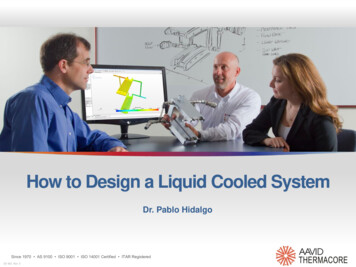
Transcription
How to Design a Liquid Cooled SystemDr. Pablo Hidalgo 2016AavidThermacore,Inc. AllRightsSince 1970 AS9100 ISO 9001ISO14001Reserved.Certified ITAR RegisteredAavid Thermacore Proprietary & ConfidentialQF 402 Rev E
Outline Introduction to liquid cooled systems Air vs liquid. Hydrodynamical requirements. Thermal requirements. Basic principles and equations Hydrodynamical Thermal 2Essential elements needed in the circuit.Liquid cooled system for computing applicationsLiquid cooled system for military applicationsSummary 2016 Aavid Thermacore, Inc. All Rights Reserved.Aavid Thermacore Proprietary & Confidential
Air vs. Liquid Cooling Heat transfer processes: Heat transport, which strongly depends on the mass flow rate and specificheat of the fluid.αΆ π π»π π» πππππ ππ Heat convection, which is primarily governed by the heat transfercoefficient h. π" π π»π π»π Air cooling is limited by specific heat. To dissipate large amounts ofpower, a large mass flow rate is needed. Higher flow speed, larger noise. Liquid cooling is able to achieve better heat transfer at much lowermass flow rates. Lower flow speed, lower noise. Heat transfer coefficients for air an liquid flows are orders of magnitudeapart. 25 hair 250 W/m2 K 100 hliquid 20,000 W/m2 K3 2016 Aavid Thermacore, Inc. All Rights Reserved.Aavid Thermacore Proprietary & Confidential
Hydrodynamical Requirements It is critical to calculate the total pressure drop(ΞPtotal) in the liquid line in order to size a pump. ΞPtotal influenced by flow regime, sudden expansions,contractions, bends, valves, etc To size a pump, two important parameters areneeded: Liquid flow rate Total head that the pump must generate to deliver therequired flow rate. 4Total head static head difference frictional head losses 2016 Aavid Thermacore, Inc. All Rights Reserved.Aavid Thermacore Proprietary & Confidential
Thermal Requirements A liquid cooled system is generally used in caseswere large heat loads or high power densities need tobe dissipated and air would require a very large flowrate. Water is one of the best heat transfer fluids due to itsspecific heat at typical temperatures for electronicscooling. Temperature range requirements defines the type ofliquid that can be used in each application. Operating Temperature 0oC, water cannot be used. Glycol/water mixtures are commonly used in militaryapplications, but the heat transfer capabilities aresignificantly lower than water.5 2016 Aavid Thermacore, Inc. All Rights Reserved.Aavid Thermacore Proprietary & Confidential
Essential Elements in a Liquid Cooled SystemPumpFan6 2016 Aavid Thermacore, Inc. All Rights Reserved.Aavid Thermacore Proprietary & ConfidentialCold PlateReservoirHeat ExchangerTubing
Hydrodynamic Equations Energy equation for steady pipe flow of an incompressible fluid.π-αΆ παΆπ π΄ π11 π ππ§1 π’1 ππ1 ππ΄1 π΄ ππ13π2ππ΄ 1π΄1 π2 2αΆ ππ§2 π’2 ππ2 ππ΄2 π΄ π1π12π2π22αΆ παΆπ π ππ§1 π’1 πΌ1παΆ ππ§2 π’2 πΌ1παΆπ2π21πΌ ΰΆ±π΄ π΄ππΰ΄€3ππ΄ Simplified energy equationπ1π12π2π22 πΌ1 π§1 βπ πΌ2 π§2 βπ‘ βπΏπΎ2ππΎ2π7 2016 Aavid Thermacore, Inc. All Rights Reserved.Aavid Thermacore Proprietary & ConfidentialLaminar Flow, Ξ± 2Turbulent Flow Ξ± 1.05ππ23ππ΄22 2
Hydrodynamic Equations Laminar flowπ1π12π2π22 πΌ1 π§1 βπ πΌ2 π§2 βπ‘ βπΏπΎ2ππΎ2π Turbulent flowπ1π2 π§1 π§2 βπΏπΎπΎπΏ π2βπΏ βπ ππ· 2π8 2016 Aavid Thermacore, Inc. All Rights Reserved.Aavid Thermacore Proprietary & ConfidentialβπΏ βπ Moody Diagram32ππΏππΎπ·2
