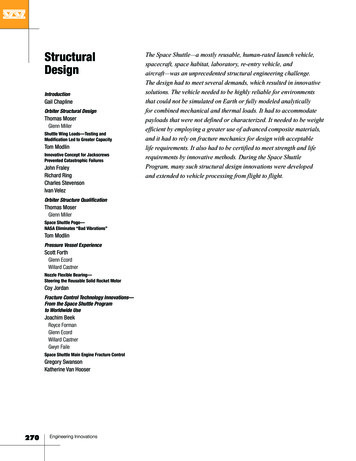
Transcription
StructuralDesignIntroductionGail ChaplineOrbiter Structural DesignThomas MoserGlenn MillerShuttle Wing Loads—Testing andModification Led to Greater CapacityTom ModlinInnovative Concept for JackscrewsPrevented Catastrophic FailuresJohn FraleyRichard RingCharles StevensonIvan VelezOrbiter Structure QualificationThomas MoserGlenn MillerSpace Shuttle Pogo—NASA Eliminates “Bad Vibrations”Tom ModlinPressure Vessel ExperienceScott ForthGlenn EcordWillard CastnerNozzle Flexible Bearing—Steering the Reusable Solid Rocket MotorCoy JordanFracture Control Technology Innovations—From the Space Shuttle Programto Worldwide UseJoachim BeekRoyce FormanGlenn EcordWillard CastnerGwyn FaileSpace Shuttle Main Engine Fracture ControlGregory SwansonKatherine Van Hooser270Engineering InnovationsThe Space Shuttle—a mostly reusable, human-rated launch vehicle,spacecraft, space habitat, laboratory, re-entry vehicle, andaircraft—was an unprecedented structural engineering challenge.The design had to meet several demands, which resulted in innovativesolutions. The vehicle needed to be highly reliable for environmentsthat could not be simulated on Earth or fully modeled analyticallyfor combined mechanical and thermal loads. It had to accommodatepayloads that were not defined or characterized. It needed to be weightefficient by employing a greater use of advanced composite materials,and it had to rely on fracture mechanics for design with acceptablelife requirements. It also had to be certified to meet strength and liferequirements by innovative methods. During the Space ShuttleProgram, many such structural design innovations were developedand extended to vehicle processing from flight to flight.
Orbiter StructuralDesignNASA faced several challenges inthe structural design of the Orbiter.These challenges were greaterthan those of any previous aircraft,launch vehicle, or spacecraft, and theOrbiter was all three. Yet, the spaceagency proceeded with tenacity andconfidence, and ultimately reached itsgoals. In fact, 30 years of successfulshuttle flights validated the agency’sunique and innovative approaches,processes, and decisions regardingcharacteristics of design.A few of the more significantchallenges NASA faced in Orbiterstructural design included the evolutionof design loads. The Orbiter structurewas designed to an early set of loadsand conditions and certified to a laterset. The shuttle achieved first-flightreadiness through a series of localizedstructural modifications and operationalflight constraints. During the earlydesign phase, computer analyses usingcomplex calculations like finite-elementmodels and techniques for combinedthermal and mechanical loads were notpossible. Later advances in analyticalmethods, coupled with test data,allowed significant reductions in bothscope and cost of Orbiter structuralcertification. The space agency had toface other challenges. Structuralefficiency had to be compromisedto assure versatile payload attachmentand payload bay door operations.Skin buckling had to be avoided toassure compatibility with thelow-strength Thermal ProtectionSystem tiles. Composite materialsbeyond the state of the art were needed.The crew compartment had to beplaced into the airframe such that thepressurized volume would effectively“float.” And it was impractical totest the full airframe under combinedmechanical and thermal loads.Thousands of analytical design loadsand conditions were proven acceptablewith flight data with one exception:the ascent wing loads were greaterthan predicted because of the effectthe rocket exhaust plume had on theaerodynamic pressure distribution.As a result, early flights were flownwithin limited flight regimes to assurethat the structural capability of thewings was not exceeded. The wingswere later “strengthened” with minorchanges in the design and weight.Shuttle Wing Loads—Testing andModification Led to Greater CapacityOrbiter wing loads demonstrated the importance of anchoring the prediction orgrounding the analysis with flight data in assuring a successful flight. The right wingof Columbia was instrumented with strain gauges for the test flights and wasload-calibrated to verify the in-flight air load distribution. The wing was alsoinstrumented with pressure gauges; however, the number was limited due toon-board recorder space limitations. This resulted in the need to obtain additionalpressure data.Space Transportation System (STS)-1 (1981) data indicated higher shear in the aftspar web than was predicted. NASA conducted analyses to determine the location andmagnitude of forces causing this condition. The results indicated an additional loadalong the outboard wing leading edge (elevon hinge line). Data obtained on STS-2(1981) through