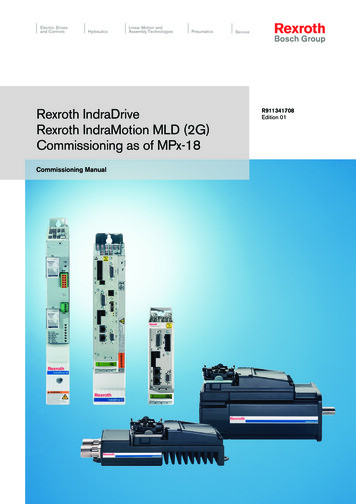
Transcription
Electric Drivesand ControlsHydraulicsLinear Motion andAssembly TechnologiesPneumaticsRexroth IndraDriveRexroth IndraMotion MLD (2G)Commissioning as of MPx-18Commissioning ManualServiceR911341708Edition 01
Bosch Rexroth AGTitleDOK-INDRV*-MLD3-F*STEP-CO01-EN-PRexroth IndraDrive Rexroth IndraMotion MLD (2G) Commissioning as of MPx-18Rexroth IndraDriveRexroth IndraMotion MLD (2G)Commissioning as of MPx-18Type of DocumentationDocument TypecodeInternal File ReferenceCommissioning 7c73cfa0a6846a501c5ff29-1-en-US-3Purpose of DocumentationThis document explains how to commission the drive and how to create asimple PLC program for IndraMotion MLD with IndraLogic 2G.Record of RevisionsSee chapter "About This Documentation", marginal note "Editions of ThisDocumentation"Copyright Bosch Rexroth AG 2013This document, as well as the data, specifications and other information setforth in it, are the exclusive property of Bosch Rexroth AG. It may not be re‐produced or given to third parties without its consent.LiabilityNoteThe specified data is intended for product description purposes only and shallnot be deemed to be a guaranteed characteristic unless expressly stipulatedin the contract. All rights are reserved with respect to the content of this docu‐mentation and the availability of the product.This document has been printed on chlorine-free bleached paper.
DOK-INDRV*-MLD3-F*STEP-CO01-EN-PRexroth IndraDrive Rexroth IndraMotion MLD (2G) Commissioning as of MPx-18Bosch Rexroth AGI/83Table of ContentsTable of ContentsPage1About This Documentation. 32Introduction. Overview. 5Reference Documentations. 7Drive Systems, System Components. 7Motors. 7Cables. 8Firmware. 8Important Directions for Use . 11Appropriate Use . 11Introduction. 11Areas of Use and Application. 11Inappropriate Use. 12Safety Instructions for Electric Drives and Controls. 13Definitions of Terms. 13General Information. 14Using the Safety Instructions and Passing Them on to Others. 14Requirements for Safe Use. 14Hazards by Improper Use. 15Instructions with Regard to Specific Dangers. 16Protection Against Contact with Electrical Parts and Housings. 16Protective Extra-Low Voltage as Protection Against Electric Shock . 17Protection Against Dangerous Movements. 18Protection Against Magnetic and Electromagnetic Fields During Operation and Mounting. 19Protection Against Contact with Hot Parts. 20Protection During Handling and Mounting. 20Battery Safety. 20Protection Against Pressurized Systems. 21Explanation of Signal Words and the Safety Alert Symbol. 21Preparation and Setup. 23Step 1: Check Hardware and Firmware Requirements. 23Hardware Requirements. 23Firmware Requirements. 23Step 2: Install Software. 24Step 3: Set up the Drive System. 24IndraMotion MLD-S. 24IndraMotion MLD-M. 26Step 4: Establish Communication between Drive Controller and Commissioning PC. 27Establishing an Ethernet Connection to the Drive Controller. 27
II/83Bosch Rexroth AGDOK-INDRV*-MLD3-F*STEP-CO01-EN-PRexroth IndraDrive Rexroth IndraMotion MLD (2G) Commissioning as of MPx-18Table of .17.3.27.3.37.47.4.17.4.27.4.38Commissioning and Parameterization. 35Step 5: General Commissioning an Parameterization of the Drive. 35Step 6: Activate and Configure the Integrated PLC (IndraMotion MLD) . 37Activating IndraMotion MLD . 37MLD Settings . 37Activating MLD-M for Multi-Axis Applications. 39Step 7: Configure the Interfaces and Data Channels of MLD. 40General Information. 40Cyclic Data Channels. 