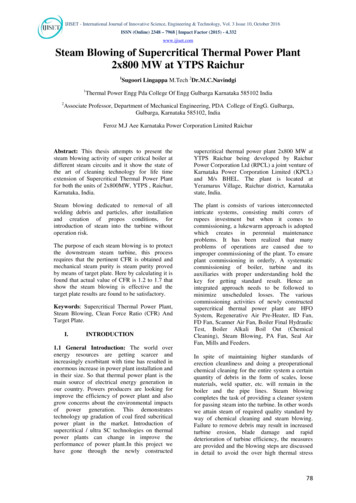
Transcription
IJISET - International Journal of Innovative Science, Engineering & Technology, Vol. 3 Issue 10, October 2016ISSN (Online) 2348 – 7968 Impact Factor (2015) - 4.332www.ijiset.comSteam Blowing of Supercritical Thermal Power Plant2x800 MW at YTPS Raichur1PSugoori Lingappa M.Tech 2Dr.M.C.NavindgiPPP1PThermal Power Engg Pda College Of Engg Gulbarga Karnataka 585102 IndiaP2PAssociate Professor, Department of Mechanical Engineering, PDA College of EngG. Gulbarga,Gulbarga, Karnataka 585102, IndiaPFeroz M.J Aee Karnataka Power Corporation Limited RaichurAbstract: This thesis attempts to present thesteam blowing activity of super critical boiler atdifferent steam circuits and it show the state ofthe art of cleaning technology for life timeextension of Supercritical Thermal Power Plantfor both the units of 2x800MW, YTPS , Raichur,Karnataka, India.supercritical thermal power plant 2x800 MW atYTPS Raichur being developed by RaichurPower Corporation Ltd (RPCL) a joint venture ofKarnataka Power Corporation Limited (KPCL)and M/s BHEL. The plant is located atYeramarus Village, Raichur district, Karnatakastate, India.Steam blowing dedicated to removal of allwelding debris and particles, after installationand creation of propos conditions, forintroduction of steam into the turbine withoutoperation risk.The plant is consists of various interconnectedintricate systems, consisting multi corers ofrupees investment but when it comes tocommissioning, a lukewarm approach is adoptedwhich creates in perennial maintenanceproblems. It has been realized that manyproblems of operations are caused due toimproper commissioning of the plant. To ensureplant commissioning in orderly, A systematiccommissioning of boiler, turbine and itsauxiliaries with proper understanding hold thekey for getting standard result. Hence anintegrated approach needs to be followed tominimize unscheduled losses. The variouscommissioning activities of newly constructedsupercritical thermal power plant are HFOSystem, Regenerative Air Pre-Heater, ID Fan,FD Fan, Scanner Air Fan, Boiler Final HydraulicTest, Boiler Alkali Boil Out (ChemicalCleaning), Steam Blowing, PA Fan, Seal AirFan, Mills and Feeders.The purpose of each steam blowing is to protectthe downstream steam turbine, this processrequires that the pertinent CFR is obtained andmechanical steam purity is steam purity provedby means of target plate. Here by calculating it isfound that actual value of CFR is 1.2 to 1.7 thatshow the steam blowing is effective and thetarget plate results are found to be satisfactory.Keywords: Supercritical Thermal Power Plant,Steam Blowing, Clean Force Ratio (CFR) AndTarget Plate.I.INTRODUCTION1.1 General Introduction: The world overenergy resources are getting scarcer andincreasingly exorbitant with time has resulted inenormous increase in power plant installation andin their size. So that thermal power plant is themain source of electrical energy generation inour country. Powers producers are looking forimprove the efficiency of power plant and alsogrow concerns about the environmental impactsof power generation. This demonstratestechnology up gradation of coal fired subcriticalpower plant in the market. Introduction ofsupercritical / ultra SC technologies on thermalpower plants can change in improve theperformance of power plant.In this project wehave gone through the newly constructedIn spite of maintaining higher standards oferection cleanliness and doing a preoperationalchemical cleaning for the entire system a certainquantity of debris in the form of scales, loosematerials, weld spatter, etc. will remain in theboiler and the pipe lines. Steam blowingcompletes the task of providing a cleaner systemfor passing steam into the turbine. In other wordswe attain steam of required quality standard byway of chemical cleaning and steam blowing.Failure to remove debris may result in increasedturbine erosion, blade damage and rapiddeterioration of turbine efficiency, the measuresare provided and the blowing steps are discussedin detail to avoid the over high thermal stress78
