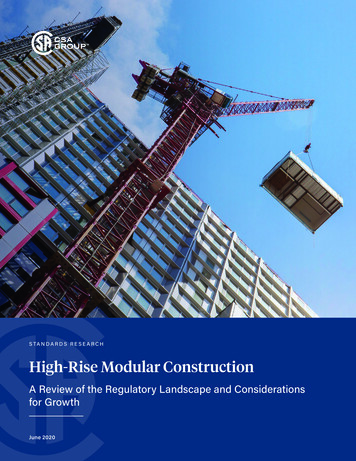
Transcription
S TA N D A R D S R E S E A R C HHigh-Rise Modular ConstructionA Review of the Regulatory Landscape and Considerationsfor GrowthJune 2020
HIGH-RISE MODULAR CONSTRUCTION – A REVIEW OF THE REGULATORYLANDSCAPE AND CONSIDERATIONS FOR GROWTHAuthorsJessica Doermann, ArupKelly Finzel, ArupJohn Barrot, ArupAdvisory PanelAubrey LeBlanc, Ontario Building Officials AssociationKevin Ernst, Oakville Stamping and Bending LimitedTom Hardiman, Modular Building InstituteAna-Maria Tomlinson, CSA Group (Project Lead)Dwayne Torrey, CSA GroupHelene Vaillancourt, CSA GroupJonathan Fernando, CSA GroupContributorsAmir Shahrokhi, SHoP ArchitectsJoseph Solway, ArupBen Paget, Polcom ModularLaurie Robert, NRB Inc.Brent Roberts, Jerol TechnologiesMohamed Al-Hussein, University of AlbertaBrett JonesNicole Dubowski, ArupCameron McCartney, National ResearchCouncil CanadaRobert Burak, Canadian Precast PrestressedConcrete InstituteChris Rausch, University of WaterlooRobert Schmidt, Marriott InternationalDavid Farnsworth, ArupRoger Krulak, FullStack ModularDavid Johnson, City of TorontoTom Greenough, EntuitiveDavid Walsh, Marriott InternationalTom Hardiman, Modular Building InstituteDavid Warne, Z ModularTroy Galvin, PCL Constructors Canada Inc.Greg Sloditskie, MBS ConsultingUlrik Seward, City of CalgaryJeremy Macht, ArupVal Sylaj, Canadian Precast PrestressedConcrete InstituteDisclaimerThe report has been produced by Arup and is owned by CSA Group. It is designed to provide information regarding the subjectmatter covered. The views expressed in this publication are those of the authors and the interviewees. The conclusions drawnin the report are those of the authors. Arup and CSA Group do not accept any responsibility for the contents or any loss ordamage which might occur as a result of following or using data or advice given by the interviewees in this publication.Front cover image reproduced with permission from SHoP Architects.csagroup.org2
HIGH-RISE MODULAR CONSTRUCTION – A REVIEW OF THE REGULATORYLANDSCAPE AND CONSIDERATIONS FOR GROWTHTable of ContentsAuthors2Advisory Panel2Contributors2Disclaimer2Executive Summary61. Introduction71.1 Methodology71.2 Terminology71.3 Modular Typologies81.4 History of Modular Construction82. Current State of Modular Construction92.1 Prevalence and Market Penetration92.2 Preconceived Notions and Views3. Drivers and Benefits of Modular Construction Growth10113.1 Cities and Urbanization113.2 Sustainability113.3 Workplace Safety123.4 Project Schedule and Cost134. Considerations for Modular Construction Growth4.1 Planning13134.1.1 Project Suitability134.1.2 Procurement Methods144.1.3 Roles and Responsibilities154.1.4 Project Financing154.1.5 Project Insurance154.1.6 Production Capacity154.1.7 Supply Chain16csagroup.org3
HIGH-RISE MODULAR CONSTRUCTION – A REVIEW OF THE REGULATORYLANDSCAPE AND CONSIDERATIONS FOR GROWTH4.2 Design and Construction174.2.1 Design for Lateral Loads174.2.2 Connections – Structural174.2.3 Connections – Building Systems184.2.4 Fire-Rated Assemblies and Structural Fire Protection184.2.5 Acoustics194.2.6 Construction Tolerances194.2.7 Building Envelope and Waterproofing214.2.8 Transport, Staging, and Storage214.2.9 Lifting, Placement, Installation, and Finishing224.2.10 Fire Safety During Construction224.2.11 Chain of Custody234.3 Approvals234.3.1 Authorities Having Jurisdiction (AHJs)234.3.2 Factory and Product Certification Programs244.3.3 Third-Party Accredited Certification Bodies254.3.4 Inspections254.4 Education254.5 Additional Considerations255. Codes and Standards Review5.1 Canada26265.1.1 National Building Code265.1.2 Standard on Certification of Prefabricated Construction265.1.3 Standard on Certification of Manufacturers of Steel Building Systems275.1.4 Standard on Manufactured Homes275.2 United States275.2.1 International Building Code275.2.2 State Certification Programs275.2.3 Standards in Development27csagroup.org4
HIGH-RISE MODULAR CONSTRUCTION – A REVIEW OF THE REGULATORYLANDSCAPE AND CONSIDERATIONS FOR GROWTH5.3 Europe/United Kingdom285.4 Australia286. Codes and Standards Gap Analysis297. Conclusion31csagroup.org5
HIGH-RISE MODULAR CONSTRUCTION – A REVIEW OF THE REGULATORYLANDSCAPE AND CONSIDERATIONS FOR GROWTHExecutive SummaryWith rapid urbanization and population growth, more people live and work in cities. This has led to an increasedneed for taller buildings in urban environments and a lack of affordable housing in cities. The construction industrycontinues to grapple with rising labour costs because of shortages in skilled labour and persistently stagnantconstruction productivity. These market dynamics present an opportunity for innovation.Modular and off-site construction can help to address these challenges. Modular construction has origins datingback to the 17th century beginning predominantly with single-family homes. Today, modular construction is used inmany applications, including residential, commercial, health care, and others. Most existing