41Acyclic Data Channels / Interfaces. 42Explanation of the MLD Data Channels. 42Programming. 63Step 8: Configure and Control the PLC. 63Overview. 63Configuring the PLC. 63Controlling the PLC. 64Step 9: Create a Program. 65Creating a New Program. 65Importing / Using an Existing Program. 68Specific Features of MLD-2G / Changes in Comparison to MLD-1G. 73Step 10: Load and Activate the Program. 74Loading the Program. 74Starting the Program. 75Creating a Boot Project. 76Step 11: Test the Program. 77Online Display. 77Monitoring Variables with Sampling Trace. 77Oscilloscope Function. 77Service and Support. 79Index. 81
DOK-INDRV*-MLD3-F*STEP-CO01-EN-PRexroth IndraDrive Rexroth IndraMotion MLD (2G) Commissioning as of MPx-18Bosch Rexroth AG3/83About This Documentation1About This DocumentationEditions of This DocumentationEditionRelease 5First editionTab.1-1:Means of Representation in ThisDocumentationRecord of RevisionsTo facilitate reading this documentation, the table below contains the meansof representation and notations of recurring terms.What?How?For example.Paths and sequences of menus.are represented step bystep in boldfaceClick Window Show view PropertiesButtons and keys. are represented in anglebracketsClick Add orImportant facts which are to behighlighted in the body textBoldfaceFor remote axes, "Active" TRUE signals that .Parameter names, diagnostic mes‐sage names, function designationsQuotation marks"Axis2" to "Axis10" correspond to the remote axes.The remote axes contained in the list "P‑0‑1801.x.10,CCD: Addresses of projected drives" .Tab.1-2:Press Ctrl Alt Conventions of NotationAll important notes are highlighted. A symbol tells you what kind of note isused in the text. The symbols have the following significances:DANGER.DANGER indicates a hazardous situation which, if not avoided, will result indeath or serious injury.WARNING.WARNING indicates a hazardous situation which, if not avoided, could resultin death or serious injury.CAUTION.In case of non-compliance with this safety instruction, minor or moderate in‐jury could occur.NOTICE.In case of non-compliance with this safety instruction, property damage couldoccur.This box contains important information that should be taken intoconsideration.This symbol highlights useful tips and tricks.
4/83Bosch Rexroth AGDOK-INDRV*-MLD3-F*STEP-CO01-EN-PRexroth IndraDrive Rexroth IndraMotion MLD (2G) Commissioning as of MPx-18About This DocumentationYour FeedbackYour experience is important for our improvement processes of products anddocumentations.If you discover mistakes in this documentation or suggest changes, you cansend your feedback to the following e-mail address:Dokusupport@boschrexroth.deWe need the following information to handle your feedback: The number indicated under "Internal File Reference". The page number.
DOK-INDRV*-MLD3-F*STEP-CO01-EN-PRexroth IndraDrive Rexroth IndraMotion MLD (2G) Commissioning as of MPx-18Bosch Rexroth AG5/83Introduction2Introduction2.1OverviewThis documentation explains how to commission the drive, install IndraWorkswith MLD-2G and create a simple PLC program for IndraMotion MLD‑S andMLD‑M with the MPx‑18VRS firmware.The paragraphs below describe the steps required when usingRexroth IndraMotion MLD for the first time. We distinguish the following pha‐ses: Preparation and Setup Commissioning ProgrammingThe steps for setup and commissioning are only required for theinitial commissioning.The figure below shows an overview of the required commissioning steps.