IJISET - International Journal of Innovative Science, Engineering & Technology, Vol. 3 Issue 10, October 2016ISSN (Online) 2348 – 7968 Impact Factor (2015) - 4.332www.ijiset.comamong the temporary pipes and some issuesduring blowing are also analyzed, which could behelpful and referenced for the similar units.1.2 Scope of the project: Keeping in view of theabove mentioned scenario, the commissioningactivity at YTPS is conducted; the present workis steam blowing of newly constructed plant. Thefollowing are included in the scope of the presentwork.1) Discharge of loose particles such as rust, scale,sand, and to certain extent, also largeforeign matter to this end high steam velocitiesare required.2) Thermal Shock induced exfoliation ofadhesive deposits.The steam blowing will only be effective if it isdone at higher steam velocities than thoseprevailing during full load operation. The resultof steam blowing or final criteria is checked bymeans of a target plate consist of a holdingfixture to which a mirror finish stainless steelplate with a specified size of minimum indents.Steam blowing results can only be expected if theprocess and steam parameter involved with thisrelevant data such as,1. CFR (clean force ratio)2. Steam pressure and temperature3. Steam mass flow rate4. Specific Volume5. Target plate dents result.Pressure reduction and number of bursts persteam blow up operation. In this thesis a detailedstudy on steam blowing and its parameter iscarried out.1.3 Plant details: The steam generator is a oncethrough super critical type (ALSTOM MAKEBOILER). The circuit which are subjected tosteam blowing are super heater section of boiler,main steam line up to HP turbine, cold re-heater,hot re-heater line up to IP turbine, HP and LP bypass line. Predicted performance data of 800MWplant are as follows,1. Steam flow (SH O/L BMCR) – 2592 TPH2. Steam flow (RH O/L) – 2069 TPH3. Feed water I/L temperature – 294 C4. MCR Steam I/L pressure to SH – 250 bar5. MCR Steam I/L pressure to RH – 60 bar.1.4 Statement of the project: The statement ofthe project is steam blowing activity ofsupercritical thermal power plant 2x800 MW atYTPS Raichur. Steam blowing is one of theimportant commissioning activities at boiler andturbine side of thermal power plant, steamblowing allows boilers and pipelines to ensurethat during normal operation no adheringmaterial in the superheaters, re-heaters and steampipelines will become dislodged to reach theturbine blades and damage them. The steamblowing operation cleans the system andprovided the steam of requisite purity for theplant.1.5 Objective of the Project: The objective ofsteam blowing project is to remove scales, loosematerial, iron cuttings, weld spatter etc, thatmight have been entrapped in super heaters,steam piping, re-heaters during manufacture,storage, erection at site. Failure to remove thedebris may result in damage to turbine blades,valves etc.1.6 Limitation of the project: The datacollected for M/s BHEL and KPCL are fromSecondary Sources and presentations given bythe company at different places. But completeand up to date data was not available as most ofthem are related to trade secret of thesecompanies and volatile in nature. The law ofprotection of confidential information effectivelyallows a perpetual monopoly in secretinformation. So that information can’t be sharedthrough the report.II. LITERATURE SURVEYMartin Herberg, Dr. Eng. Zoran Micevic.,(2014): This article shows the state of the art ofcleaning technology for modernization andreconstruction of large Thermal Power. Thechosen combination of chemical cleaning andsteam blowing assured the best possible cleaningresult and an optimal time schedule to theproject. Chemical cleaning was dedicated toremove iron oxides and all mineral. Steamblowing was dedicated to removal of allremaining after installation and creation ofproper conditions for introduction of steam intoturbine without operational risk. The approach toproject were as follows Orders integration avoidscoordination problems, short rebuilding phasesbetween chemical clean and steam blow, use oftemporary steam blow pipes for execution ofchemical cleaning, use of same equipment forchemical cleaning and steam blow, temporarysteam blow pipes are already cleaned up to thetarget [1].J.B. Pier and G. Goldman., (1990): Studiedshown that compressed air blows may be themost effective and economical approach tocleaning main steam lines. Benefits are flexiblescheduling because air-blows can be worked intothe start-up schedule without affecting othermajor critical path activities, except for work onthe boiler and steam-line pressure parts. Balanceof plant equipment associated with the boiler and79
IJISET - International Journal of Innovative Science, Engineering & Technology, Vol. 3 Issue 10, October 2016ISSN (Online) 2348 – 7968 Impact Factor (2015) - 4.332www.ijiset.comboiler auxiliary systems must be completed andchecked before steam blowing is possible, reducemanpower, time, fuel and cost, extends boiler lifeby eliminating temperature cycles in the boilerassociated with steam blows. In all cases thesuper-heater, re-heater, and main steam pipingwere cleaned with compressed air [2].III.SUPER CRITICAL THERMAL POWERSTATION3.1. Super critical power generation: The heatenergy is produced by fuel combustion is used totransform the boiler feed water into superheatedsteam. The steam of high temperature andpressure is then