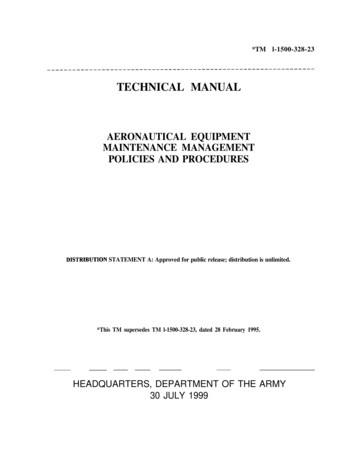
Transcription
*TM l-1500-328-23-- -TECHNICAL MANUALAERONAUTICAL EQUIPMENTMAINTENANCE MANAGEMENTPOLICIES AND PROCEDURESDISTRIDUTION STATEMENT A: Approved for public release; distribution is unlimited.*This TM supersedes TM l-1500-328-23, dated 28 February 1995.HEADQUARTERS, DEPARTMENT OF THE ARMY30 JULY 1999
TM 1--1500--328--23C1CHANGENO.HEADQUARTERSDEPARTMENT OF THE ARMYWASHINGTON, D.C., 25 November 20021TECHNICAL MANUALAERONAUTICAL EQUIPMENTMAINTENANCE MANAGEMENTPOLICIES AND PROCEDURESREPORTING ERRORS AND RECOMMENDING IMPROVEMENTSYou can help improve this manual. If you find any mistakes or if you know of a way to improve theprocedures, please let us know. Mail your letter or DA Form 2028 (Recommended Changes toPublications and Blank Forms) or DA Form 2028-2 located in the back of this manual directly to:Commander, US Army Aviation and Missile Command, ATTN: AMSAM-MMC-MA-NP, Redstone Arsenal,AL 35898-5000. You may also submit your recommended changes by E-Mail directly to2028@redstone.army.mil or by fax (256) 842-6546/DSN 788-6546. A reply will be furnished directly toyou. Instruction for sending an electronic 2028 may be found at the back of this manual immediatelypreceding the hard copy 2028. For World Wide Web use: https://amcom2028.redstone.army.mil.DISTRIBUTION STATEMENT A: Approved for public release; distribution is unlimited.TM 1--1500--328--23, dated 30 July 1999, is changed as follows:1.Remove and insert pages as indicated below. New or changed text material is indicated by a vertical bar inthe margin. An illustration change is indicated by a miniature pointing hand.2.Remove pagesInsert pages-- -- -3--1 and 3--28--5 and 8--6A/(B--blank)3--1 and 3--28--5 and 8--6Retain this sheet in front of manual for reference purposes.
TM 1-1500-328-23C1By Order of the Secretary of the Army:Official:ERIC K. SHINSEKIGeneral, United States ArmyChief of StaffJOEL B. HUDSONAdministrative Assistant to theSecretary of the Army0232504DISTRIBUTION:To be distributed in accordance with Initial Distribution Number (IDN) 313115, requirements for TM 1-1500-328-23.