modular buildings arelow or mid-rise, however there have been several high-rise volumetric modular buildings constructed in the lastdecade and demand appears to be increasing.This research report explores the current state, drivers, benefits, and barriers to the growth of high-rise volumetricmodular construction. This report includes findings from a workshop and interviews with modular manufacturers,designers, regulators, and industry trade groups as well as existing research in modular construction.North American model codes and standards organizations, including the Canadian Standards Association (CSA) andthe International Code Council (ICC), have recognized the need for codes and standards to be developed or tailoredto respond to the specific challenges of modular construction. A review and gap analysis of codes and standardsrelated to modular construction has yielded several recommendations for the Canadian market.The following are the four highest priority items that were identified through this research project with respect tocodes and standards development for modular construction (see Section 7 for more information):1. Develop a new standard for off-site/modular construction.2. Increase and expand adoption of CSA Standard A277 by the provinces.3. Review and update CSA Standard A277.4. Develop guidance for AHJs for off-site/modular buildings.There are many factors that contribute to the uptake of modular construction. The above recommendations willsupport growth in modular construction by providing a more comprehensive and consistent regulatory environmentfor the design, construction, and approval of modular buildings.csagroup.org6
HIGH-RISE MODULAR CONSTRUCTION – A REVIEW OF THE REGULATORYLANDSCAPE AND CONSIDERATIONS FOR GROWTH“The benefits of volumetric modularconstruction can be maximizedwhen as much work as possible iscompleted off-site.”Reproduced with permission from Z Modular1. IntroductionThis research report explores the current state, benefits,drivers, and barriers of growth of high-rise volumetricmodular construction as well as provides a review andgap analysis of the regulatory landscape pertaining tomodular construction in Canada.1.1 MethodologyA literature review was completed to evaluate availablepublished information regarding high-rise volumetricmodular construction. Resources included researchreports from academia, industry trade groups, andsubject matter experts. Additionally, interviews wereconducted with industry stakeholders that wereidentified as having extensive knowledge in themodular construction industry, including designers,manufacturers, regulators, researchers, trade groups,and general contractors. Finally, a workshop wasconducted with industry experts to explore and validatefindings that had been identified through the literaturereview and interviews. The research included sources,interviews, and experiences from within and outside ofCanada. Although generally having a North Americanfocus, most of the content could have applicabilityinternationally as well.Due to the limited number of completed high-risevolumetric modular projects, the report also incorporatesresearch and expertise from low-rise applications.Therefore, the information presented has relevanceto low-rise applications as well. This report does notdirectly consider modular construction for single-familydwellings.1.2 TerminologyConventional construction refers to approaches wherecomponents, systems, and assemblies are constructedat the final installed location of the building.Off-site construction refers to manufacturing andassembly of building elements at a location other thanthe final installed location of the building. Panelizedconstruction and modular construction are bothmethods of off-site construction.Panelized construction refers to the manufacturing andassembly of wall panels and floor panels off-site that areshipped to a site and require additional assembly to formthree-dimensional spaces and a completed building. Itis off-site construction but not modular construction.Modular construction refers to the manufacturing andassembly of modules off-site such as a fully finishedbathroom pod, or a subassembly for mechanical,electrical, and plumbing (MEP) systems. The modulesare shipped to site and assembled to form a completedbuilding.Volumetric modular construction refers to themanufacturing and assembly of modules that will includecomplete spaces such as an apartment, bathroom, andcorridor (or portion thereof) in a single module. Thesecan be fully finished off-site. Volumetric modules usuallycsagroup.org7