fed through turbines to producemechanical power which in turn drives anelectric generator to produce electricity. Theexhausted steam which can no longer drive theturbines is finally condensed into liquid throughthe condenser before it is re-circulated back tothe boiler thereby completing the cycle this isknown as Rankine cycle. SC is a thermodynamicexpression describing state of substance wherethere is no clear distinction between the criticaland gaseous phase. Water reaches this phase at apressure above around 221 bar and temperature374.15 C. In addition there is no surface tensionin a SC fluid as there is no boundary betweenliquid and gas phase. By changing the pressureand temperature of the fluid, the properties canbe “tuned” to be more liquid- or more gas like.Carbon dioxide and water are the mostcommonly used SC fluids, being used .2. Supercritical technologyThe SC technology in India is in itsnascent stage as compared to the USA, which isone of the world’s leading electricity generator.If we compare the per capita energy or electricityavailability in India which is 6419.30 KWh andthe world’s average then it is found to be a verysmall fraction of that. The India has laid moreemphasis on the efficiency improvement of thepower plant through advanced technology likethe SCl Technology. The meaning of SC issubject to interpretation. Depending on upperlimit of pressure and temperature parameters, thissystem is generally categorized as SC, and thereare further developed such as ultra-supercriticaland advanced ultra-supercritical as indicatedbelow SC is a thermal cycle with main steamtemperature between 565 to 593 C operating atpressures between 221.18 and 275 bar.Fig 3.2: SC steam cycle temperature v/s entropyWhere,1 - 2 CEP work2 – 2s Regeneration2s - 3 Boiler superheating3 – 4 HPT expansion4 – 5 Reheating5 – 6 IPT &LPT expansion6 – 1 Condenser Heat rejection.3.9. Introduction to steam blowing: In spite ofmaintaining higher standards of erectioncleanliness and doing a pre-operational chemicalcleaning for the entire system or part there off, acertain quantity of debris in the form of scales,loose materials, weld spatter, etc. Will remain inthe boiler and the pipe lines. While chemicalcleaning ensures cleanliness of the contourssubjected to the cleaning resulting in surfacecleaning and collection of loose materials, loosematerials collected are to be removed effectively.Subsequent steam blowing completes the task ofproviding a cleaner system for passing steam intothe turbine. In other words we attain steam intothe turbine. In other words we attain steam ofrequired quality standard by way of chemicalcleaning and steam blowing. Failure to removedebris may result in increased turbine erosion,blade damage and rapid deterioration of turbineefficiency.3.10. Principle of steam blowing: Steamblowing is carried out by adopting puffingmethod. It is performed by raising the boilerpressure 60 bar and releasing the steam through aquick opening valve. This technique gives athermal shock to the contours being purged. Thisresults in loosening of the adhered scale which issubsequently removed by expanding steam. Thesteam generator and turbine manufactures, pipingsystems suppliers, and the operator must reachjoint decision on the type of cleaning method, thecriteria for evaluation of cleanliness and therequired degree of cleanliness.80
IJISET - International Journal of Innovative Science, Engineering & Technology, Vol. 3 Issue 10, October 2016ISSN (Online) 2348 – 7968 Impact Factor (2015) - 4.332www.ijiset.com3.11. Steam blowing of power stationpipelines: Steam blowing allows power stationboilers and pipelines to ensure that during normaloperation no adhering material in the superheaters, re-heaters, and steam pipelines willbecome dislodged, reach the turbine blades, anddamage them. Puffing and continuous methodsare mainly used for steam blowing.3.12 Definition of steam blowing: The blowingof steam through piping to remove debris fromthe pipe, cleaning steam lines to a steam turbine,cleaning plant expansion lines, or new installs.As the definition says, to steam blow a piperequires steam to blow through the pipe. Thispipe can be attached to a boiler and the other endof the pipe can be attached to a steam turbine.3.13. Why steaming blowing is done: Thesteam blowing operation cleans all the debris inthe super-heater, re-heater and the st
steam blowing are super heater section of boiler, main steam line up to HP turbine, cold re-heater, hot re-heater line up to IP turbine, HP and LP by pass line. Predicted performance data of 800MW plant are as follows, 1. Steam flow (SH O/L BMCR) – 2592 TPH 2. Steam flow (RH O/L) – 2069 TPH 3. Feed water I/L temperature – 294 C 4. MCR Steam I/L pressure to SH – 250 bar 5. MCR Steam I .