TM 1--1500--328--23LIST OF EFFECTIVE PAGESInsert latest changed pages; dispose of superseded pages in accordance with regulations.NOTE: On a changed page, the portion of the text affected by the latest change is indicated by a vertical line,or other change symbol, in the outer margin of the page. Changes to illustrations are indicated by miniaturepointing hands. Changes to wiring diagrams are indicated by shaded areas.Dates of issue for original and changed pages are:Original 0 . . . . . . . . . . . . . . . . . 30 July 1999Change 1 . . . . . . . . . . . . . . . . . . 25 November 2002PageNo.*ChangeNo.Cover . . . . . . . . . . . . . . . . . . . . . . . . . . .Blank . . . . . . . . . . . . . . . . . . . . . . . . . . .A .B Blank . . . . . . . . . . . . . . . . . . . . . . . . .i through iv . . . . . . . . . . . . . . . . . . . . . .1--1 and 1--2 . . . . . . . . . . . . . . . . . . . . .2--1 through 2--11 . . . . . . . . . . . . . . . . .2--12 blank . . . . . . . . . . . . . . . . . . . . . .3--1 . . . . . . . . . . . . . . . . . . . . . . . . . . . .3--2 through 3--8 . . . . . . . . . . . . . . . . . .4--1 through 4--12 . . . . . . . . . . . . . . . .5--1 and 5--2 . . . . . . . . . . . . . . . . . . . . .6--1 and 6--2 . . . . . . . . . . . . . . . . . . . . .7--1 thru 7--7 . . . . . . . . . . . . . . . . . . . . .7--8 blank . . . . . . . . . . . . . . . . . . . . . . .001100001000000PageNo.*ChangeNo.8--1 through 8--4 . . . . . . . . . . . . . . . . . .8--5 . . . . . . . . . . . . . . . . . . . . . . . . . . . . .8--6 . . . . . . . . . . . . . . . . . . . . . . . . . . . .9--1 thru 9--9 . . . . . . . . . . . . . . . . . . . . .9--10 blank . . . . . . . . . . . . . . . . . . . . . .10--1 thru 10--3 . . . . . . . . . . . . . . . . . . .10--4 blank . . . . . . . . . . . . . . . . . . . . . .11--1 through 11--4 . . . . . . . . . . . . . . . .12--1 through 12--5 . . . . . . . . . . . . . . .12--6 blank . . . . . . . . . . . . . . . . . . . . . .13--thru 13--7 . . . . . . . . . . . . . . . . . . . .13--8 blank . . . . . . . . . . . . . . . . . . . . . .A--1 . . . . . . . . . . . . . . . . . . . . . . . . . . . .A--2 blank . . . . . . . . . . . . . . . . . . . . . . .01000000000000*Zero in column indicates an original page.Change 1A/(B--blank)
TMTECHNICAL MANUALNO. l-1500-328-23l-1500-328-23HEADQUARTERSDEPARTMENT OF THE ARMYWASHINGTON, D.C., 30 July 1999AERONAUTICAL EQUIPMENT MAINTENANCE MANAGEMENTPOLICIES AND PROCEDURESREPORTING ERRORS AND RECOMMENDING IMPROVEMENTSYou can help improve this manual.If you find anyMistakes or if you know of a way to improve theMail your letter orProcedures please let us know.DA Form 2028 (Recommended Changes to PublicationsAnd Blank Forms) to: Commander, U.S. Army AviationAnd Missile Command (AMCOM), ATTN: AMSAM-MMC-RE-FF,Redstone Arsenal, Alabama 35898-5230. A reply willBe furnished directly to you.TABLE OF CONTENTSSection/ParagraphGENERALSection t Record Keeping1-5Computer Generated Records1-6Responsibilities1-7Section AFT PREVENTIVE MAINTENANCE SYSTEMSGeneralFlights and Maintenance InspectionsUnder Operational EmergenciesEvacuation of Grounded AircraftScheduled Preventive and PhaseMaintenance InspectionsPhase Maintenance Inspection MethodProgressive Phase Maintenance(PPM) MethodPeriodic/PMS Inspection MethodCombat Phase Maintenance (CPM) orCombat Periodic (CPE) InspectionRecurring Special InspectionsScheduling of Recurring SpecialInspectionsNon-recurring Special InspectionsPreflight InspectionThru-flight 2-52-62-72-72-8Z-102-102-10
TM ion III3-13-23-33-43-53-63-7Section -154-16SectionV5-15-25-3Section VI6-16-26-3iiPost-flight InspectionAcceptance InspectionInspection of Aircraft In StorageTransfer InspectionPage2-102-112-112-11MAINTENANCE TEST FLIGHTS AND OPERATIONAL CHECKSDefinitions3-lGeneral3-lMaintenance Test Flight Accomplishment3-4Maintenance Test Flight Check Sheets3-6Recording Maintenance Test Flights3-6Maintenance Operational CheckRequirements3-7Maintenance Operational CheckAccomplishment3-7AIRCRAFT COMPONENT REPLACEMENT AND REUSE PROCEDURESDefinitions4-lGeneral4-2The Army Warranty Program4-3Replacement of Limited ServiceLife Components4-3Replacement of Components on4-5Aircraft Being TransferredRemoval of Components4-5Reuse Of Serviceable Parts4-6Components Obtained through4-7CannibalizationReuse Of Components Removed4-7From Damaged AircraftComponents Exposed to Fire4-8and/or Saltwater Immersion4-8Repair and Overhaul of Components4-9Component Historical RecordsReceipt of Electronic Messages or4-10Technical BulletinsManaged Components with Missing4-11Data PlatesCounterfeit or Bogus Component/Part4-11AwarenessHistorical Data Assistance4-12ActivitiesCOMPONENT SERIALIZATIONGeneralConditions That Require ItemSerializationAssignment of New Component SerialNumbersAIRCRAFT COMPONENT REPAIR KITSDefinition of A Repair KitGeneralProcedures for Obtaining and Useof Repair Kits5-l5-l5-l6-l6-l6-1
