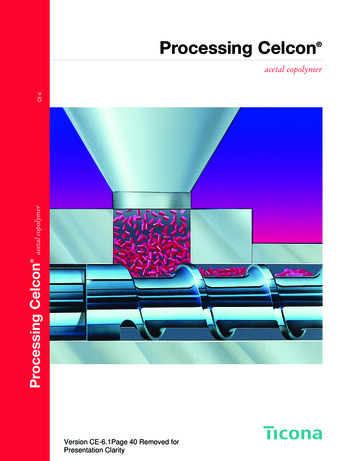
Transcription
Processing Celcon Processing Celcon acetal copolymerCE-6acetal copolymerVersion CE-6.1Page 40 Removed forPresentation Clarity
Celcon acetal copolymerForewordThe Celcon Acetal Copolymer Processing and Troubleshooting guide is written for plastics processors whorequire specific information on start-up, processing techniques and troubleshooting using this versatile group ofproducts. Material handling techniques, resin drying conditions and health and safety issues are also included.Chapters 1 and 2 cover an introduction to Celcon acetal copolymer grades and physical characteristics,regulatory and flammability listings, start-up and shutdown procedures, and the safety and health aspectspertaining to handling Celcon acetal copolymer. This information is pertinent to all processing methods.These two chapters should be read before attempting to process any grade of Celcon acetal copolymer.Chapter 3 is devoted to the important topic of molded part dimensional stability, including part shrinkage,annealing, dimensional tolerances and the effect of moisture absorption on part dimensions. Each of the finalfour chapters of the manual describes a specific processing technique: injection molding, extrusion, blow moldingand rotational casting, and includes a troubleshooting section. Information on machine settings, mold design, and(where appropriate) screw design is also included.For more information on material characteristics and part and mold design, consult the following manuals:Celcon acetal copolymer Short Term Properties (CE-4), Designing with Plastic: The Fundamentals (TDM-1)and Designing with Celcon acetal copolymer (CE-10). They are available by contacting your local Ticonasales representative, by calling our Technical Information Hotline at 1-800-833-4882, or on our web site,www.ticona.com.Comments and suggestions for improving this and other Ticona literature are always welcome, and may be sent tous at the above phone number, by writing to us at the address shown on the back cover or by e-mailing thewebmaster on our internet site.1
Celcon acetal copolymerTable of 41.5Chemistry of Acetal CopolymersGeneral CharacteristicsProduct TypesRegulatory Codes and Agency ListingsProduct Support777882.General Guidelines112.12.22.32.42.52.62.7Storage and HandlingSafety and Health InformationFlammabilityDryingProcessing Start-UpChanging from Another ResinChanging from a Different Grade ofCelcon Acetal Copolymer2.8Processing Shutdown2.9Use of Regrind2.10Secondary Operations2.10.1 Finishing2.10.2 Surface Treatment1111111212121313131414143.Dimensional Stability153.1153.23.33.43.53.6Shrinkage Caused by Processing(Injection Molding)Part WarpagePost-Molding ShrinkageAnnealingTolerancesMoisture Absorption4.Injection 4.2.4EquipmentBarrel and ScrewNozzlesPlasticizing CapacityClamping ForceMold DesignGeneral CriteriaMold BasesMold Cavities and CoresMold Surface ines2DimensionalStability3InjectionMolding4Blow Molding5Extrusion6RotationalCasting72
Celcon acetal 7.24.84.8.14.8.2Sprue BushingsRunnersRunnerless MoldingMolded-In InsertsOutsert MoldingGatingVentsCooling ChannelsDraftParting LineAuxiliary EquipmentMold Temperature Control UnitsProcess ControlProcessingTypical Molding ConditionsMelt TemperatureMold Surface TemperatureInjection PressureCavity Pressure Measurement(CPM) TechnologyCushionInjection SpeedSolidification TimeDecompression SettingsScrew SpeedCycle TimeProcess Optimization: Conducting a Designof Experiments (DOE)Quality Control of Molded PartsPart WeightPart DimensionsEffect of Molding Conditions onMechanical PropertiesUnreinforced Celcon Acetal GradesGlass/mineral Coupled Celcon Acetal GradesMolding ProblemsDeposits in MoldTroubleshooting5.Blow Blow Molding MethodsExtrusion Blow MoldingInjection Blow MoldingEquipmentExtruderScrewsScreen PackBreaker PlateDie 3232
