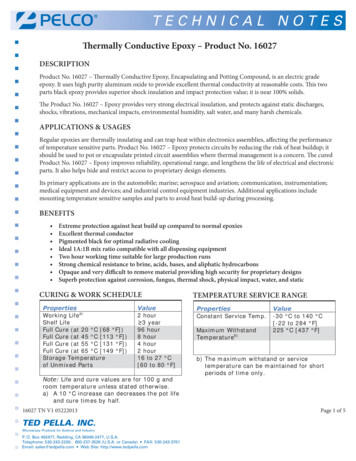
Transcription
PELCO Thermally Conductive EpoxyThermally ConductiveEpoxyEncapsulating& Potting CompoundEncapsulating&I S832TC Technical Data Sheet832TC832TCDescription Thermally Conductive Epoxy – Product No. 16027DescriptionThe 832TC Thermally Conductive Epoxy, Encapsulating and Potting Compound, is an electric grade oxy, Encapsulatingand conductivityPotting Compound,is an electricepoxy.It usespurityaluminumoxide to provideexcellent thermalat reasonablecosts. gradeThis k No.epoxyprovidessuperiorshock Epoxy,insulationand impactvalue; it100%Product16027– ThermallyConductiveEncapsulatingand protectionPotting Compound,is isannearelectricgradesolids. nimpactprotectionvalue; it costs.is altoprovideexcellentandthermalconductivityat reasonableThistwoTheepoxy.832TCepoxyprovidesvery stronginsulation,and protectsagainststatic nsulationand impactvalue;it isagainstnear100%solids.The ion,and andprotectsstaticdischarges, rations, mechanical impacts, environmental humidity, salt water, and many harsh chemicals.The Product No. 16027 – Epoxy provides very strong electrical insulation, and protects against static discharges,Applications& Usages impacts, environmental humidity, salt water, and many harsh chemicals.shocks,vibrations, mechanicalApplications& UsagesRegular epoxies are thermally insulating and can trap heat within electronics assemblies, affecting theRegular epoxiesarethermallyinsulatingand832TCcan trapheat withinelectronicsassemblies,theperformanceof temperaturesensitiveparts. Theprotectscircuitsby reducingthe risk ofaffectingheatAPPLICATIONS& USAGESperformancesensitiveparts.printedThe 832TCprotectscircuitsby reducingthe risk of heatbuildup;it should ofbetemperatureused to pot orencapsulatecircuitassemblieswherethermal managementisRegularepoxiesare thermallyinsulatingcanreliability,trap ebuildup;it curedshouldbe usedto potorandencapsulatecircuit range,assemblieswherethermalmanagementisa concern.The832TCepoxyimprovesoperationaland f range, andlengthensthe lifeitofelectricaland electronicparts.It alsohelpshide– cparts. Italso helpsand restrictaccessmanagementto proprietarydesign elements.shouldbe usedpot or encapsulateprintedcircuit hideassemblieswhere thermalis a concern.The curedIts primary applications are in the automobile; marine; aerospace and aviation; ricalandelectronicIts primary applicationsare in communication,instrumentation;medical equipmentanddevices; andindustrialcontrolandequipmentparts.It also helps hideand restrictaccess mentdevices;and elements.industrial control equipment industries.BenefitsIts primary applications are in the automobile; marine; aerospace and aviation; communication, instrumentation;Benefitsmedicalequipment and devices; and industrial control equipment industries. Additional applications include Extreme protection against heat build up in electronic equipment compared to normal epoxiesmountingtemperaturesensitive samplesand heatparts tobuildavoidupheatinbuild-upduringprocessing. d to normal epoxiesExcellent thermal conductor Excellent thermal conductorBENEFITS Pigmented black for optimal radiative cooling Pigmented black for optimal radiative cooling Ideal1A:1Bmix ratiocompatibleall dispensingequipment Extremeprotectionagainstheat buildwithup comparedto normalepoxies ExcellentIdeal 1A:1Bmixratiocompatiblewithalldispensingequipment thermal conductor Two hour workingtime suitable for large production runs blackfor optimalradiativecooling PigmentedTwo hourworkingtimesuitablefor large production runs Strongchemical resistance to brine, acids, bases, and aliphatic hydrocarbons Ideal1A:1Bmixratiocompatiblewithalldispensing equipment Strong chemical resistance to brine, acids, bases, and aliphatic hydrocarbons Opaqueandverydifficulttoremovematerial runsproviding high security for proprietary designsTwo hour working time suitable for large ovidinghigh security for proprietary designs Strongchemical resistanceto