TM l-1500-328-23Section/ParagraphSection VIIDEPOT LEVEL REPAIR/OVERHAUL OPERATIONS7-1Definitions7-2General7-3Programmed Depot Maintenance ofArmy Aircraft7-4Un-programmed Depot Maintenance ofArmy Aircraft7-5Limited Depot Level MaintenancePerformed By AVIM Activities7-6Special Responsibilities7-7Depot Maintenance StandardsRecording and Reporting7-8Section VIII8-18-28-38-48-58-68-78-88-98-10Section IX9-19-29-39-49-59-69-79-89-99-10Section XPage7-l7-l7-37-47-47-57-67-7AVIATION CORROSION PREVENTION AND CONTROL POLICYAviation Corrosion Prevention andControl -2Procedures8-4Geographical Location CPC Inspectionand Wash Frequency8-5Operating Environment CPC Inspectionand Wash Requirements8-5Aviation Associated Equipment8-5Required References8-5CPC Training8-6PROCESSING REQUIREMENTS FOR AERONAUTICAL EQUIPMENTPRIOR TO DISPOSALDefinitions9-lGeneral9-2Identification and Processing ofFSCAP Items9-3Responsibility for Mutilation9-4Criteria for Condemnation9-5How To Mutilate9-6Data Plates, Information Tags andEtched Markings9-7Parts for Training, Educational,Research, and Developmental9-7Verification and certification9-8Disposal of Non-Condemned ItemsThrough the DRMO9-9CONTROLLED EXCHANGE AND CANNIBALIZATION OF AVIATIONMATERIEL10-lDefinitions10-lControlled Exchange or10-2Cannibalization of Material10-lControlled Exchange By Unit,10-310-lOrganization, Or Activityiii
TM l-1500-328-23Section/Paragraph10-410-510-6Section XIDocumentation RequiredControlled Exchange ApprovalInventory Control of CannibalizedManaged ComponentsPage10-210-210-311-6STATIC AND MUSEUM DISPLAYSPurposeRequests for Display Aircraft andAeronautical ItemsProcessing RequirementsExplanation of Preparation ActionsReporting of Pilfered or MissingDisplay ItemsDisposition Of Display Aircraft12-l12-212-3STANDARDS OF SERVICEABILITY FOR TRANSFER OF AIRCRAFTDefinitions12-lGeneral12-lStandards of Serviceability12-l11-111-211-311-411-5Section XII11-l11-111-l11-211-411-4Section XIIIAERONAUTICAL ITEMS USED FOR MAINTENANCE TRAINING13-lDefinitions13-l13-2General13-l13-3MTA Mission Design Series (MDS)13-213-4FTAD Training Device13-213-5Item Identification13-213-6Maintenance Requirements13-213-7Configuration Control13-313-8Records and Historical Data13-313-9Lost or Missing Logbook/Historical Data13-313-10DA Form 2410 Submission13-313-11Theft or Misappropriation of13-4Training Items13-12Controlled Substitution of Components13-513-13Classification/Reclassification to13-5Training Aircraft/MTADesignation of Components as IATE Items13-1413-613-6Aircraft Data Plate Control13-15Disposition of Maintenance Training13-16Aircraft/MTA13-6Appendix AivREFERENCESA-l
TM l-1500-328-23SECTION IGENERAL1-1.Purpose.This manual establishes standards, that apply tomaintenance and maintenance management of all Army aircraft, andancillary aeronautical equipment.1-2.Scope.This manual applies to all elements of the Armyincluding the Army National Guard, Army Reserve, depots andcontractors engaged in the operation, maintenance, or storage of Armyaircraft, aviation associated equipment and applicable componentsowned and managed by the Army, with the exception of Unmanned AirVehicles.1-3. Definitions.For the purpose of this manual, definitionscontained in the following sections apply, in addition to thosecontained in Army Regulation (AR) 310-25 (Dictionary of U.S. ArmyTerms).1-4.General.The maintenance management standards contained in this manuala.are established as basic mandatory requirements to which aeronauticalequipment will conform.Specific maintenance tasks and inspections will be performed inb.accordance with all appropriate publications; such as, ArmyRegulations (AR), Technical Bulletins (TB), Technical Manuals (TM),Electronic Technical Manuals (ETM), Interactive Electronic TechnicalManuals (IETM) and other applicable publications.This manual iscategorized as a "general information publication;" therefore, if aDepartment of the Army (DA), or Department of Defense (DOD) regulationor technical publication conflicts with the requirements orinformation in this manual, the regulation or technical publicationwill take precedence, unless specifically stated otherwise.For specific information pertaining to airframe mounted AviationC.Life Support Equipment (ALSE) or avionics equipment, refer to theapplicable publications.DA Pamphlet 738-751, Functional Usersl-5. Aircraft Record Keeping.Manual for The Army Maintenance Management System-Aviation (TAMMS-A),is the Army's authority for the use, preparation and disposition ofExcept for the special instructionsaircraft forms and records.stated in this TM, letters of deviation, written correspondence from1-1