HIGH-RISE MODULAR CONSTRUCTION – A REVIEW OF THE REGULATORYLANDSCAPE AND CONSIDERATIONS FOR GROWTHarrive on-site complete with all elements intact, includingfinishes, and only require placement and connections tobe made [1]. The distinction from panelized and modularis that volumetric modules can be erected or stackedon-site to form the completed building. Structural andbuilding service connections need to be made on-site tothe foundation and to the utilities, and between modules.and internationally. In the United States and Canada,recent and upcoming code changes allow for the useof mass timber (e.g., cross-laminated timber) in highrise applications, providing another option for structuralmaterials. Mass timber in high-rise applications hastypically been panelized, though there are volumetricsystems emerging as well.This report will use the term high-rise volumetricmodular construction given the focus on high-riseapplications. Other terms are used in the industryfor three-dimensional modular construction such asprefabricated prefinished volumetric construction(PPVC), permanent modular construction (PMC), andprefabricated prefinished modular construction, off-siteconstruction.1.4 History of Modular Construction1.3 Modular TypologiesPrior to the 1940s modular construction was primarilyused for single-family homes. It was at this timethat modular construction methods were applied tocommercial projects and later used in hospitality andmulti-family residential buildings [2]. The common threadwith these historical booms in modular constructionwas a rising demand for housing.The benefits of volumetric modular construction can bemaximized when as much work as possible is completedoff-site. While the foundations will be constructed usingconventional construction methods for all projects,the remaining portions of the building could be fullymodular up to a certain number of storeys. For tallerbuildings, a conventionally built lateral system may berequired. However, modular construction does not haveto be an all or nothing strategy. Where subassemblies(e.g., bathroom pods) are built modularly, these can becombined with either volumetric modular constructionor conventional construction methods.Modular projects can be constructed from structuralmaterials, including steel, concrete, or wood, or acombination of these. It is estimated that in the UnitedStates and Canada, wood frame, steel, and concretemake up respectively 70%, 25%, and 5% of materialsused in modular construction. This distribution relatesdirectly to the material choices for low-rise construction,which has historically been the largest portion of themodular market. In Singapore and Hong Kong, concretemodules are more common than in North America.For high-rise volumetric modular buildings, a steelstructural system has been the predominant type inNorth America. Prefabricated concrete floors havebeen used in volumetric applications in North AmericaThe first applications of modular construction can betraced back to as early as 1670 when prefabricatedbuildings were shipped from England to the UnitedStates [2]. During the gold rush of the 1800s and thepost–Second World War era of the 1940s, modularconstruction was used to provide fast, low-cost housingfor workers and returning servicemen [2].The tragic collapse of the Ronan Point 22-storeyapartment building in London, England, in 1968 resultedin public distrust in prefabricated construction. A gasexplosion caused the prefabricated concrete floors andslabs to fail in one corner of the building, causing fourfatalities and 17 injuries [3].Modular construction has been used for many differenttypes of building occupancies, including singlefamily dwellings, multi-family residential units, studenthousing, hospitality, health care, office, commercial, andeducational.While most of the existing modular construction is lowrise, there are several high-rise volumetric modularbuildings that have been completed globally (see Table 1).As of July 2019, the Clement Canopy building located inSingapore is known as the tallest volumetric modularbuilding in the world. This project includes two 40-storeytowers with 505 residential apartments. The towers aremade up of 1,899 modules and took 30 months tocomplete.csagroup.org8
HIGH-RISE MODULAR CONSTRUCTION – A REVIEW OF THE REGULATORYLANDSCAPE AND CONSIDERATIONS FOR GROWTHTable 1: Select completed high-rise volumetric modular buildings [4]BuildingHeightYear Completed24 storeys, 251 ft200919 storeys201532 storeys, 359 ft2016CitizenM Shoredich, London, UK10 storeys2016Chapter Lewisham, London, UK12 storeys2016Grand Felda House, Wembley, UK17 storeys2016Apex House, Wembley, UK29 storeys201711 Mapleton Crescent, Wandsworth, UK27 storeys2018Alt Hotel Calgary, Alberta, Canada9 storeys2019101 George Street, Croydon, UK44 storeys2019Clement Canopy, Singapore40 storeys2019AC Hotel NoMad, New York, NY26 storeysUnder constructionVictoria Hall, Wolverhampton, UKFelda House, Wembley, UK461 Dean Street, Brooklyn, NY, USAAs designers and manufacturers look to build taller,many are focusing their interest on volumetric modularconstruction because of the amount of work that can becompleted off-site, in addition to the numerous benefitsit provides to project stakeholders and the community.2. Current State of Modular ConstructionThis section describes the current state of modularconstruction, including the prevalence and marketpenetration as well as the perception of modularconstruction