STS-4 (1982) substantiated these results. This caused concern for theoperational wing limits that were to be imposed after the flight test period.The additional load caused higher bending and torsion on the wing structure,exceeding design limits. The flight limits, in terms of angle of attack and sideslip,would have to be restricted with an attendant reduction in performance.The recovery plan resulted in modification to the wing leading edge fittings. The majorimpact was to the structure between the upper and lower wing skins, which weregraphite-epoxy. These required angle stiffeners on each flat to increase the bucklingstress. The weight of the modifications resulted in a loss of performance. The resultingflight envelope was slightly larger than the original when accounting for the negativeangle-of-attack region of the flight regime.Engineering Innovations271
Payload Access and StructuralAttachments—Mid-Fuselageand Payload Bay DoorsNASA designed the mid-fuselage ofthe Orbiter to be “flexible” so as toaccommodate the closing of payloadbay doors in space. The design also hadto accommodate a wide range ofpayload sizes, weights, and number.Typical Payload Attachment SchemePrimary FittingLatchGear MotorBridge Pin3 PayloadSill LongeronThe payload bay doors were an integralpart of the fuselage structure. Theclassical structural design would havethe doors provide strength when thefuselage encountered loads frombending, twisting, shear, internalpressure, and thermal gradients. Thedoors also had to open in space toprovide access to the payload andenable the radiators to radiate heat tospace. Equally important, the doors hadto close prior to re-entry into Earth’satmosphere to provide aerodynamicshape and thermal protection.To balance the functional and strengthrequirements, engineers designed thedoors to be flexible. The flexibilityand zipper-like closing ensured thatthe doors would close in orbit even ifdistorted thermally or by changes inthe gravity environment (from Earthgravity to microgravity). If the latchesdid not fully engage, the doors couldnot be relied on to provide strengthduring re-entry for fuselage bending,torsion, and aerodynamic pressure.Thus, the classical design approachfor ascent was not possible for re-entry.The bulkheads at each end of thepayload section and the longerons oneach side required additional strength.To reduce weight and thermal distortion,engineers designed the doors usinggraphite epoxy. This was the largestcomposite structure on any aircraft orspacecraft at the time.272Engineering InnovationsBridgeFittingMain FramePrimaryFittingsX and Z LoadsStabilizerFittingZ LoadsPayload Bay DoorsKeel FittingY LoadsSets of moveable attachment fittings on the longerons and frames accommodatedmultiple payloads. The Monte Carlo analyses of the full spectrum of payload quantities,sizes, mass properties, and locations determined the mid-fuselage design loads.These design loads were enveloped based on a combination of 10 million load cases.Decoupling the design of the mid-fuselage and payloads enabled a timely design of both.The mid-fuselage had to accommodatethe quantity, size, weight, location,stiffness, and limitations of known andunknown payloads. An innovativedesign approach needed to provide astatically determinant attachment systembetween the payloads and mid-fuselage.This would decouple the bending,twisting, and shear loads between thetwo structures, thus enabling engineersto design both without knowing thestiffness characteristic of each.Designing to MinimizeLocal DeflectionsThe Orbiter skin was covered with morethan 30,000 silica tiles to withstand theheat of re-entry. These tiles had alimited capacity to accommodatestructural deflections from thermalgradients. The European supersonicConcorde passenger aircraft (first flownin 1969 and in service from 1976 to2003) and the SR-71 US military
aircraft encountered significant thermalgradients during flight. The designapproach in each was to reduce stressesinduced by the thermal gradients byenabling expansion of selected regionsof the structure; e.g., corrugatedwing skins for the SR-71 and “slots”in the Concorde fuselage. Afterconsulting with the designers of bothaircraft, NASA concluded that theOrbiter design should account forthermally induced stresses but resistlarge expansions and associated skinbuckling. This brute-force approachprotected the attached silica tile aswell as simplified the design andmanufacture of the Orbiter airframe.NASA developed these designcriteria so that if the thermal stressesreduced the mechanical stresses, thereductions would not be considered inthe combined stress calculations.To determine the thermally inducedstresses, NASA establisheddeterministic temperatures for eightinitial temperature