6/83Bosch Rexroth AGDOK-INDRV*-MLD3-F*STEP-CO01-EN-PRexroth IndraDrive Rexroth IndraMotion MLD (2G) Commissioning as of MPx-18IntroductionFig.2-1:Commissioning Rexroth IndraMotion MLD
DOK-INDRV*-MLD3-F*STEP-CO01-EN-PRexroth IndraDrive Rexroth IndraMotion MLD (2G) Commissioning as of MPx-18Bosch Rexroth AG7/83Introduction2.2Reference Documentations2.2.1Drive Systems, System ComponentsDrive Systems with Single-Axis or Double-Axis Drive ControllersTitleKind of documentationDocument typecode1)Material numberDOK-INDRV*- R911 Project Planning ManualHCS01******-PRxx-EN-P322210Project Planning ManualKCU02 KSM02-PRxx-EN-P335703Project Planning ManualSYSTEM*****-PRxx-EN-P309636Project Planning ManualHMV-S-D HCS-PRxx-EN-P318790Project Planning ManualCxx02******-PRxx-EN-P338962Project Planning ManualADDCOMP****-PRxx-EN-P306140Rexroth IndraDrive CsDrive Systems with HCS01Mi Drive Systemswith KCU02, KSM02, KMS02Drive Systems with HMV01/02HMS01/02, HMD01, HCS02/03Supply Units, Power SectionsHMV, HMS, HMD, HCS02, HCS03Control SectionsCSE02, CSB02, CDB02, CSH02Additional Components and Accesso‐ries1)Tab.2-1:2.2.2In the document typecodes, "xx" is a wild card for the current edition ofthe documentation (example: PR01 is the first edition of a ProjectPlanning Manual)Documentations – Drive Systems, System ComponentsMotorsTitleKind of documentationRexroth IndraDyn Document typecode1)Material numberDOK-MOTOR*- R911 A Asynchronous Motors MAD / MAFProject Planning ManualMAD/MAF****-PRxx-EN-P295781H Synchronous Kit Spindle MotorsProject Planning ManualMBS-H******-PRxx-EN-P297895L Synchronous Linear MotorsProject Planning ManualMLF********-PRxx-EN-P293635L Ironless Linear Motors MCLProject Planning ManualMCL********-PRxx-EN-P330592S Synchronous Motors MKEProject Planning ManualMKE*GEN2***-PRxx-EN-P297663S Synchronous Motors MSKProject Planning ManualMSK********-PRxx-EN-P296289S Synchronous Motors MSMData SheetMSM********-DAxx-EN-P329338S Synchronous Motors QSKProject Planning ManualQSK********-PRxx-EN-P330321T Synchronous Torque MotorsProject Planning ManualMBT********-PRxx-EN-P2987981)Tab.2-2:In the document typecodes, "xx" is a wild card for the current edition ofthe documentation (example: PR01 is the first edition of a ProjectPlanning Manual)Documentations – Motors
8/83Bosch Rexroth AGDOK-INDRV*-MLD3-F*STEP-CO01-EN-PRexroth IndraDrive Rexroth IndraMotion MLD (2G) Commissioning as of MPx-18Introduction2.2.3CablesTitleKind of documentationRexroth Connection CablesIndraDrive and IndraDynSelection Data1)Tab.2-3:2.2.4Document typecode1)Material numberDOK-CONNEC- R911 CABLE*INDRV-CAxx-EN-P322949In the document typecodes, "xx" is a wild card for the current edition ofthe documentation (example: CA02 is the second edition of the docu‐mentation "Selection Data")Documentations – CablesFirmwareTitleKind of documentationDocument typecode1)Material numberR911 Rexroth IndraDriveApplication ManualDOK-INDRV*-MP*-18VRS**APxx-EN-P338673Release e BookDOK-INDRV*-GEN1-PARA**RExx-EN-P328651Reference on tion ce on 8FunctionsRexroth IndraDriveMPx-18Version NotesRexroth IndraDriveMPx-16 to MPx-18ParametersRexroth IndraDriveMPx-16 to MPx-18Diagnostic MessagesRexroth IndraDriveIntegrated Safety Technologyas of MPx-1x (Safe Torque Off)Rexroth IndraDriveIntegrated Safety Technologyas of MPx-1x (Safe Motion)Rexroth IndraDriveRexroth IndraMotion MLD (2G)Libraries as of MPx-18Rexroth IndraDrive2)RexrothIndraMotion MLD (2G)as of MPx-18
DOK-INDRV*-MLD3-F*STEP-CO01-EN-PRexroth IndraDrive Rexroth IndraMotion MLD (2G) Commissioning as of MPx-18Bosch Rexroth AG9/83IntroductionTitleKind of documentationDocument typecode1)Material numberR911 Rexroth IndraDrive2)RexrothCommissioning ce on MLD (2G)as of MPx-18Rexroth IndraMotionMLD 13VRSService Tool1)2)Tab.2-4:In the document typecodes, "xx" is a wild card for the current edition ofthe documentation (example: RE02 is the second edition of a Refer‐ence Book)In preparationDocumentations – Firmware
10/83Bosch Rexroth AGDOK-INDRV*-MLD3-F*STEP-CO01-EN-PRexroth IndraDrive Rexroth IndraMotion MLD (2G) Commissioning as of MPx-18