Celcon acetal 637373838385.4.15.4.25.4.3DieHopperMoldsProcessing ParametersBarrel TemperatureMold TemperatureBlowing PressureEffects of Process Variables on PartDimensional Stability and Part QualityMold ShrinkageSurface AppearanceImpact uipmentMaterials of ConstructionExtruder BarrelScrew DesignScreen PackHead and Die DesignHopperHigh Speed Tubing ExtrusionEquipmentProcessing ParametersProfile ExtrusionEquipmentProcessing ParametersTroubleshootingProfile 4444444444457.Rotational MoldsParticle SizeProcessing ParametersResin Drying ConditionsPart Heating Oven ParametersPart Cooling olding4Blow Molding5Extrusion6RotationalCasting74
Celcon acetal copolymerList of TablesTable 1.1Table 2.1Table 2.2Table 2.3Table 3.1Table 3.2Table 3.3Table 4.1Table 4.2Table 4.3Table 4.4Table 4.5Table 4.6Table 4.7Table 4.8Table 5.1Table 5.2Table 5.3Table 5.4Table 6.1Table 6.2Table 6.3Table 6.4Table 6.5Table 6.6Table 7.15Regulatory ListingsTypical Start-Up ConditionsEffect of Remolding (Regrind) on theProperties of UnreinforcedCelcon AcetalEffect of Remolding (Regrind) on theProperties of Glass-CoupledCelcon AcetalEffect of Processing Conditionson Part ShrinkageShrinkage Before and After AnnealingRecommended Annealing ProcedureTypical Injection Molding Screw forPlasticizing Celcon Acetal CopolymerTypical Runner Size Recommendationsfor Celcon Acetal CopolymerRecommended Gate Dimensions forRectangular Edge GatesTypical Start-Up ConditionsApproximate Cycle Times as a Functionof Wall Thickness – Unreinforced GradesEffect of Molding Conditions onMechanical Properties Unreinforced GradesTypical Molding Conditions forShrinkage Range - Unreinforced GradesTroubleshooting Guide - InjectionMolding Celcon Acetal CopolymerComparison of Injection and ExtrusionBlow Molding ProcessesTypical Screw Characteristics to PlasticizeCelcon Acetal Copolymer Blow MoldingTypical Blow Molding ConditionsTroubleshooting Guide - Blow moldingRecommended Metering ScrewDimensions for Extruding Celcon AcetalTypical Conditions for Tubing ExtrusionHigh Speed Tubing ExtrusionTroubleshooting GuideTypical Conditions for Filmand Sheet ExtrusionFilm and Sheet Troubleshooting GuideProfile Extrusion Troubleshooting GuideRotational Casting Troubleshooting 464749
Celcon acetal copolymerList of FiguresOverviewFig. 3.1Fig. 3.2Fig. 3.3Fig. 3.4Fig. 4.1Fig. 4.2Fig. 4.3Fig. 4.4Fig. 4.5Fig. 5.1Fig. 5.2Fig. 5.3Fig. 5.4Fig. 5.5Fig. 5.6Fig. 5.7Fig. 5.8Fig. 6.1Fig. 6.2Fig. 7.1Effect of Molding Conditions andWall Thickness on Mold ShrinkageShrinkage due to Heat Aging for 9.0Standard Melt Flow Grade of Celcon AcetalWater Absorption by Unfilled CelconAcetal Under Various ConditionsDimensional Changes due to WaterAbsorption by Unfilled Celcon AcetalTypical Screw Profile for InjectionMolding Celcon AcetalRecommended Check Valve DesignRecommended Molded-in Insert DesignsOutsert Molded Moving Parts: Gear,Cam and SpringSome Basic Gate Designs Suitablefor Celcon AcetalFlow Pin Divider to Promote SmoothFlow and Avoid Weld LinesParison Die with Adjustable CorePin for Control of Parison ThicknessEffect of Mold Temperature on ShrinkageEffect of Cooling Time on ShrinkageEffect of Blow Pressure on ShrinkageEffect of Wall Thickness on ShrinkageLanded Pinch-Off for ImprovedImpact StrengthBlow Molded Fluidics ContainerRecommended Metering Screw for ExtrusionMiscellaneous Post-Formed ProfilesRotational Molding ty3InjectionMolding4Blow 363838383839394145486