brine,acids,fungus,bases, andaliphatichydrocarbons Superb protectionagainstcorrosion,thermalshock,physical impact, water, and static andprotectionvery difficultagainstto removecorrosion,material providingsecurityfor proprietarydesignswater, and static OpaqueSuperbfungus, highthermalshock,physical impact, Superb protection against corrosion, fungus, thermal shock, physical impact, water, and staticCuring & Work ScheduleCuring && WORKWork ueWorkingLifea)2 hourLifea)2 hourShelfWorkingLife 3 yearShelf(atLife20 C [68 F]) 3 yearFull Cure96 hourFull Cure(at C20[113 C [6896 hourFull Cure(at 45 F]) F])8 hourFull Cure(at C45[131 C [1138 hourFull Cure(at 55 F]) F])4 hourFull Cure(at C55[149 C [1314 hourFull Cure(at 65 F]) F])2 hourFull TemperatureCure (at 65 C [149 F])hourStorage16 to227 CStoragePartsTemperature1680to F]27 Cof Unmixed[60 toof Unmixed Parts[60 to 80 F]Note: Life and cure values are for 100 g andLife and unlesscure valuesfor 100 g eratureunlessstatedotherwise.a) A 10 C increase can decreases thepot lifea)A10 Cincreasecandecreasesthe pot lifeand cure times by half.and cure times by half.16027 TN V1 05222013Rev. Date: 07 August 2012 / Ver. 1.02TED Rev.PELLA.INC.Date: 07August 2012 / Ver. 1.02Temperature ServiceTEMPERATURESERVICERangeRANGETemperature Service RangePropertiesValuePropertiesValueConstantService Temp. -30 Cto 140 CConstant Service Temp. C to[-22 -30to 284 F]140 C[-22to 284Maximum Withstand225 C[437 F] F]b)MaximumWithstand225 C [437 F]TemperatureTemperatureb)b) The maximum withstand or serviceb) The maximumor forservicetemperaturecan edfor shortperiods of time only.periods of time only.Page 1 of 7Page 1 of 7Microscopy Products for Science and IndustryP. O. Box 492477, Redding, CA 96049-2477, U.S.A.Telephone: 530-243-2200; 800-237-3526 (U.S.A. or Canada) FAX: 530-243-3761Email: sales@tedpella.com Web Site: http://www.tedpella.comPage 1 of 5
832TC Technical Data Sheet832TCPRACTICAL COMPONENTSPrincipal ComponentsNameCAS Number CAS thylenetetramineAluminumOxidesAluminum operties of832TCPROPERTIESOFCuredCUREDPRODUCT NO. 16027 – THERMALLY CONDUCTIVE EPOXYPhysical PropertiesColorDensity (at 26 C)HardnessTensile StrengthElongationLap Shear StrengthIzod Impactb)Compression StrengthFlexural StrengthMethodVisualElectric PropertiesBreakdown Voltage @ 3.118 mmDielectric StrengthBreakdown Voltage @3.175 mm [1/8”]Dielectric StrengthVolume ResistivitySurface Resistanced)Comparative Tracking IndexDielectric Dissipation & ConstantDissipation & Constant@1 MHzMethodASTM D 149"Reference fitc)"ASTM D 257"ASTM D 3628Thermal PropertiesThermal ConductivityThermal DiffusivityVolumetric Specific HeatCTE (prior Tg) eCTE (after Tg) eOverall CTE (-40 to 250 C) eGlass Transition Temperature (Tg)Heat Deflection TemperatureMethod(Shore D durometer)ASTM D 638"ASTM D 1002ASTM D 256ASTM D 695ASTM D 790ASTM D 150-98ASTMASTMASTMASTMASTME 831E 831E 831D 3418D 648Valuea)Black1.83 g/cm382D18.85 N/mm21.87%22.2 N/mm21.7 kJ/m228.19 N/mm2113.76 N/mm2[2,734 lb/in2][3224 lb/in2][0.80 ft·lb/in][4,088 lb/in2][5,352 lb/in2]Value45.7 kV14.7 kV/mm [373 V/mil]46.2 kV14.6 kV/mm [370 V/mil]2.58 x1015 Ω cm3.16 x1016 Ω/sqNot establisheddissipation, Dconstant, k’0.0114.41Value0.682 W/(m K)0.38 mm2/s1.9 MJ/(m3 K)66.2 ppm/ C166.9 ppm/ C148.3 ppm/ C25.4 C [77.7 F]35.4 C [95.6 F]a) N/mm2 mPa; lb/in2 psib) Cantilever beam impactc) To allow comparison between products, the Tautschter equation was fitted to 5 experimental dielectricstrengths and extrapolated to a standard reference thickness of 1/8” (3.175 mm).d) The surface (sheet) resistivity unit is commonly referred to as “Ohm per square”e) Coefficient of Thermal Expansion (CTE) units are in ppm/ C in/in/ C 10-6 unit/unit/ C 10-6Rev. Date: 07 August 2012 / Ver. 1.02Page 2 of 716027 TN V1 05222013TED PELLA. INC.Microscopy Products for Science and IndustryP. O. Box 492477, Redding, CA 96049-2477, U.S.A.Telephone: 530-243-2200; 800-237-3526 (U.S.A. or Canada) FAX: 530-243-3761Email: sales@tedpella.com Web Site: http://www.tedpella.comPage 2 of 5
