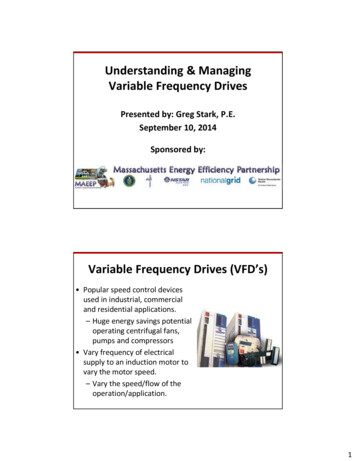
Transcription
Understanding & ManagingVariable Frequency DrivesPresented by: Greg Stark, P.E.September 10, 2014Sponsored by:Variable Frequency Drives (VFD’s) Popular speed control devicesused in industrial, commercialand residential applications.– Huge energy savings potentialoperating centrifugal fans,pumps and compressors Vary frequency of electricalsupply to an induction motor tovary the motor speed.– Vary the speed/flow of theoperation/application.1
VFD Applications Industrial– Fans, Pumps, Compressors– Conveying Systems Commercial– HVAC Compressors– Pumps and Air Handlers Residential– Variable Speed HVAC equipment– Energy Efficient Washing MachinesHow Have We Varied Speed Historically? Change Speed––––Belts & pulleysChains & sprocketsGear drivesMulti-speed motors Vary Speed––––––Variable pitch belts & pulleysEddy current clutchHydrostatic drivesWound rotor motorDC DrivesAC Variable Frequency Drives2
How Have We Varied Flow Historically?Typical Airflow Requirements60005000CFM Size motor/systemfor maximum flow Use throttlingdevices on fans,pumps &compressors toreduce flow h– Valves– Vanes & DampersConsiderations? Initial Cost– VFD vs other device Maintenance Cost– VFD vs other device Maintenance Issues(Downtime, etc) Effectiveness– How well does it do what Ireally want/need it to do? Others?3
Induction Motor Constant Speed? Synchronous Speed– Speed the motor’s magnetic field rotates.– Theoretical speed with no torque or friction.– A well built motor may approach synchronousspeed when it has no load.– Factors Electrical Frequency (cycles/second) # of poles in motorSpeed (120 * Frequency)/(# of poles) Rated Speed– Speed the motor runs at when fully loaded andsupplied rated nameplate voltage.VFD Principles of Operation Motor speed can be varied by changing the frequency, # ofpoles, or both. Example:– 4 pole motor @ 60 hertz 1800 rpm– 4 pole motor @ 50 hertz 1500 rpm– 4 pole motor @ 40 hertz 1200 rpm4
Drive Function Input:– 60 hertz AC & rated voltage Converter– Rectifies to DC & changesfrequency to desired value Inverter– Converts DC back to AC Regulator– Adjusts voltage level to desiredvalue as a % of speed/frequencyvalue.– Volts/Hertz Ratio (480/60 8) AC Output:– Desired frequency and voltagefor speed requirement.Torque vs Speed What happens to torque whenspeed is decreased?– Torque increases If torque increases, currentincreases and producesadditional heat in the windings.5
However!!!! For many types of loads, asspeed drops, torquerequirements also drop. What happens when speedAND torque decrease?– Reduced Horsepower Reduces our energy costs!Increase Speed? What about increasing speed above themotor’s synchronous speed usingfrequency higher than 60 hertz?– 4 pole motor @ 60 hertz 1800 rpm– 4 pole motor @ 70 hertz 2100 rpm Most motors were not balanced tooperate above synchronous speed. The load may not have been balancedabove this speed either.6
Common Applications Constant Torque Loads– conveyor belts, augers,reciprocating pumps &compressors, extruders,gear pumps. Variable Torque Loads– centrifugal fans, pumps,and compressors Constant HorsepowerLoads– winding machinesTorque-Speed Curve Amount of Torqueproduced by motorsvaries with Speed. Torque Speed Curves– Starting Torque– Pull Up Torque– Breakdown Torque7
Torque-Speed Issues Some single phasemotors have startingand running windings The starting windingscan not be energizedcontinuously If a VFD is used andspeed is reduced toomuch the startingwindings burn out.Constant Torque Loads Require the same amount oftorque at low speeds as highspeeds.– For a given weight on the belt, thetorque to turn the belt is alwaysthe same regardless of speed. Horsepower increases ordecreases as a direct function ofspeed. Examples:– Conveyor belts, reciprocatingpumps & compressors8
Constant Torque Loads Horsepower increases ordecreases as a direct functionof speed.– A 50% drop in speed produces a50% reduction in power required toturn the load. Energy savings using a VFD tocontrol the speed of aconstant torque load is adirect function of speedreduction.Variable Torque Loads Require much lower torque &horsepower at low speeds than athigh speeds. Power required varies as the cubeof the speed. Examples:– Centrifugal fans, pumps &compressors, mixers and agitators.9
Variable Torque Loads Horsepower increases ordecreases as cubic function ofspeed.– A 50% drop in speed producesalmost an 88% reduction in powerrequired to turn the load. Energy savings using a VFD tocontrol the speed of avariable torque load can bevery large due to howcentrifugal loads operate.Constant Horsepower Loads Constant horsepower loadsinclude equipment such asgrinders, winders, and lathes.– Since the power requiredremains the same regardless oftorque or speed requirements ofthe operation, there are no directenergy savings from installingVFD's with constant horsepowerloads.10