Celcon acetal copolymer1. Overview1.1 Chemistry of Acetal PolymersAcetal polymers are chemically known aspolyoxymethylenes (POM). Two types of acetalpolymers are commercially available:Homopolymer is prepared by polymerizinganhydrous formaldehyde to form a polymercomposed of oxymethylene repeating units(-CH2O-). Acetal homopolymer products havesomewhat better short term mechanical propertiesthan the copolymer.Copolymers, including Celcon acetal copolymer,are prepared by copolymerizing trioxane (a cyclictrimer of formaldehyde) with a cyclic ether (usuallycontaining an ethoxy or other oxyalkylene group) toform a polymeric chain composed of oxymethylene(-CH2O-) and oxyethylene (-CH2-CH2-O-) orsimilar repeating units. Copolymers have a widerprocessing window, better long term mechanicalproperties and superior chemical resistance comparedto homopolymers, and are inherently more stable andresistant to thermal degradation during service life.This is because the randomly dispersed comonomerunits block polymer “unzipping” under thermalstress, or exposure to hot water or hot alkalinesolutions.Both the homopolymer and copolymer are endcapped, and also contain specific additives to preventirreversible thermo-oxidative depolymerizationof the polymer backbone during processing.1.2 General CharacteristicsCelcon acetal copolymer is a high strength, crystallineengineering thermoplastic material having an unusualand desirable balance of properties. It is an idealcandidate to replace metals and thermosets becauseof its predictable long-term performance overa wide range of in-service temperatures and harshenvironments. Celcon acetal retains properties suchas high strength, creep resistance, fatigue endurance,wear resistance and solvent resistance under verydemanding service conditions.Celcon acetal can be easily converted from pelletform into parts of different shapes using a variety ofprocesses such as injection molding, blow molding,extrusion, rotational casting and compressionmolding. Rod, slab and sheet stock which can bereadily machined into desired shapes are also available.71.3 Product TypesBoth standard and special grades of Celcon acetalcopolymer are designed to provide a wide range ofproperties to meet specific applications. Standard andcustom grades of Celcon acetal copolymer can beobtained in pre-compounded color form or colorconcentrates which may be blended with othergrades. All colorants used in Celcon resins are lead,mercury, and cadmium-free, and all Celcon acetalproducts conform to current environmental(OSHA) regulations for these metals. Consult ourbrochure: “Celcon Acetal Copolymer Short TermProperties” (CE-4) for information on specificgrades. The most common categories of Celconresins are described below.General Purpose: General purpose M-series productsare identified by melt flow rate. Divide the gradenumber by 10 to obtain the melt flow rate. Forexample, Celcon M90 has a melt flow rate of 9.0(grams per 10 minutes, per ASTM D 1238 or ISO1133, @ 190 C and 2.16 Kg. load). In comparison toM90, products designated by a higher melt flow rate,i.e. M270, fill thinner walls and complex shapes morereadily, maintain the same strength and stiffness, butexhibit a slight decrease in toughness. Products withlower melt flow rates, i.e. Celcon M25, exhibitincreased toughness compared to Celcon M90 butmay be more difficult to mold into parts with thinwalls or long flow paths.Glass Fiber Coupled: Glass fiber coupled (GC)products provide higher strength, stiffness and creepresistance than the unfilled grades. These products areidentified with a number indicating the percentage ofshort glass fiber in the product and are based ongeneral purpose Celcon polymers. The glass fibers arechemically coupled to the polymer matrix.Glass Bead Filled: These glass bead (GB) filledgrades contain glass beads for lower shrinkage,better dimensional tolerances and warp resistance,and are especially helpful when molding large, flatand thin-walled parts.Low Wear: Low wear (LW) grades are chemicallymodified to provide low coefficient of friction andenhanced wear resistance, and are exceptional fordemanding applications requiring good slidingproperties, reduced gear and bearing noise andenhanced lubricity.