DOK-INDRV*-MLD3-F*STEP-CO01-EN-PRexroth IndraDrive Rexroth IndraMotion MLD (2G) Commissioning as of MPx-18Bosch Rexroth AG11/83Important Directions for Use3Important Directions for Use3.1Appropriate Use3.1.1IntroductionRexroth products reflect the state-of-the-art in their development and theirmanufacture. They are tested prior to delivery to ensure operating safety andreliability.WARNINGPersonal injury and property damage causedby incorrect use of the products!The products have been designed for use in industrial environments and mayonly be used in the appropriate way. If they are not used in the appropriateway, situations resulting in property damage and personal injury can occur.Rexroth as manufacturer is not liable for any damages resultingfrom inappropriate use. In such cases, the guarantee and theright to payment of damages resulting from inappropriate use areforfeited. The user alone carries all responsibility of the risks.Before using Rexroth products, the following pre-requisites must be met toensure appropriate use of the products:3.1.2 Personnel that in any way, shape or form uses our products must firstread and understand the relevant safety instructions and be familiar withtheir appropriate use. If the products take the form of hardware, then they must remain in theiroriginal state, in other words, no structural changes are permitted. It isnot permitted to decompile software products or alter source codes. Damaged or faulty products may not be installed or put into operation. Make sure that the products have been installed in the manner descri‐bed in the relevant documentation.Areas of Use and ApplicationDrive controllers made by Rexroth are designed to control electrical motorsand monitor their operation.Control and monitoring of the Drive controllers may require additional sensorsand actors.The drive controllers may only be used with the accessories andparts specified in this documentation. If a component has notbeen specifically named, then it may neither be mounted nor con‐nected. The same applies to cables and lines.Operation is only permitted in the specified configurations andcombinations of components using the software and firmware asspecified in the relevant Functional Descriptions.Drive controllers have to be programmed before commissioning to ensurethat the motor executes the specific functions of an application.Drive controllers of the Rexroth IndraDrive line have been developed for usein single- and multi-axis drive and control tasks.
12/83Bosch Rexroth AGDOK-INDRV*-MLD3-F*STEP-CO01-EN-PRexroth IndraDrive Rexroth IndraMotion MLD (2G) Commissioning as of MPx-18Important Directions for UseTo ensure application-specific use of Drive controllers, device types of differ‐ent drive power and different interfaces are available.Typical applications include, for example: Handling and mounting systems, Packaging and food machines, Printing and paper processing machines and Machine tools.Drive controllers may only be operated under the assembly and installationconditions described in this documentation, in the specified position of normaluse and under the ambient conditions as described (temperature, degree ofprotection, humidity, EMC, etc.).3.2Inappropriate UseUsing the Drive controllers outside of the operating conditions described inthis documentation and outside of the technical data and specifications givenis defined as "inappropriate use".Drive controllers may not be used, if . they are subject to operating conditions that do not meet the specifiedambient conditions. This includes, for example, operation under water,under extreme temperature fluctuations or extremely high maximumtemperatures. Furthermore, Drive controllers may not be used in applications whichhave not been expressly authorized by Rexroth. Please carefully followthe specifications outlined in the general Safety Instructions!Components of the Rexroth IndraDrive system are products ofcategory C3 (with limited availability) according to IEC 61800‑3.To ensure that this category (limit values) is maintained, suitableline filters must be used in the drive system.These components are not provided for use in a public low-volt‐age network supplying residential areas with power. If these com‐ponents are used in such a public network, high-frequency inter‐ference is to be expected. This can require additional measuresof radio interference suppression.