in the marketplace.2.1 Prevalence and Market PenetrationPermanent modular construction represented nearly4% of the overall construction market in Canada in 2018[2], and the market penetration is similar in the UnitedStates. Prevalence and market penetration is attributableto various factors that include the quality perceptionof modular construction, which was identified byMcKinsey as one of seven determining factors [5]. Theother six factors are access to materials, supply chainand logistics, labour dynamics, local site constraints,and consolidated and continuous demand volumes [5].Based on these factors, certain geographical marketsmay be better suited to promote the growth of themodular construction industry than others. Currently,the use of modular construction is present in mostmarkets; however, some markets have been quicker torecognize its benefits and adopt modularization.A given market’s access to materials, supply chain, andlogistics can have a major impact on the financials of aproject. In many cases, these factors become interrelated.As modular construction increases in popularity,countries may not have the manufacturing capacity tokeep up with demand, which may result in the outsourcingof manufacturing to foreign markets. This provides asolution to the issue of supply chain quantity; however,csagroup.org9
HIGH-RISE MODULAR CONSTRUCTION – A REVIEW OF THE REGULATORYLANDSCAPE AND CONSIDERATIONS FOR GROWTHdifficulties may arise when addressing differing materialratings and testing requirements between jurisdictions.Additional project costs may accrue if there is a need toperform component/assembly testing or instead sourcepreviously tested and approved materials that complywith the requirements of the final build site. Utilizing aglobal supply chain can therefore help ensure volumedemand is met but requires additional considerationsthat are not necessary when utilizing a domestic supplychain.it is generally regarded that Europe, specifically theUnited Kingdom, is the most developed geographicalarea in the modular construction industry. Industryprofessionals believe that North American countries arebehind, but the combination of housing demand, skilledlabour cost and availability, as well as several otherfactors have these markets poised for significant growthin the coming years.Modular construction can help address skilled labourshortages by broadening the labour pool. For modularprojects, most work is performed off-site in factorieswhere workers at stations tend to have a narrower scopeof work and therefore may not need the same breadthof skills that tradesmen on a traditional site wouldrequire. Factory and module certification programsmay have requirements for qualifications and licensingof construction workers and design professionals thatneed to be considered. Similarly, labour laws, prevailingwages, and union/non-union labour agreements shouldbe taken into consideration but given the complexityand geographic differences will not be examined furtherin this report.Generally, perceptions of modular construction areaccompanied by criticism and skepticism regarding thebenefits that can be derived from its implementation.While there are some markets that recognizemodular construction as a step up in quality fromconventional construction methods, many populationsand geographical locations have yet to adopt thisview. Modular construction can evoke images ofprefabricated structures such as trailers located behindschools (i.e., pods or portables), trailer homes, ortemporary structures that are being used well beyondtheir intended life cycle. It has been associated with astigma of being old, cheap, ugly, of poor-quality, andlacking in innovation [5]–[7]. One company believes sostrongly that the word “modular” carries a stigma that itinstead uses the term “off-site construction” [7], whichis becoming more prevalent.Site constraints can impact the ability of modularconstruction to penetrate a market. For cold weatherclimates, such as in Northern Canada, modularconstruction can be a positive alternative to conventionalconstruction methods because progress can continueirrespective of weather conditions.These factors have and continue to shape themarket penetration of modular construction globally.Singapore’s desire for quick construction has led itsHousing Development Board to build roughly 20,000to 30,000 units a year using off-site construction [5]. InJapan modular construction is viewed in higher regardthan conventional construction methods, helpingthe country achieve a broader adoption of modularconstruction principles. The United States has relativelyfragmented and small-scale construction ecosystemsdue to low-capacity manufacturers and a multitudeof differing jurisdictions [5]. While the world’s tallestmodularly constructed building resides in Singapore,2.2 Preconceived Notions and ViewsDespite current perceptions, industry professionalsbelieve that modular is going to play a major role inthe future of construction. In recent years, people havebegun to see modular construction in a more positivelight, which is leading to higher demand and increasedindustry growth.Increased advocacy and success stories are pivotal intransforming the negative views and stigmas surroundingmodular construction [8]. News articles accompanyingstories about Clement Canopy, for example, containinformation about the Government of Singapore’spush to improve construction productivity along witha brief outline of some of the construction timelines,labour utilization, and sustainability benefits thatmodular construction can provide [9]. Publicity aboutsuccessful projects that include information about thecsagroup.org10