Celcon acetal copolymerMineral Coupled: These mineral coupled (MC)products contain chemically coupled mineral fillers invarying percentages. The mineral filled grades arerecommended whenever resistance to warpage(especially in thin sections) and dimensional stabilityare key application parameters. They are generallytougher than the glass bead filled polymers but aremore difficult to color uniformly.Ultraviolet Resistant: The ultraviolet resistant (UV)products are available with various melt flow rates innatural and a wide variety of colors and are lead,mercury and cadmium-free. They are speciallyformulated for improved resistance to color shift andmechanical degradation from ultraviolet light (bothsunlight and fluorescent lighting). Consult the Ticonabrochure, “Celcon Ultraviolet-Resistant GradesExtend Part Life in Harsh Environments” (CE-UV)for further information about these products.Weather Resistant: Weather resistant (WR) productsare formulated for maximum outdoor weatheringresistance. Several different melt flow rate grades areoffered. They are available in black color only.Antistatic: These antistatic (AS) products arechemically modified to decrease static build-up forapplications such as conveyer belt links and audio andvideo cassette hubs and rollers.Electrically Conductive: These electrically conductive(EC) grades are used for applications requiring lowelectrical resistance and/or rapid dissipation of staticbuild-up. Some electrically conductive grades containcarbon fibers and exhibit high strength and stiffness.Laser Markable: The laser markable (LM) grades ofCelcon acetal copolymer have been developed withenhanced capability for laser printing. These blackproducts produce extremely robust white markingsfor applications such as bar codes, graphic oralphanumeric characters, and 2-D symbology.One of the grades has good ultraviolet light stability.Both grades have excellent toughness and dimensionalstability for many applications includingautomotive parts.Colors: Most grades are available in natural, blackand custom colors. There are standard colorconcentrates available for use in all natural grades.Custom color concentrates can also be made.1.4 Regulatory Codes and Agency ListingsMany grades of Celcon acetal are in compliance with,or approved under a variety of agency specificationsand regulatory standards as shown in Table 1.1. Notall grades are covered by all regulatory listings. CallProduct Information Services at 1-800-833-4882 forfurther information on which grades are approvedunder the various regulations.1.5 Product SupportIn addition to our technical publications, experienceddesign and application development engineers areavailable for assistance with part design, moldflowcharacterization, materials selection, specificationsand molding trials. Call your local Ticona Polymerssales representative, or Product Information Servicesat 1-800-833-4882 for further help.Impact Modified: The impact modified (TX)products are formulated to provide moderate to highlevels of improvement in impact strength and greaterflexibility compared to the standard product.81
Celcon acetal copolymerTable 1.1 · Regulatory ListingsPlumbing Code Bodies:International Association of PlumbingMechanical Officials (IAPMO)Building Officials Conference of America (BOCA)Southern Standard Building Code9Plumbing fixtures and specific plumbing and mechanicalapplications covered in the various codesCanada Standards Association (CSA)Plumbing fixtures, fittings and potable water contact items,“UL” ratings in CanadaPlastic Pipe Institute (PPI)Recommended Hydrostatic Design Stress (RHDS) ratingof 1,000 psi at 23 C (73 F) as an injection moldedplumbing fittingFood and Drug Administration (FDA)Repeated-use food contact applications including foodmachinery components conforming to 21 CFR 177.2470United States Pharmacopoeia (USP)Class VI CompliantNSF InternationalStandards 14, 51, 61Items including plumbing components, beveragedispensers, etc., for contact with potable waterUnderwriters Laboratories (UL)Various UL ratings for flammability, electrical and thermalservice useInternational Association of Food Industry Suppliers (IAFIS)Sanitary Standards 3AUnited States Department of Agriculture (USDA)Approved for direct contact use with meat and poultryproductsASTM D 4181 [Supersedes ASTM D2133,Military Specification LP-392-A, Mil-P-6137A(MR)]General Material SpecificationSAE J2274Society of Automotive Engineers Global SpecificationsISO 9988-1, -2Designation system processing conditions andtesting protocols for comparative properties.