DOK-INDRV*-MLD3-F*STEP-CO01-EN-PRexroth IndraDrive Rexroth IndraMotion MLD (2G) Commissioning as of MPx-18Bosch Rexroth AG13/83Safety Instructions for Electric Drives and Controls4Safety Instructions for Electric Drives and Controls4.1Definitions of TermsApplication DocumentationApplication documentation comprises the entire documentation used to in‐form the user of the product about the use and safety-relevant features forconfiguring, integrating, installing, mounting, commissioning, operating, main‐taining, repairing and decommissioning the product. The following terms arealso used for this kind of documentation: Operating Instructions, Commis‐sioning Manual, Instruction Manual, Project Planning Manual, Application De‐scription, etc.ComponentA component is a combination of elements with a specified function, whichare part of a piece of equipment, device or system. Components of the elec‐tric drive and control system are, for example, supply units, drive controllers,mains choke, mains filter, motors, cables, etc.Control SystemA control system comprises several interconnected control componentsplaced on the market as a single functional unit.DeviceA device is a finished product with a defined function, intended for users andplaced on the market as an individual piece of merchandise.Electrical EquipmentElectrical equipment encompasses all devices used to generate, convert,transmit, distribute or apply electrical energy, such as electric motors, trans‐formers, switching devices, cables, lines, power-consuming devices, circuitboard assemblies, plug-in units, control cabinets, etc.Electric Drive SystemAn electric drive system comprises all components from mains supply to mo‐tor shaft; this includes, for example, electric motor(s), motor encoder(s), sup‐ply units and drive controllers, as well as auxiliary and additional compo‐nents, such as mains filter, mains choke and the corresponding lines and ca‐bles.InstallationAn installation consists of several devices or systems interconnected for adefined purpose and on a defined site which, however, are not intended to beplaced on the market as a single functional unit.MachineA machine is the entirety of interconnected parts or units at least one ofwhich is movable. Thus, a machine consists of the appropriate machine driveelements, as well as control and power circuits, which have been assembledfor a specific application. A machine is, for example, intended for processing,treatment, movement or packaging of a material. The term "machine" alsocovers a combination of machines which are arranged and controlled in sucha way that they function as a unified whole.ManufacturerThe manufacturer is an individual or legal entity bearing responsibility for thedesign and manufacture of a product which is placed on the market in the in‐dividual's or legal entity's name. The manufacturer can use finished products,finished parts or finished elements, or contract out work to subcontractors.However, the manufacturer must always have overall control and possessthe required authority to take responsibility for the product.ProductExamples of a product: Device, component, part, system, software, firmware,among other things.Project Planning ManualA project planning manual is part of the application documentation used tosupport the sizing and planning of systems, machines or installations.Qualified PersonsIn terms of this application documentation, qualified persons are those per‐sons who are familiar with the installation, mounting, commissioning and op‐eration of the components of the electric drive and control system, as well aswith the hazards this implies, and who possess the qualifications their work
14/83Bosch Rexroth AGDOK-INDRV*-MLD3-F*STEP-CO01-EN-PRexroth IndraDrive Rexroth IndraMotion MLD (2G) Commissioning as of MPx-18Safety Instructions for Electric Drives and Controlsrequires. To comply with these qualifications, it is necessary, among otherthings,1) to be trained, instructed or authorized to switch electric circuits and devi‐ces safely on and off, to ground them and to mark them2) to be trained or instructed to maintain and use adequate safety equipment3) to attend a course of instruction in first aidUserA user is a person installing, commissioning or using a product which hasbeen placed on the market.4.2General Information4.2.1Using the Safety Instructions and Passing Them on to OthersDo not attempt to install and operate the components of the electric drive andcontrol system without first reading all documentation provided with the prod‐uct. Read and understand these safety instructions and all user documenta‐tion prior to working with these components. If you do not have the user doc‐umentation for the components, contact your responsible Rexroth sales part‐ner. Ask for these documents to be sent immediately to the person or per‐sons responsible for the safe operation of the components.If the component is resold, rented and/or passed on to others in any otherform, these safety instructions must be delivered with the component in theofficial language of the user's country.Improper use of these components, failure to follow the safety instructions inthis document or tampering with the product, including disabling of safety de‐vices, could result in property damage, injury, electric shock or even death.4.2.2Requirements for Safe UseRead the following instructions before initial commissioning of the compo‐nents of the electric drive and control system in order to eliminate the risk ofinjury and/or property damage. You must follow these safety instructions. Rexroth is not liable for damages resulting from failure to observe thesafety instructions. Read the operating, maintenance and safety instructions in your lan‐guage before commissioning. If you find that you cannot completely un‐derstand the application documentation in the available language,please ask your supplier to clarify. Proper and correct transport, storage, mounting and installation, as wellas care in operation and maintenance, are prerequisites for optimal andsafe operation of the component. Only qualified persons may work with components of the electric driveand control system or within its proximity. Only use accessories and spare parts approved by Rexroth. Follow the safety regulations and requirements of the country in whichthe components of the electric drive and control system are operated. Only use the components of the electric drive and control system in themanner that is defined as appropriate. See chapter "Appropriate Use". The ambient and operating conditions given in the available applicationdocumentation must be observed. Applications for functional safety are only allowed if clearly and explicitlyspecified in the a
The paragraphs below describe the steps required when using Rexroth IndraMotion MLD for the first time. We distinguish the following pha‐ ses: Preparation and Setup Commissioning Programming The steps for setup and commissioning are only required for the initial commissioning.