PRACTICAL COMPONENTSName CAS NumberPart A: Bis-F Epoxide ResinAluminum OxidesPart B: Curing PolyamideTriethylene tetramineAluminum OxidesThermally Conductive ncapsulatingPotting TC Technical DataSheet112-24-3832TC Technical Data opertiesofOFUncuredPROPERTIESCURED832TCPRODUCT NO. 16027 – THERMALLY CONDUCTIVE EPOXYPhysicalPropertyPhysical PropertyColorColorViscosity2020 C C[73[73 F]a F]aViscosityatatDensityDensityMix Ratio by Volume RatiobyWeight(A:B)Solids Content (w/w)MixtureMixture(1A:1B)(2A:1B)Mixtur e (2A:1B)BlackBlack38,000 cPto 40,000cP 40,000[38 Pa·s cPto 40Pa·s]38,000cP to[38Pa·s to 40 Pa·s]1.616 g/mL1.616g/mL1.0:1.01.0:1.01.2:1.01.2:1.0 100%Physical PropertyColorPhysical PropertyViscosityat 24 C [73 F] aColorDensityFlashPoint at 24 C [73 F] aViscosityOdorDensityPart APart BBlackBlackA17,900 cP [17.9PartPa·s]23,100 cP [23.1 Pa·s]Part BBlack1.802 g/mL Black1.504 g/mL190 17,900 C [374 F] F]cP [17.9 Pa·s] 93 C [19923,100cP [23.1 Pa·s]Slight OdorSlight Odor 1.504 g/mL1.802 g/mLSolids Content (w/w)Flash PointOdor 100%190 C [374 F]Slight Odora) Brookfield viscometer at 20 RPM for Part A and 10 RPM Part B with spindle LV493 C [199 F]Slight Odora) Brookfield viscometer at 20 RPM for Part A and 10 RPM Part B with spindle LV4CompatibilityAdhesion—As seen in the substrate adhesion table, the 832TC epoxy adheres to most materials found onprinted circuit assemblies; however, it is not compatible with contaminants like water, oil, and greasy fluxCOMPATIBILITYresidues that may affect adhesion. If contamination is present, clean the printed circuit assembly withelectronic cleaner such as MG Chemicals 4050 Safety Wash, 406B Superwash, or 824 Isopropyl Alcohol.CompatibilityAdhesion—Asseenseenin theinsubstrateadhesion adhesiontable, ProductNo. 16027– Epoxyepoxyadheresto most materialshowever,Adhesion —Asthe substratetable,the 832TCadheresto most found;materialsfound onitSubstrateis not luxresiduesthatmayaffectadhesion.Ifcontaminationis n in Decreasing isopropanol.residues that may affect adhesion. If contamination is present, clean the printed circuit assembly withPhysical PropertiesAdhesionelectronic cleaner such as MG ChemicalsStronger4050 Safety Wash, 406B Superwash, or 824 Isopropyl ngDECREASINGORDERSubstrate AdhesionOrderFiberglassWoodPhysical lassPolycarbonateAcrylicPolypropylenea)a) Does not bond to polypropyleneWeakera) Does not bond to polypropylene16027 TN V1 05222013Rev. Date:07 August2012 / Ver. 1.02TEDPELLA.INC.Page 3 of 7Microscopy Products for Science and IndustryP. O. Box 492477, Redding, CA 96049-2477, U.S.A.Telephone: 530-243-2200; 800-237-3526 (U.S.A. or Canada) FAX: 530-243-3761Email: sales@tedpella.com Web Site: http://www.tedpella.comPage 3 of 5
Chemical Resistance— The chemical solvent resistance table presents the percent weight change over the indicated period.The results show low water absorption and a high chemical resistance to water and most ionic species. Softening andswelling occurs for aggressive organic solvents.STORAGEStore between 16 and 27 C [60 and 80 F] in dry area away from sunlight. Prolonged storage or storage at or near freezingtemperatures can result in crystallization. If crystallization occurs, reconstitute the component to its original state bytemporarily warming it to 50 to 60 C [122 to 140 F]. To ensure full homogeneity, stir thoroughly the warm component,reincorporating all settled material. Re-secure container lid and let cool down before use.APPLICATION INSTRUCTIONSFollow the procedure below for best results. If you have little or no experience with Product No. 16027 – Epoxy, pleasefollow the long instructions instead. The short instructions provided here are not suitable for first time users.To prepare 1:1 (A:B) epoxy mixture (100g)1.2.3.4.5.6.7.Carefully scrape any settled material in the Part A container; and stir and fold material until homogenous.Carefully crape any settled material in the Part