Constant Horsepower Loads Traditionally considered DCDrive applications Some movement to use ofnewer AC Flux Vector Drives The only justification forinstallation of an VFD wouldbe based on improvement inthe process control of theoperation.Advantage: Energy Savings Traditionally used to justifyinstallation. Centrifugal Fans, Pumps,Compressors– As the speed of thedevice is slowed, thetorque and powerrequired to run theoperations is significantlyreduced.11
Throttling Flow May Not Save Energy Traditional methods ofreducing flow by throttling(dampers, vanes, valves) don’tconsistently provide energysavings. Depending on where thesystem is on the pump curve,reducing flow has the result ofincreasing pressure on theback side of the pump andchanging the pump efficiency.Energy Savings With VFDs Using a VFD can result insignificant energy savings whenthrottling flow for centrifugal fans,pumps and compressors. The reduction in flow and pressurein the system from controllingflow with fan/pump speed willresult in a decrease in powerrequired to turn the deviceresulting in energy savings at thereduced flow rate.12
VFD’s Increase Power Factor Power Factor Penalties can bea part of commercial andindustrial electric bills VFD’s have two types of powerfactor– Total Power Factor– Displacement Power Factor Utilities measure displacementpower factor so a VFD canimprove power factor of asystem without addingcapacitorsAdvantage: Reduced Voltage Starting An VFD acts like a reducedvoltage starter to limit the inrush current when the motorstarts. VFD’s can generally limit inrush current to a maximum of150% of a motors FLA/RLA ifdesired.– What is the downside of limitingstarting amps?13
Why Reduced Voltage (Soft) Starting Reduce motor in-rushcurrent and the associatedvoltage drop when startingthe motor for power qualitybenefits.– Can cause nuisance tripping ofsensitive electronicequipment. Reduce mechanical shock toproducts and drive systemsduring startup.Advantaged: Improved Process Control Can be linked intoprocess control systemsto provide feedback toDCS and PLC’s. More consistent controlof manufacturingoperation.– Better dissolvedoxygen control?14
Advantage: Lower System Maintenance Eliminate need for maintenanceitems in some system. Extend operating life ofequipment that is occasionallyoverloaded and the system isnot optimized. Reduces motor cycling andassociated driveline shock insome systems.Can Eliminate Some MaintenanceRequirements May eliminate theneed for complexbelt, gearboxes,valve and dampersystems and theassociatedmaintenancerequirements.15
Maintenance: ReducedShort Cycling Frequently starting andstopping motors cansignificantly reduce theiroperating life. A VFD can reduce inputflow rate so that pumpsdo not have to befrequently started andstopped.VFD Maintenance Drives are similar to a powersupply & computer– Keep it Clean– Keep it Dry– Keep connections Tight NEMA 1 or NEMA 12 are themost common enclosures– NEMA 1 dust and moistureissues occasionally are an issue16
Advantage: Bypass Capability If there is a problem with the drive, it can be bypassedeasily and the motor operated without the drive.(Although without speed control)Advantage: Multi-Motor Control Some VFD’s cancontrol multiplemotors from the samedrive. Reduces sizerequirements and theinitial cost.17
Advantage: Phase Conversion VFD’s can be used to operate 3-phasemotors from single phase powersupplies. Motor starting currents of 150%producing full torque starts up to 125Hp Issues:– Cost of VFD vs Phase Converter– Drive is 95% efficient– Need for Reduced Voltage Start?– Eliminates need for “Pump Panel”– Multi-motor control (center pivot)– * Harmonic output is usuallyhigher when used single phaseDisadvantage: Initial Cost Initial cost of an VFD isgreater than the cost ofother types of variablespeed controlequipment. Energy savings isgenerally low forapplications whereaverage speedrequirements are nearthe motors ratedspeed.18
VFD on a Constant Speed Pump? Are there energy savings fromusing a VFD on a constantspeed/flow pump?– Flow is never throttled so flow andenergy use will never be lowered.– There might be other advantageslike maintenance, soft start, etc. How about a pumping systemwhere multiple pumps feedmultiple systems and valves areused to match the number ofpumps with the amount of flowneeded for the number of systemsoperating?Disadvantage: Complexity VFD’s like other solidstate devices requirespecializedtroubleshootingknowledge. Manufacturer’s aremaking progress withsimplicity & selfdiagnostic programs.19