TM l-1500-328-23Aviation and Missile Command (AMCOM), AMSAM-MMC-RE-FF, or HeadquartersDA, Department of Army Logistics Organization (DALO), or an AMCOMelectronic message; such as, Safety of Flight (SOF), Aviation SafetyAction Message (ASAM), or Maintenance Information Message (MIM), nodeviation from DA Pamphlet 738-751 is authorized.l-6. Computer Generated Records. Authorized computer-generated formswill normally have an "E" suffix added to the basic Army form number."E" forms are considered the same as the basic (manual) form.Therefore, the same procedures stated in DA Pamphlet 738-751 willAn authorized exception between the manual and automatedapply.record keeping will be the 'Status Symbol.'On computer generatedrecords ("E" forms) the 'Status Symbol' is BLACK; on manual records itwill be RED or BLACK.l-7. Responsibilities.It is the responsibility of each Commander,at every level of management, to ensure full compliance with thestandards prescribed in this manual.l-2
TMl-1500-328-23SECTION IIAIRCRAFT PREVENTIVE MAINTENANCE SYSTEM2-1.General.a.The aircraft preventive maintenance inspection system consistsof a series of recurring inspections, checks, and services.Thesystem is designed to provide a systematic examination of aircraft andaviation associated equipment during the item's life cycle. Itprovides for scheduled inspections, checks, services, and maintenanceactions required by certain situations, conditions, or incidents at apredetermined interval.Required inspections and maintenance actionsare normally listed in Chapter 1 of the appropriate -23 TMs, publishedin TBs, SOF messages, ASAMs or MIMs.b.It is the Commander's responsibility to emphasize the importanceof proper maintenance and ensure that all maintenance actions areaccomplished per the proper maintenance publications.Specificpreventive maintenance requirements for various aviation-associatedequipment (such as, avionics and weapon systems) are published inPreventiveseparate technical publications for each system.maintenance on aviation-associated equipment will be scheduled andcompleted together with aircraft maintenance inspections to lessendowntime and increase available flying hours and resources.The variety of aircraft in the Army inventory has resulted inC.several different inspection methods being used.These methodsinclude Phase Maintenance (PM), Progressive Phase Maintenance (PPM),Combat Phase Maintenance (CPM), Periodic (PE) and Combat Periodic(CPE) inspections. No matter what the name of the method is, theinspections are all part of The Aviation Preventive MaintenanceProgram.The preventive maintenance program includes instructions forinspecting aircraft, and processing aircraft that have been damageddue to environment, weather, or accident/incident. All inspections,checks, services, and related maintenance actions must be documentedmanually on the appropriate forms and records, or electronically(ULLS-A, ELAS, or LAS) per DA Pamphlet 738-751.Items designated as managed components/parts are listed ind.TB l-1500-341-01, Aircraft Components Requiring Management andHistorical Data Reports, for units using manual forms and records, andIt isfor ULLS-A user's in the ULLS-A Component Legitimate Code File.extremely important that the requirements of TB l-1500-341-01 and theULLS-A Component Legitimate Code File are fully complied with by allpersonnel when dealing with managed components and parts.The Commander is authorized to increase the scope and frequencye.of any maintenance action when an aircraft or aviation-associated itemis subjected to unusual situations; such as, adverse environmental or2-l
TM l-1500-328-23weather conditions, mission type, periods of extended inactivity, orflight crew and/or maintenance personnel experience level.f.Under no circumstance should the operating hours on an airframebe zeroed or adjusted as a result of a basic overhaul, or depot levelairframe modification. AMCOM may direct that the original airframehours be zeroed when an aircraft undergoes extensive depot level work,which results in a major configuration change that includes theassignment of a new airframe serial number.Annotate the DA Form2408-15, Historical Record For Aircraft, with the old airframe serialnumber and airframe hours logged against that serial number, andsubmit two DA Form 241Os, copy 3 showing an "M" loss for the oldserial number and a copy 2 showing an "S" gain for the new serialnumber.NOTEThe variety of aircraft types, combined with severaldistinctly different inspection methods and an assortment ofinspection checklists, may cause confusion as to the properprocedure to use when documenting an inspection and relatedfaults or requirements.In the event that any checklist,regardless of the date the checklist was published, therequirements of DA Pamphlet 738-751 and any related AMCOMelectronic message dated later then the DA Pamphlet 738-751,will take precedence.2-2.Flights and Maintenance Inspections under OperationalEmergencies.Required inspection and maintenance action intervalswill not be exceeded except when an actual operational emergencyexists.Operational emergencies are combat, weather, environmental,or other conditions, which would require flight to evacuate aircraft,personnel, or essential equipment.Commanders are authorized topostpone essential maintenance actions during emergency conditions.Since safety can be jeopardized when inspections or maintenanceactions are delayed, each emergency operational extension must beevaluated, on a case by case basis.When an aircraft is operatedbeyond the scheduled inspection or component replacement due timeunder an emergency condition, a "Circled Red/Black X" status symboland an appropriate statement, must be entered on DA Form 2408-13-1(-E)per DA Pamphlet 738-751.The Commander must ensure that the aircraftstatus symbol is changed to a Red/Black "X" immediately uponUNDER NO CIRCUMSTANCE will any type oftermination of the emergency.training or evaluation exercise be considered an emergency.Commanders may determine itEvacuation of Grounded Aircraft.2-3.necessary to evacuate an aircraft that is on a Red/Black "X" status.The "one time evacuation mission" clearance provision stated in DAPamphlet 738-751 will be followed.2-2
TM l-1500-328-232-4.Scheduled Preventive and Phase Maintenance Inspections.a. These inspections are due at predetermined flying hour orcalendar intervals.They provide for systematic examination of theaircraft, and associated equipment at specified intervals during theirservice life.The intervals for scheduled maintenance inspections arepublished in the applicable aircraft maintenance TM or phasemaintenance checklist.Planning and scheduling will be used tomaximize use of available flying hours and make sure the inspectionintervals are not exceeded.b. Most TMs for standard aircraft (aircraft identified in AR700-138) include a series of preventive maintenance checklists.Thechecklists assist maintenance personnel by organizing required tasksin an easy to follow sequence.The checklist is an extension of theaircraft -23 TM.If a checklist has not been developed for a specifictype or model aircraft, the inspection and servicing instructions areincluded in the -23 TM.C.Aircraft that are classified as non-standard aircraft (aircraftnot identified in AR 700-138) will be inspected and maintained asfollows:(1) Standard aircraft that have been reclassified to non-standardwill be inspected and maintained using the original TMs andmaintenance procedures.(2) Aircraft gained from other United States military services(Air Force, Navy, or Marines) will be inspected and maintained usingthe manuals and methods of the other military service.(3) Aircraft that are "civilian in nature," extensively modified,or in development evaluation, seldom have established militarymaintenance procedures.These aircraft will be inspected andmaintained using the manufacturer's maintenance instructions andmanuals.All actions shall be documented per DA Pamphlet 738-751,unless specifically directed by AMCOM to be documented per FederalAviation Regulations (FAR), and Federal Aviation Administration (FAA)policies.2-5.Phase Maintenance Inspection Method.a. This system includes two inspection elements, the PhaseMaintenance Inspection (PM) and a Preventive Maintenance Daily (PMD)or a Preventive Maintenance Service (PMS).It provides a methodicalexamination of the aircraft and associated equipment.Requirementsfor these inspections are in the applicable PMD, PMS and PM inspectionchecklists.2-3