HIGH-RISE MODULAR CONSTRUCTION – A REVIEW OF THE REGULATORYLANDSCAPE AND CONSIDERATIONS FOR GROWTHstructure as well as the benefits that modular may offerto the community or environment may help to combatnegative views. Project experiences that highlightmodularly constructed buildings as indistinguishablefrom traditional ones are also important in combattingnegative views [7].3. Drivers and Benefits of ModularConstruction GrowthCurrent industry challenges as well as an increasedrecognition of the benefits of modular constructionhave recently helped it gain traction in the marketplace.Skilled labour shortages are currently at an all-time highand they are reflected by the increasing cost of on-sitelabour. Build Force Canada predicts a net labour lossof more than 33,000 workers over the next decade[10]. Other challenges such as housing shortages andthe desire for shortened project schedules are alsodriving the growth of the modular construction industry.Conventional construction is “laden with issues such asinefficiency, resource waste, a large carbon footprint,and health related issues for workers and nearbyresidents” [8]. Comparatively, modular construction’smeans and methods have the potential to mitigate issuessurrounding sustainability and worker/community safetyand to benefit many other aspects of the procurementand construction process, including the predictability ofconstruction costs and project schedules.3.1 Cities and UrbanizationMass urbanization of cities contributes to an evergrowing affordable and available housing crisis thatis prevalent across the globe. The United Nationsestimates that 68% of the world’s population will live inurban areas by 2050 – a 13% increase from 2018 [11].The World Bank estimates that 300 million new housingunits will be required by 2030 to accommodate theapproximate 3 billion people who will need new housingand basic infrastructure. [12].Countries such as Singapore, the United Kingdom,and the United States have begun exploring modularconstruction in order to keep up with the projecteddemand for new housing that will be needed. In NewYork City, the Department of Housing and PreservationDevelopment piloted a construction program, ModularNYC, to examine how modular construction could“deliver affordable housing opportunities fasterand more effectively” [13]. The program includedsolicitations for expressions of interest from owners/developers to participate. The city has a goal of building300,000 affordable homes by 2026 and is interestedin leveraging the innovative, sustainable, and speedbenefits of modular construction to do so [13], [14].Modular construction is particularly well suited toaddress the affordable and available housing crisis. Therepeatable floor plates of residential structures favourmodular construction (see Section 4.1.1) and can amplifythe construction schedule’s predictability and costcertainty generally associated with a modular approach(see Section 3.4).3.2 SustainabilityThe sustainable concepts of modular constructionpractices are an opportunity to satisfy shifting attitudestowards attaining greener practices, combatting climatechange, and reducing carbon emissions.Waste reduction is a significant benefit of modularconstruction. One case study of a high-rise volumetricmodular construction building in England saw wasteproduction equivalent to about 5% of the overallconstruction weight compared to an industry averageof about 10 to 13% [15]. Compared to conventionalconstruction methods where almost no waste isrecycled, approximately 43% of waste created duringthe modular manufacturing process is recycled [15].Material efficiencies begin in the factory where studieshave shown that the manufacturing process is moresustainable than conventional construction even beforegetting into specific building systems and materialselections [7]. This is because modular constructionprovides greater control over materials as they arepurchased and sized for a specific project, and thecontrolled environment of the factory allows unusedmaterials to be recycled back into the system to be usedin future projects [16], [6].csagroup.org11
