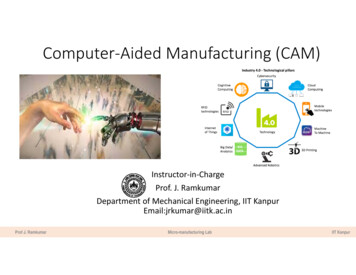
Transcription
Computer‐Aided Manufacturing (CAM)Instructor‐in‐ChargeProf. J. RamkumarDepartment of Mechanical Engineering, IIT KanpurEmail:jrkumar@iitk.ac.inProf J. RamkumarMicro-manufacturing LabIIT Kanpur
ME 761A Computer Aided Manufacturing9 credit courseInstructorProf.J.RamkumarDepartment of Mechanical EngineeringNL-115 Ljrkumar@iitk.ac.inTeaching assistants : Mr.Vyom sharma, vyom@iitk.ac.inMr.Mahavir Singh, mahavir@iitk.ac.inClass Hours : Wednesday & Friday : 10:30 to 12:00Class Room : TB 103Office Hours : Friday 3:00 to 4:00 PM at TA202A ME labCourse Website : http://home.iitk.ac.in/ jrkumar/Course Description :Introductory course of CAD, CAM, RP, Reverse engineering and CAPPPrerequisites :Fundamental understanding of design and manufacturing
Course objectives:1. Acquire fundamental understanding of the principles of CAD/CAM, including engineeringdrawing, geometric and surface and feature-based design2. Math behind geometry to understand CAD3. Applying CAD/CAM concept to product design and manufacturing4. Exposure to CAD/CAM softwares5. Exposure to machines at Imagineering labCourse outcomes:The student will be able to1. Understand engineering design concepts2. Product specification methods3. Construct 3D part models4. Geometric tolerance5. Understanding process planning6. Rapid Manufacturing
Text Book:1. Chang, T. C., Wysk, R. A., Wang, H. P, “Computer aided Manufacturing,” Prentice Hall, Third Ed.,2. Nanua Singh, “Systems Approach to Computer Integrated Design and Manufacturing, “John Wiley and Sons Ltd,First Ed.,Grading Policy Mid sem examEnd sem examPaper reviewMini term ProjectLab exercise1.2.3.4.All exams are closed book and notesProject report and lab exercise report must be typesProjects and review paper have to be individualLate submission will lead to 50% reduction in the assigned marks20%40%10%15%15%
Topics covered in course Engineering product specificationEngineering drawing and orthographic projectionPart modelingSolid and feature based designGeometric modellingProcess engineeringTooling and fixtureCNCRP/RTDFM/DFAProduct lifecycle managementReport formattingCover page requirements Course Name Assignment Name Your name with roll number (& team members if applicable) Total Number of pages
General Policy:Student ConductIt is the responsibility of each student to adhere to the principles of academic integrity. Academic integrity meansthat a student is honest with him/herself, fellow students, instructors, and the University in matters concerning hisor her educational endeavors.Thus, a student should not falsely claim the work of another as his/her own, ormisrepresent him/herself so that the measures of his/her academic performance do not reflect his/her own work orpersonal knowledge. In this regard, cheating will not be tolerated. Cheating includes (but is not limited to) anycommunication (written or oral) during examinations and sharing of work, such as using the same models orcomputer programs or copying work. All homework and projects must be an individual effort unless specificallynoted. Student found cheating in assignment and examination will assigned a F grade for the course.Policy on Classroom Attendance:All students are expected to attend all lectures, quizzes, and examinations. Although classroom attendance does notcontribute to the final course grade, active class participation may help to boost up the course grade in those“borderline” cases”.
Human evolutionNowProf J. RamkumarMicro-manufacturing LabIIT Kanpur
Evolution of computerProf J. RamkumarMicro-manufacturing LabIIT Kanpur
Prof J. RamkumarMicro-manufacturing LabIIT Kanpur
Evolution of cycleProf J. RamkumarMicro-manufacturing LabIIT Kanpur
Manufacturing changes
Manufacturing changes Manufacturing industry affect all facet of our daily life Companies constantly seek ways to optimize process and decreasecost – Manufacturing changes 1990’s – quality was the driving force 2000’s – safety Today – environmental sustainabilityAll lead to internal change in manufacturing industries Automation ‐ old Automation – new – machine size and operability cost decrease Human’s out of blue collar job
Manufacturing change Robotics have become common, easy to use and efficient But still human is required Insourcing Vs outsourcing The primary variation between outsourcing and insourcing is the method inwhich work is divided between various companies or departments forstrategic purposes. Assigning a project to a person or department within thecompany instead of hiring an outside person or company to do the work isconsidered insourcing Outsourcing – shipping delay, quality problems andmiscommunications – calling back of products Area closer to home
Top trends in manufacturing technology Green manufacturing will replace existing methodologies Linear economy to circular economy
Top trends in manufacturing technologyCompanies will turn to low‐cost marketing and funding solutionsNew technology can help manufacturers reach new markets and create new products. However, morecompanies are still looking for cost‐effective ways to develop and test prototypes, and social media andcrowdfunding may be the solution. Most companies already have technologies in place to interact withcustomers, but crowdfunding and social media provides another channel for communication.Responsiveness Will Become Synonymous With Real Time.Manufacturers have always faced a battle with responsiveness. Business‐to‐business and omnichannel sales aremaking this challenge more difficult. However, greater visibility and speed in production are helpingmanufacturers create price quotes for new products and get products from the factory to the end user morequickly.