conditions on theOrbiter at the time of re-entry as wellOrbiter Thermal Stress Analysis ModelingCourse Grid ElementComputer-derived ib CapStructural Element withConsiderably Fewer NodesLocalized Thermal Math Modelas at several times during re-entry.Engineers generated 120 thermalmath models for specific regions ofthe Orbiter. Temperatures wereextrapolated and interpolated to nodeswithin these thermal math models.Use of UniqueAdvanced MaterialsEven though the Orbiter was a uniqueaircraft and spacecraft, NASA selected aconventional aircraft skin/stringer/framedesign approach. The space agencyalso used conventional aircraft material(i.e., aluminum) for the primarystructure, with exceptions in selectedregions where the use of advancedstate-of-the-art composites increasedefficiency due to their lower density,minimum thermal expansion, or highermodulus of elasticity.Other exceptions to the highlyreliable conventional structures werethe graphite-epoxy OrbitalManeuvering System skins, whichwere part of a honeycomb sandwichstructure. These graphite honeycombstructures had a vented core torelieve pressure differentials acrossthe face sheets during flight. Theyalso required a humidity-controlledenvironment while on the groundto prevent moisture buildup in thecore. Such a buildup could become asource of steam during the highertemperature regimes of flight. Finally,during the weight-savings programinstituted on Discovery, Atlantis, andEndeavour, engineers replaced thealuminum spar webs in the wing witha graphite/epoxy laminate.Large doors, located on the bottom ofthe Orbiter, were made out of beryllium.These doors closed over the ExternalTank umbilical cavity once the vehicleEngineering Innovations273
Early Trade Studies Showed CostBenefits That Guided Materials SelectionTitanium offered advantages for the primary structure because of higher temperaturecapability—315 C vs. 177 C (600 F vs. 350 F). When engineers considered thecombined mass of the structure and Thermal Protection System, however, they noted aless than 10% difference. The titanium design cost was 2.5 times greater. The schedulerisk was also greater. NASA considered other combinations of materials for the primarystructure and Thermal Protection System and conducted a unit cost comparison. Thisstudy helped guide the final selections and areas for future development.Orbiter Structure/Thermal Protection System First Unit Cost ComparisonWeight(kg x 103)(lb x 103)3680Cost( M)Weights32706027605023504030Costs20101234Thermal Protection System56Structure789Weight of Structure Thermal Protection System1—Aluminum Alloy 7075-T6 Structure, Ablator Thermal Protection System2—Aluminum Alloy 7075-T6 Structure, Reusable Thermal Protection System LI-1500(Lockheed-produced tiles)3—Aluminum Alloy 2024-T81 Structure, Reusable Thermal Protection System LI-15004—Aluminum Alloy 7075-T6, Reusable Thermal Protection System on Beryllium Panels5—Magnesium Alloy HM21A-T8 Structure, Reusable Thermal Protection System LI-15006—Aluminum Alloy 7075-T6, Metallic Inconel Thermal Protection System7—Combination Aluminum and Titanium Alloys Structure, Reusable ThermalProtection System LI-15008—Beryllium and Titanium Alloys Structure, Reusable Thermal Protection System LI-15009—Titanium Alloy 6Al-4V Structure, Reusable Thermal Protection System LI-1500was on orbit. These approximately1.3-m (50-in.) square doors maintainedthe out-of-plane deflection to less than274Engineering Innovations20 mm (0.8 in.) to avoid contact withadjacent tiles. They also had the abilityto withstand a 260 C (500 F)environment generated by ascentheating. The beryllium materialallowed the doors to be relativelylightweight and very stiff, and toperform well at elevated temperatures.The superior thermal performanceallowed the door, which measured25.4 mm (1 in.) in thickness, to flywithout internal insulation duringlaunch. Since beryllium can beextremely toxic, special proceduresapplied to those working in its vicinity.The truss structure that supportedthe three Space Shuttle Main Engineswas stiff and capable of reacting toover a million pounds of thrust.The 28 members that made up thethrust structure were machined fromdiffusion-bonded titanium. Titaniumstrips were placed in an inertenvironment and bonded togetherunder heat, pressure, and time. Thisfused the titanium strips into a single,hollow, homogeneous mass. To increasethe stiffness, engineers bonded laye
frames as stabilizing elements. Technicians bonded these composite tubes to titanium end fittings and saved approximately 139 kg (305 pounds) over a conventional aluminum tube design. During ground operations, however, composite tubes in high traffic areas were repeatedly damaged and were eventually replaced with an aluminum design to increase robustness