Disadvantage: Motor Heating VFD’s used to run constanttorque loads (conveyorbelts) at slow speeds havepotential for overheating.– At low speed, the fan onthe motor produces lesscooling air. Constant torquerequirements withreduced cooling air resultsin motor heating.VFD Slow Speed/Heating Options Increase cooling air flow– Add Pony Motor/Fan ( ) Use better motor insulation– General Purpose Motor with ahigher than standard insulationclass (Class F, H, N, etc) ( )– Invertor Ready Motor ( )– Invertor Duty Motor ( )20
Disadvantage: Power Quality VFD’s can produce significantinput & output waveformdistortion including harmonicdistortion, noise and linenotching. Input Side– Can cause multiple problemsimpacting sensitive electronicdevices, transformers,capacitors, neutral conductorsand neighboring services. Output Side– Causes multiple issues formotors and circuit conductors.Drives As Power Quality Problem Sources1. Induce harmonic distortion onthe incoming supply lines.1.2.3.4.Interfere with other electronics at thesame service or neighboring servicesOverload neutrals and transformersStrange breaker tripsCapacitor failures2. Produce harmonic distortionon the output circuit to themotor/load.1.2.3.Excessive motor heatingExcessive bearing vibration/wearVoltage overshoot on motors &cables.21
Harmonic DistortionHarmonic Distortion( )Voltage3rd Harmonic(-)– 2nd is 2 X 60 120– 3rd is 3 X 60 180– 4th is 4 X 60 240 Odd harmonics are usuallythe problematicfrequencies.TimeResultant Waveform250200150100Voltage Harmonic distortion is“noise” created by theoperation of electronicdevices with “internal AC toDC power supplies” It causes the system toresonate at differentfrequencies of the 60 cs Can Be Quantified VFD’s produce specific harmonicfrequencies with highmagnitudes.– This “fingerprint” can helpdetermine where harmonics arecoming from Standard Electronic Harmonics– Odd harmonics stairstep down– 3rd, 5th, 7th, 11th, 13th, 15th, etc. VFD harmonics– Function of drive “pulse number”– Produce “pairs” of odd harmonics– 5th& 7th, 11th & 13th, etc.22
Total Harmonic Distortion (THD) Common way of quantifying “how muchharmonic distortion” is present.– The amount of distortion from each harmonicfrequency in a waveform can be measured as apercentage of the fundamental frequency.– The individual harmonic % is squared, summedand the square root taken to determine the totalharmonic distortion (THD) content.– Example: 7% voltage THD 7% of the total voltage is non 60 hertz frequencies This is commonly done for both voltage andcurrent.Line Side-Harmonic Distortion Interfereswith Operation of Electronics Line side harmonic current fromdrives can distort the distributionvoltage within your facility and atother customer locations. Distorted current interacts with thesystem impedance to distort thevoltage somewhere else. If the harmonics are large enough,they can impact the operation ofelectronics equipment and VFD’s atneighboring customer locations.23
Harmonic Current Distortion Data Interference Problems AC currents generateelectromagnetic fields The higher thecurrent frequency,the higher theelectromagnetic fieldfrequency These fields caninterrupt data flowcausing; data errors,lost data, and slowerdata transmissionratesLine Side-Unusual Breaker Tripping Customers often report having bad breakersthat trip below rated levels.– If measuring the current trip point without a TrueRMS device, the current value may not be measuredaccurately. Non-True RMS meters don’t really measure the RMS voltage,they calculate it based on assuming a pure sine waveform. Non-True RMS ammeters commonly measure low whenattempting to measure a highly distorted current. Most true RMS meters usually indicate on theircover that they are true RMS meters. Otherswill say in their specifications that they are atrue RMS sensing meter.– A quick check with the vendor or manufacturer canverify any questions.24
Line Side-Overloaded Transformers Current harmonics produce abnormalheating in transformer windings.– Heating reduces the life of the transformer K-Factor Transformers– Transformer with a higher grade ofinsulation to better withstand theadditional heating from the harmonics.– Should be used where significant harmonicdistortion is pre
VFD’s have two types of power factor – Total Power Factor – Displacement Power Factor Utilities measure displacement power factor so a VFD can improve power factor of a system without adding capacitors Advantage: Reduced Voltage Starting An VFD acts like a reduced voltage starter to limit the in-rush current when the motor starts.