation aredecreased.4. ConclusionResults show that, in comparison tothe other parameters, ultimate tensilestrength is more sensitive to the fatigue testthat can be a reliable criterion for fatiguedamage. It is found that rotating bendingfatigue test is induced that ultimate tensilestrength and yield strength are increased and7
2.1 Rotating bending fatigue test machine Rotating bending fatigue test is a simple method of determining fatigue properties by applying known bending moments to rotating round specimens. The specimen has a continuous radius such that the maximum bending stresses are constant at all cross sections. The stress at a point on the surface of a .