Top trends in manufacturing technologyMore Off‐Site IT Investments Will Be Made.The days of in‐house IT departments are obsolescent. Cloud‐based technologies are replacing antiquated, legacysystems, and major manufacturers are planning to launch new investments into customer relationshipmanagement (CRM) tools.Avoiding the IIoT Will Be Impossible.Some companies have held out on implementing the IIoT in manufacturing for initial investment reasons, cybersecurity concerns or other issues. However, this will become an impossibility in 2017. Any type of new systempurchased will have connectivity with the internet, provided the company has internet accessCustomization Will Replace Traditional Inventory Management.Traditional inventory management operations will change in 2017. Inventory management will become morereliant on advanced computer analytics systems to manage inventory in real time. This will eliminate shrink fromtheft, damages and errors during shipping, reducing overhead and improving operations
Today’s new Termination1. Flexible Manufacturing System2. Variable Mission Manufacturing3. Computerized Manufacturing System
General FMS
Product realization process The purpose of manufacturing is to produce a product. The product can be single component, such asscrew, gear or it can be a complex assembly such as aeroplane or car. Regardless of the complexity of the product, all products go through a common development activity:product realization process.ScrewGearProf J. RamkumarCar assemblyMicro-manufacturing LabIIT Kanpur
Product realization process cont 1. Planning of product realization4. Purchasing4.1 Purchasing process4.2 purchasing information4.3 verification of purchased product2. Customer related processes2.1 Determination of requirements related to the product2.2 Review of requirements related to the product5. Production and service provision2.3 Customer communication5.1 control of production and service provision5.2 validation of processes for production andservice provision5.3 identification and traceability5.4 customer property5.5 preservation of product3. Design and development3.1 design and development planning3.2 design and development inputs3.3 design and development outputs6. Control of monitoring and measuring devices3.4 design and development review3.5 design and development verification3.6 design and development validation3.7 control of design and development changesProf J. RamkumarMicro-manufacturing LabIIT Kanpur
Engineering process for product realizationProductspecification After an initial design is completed, engineering analysis iscarried out. An assembly may need kinematics analysis toensure that the motion of the parts will achieve thedesired functions. For individual parts, stress and temperature propertiesunder operational conditions may need to be determine. A wide range of analytical and computational tool such asfinite‐element analysis software and kinematics simulationtools are available. Some of these tools have been integrated into CADsoftware, many others can import design data through atranslator. On the basis of the results of analysis, improvements tothe design can be made to reduce the value of thetargeted deign parameters.Prof J. RamkumarMicro-manufacturing LabDesign synthesis(design for X)DesignrepresentationDesign acturingexecutionInspectionIIT Kanpur
Evolution of product realizationBefore we focus on the history of CAM, it is worthwhile to look at the historical development of manufacturingCategorySkeletonHand tools: thousand of year to several thousands of yearsMuscleMachine tool: Industrial Revolution, 18th century, custom‐madeproductSmartnessGauges: Late 19th century, interchangeabilityResourceManufacturing system: early 20th centuryManagementModern management transfer line pull technologyNerveNumerical control, robot (19500s, 1960s, 1970s), flexiblemanufacturing systems, sensor, visionBrainComputer‐aided manufacturing, intelligent manufacturing Prof J. RamkumarMilestoneThe major manufacturing milestones that took place during the course of humancivilization.It is said that what differentiates human being from other animals is our ability to usetools.Some animals do use tools to help them get their food.Human are the only species that know how to build (i.e. manufacture).Today manufacturing equipment is commonly control by digital devices throughsoftware programsMicro-manufacturing LabIIT Kanpur
CAM and its historical developmentYearSoftwareHardware James T. Parsons proposed NC concept1945‐19501950‐1955 Part programming prepared manually MIT servo mechanism lab USAF NC milling machine proj. 1st successful demo1955‐1960 MIT started APT development Al, Dartmouth conference LISP language APT language Automatic tool changer‐IBM 1st production skin miller Machining centre1960‐1965 SKETCHPAD Interactive computer graphics coons patch, sculpturedsurfaces 1st industrial robot CRT display Adaptive control‐Bendix1965‐1970 Bezier patch, sculptured surfaces CAD Drafting 7700 NCs installed CNC, DNC concept and mini‐computers PLC 1st DNC system1970‐1975 Solid modelling development started Build‐1 solid modeler CAM, CAD/CAM Microcomputers FMS1975‐1980 PADL‐ 1 solid modeler IGES graphics exchange standards supercomputers Super minicomputers1980‐1985 Solid modeller became commercialized PC—based CAD Micro based workstations GM MAP LAN standard1985‐1990 MAP, TOP LAN standards Computer vision Automated factory1990‐1995 Neural nets In‐Situ sensing and control MEMS1995‐2000 Virtual manufacturing Enterprise manufacturing Collaborative manufacturing Nano manufacturing (1‐100nm)Prof J. RamkumarMicro-manufacturing LabIIT Kanpur
Design and development 3.1 design and development planning 3.2 design and development inputs 3.3 design and development outputs . Brain Computer‐aided manufacturing, intelligent