HIGH-RISE MODULAR CONSTRUCTION – A REVIEW OF THE REGULATORYLANDSCAPE AND CONSIDERATIONS FOR GROWTH“Workers on modular projectsexperience less hazardousconditions when constructingmodules in a factory, includingless exposure to extreme weatherconditions, decreased noise, andimproved air quality.”Reproduced with permissions from PCL Constructors Inc.The use of off-site/modular construction results in lesswork being completed on-site, which benefits the localenvironment and community. It reduces the impacton local habitats, reduces site disturbance [7], andlessens noise pollution as it requires fewer workersand resources on-site, such as scaffolding, cranes, andbuilding materials [6]. Modular construction has alsoresulted in up to a 70% reduction in the number of visitsto the site by delivery vehicles [15]. The amount of airand water pollution due to dust and other constructionbyproducts is also decreased. Overall, the communitysurrounding the project site also benefits because mostof the work is completed off-site and the work on-site isdone on a reduced project schedule.Environmentally conscious individuals are demandinggreater accountability regarding wasted resources,such as construction debris that ends up in landfills. Thispopulation is actively seeking avenues to incorporatesustainable practices into their everyday lives, andmodular construction is a proven solution to reducingconstruction waste [2].3.3 Workplace SafetyCompleting a project modularly can result in improvedsafety for on-site workers as well as a reduction in timelost due to resulting injury [5], [6]. It is estimated that inmost modular construction projects, up to 80% of thelabour activity can be moved off-site [5] to ngworkplace safety.Workers on modular projects experience less hazardousconditions when constructing modules in a factory,including less exposure to extreme weather conditions,decreased noise, and improved air quality [16], [6], [1].The increased level of automation and the use of roboticsin some factories may pose new safety considerationsbut they can also reduce risk as fewer workers are nearconstruction materials. Additionally, because muchof construction occurs off-site there is a reduction inworksite debris that may otherwise present a trip hazardor a fire hazard [17].Workers may also experience less hazardous operationsin modular construction as work that was traditionallyconducted at high elevations (within or exterior tostructures or overhead) is shifted to a low elevationwithin a controlled factory environment. Reported fallrates on modular construction sites are substantiallylower compared to those on conventional constructionsites [16] that result in a significant reduction in thehours of leading-edge work. Fall risks are also reducedbecause less work is completed from scaffolding. Asthose entering the workforce look for employmentopportunities, placement in a hands-on position withcomparatively better safety is a substantial benefit toworkers and has the potential to drive significant growthfor the modular construction industry.It should be noted that there may be a potential additionalsafety risk in modular construction associated with thecsagroup.org12
HIGH-RISE MODULAR CONSTRUCTION – A REVIEW OF THE REGULATORYLANDSCAPE AND CONSIDERATIONS FOR GROWTHadded step of transporting modules from a factory tothe site, which may include transport of modules acrossprovinces or countries via multiple modes of transport.Once modules are at the site, crane and hoist activityto place modules can also present an additional risk toworkers. This risk can be mitigated by using experiencedprofessionals, and reducing the use of heavy equipment,swing stages, scaffolding, and leading-edge work canhelp further decrease the overall safety risk to workers.Overall a modular approach may offer a safer workenvironment than conventional construction byreducing some of the risk factors associated with thehighest number of labourer fatalities in the constructionindustry [18].3.4 Project Schedule and CostModular construction can be a faster and morecost-effective building strategy when compared toconventional construction methods. Many projectscan realize significant cost savings by completingwork using modular methods, with some plannedprojects forecasting cost savings of as much as 20% [5].However, there are documented cases where projectcosts increased using modular methods compared tocompletion using conventional construction. The abilityof modular construction to reduce project costs isdependent on many factors; therefore, every project maynot be able to achieve the potential financial benefitsof modular. These varying factors must be consideredholistically to determine if modular construction will befinancially beneficial.One of the greatest influencing factors for cost savingsin a modular construction project is the predictabilityand acceleration of the project schedule [8], withsome recent projects achieving a
(e.g., bathroom pods) are built modularly, these can be combined with either volumetric modular construction or conventional construction methods. Modular projects can be constructed from structural materials, including steel, concrete, or wood, or a combination of these. It is estimated that in the United