TM l-1500-328-23The PMD and PMS are visual inspections that include someb.operational checks.The aircraft and associated equipment is checkedto ensure satisfactory performance during the interval between phaseinspections.Disassembly of components is not required unless majorfaults are found, but removal of screens, panels, and inspectionplates may be required to complete the inspection.(1) PMD Inspection.Inspection required after the last flight ofthe mission day or before the first flight of the next mission day.Flights/missions extending beyond 24 hours from the first take off ofthe mission, that calls for intermediate stops, loading/unloading,servicing, and so on does not require a new PMD inspection to completethe mission.The PMD is due at first engine shutdown or crew changeafter passing the 24-hour mark from the first take off of the mission.Refer to the individual aircraft PMD checklist for specific PMDrequirements.(2) PMS Inspection.The PMS is similar to a PMD inspection withthe primary difference being when it is due.Usually a PMS is dueevery 10 flying hours or 14 days, which ever occurs first; however,the interval may vary depending on the type of aircraft.This type ofinspection is considered a recurring inspection and must be listed onthe aircraft DA Form 2408-18.The tolerance window stated inparagraph 2-10 shall not be used to extend the PMS inspectioninterval. Several PMS checklists state that when the forecasted flyinghours for a mission, is greater than the number of hours remaininguntil the PMS is due, the inspection must be completed before thestart of the mission; however, some checklists permit an extension ofthe due time. Deliberate over-flights of the PMS due time shall beavoided, any extension or deferment of the PMS could be inherentlyUnless specifically authorized in the applicable PMSdangerous.checklist, or approved by the Commander under the provisions inparagraph 2-2 or 2-3, over-flight of the PMS inspection interval isprohibited.Phase Maintenance Inspection.The PM inspection is a thoroughC.and searching examination of the aircraft and associated equipment.Removals of access plates, panels, screens, and some partialdisassembly of the aircraft is required to complete the inspection.PM inspections are due after an appointed number of flying hours orcalendar interval from the completion of the last PM inspection. PMinspection cycle numbers and requirements are listed in the applicableRequirements may vary depending on the PMaircraft PM checklist.PM inspections are numbered consecutivelyinspection cycle number.within a cyclic system. When the last inspection in the cycle iscompleted, the numbering system restarts with the next inspection dueFor example; aircraft that have a four inspectionbeing number one.thephaseinspectionswill be number 1, 2, 3, 4 (end of firstcycle,performinspectionnumber 1, 2, 3, 4 (end of secondrestart,cycle);PMinspectionsmustbe completed in sequence. Ifandsoon.cycle),2-4
TM l-1500-328-23an aircraft is subjected to a depot level overhaul, before the end ofa cycle, the sequence number will be reset to number one.Thesequence number will not be reset when only depot level repairs aredone.Depot level repairs must not be confused with depot overhaul.A PM inspection is complete when all maintenance and inspectionrequirements have been completed.2-6.Progressive Phase Maintenance (PPM) Method.a. This inspection method resembles the PM method; however, it is aseparate inspection method that must not be confused with the PMmethod.This inspection method currently applies only to the OH-58Dand OH-58D(I) helicopters.The PPM inspection method consists of twointerrelated parts.Part I is a series of separate progressiveinspection checklists that become due after a designated number ofPart II consists of a PMS type inspection that isflying hours.required after a designated number of flying hours, or expiration of anumber of calendar days (whichever comes first).The PMS requirementsare performed between progressive phase inspection intervals and arealso included as a part of each PPM element.The unique nature ofthis inspection method provides the greatest mission flexibility;however, the requirements stated in the PPM checklist must be followedas written.b.Part I of the PPM inspection method is a series of progressiveinspection checklists that are sequentially numbered and must beperformed in sequence.Inspections are due after an appointed numberof flying hours.Each progressive inspection due time is figured fromthe start of the progressive inspection cycle, not from the completionof the last PPM.If an inspection is completed early or late it doesnot effect the scheduling of the remaining inspections in the cycle.For example, if there are 15 inspections per cycle, and the intervalbetween inspections is 40 flying hours, and the current cycle startedwhen the aircraft had 1380 hours, the first progressive inspection isdue at 1420 hours, the second at 1460 hours, the third at 1500 hours,and so forth.If the second progressive inspection was completed at1455 