Hydrodynamic Equations The head loss produced by the flow through bends, inlets, valves, etc is expressed by the equation:π2βπΏ πΎ2π Some of those K values are shown on theadjacent table. Energy equation is rewritten as:π1 π12π2 π22 π§1 π§2 βπΏπΎ 2ππΎ 2π Where the sum of hL includes frictionallosses, and losses due to fittings, contrations, valves, etc that are present in theflow loop.9 2016 Aavid Thermacore, Inc. All Rights Reserved.Aavid Thermacore Proprietary & Confidential
Thermal Equations (Heat Source) Heat source follows the Newtonβs law of cooling ππ " β(ππ ππ )where Tm depends on constant heat flux or constant temperatureboundary conditions and h is the LOCAL heat transfer coefficient (HTC). Energy balance equation:πππππ£ ππαΆ π ππ,π ππ,π If constant surface temperature boundary condition, heat rate equation:ΰ΄₯ π πππ where πΰ΄₯ is the average HTC and πππ is the log meanπππππ£ ππ΄temperature difference. Heat transfer coefficient can be estimated using the Nusselt number.βπ·ππ’ π Multiple correlations exists for laminar flow, turbulent flow, fullydeveloped flow, developing flow, heat source boundary conditions, etc that can be summarized in the following table:Aavid Thermacore, Inc. All Rights Reserved.10 2016Aavid Thermacore Proprietary & Confidential
Thermal Equations (Heat Source)Source Fundamentals of Heat anMass Transfer, Incropera and DeWittAavid Thermacore, Inc. All Rights Reserved.11 2016Aavid Thermacore Proprietary & Confidential
Thermal Equations (Heat Exchanger) Counterflow heat exchangers are the most efficient ones to be used. Cross-flow heat exchangers are typical in these applications but the thermalcharacteristics are very similar to that of counterflow but a correction factormust be applied. Overall energy balance is used to estimate maximum heat transfer rategiven certain input parameters (i.e. mass flow rate, fluid temperature, etc ) Heat exchanger calculations are based on the log mean temperaturedifference.π ππ΄πΉ ππππβ,π ππ,π πβ,π ππ,π π2 π1 πππ ππ π2 Ξ€ π1ππ πβ,π ππ,π ΰ΅ πβ,π ππ,π1π 1Ξ€βπ 1Ξ€βπ hi and ho can be calculated using the Nusselt number correlations shownearlier. Another way to size a heat exchanger would be to use the effectivenessNTU method.Aavid Thermacore, Inc. All Rights Reserved.12 2016Aavid Thermacore Proprietary & Confidential
Liquid Cooled System for ComputingApplications 2016AavidThermacore,Inc. AllRightsSince 1970 AS9100 ISO 9001ISO14001Reserved.Certified ITAR RegisteredAavid Thermacore Proprietary & ConfidentialQF 402 Rev E
Computer Desktop Liquid Cooling SystemHeat ExchangerLiquid PumpConnective TubingFluid Not ShownCold PlatesAavid Thermacore, Inc. All Rights Reserved.14 2016Aavid Thermacore Proprietary & Confidential
Key Reliability Issues Pump Reliability All Electro-mechanical devices such as pumps have finite life whichleads to reliability issues. Fluid Permeation Loss. Fluids tend to permeate through polymermaterials and joints. If too much fluid is lost due to permeation, the LCScould eventually stop working. Fluid Leakage Environmental Impact: Environmental concerns with cooling fluidleakage and disposal are issues.Aavid Thermacore, Inc. All Rights Reserved.15 2016Aavid Thermacore Proprietary & Confidential
Sub 1U LCS for High End Server Compute ModuleHeat Exchanger βSub 1U 4 x 95W AMD CPUβs 90 CFM per Module 0.20 C/W (c-a) 2 Pumps PCBPowered Sub 1U PCB Spacing2 Liquid PumpsAavid Thermacore, Inc. All Rights Reserved.16 2016Aavid Thermacore Proprietary & Confidential4 PMCP ColdPlatesLowPermTubing