Celcon acetal copolymerPower Seat BeltTransmission Gear Set1Celcon M90 Acetal Copolymer Provides: Lubricity Low Coefficient of Friction Resistance to Lubricants Mechanical Strength Fatigue Endurance Surface Hardness Dimensional Stability Ease of Molding10
Celcon acetal copolymer2. General Guidelines2.1 Storage and HandlingCelcon acetal copolymer should be stored in itsoriginal container on pallets in a dry place. Opencontainers should be carefully resealed beforereturning to storage. In the winter, containers of resinshould be brought into the warm processing area atleast 24 hours prior to use and allowed to come toroom temperature before opening. If this is not done,moisture in the air may condense on the surface ofthe pellets and lead to surface defects on molded orextruded plastic parts. This is especially critical withimpact modified grades which can be moisturesensitive and deteriorate during processing.The use of a hopper magnet in the feedstream ishighly recommended to insure against any form ofmetallic contamination which could occur whiletransporting the resin and cause equipment damage.Every effort should be made to avoid pellet spills orloss. Spilled pellets can be very slippery and mayresult in employee accidents. Pellet loss to theenvironment could lead to fines or other penaltiesunder Storm Water Regulations issued by theEnvironmental Protection Agency.Ticona Polymers supports the Society of the PlasticsIndustry Operation “Clean Sweep” program.2.2 Safety and Health InformationThe usual precautions must be observed as whenprocessing any hot and molten thermoplastic.CAUTION: Normal processing temperaturesand residence times should not be exceeded.Celcon acetal copolymer should never be heatedabove 238 C (460 F) nor be allowed to remainabove 193 C (380 F) for more than 15 minuteswithout purging. Excessively high temperature orlong residence time in a heated chamber can causethe resin to discolor and, in time, degrade to releaseformaldehyde, a colorless and irritating gas. Thisgas can be harmful in high concentrations, so properventilation is essential. If venting is inadequate, highpressures could develop in the equipment which maylead to blow back through the feed area. If no exit isavailable for these gases, the equipment mayrupture and endanger personnel.11Consult the current Celcon acetal copolymer MaterialSafety Data Sheets (MSDS) for health and safety datafor specific grades of Celcon acetal copolymer priorto processing or otherwise handling these products.Copies are available by calling your local Ticona salesoffice or Customer Services at 1-800-526-4960 orfrom the internet site, www.ticona.com.2.3 FlammabilityWhen ignited, Celcon acetal copolymer burns withlittle or no smoke, and with a barely visible blueflame. Combustion products are carbon dioxide andwater. If Celcon acetal copolymer burns with amuffled flame and combustion is incomplete,
Table 4.8 Troubleshooting Guide - Injection 32 Molding Celcon Acetal Copolymer Table 5.1 Comparison of Injection and Extrusion 35 Blow Molding Processes Table 5.2 Typical Screw Characteristics to Plasticize 36 Celcon Acetal Copolymer Blow Molding Table 5.3 Typical Blow Molding Conditions 37 Table 5.4