hours, the third progressive inspection is still due at 1500This method is unusual in that when a progressive inspectionhours.comes due the aircraft is not taken out of service, instead it isallowed to continue in use with the checklist requirements beingperformed when the aircraft is available.The checklist requirementsmay be performed all at one time, or spread out over a period timeuntil the next progressive inspection is due.For example, if theprogressive inspection interval is 40 hours, with the next progressiveinspection being due at 1320 hours, and the PPM checklist authorizesthe PPM element to be started up to 4 hours early (as early as 1316aircraft hours), all tasks listed in the PPM element and the PMSchecklist must be completed no later then 1360 aircraft hours (aIf the PPM inspection element is not completedwindow of 44 hours).2-5
TMl-1500-328-23before the next scheduled PPM (1360 in the example above), theaircraft must be placed in a Red/Black "X" status until all requiredactions have been completed.C.Part II of the PPM inspection method is considered a preventivemaintenance service.The PPM-PMS checklist has a dual purpose.Firstit details the requirements of the PPM-PMS inspection that must beperformed after an appointed number of flying hours or calendar days.Second, it reduces the overall size of the PPM manual by listing itemsthat are common to all PPM elements.The appointed number of flyinghours or calendar days between PPM-PMS inspections is stated in thePPM manual.It is necessary that the PPM-PMS inspections be completedat regular intervals.However, if the forecasted flying hours for amission are greater than the number of hours remaining until the nextPPM-PMS inspection, the inspection should be completed before thestart of the mission. The PPM-PMS inspection should not be overflownexcept, for the conditions stated in paragraphs 2-2 and 2-3.2-7.Periodic/PMS Inspection Method. Currently only "H-60" seriesaircraft use the Periodic (PE) type inspection method.Under thissystem, two inspection elements are used.These elements are referredto as PMS-1, an hour/calendar PMD type inspection, and PMS-2, aperiodic inspection.The two elements provide a systematicexamination of the aircraft and associated equipment.The primedifference between a Phase Inspection and a Periodic Inspection isthat the inspection requirements under the periodic are always thesame.The Phase Inspection Method also uses the acronym PMS to referto some of its elements; however, the Periodic/PMS and PPM-PMSinspection methods are distinctly different and must not beintermixed.Requirements listed in PMS checklists 1 and 2, aredefined as follows:The PMS-1 (lo-hours/l4 day) is like the PMD inspection, thea.primary difference being when it is due. The inspection is to becompleted after 10 flying hours or 14 days whichever comes first.This is a visual inspection that may require some limited operationalThe disassembly of components is not required; but somechecks.screens, panels, or inspection plates may need to be removed.ThePMS-1 inspection is considered a recurring inspection that must belisted on the aircraft DA Form 2408-18; however, the tolerance windowstated in paragraph 2-10 is not authorized.If there are aninsufficient number of flying hours available to complete a scheduledflight, the current H-60 series PMS-1 checklist allows for anextension of the due time, however, flight operations may exceed theauthorized extension only under the conditions stated in paragraph 2-2Deliberate over flights of the inspection interval for theand 2-3.If the 14-daypurpose of utilizing the PMS-1 extension is prohibited.inspection comes due before the hourly requirement, the PMS-1 must becompleted before the first flight of the mission day.2-6
TM l-1500-328-23b.The PMS-2 inspection is a thorough and searching examination ofthe aircraft and associated equipment.During the PMS-2 inspectionaccess plates, panels, and screens are removed and some partialdisassembly of the aircraft will be required.Requirements under thePhase Method often vary between the phase elements.PMS-2 inspectionsare due after a designated number of flying hours since new or thecompletion of the last periodic inspection.The PMS-2 inspectionsmust be accomplished when due and may be overflown only under theconditions stated in paragraph 2-2 a
Manual for The Army Maintenance Management System-Aviation (TAMMS-A), is the Army's authority for the use, preparation and disposition of aircraft forms and records. Except for the special instructions stated in this TM, letters of deviation, written correspondence from 1-1.