Cold Plate TechnologyExamples of Cold Plate TechnologiesVertical Fin Cold Plate (VFCP) Utilizes closely spaced vertical finsto dissipate heat Moderate heat transfer coefficientspossiblePowder Metal Cold Plate (PMCP) Uses high surface area density todissipate heat High effective heat transfercoefficients possible Many flow geometries possibleInletOutletInletThermacoreTechnologyMetal PowderParticlesHeat Entersfrom BottomAavid Thermacore, Inc. All Rights Reserved.17 2016Aavid Thermacore Proprietary & Confidential
Cold Plate β Porous MetalAdvantages High Surface AreaHigh Heat Transfer CoefficientHigh Heat Flux ( 300 W/cm2)Low Thermal ResistanceLow Profile PackagingLow Mass ( 75 grams)Cool Single PhaseCoolant InWell-Bonded PorousMetal MatrixWarm Single PhaseCoolant OutHeat Sourcee.g.: computer chip,particle beam, EM radiation,laser diode arrayLiquid cooled heat sinks makeuse of high surface area andeffective heat transferavailable in a well-bondedporous metal matrix.Aavid Thermacore, Inc. All Rights Reserved.18 2016Aavid Thermacore Proprietary & Confidential
Performance Comparison - VFCP vs. PMCPResistance (deg-C/W/cm 2)0.12Lower Thermal Resistance Better Performance0.100.08VFCP Heat Input: 12mm x 12mm0.06BenefitPMCP Heat Input: 7mm x 7mm 40%0.040.02Courtesy: Dr. Kevin Wert0.000.00.10.20.30.4Coolant Flow Rate (GPM)Aavid Thermacore, Inc. All Rights Reserved.19 2016Aavid Thermacore Proprietary & Confidential0.50.6
Liquid-to-Air Heat Exchanger β Flat Tube with Rolled Fins All Aluminum Liquid-to-Air Heat Exchanger Maximizes Heat Transfer Efficiency & Volume Flat, low profile tubes that provide moresurface area. Metallurgical bond between components. Highly Reliable and Durable One-piece integral structure. Components are joined together by analuminum brazing process . Leak-tight .Desktop Heat Exchanger Custom designed for the specific application Desktop Chassis 1U Server Chassis Vertical position blade server1U Server Heat ExchangerAavid Thermacore, Inc. All Rights Reserved.20 2016Aavid Thermacore Proprietary & Confidential
Example Heat Exchanger Specs1U Server Heat ExchangerDesktop Heat ExchangerHEX Spec. β 1U Server ChassisHEX Spec. β Desktop cation Specific: 150mm shownTypical: 100 -150mmLengthApplication Specific: 130mm shownTypical: 100 β 275 mmHeightApplication Specific: 150mm shownTypical: 100 -150mmHeightApplication Specific: 40 mm shownTypical: 30 - 50mmDepth25mmDepth25mmMassApplication Specific: 350 gramsTypical: 250 -350mmMassApplication Specific: 85 gramsTypical: 85 -150mmAavid Thermacore, Inc. All Rights Reserved.21 2016Aavid Thermacore Proprietary & Confidential
Liquid Pump SpecsCompact Form Factor PumpPump Spec. β 1U Server ChassisPump Spec.FlowrateAcoustic PowerDimensions 0.25gpm @3.6 psi headTarget 3.3 BA62 mm W x 38mm H x87mm L w/ barbsFlowrateAcoustic PowerDimensions 0.125 gpm @ 3psi headTarget 3.3 BA32 mm W x 32mm H x 89mm LMass200 gramsMass135 gramsPower12WPower10WVoltage/Amps12Vdc / 1A continuousAavid Thermacore, Inc. All Rights Reserved.22 2016Aavid Thermacore Proprietary & ConfidentialVoltage/Amps12Vdc / 0.6A continuous
Liquid Cooled System for MilitaryApplications 2016AavidThermacore,Inc. AllRightsSince 1970 AS9100 ISO 9001ISO14001Reserved.Certified ITAR RegisteredAavid Thermacore Proprietary & ConfidentialQF 402 Rev E
System Requirements Military applications have much tighter and controlled requirementscompared to computing liquid cooled systems. Subject to MIL specs.Extreme temperature ranges (-55oC to 70oC).Extreme environmental conditions.Air-tight enclosures.Low accessibility for servicing.Shock and vibration requirements.Feedback controllers for optimized heat removal in any conditions.Multiple sensors to monitor faults in the system.Redundant elements are generally required. In airborne applications, low weight materials need to be used, (i.e.aluminum), which have worse thermal conductivity than copper. Thermal path from the electronics to the heat exchanger is critical toreduce thermal resistance.Aavid Thermacore, Inc. All Rights Reserved.24 2016Aavid Thermacore Proprietary & Confidential