B container; and stir and fold material until homogenous.Measure one parts by volume of the pre-stirred A, and pour in the mixing container.Measure one part by volume of the pre-stirred B, and slowly pour in the mixing container while stirring.Put in a vacuum chamber, bring to 25 Hg/in pressure, and wait for 2 minutes to de-air. —OR— Let sitfor 30 minutes to de-air.If bubbles are present at top, use the mixing paddle to gently break them.Pour mixture into the mold or container containing the components to be encapsulated.ATTENTION! Mixing 500 g [0.4 L] of Part B at a time into A decreases working life and promotes flash cure. Use ofepoxy mixing machines with static stirrer recommended for large volumes. Limit size of hand-mixed batches.TIP: Due to the high viscosity and abrasiveness of the aluminum oxide filler, you may preheat parts A and part B withtemperature jacket to increase the flow and improve air release. This will help reduce the wear on the mixing equipment,but it will shorten the working life.To room temperature cure Product No. 16027 – EpoxyLet stand for 24 hours.To heat cure Product No. 16027 – EpoxyPut in oven at 45 C [113 F] for 8 hours.–OR–Put in oven at 55 C [131 F] for 4 hour.–OR–Put in oven at 65 C [149 F] for 2 hour.ATTENTION! Due to exothermic reaction, heat cure temperatures should be at least 25% below the maximumtemperature tolerated by the most fragile PCB component. For larger potting blocks, reduce heat cure temperature bygreater margins.16027 TN V1 05222013TED PELLA. INC.Microscopy Products for Science and IndustryP. O. Box 492477, Redding, CA 96049-2477, U.S.A.Telephone: 530-243-2200; 800-237-3526 (U.S.A. or Canada) FAX: 530-243-3761Email: sales@tedpella.com Web Site: http://www.tedpella.comPage 4 of 5
832Health, Safety, and Environmental AwarenessHEALTH, SAFETY, AND ENVIRONMENTAL AWARENESSPlease see the 832TC Material Safety Data Sheet (MSDS) parts A and B for more details urityguidelines.Pleasesee Product No.16027 – EpoxyMaterialDataSheet (MSDS)parts A and B for more details ontransportation, storage, handling and other security guidelines.HealthandandSafety:Product No.– Epoxypartscanigniteignite ifif theis liquidis heated.Wearsafetyglassesor gogglesdisposablechloride,neoprene,chloride,or nitrile gloveswhile handlingliquids.Part posablepolyvinylneoprene,or nitrileglovesinhandlingparticular eralongperiodoftime.Theepoxyisblackandliquids. Part B in particular causes skin burns and may cause sensitization if exposed over a lowillnotwashoff onceThecured:wear protectivethoroughlyafterwearuse orprotectiveif skin contactoccurs.Doperiod of time.epoxyis black workand clothing.will not Washwashhandsoff oncecured:workclothing.Wanotingest.hands thoroughly after use or if skin contact occurs. Do not ingest.Althoughthe theproducthas lowhasvolatilityand moderateodor,use it in a odor,well-ventilatedarea.Althoughproductlow volatilityandmoderateuse it ina well-ventilated area.Thecuredepoxyresin presentsno known hazard.Thecuredepoxyresin presentsno known hazard.Part AHMIS RATINGNFPA 704 CODESHEALTH:2FLAMMABILITY:1PHYSICAL HAZARD:012PERSONAL PROTECTION:0Part BHMIS RATINGNFPA 704 CODESHEALTH:2FLAMMABILITY:1PHYSICAL HAZARD:012PERSONAL PROTECTION:0Approximate HMIS and NFPA Risk Ratings Legend:0 (Low or none); 1 (Slight); 2 (Moderate); 3 (Serious); 4 (Severe)16027 TN V1 05222013TED PELLA. INC.Rev. ProductsDate:07 AugustMicroscopyfor Scienceand Industry 2012 / Ver. 1.02Page 5 of 5Page 5 of 7P. O. Box 492477, Redding, CA 96049-2477, U.S.A.Telephone: 530-243-2200; 800-237-3526 (U.S.A. or Canada) FAX: 530-243-3761Email: sales@tedpella.com Web Site: http://www.tedpella.com
The 832TC Thermally Conductive Epoxy, Encapsulating and Potting Compound, is an electric grade epoxy. It uses high purity aluminum oxide to provide excellent thermal conductivity at reasonable costs. This two parts black epoxy provides superior shock insulation and impact protection value; it is near 100% solids. .