LCS Flow DiagramPumpsHX with chilledwaterReservoirHeater3-way temp.controlled valveFilterAntennaPurge LineAavid Thermacore, Inc. All Rights Reserved.25 2016Aavid Thermacore Proprietary & ConfidentialStrainer
Intelligent Thermal Management System (iTMS) Application: Airborne Mapping & Imaging Laser Diode Cooling Power: 1.1kW Thermal TechnologiesTECβsHeat Pipe Cold PlateAl Vacuum Brazed Cold PlatesPumped Liquid CoolingSub-ambient CoolingSophisticated Control SystemAavid Thermacore, Inc. All Rights Reserved.26 2016Aavid Thermacore Proprietary & Confidential
Intelligent Thermal Management System (iTMS)Internal HeatExchangerExternal HeatExchangerCold PlatesHeat PipeAssyβs Application:Rugged, Liquid CoolingSystem (rLCS) Ruggedized Electronics Cooling Thermal Load/Power: 1 kW Designed / Tested to MIL Specs. Cooling System includes: Heat pipesLiquid-cooled cold platesInternal brazed aluminum liquid-to-air heat exchangerDip brazed aluminum cold platesAn external brazed aluminum liquid-to-air heatexchangerAavid Thermacore, Inc. All Rights Reserved.27 2016Aavid Thermacore Proprietary & ConfidentialRedundant Pumps Sealed air-tight chassis Upgradeable Electronics
Intelligent Thermal Management System (iTMS) Application Airborne Computer Cooling Dissipates thermal load into ambient air at 75k feet Primary Components Vacuum Brazed Aluminum HXsVibration Isolation (40G operational)Brushless DC PumpsPTFE HosesCustom Machined Chassis & ReservoirCustom Motor Control Key Features Sub Ambient CoolingPID temperature controlConditioning heaters to facilitate rapid βcold startβLiquid level sensorsFault Tolerance/Safety flow switch provides visualand electrical confirmation of coolant flowPLC control of pumps, heaters, valves, etc.LED status indicatorsData loggingColor touchscreen display/interface panelShock Mounted for Vibration IsolationAavid Thermacore, Inc. All Rights Reserved.28 2016Aavid Thermacore Proprietary & Confidential
Summary Liquid cooling is a necessary technology applied incases where power densities are too high to bemanaged by traditional air cooling. Liquid heat transport capabilities are far much greater thanair. Liquid cooled systems can be simple but in someapplications can have very complex architecture. Basic elements: pump, cold plate, heat exchanger, liquidline. Total pressure head is necessary to be estimated toproperly size a pump. Static head, difference in elevation. Frictional head losses calculated using known documentedfriction factors.Aavid Thermacore, Inc. All Rights Reserved.29 2016Aavid Thermacore Proprietary & Confidential
Summary Heat balance equation and heat rate equation areused in sizing a heat exchanger. Necessary to know fin area and flow rate to dissipate theheat. Selection of liquid will depend on application andmaterials used in the system. Computing liquid cooled applications donβt requirestrict requirements compared to military applications. Redundant systems, extreme temperatures, shock andvibrations, etc Aavid Thermacore, Inc. All Rights Reserved.30 2016Aavid Thermacore Proprietary & Confidential
Air cooling is limited by specific heat. To dissipate large amounts of power, a large mass flow rate is needed. Higher flow speed, larger noise. Liquid cooling is able to achieve better heat transfer at much lower mass flow rates. Lower flow speed, lower noise. Heat transfer coefficients for air an liquid flows are orders of .