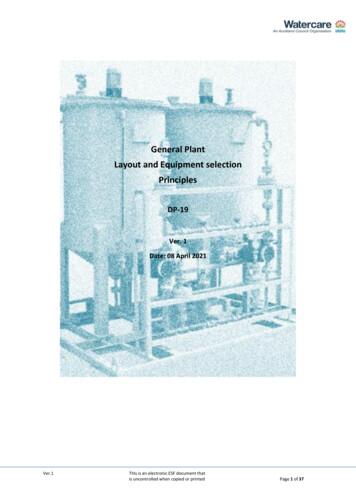
Transcription
General PlantLayout and Equipment selectionPrinciplesDP-19Ver. 1Date: 08 April 2021Ver.1This is an electronic ESF document thatis uncontrolled when copied or printedPage 1 of 37
RevisionDescriptionReleased ByDate0.1Working draftJ de Villiers25/03/20201First releaseJ de Villiers08/04/2021Ver.1This is an electronic ESF document thatis uncontrolled when copied or printedPage 2 of 37
Table of contentsDEFINITIONS . 6PART A –GENERAL REQUIREMENTS . 71.INTRODUCTION . 82.‘MUST’ VERSUS ‘SHALL’ VERSUS ‘WILL’ . 83.REFERENCED STANDARDS . 83.1STANDARDS LIST . 83.1.1Watercare standards . 83.1.2National and international standards . 83.1.3Regulations . 93.1.4Other publications . 94.MATERIAL SCHEDULES - MATERIAL SELECTION AT DESIGN . 95.DESIGN REQUIREMENT EXEMPTIONS . 9PART B – LAYOUT DESIGN . 101.PREMISES ACCESS CONTROL. 112.CHEMICAL MANAGEMENT AND STORAGE . 122.1 GENERAL . 122.2 TREATMENT CHEMICALS . 122.2.1Hazardous substance classes . 122.2.2Storage . 122.2.3Labelling and signage . 132.2.4Waste management . 132.2.5Record keeping . 133HAZARDOUS AREAS. 134CROSS-CONNECTION CONTROL . 144PROCESS AND POTABLE WATER IN PLANT PIPING . 145COMMON WALL CONSTRUCTION . 146CONFINED SPACES . 157EQUIPMENT GENERAL POSITIONING . 15PART C – MECHANICAL DESIGN . 161.Ver.1GUARDS . 17This is an electronic ESF document thatis uncontrolled when copied or printedPage 3 of 37
2.MAXIMUM EQUIPMENT NOISE LEVELS . 173.PIPING LAYOUTS. 174.FRAMES AND MOUNTINGS . 185.ACOUSTIC LOUVERS . 196.MATERIAL AND EQUIPMENT HANDLING . 197.PLATFORMS AND ACCESS STRUCTURES . 198.GANTRIES AND CRANES . 209.LOADING MATERIALS, HOPPERS AND CONVEYORS FOR HANDLING . 209.1LOADING ACCESS . 209.2HOPPERS AND CONVEYERS . 2010.COATING COLOURS . 2010.1WATER TREATMENT PLANT COLOUR SCHEME . 2110.2RESOURCE RECOVERY (WASTEWATER) TREATMENT PLANT COLOUR SCHEME . 22PART D – SEISMIC DESIGN OF EQUIPMENT, EQUIPMENT SUPPORTS AND TANKS . 251.GENERAL . 262.TANKS OUTSIDE BUILDINGS . 263.SPECIFIC EARTHQUAKE ANALYSIS. 284.SEISMIC LOADING COEFFICIENT. 285.EQUIPMENT SUPPORTED BY BUILDING STRUCTURES . 286.FREE STANDING EQUIPMENT . 287.PRESSURE VESSELS . 28PART E – SPECIFIC MATERIALS CONSIDERATIONS FOR PROCESSES . 291.INTRODUCTION . 302.MATERIALS THAT MAY NOT BE USED . 303.PIPING SYSTEMS . 303.1MILD STEEL (MS) . 303.2STAINLESS STEEL . 303.3DUCTILE IRON . 303.4POLYVINYL CHLORIDE (PVC) . 313.5ACRYLONITRILE BUTADIENE STYRENE . 313.6POLYETHYLENE . 313.7FIBRE REINFORCED PLASTIC . 31Ver.1This is an electronic ESF document thatis uncontrolled when copied or printedPage 4 of 37
3.8HOSE . 313.9SUBSOIL DRAINAGE . 314.PIPE FITTINGS . 324.1GENERAL . 324.2STAINLESS STEEL AND MILD STEEL. 324.3POLYVINYL CHLORIDE (PVC) AND ACRYLONITRILE BUTADIENE STYRENE (ABS) . 324.4CONCRETE . 324.5VITRIFIED CLAY. 325.JOINTING SELECTION . 325.1GENERAL . 325.2STEEL WELDING. 325.3HDPE . 325.4PVC . 335.5FLANGES . 335.6FLEXIBLE COUPLINGS . 335.7PRESSED COUPLINGS . 336.VALVE SELECTION . 337.FIXINGS AND BRACKETS . 368.DOSE PUMPS . 369.CORROSION CONTROL. 37Ver.1This is an electronic ESF document thatis uncontrolled when copied or printedPage 5 of 37
DefinitionsTreatment (plant)Water treatment plants for the treatment of raw water by mechanicalor chemical processes to meet the Drinking water Standards for NewZealand, orWastewater treatment that receives wastewater from Wastewatertransmission (ref. “Transmission”) to remove contaminants throughmechanical, chemical and biological processes.AcronymsVer.1CADComputer aided designkPaKilo PascalLLitremMetrem²Metre squarem³Metre cubicmmMillimetreNBNominal boreO&MOperations and MaintenancePVCPolyvinyl chloride pipesecsecondsThis is an electronic ESF document thatis uncontrolled when copied or printedPage 6 of 37
Part A –General requirementsVer.1This is an electronic ESF document thatis uncontrolled when copied or printedPage 7 of 37
1. IntroductionThis document is to describe the general considerations for process plant layout and material selection inconjunction with the Health and Safety in Facility design guidelines and particular plant design requirements.2. ‘Must’ versus ‘Shall’ versus ‘Will’Where the verbs must, shall and will (or its past tense forms) are used they describe a requirement forcompliance with the statement in which it is used.‘Shall’ and ‘must’ expresses a mandatory condition or action. ‘Will’ is used to prescribe a performance outcomeor intent.3. Referenced standards3.1 Standards listThis standard must be read in conjunction with the Watercare, national and international standards listed below.Where conflict or ambiguity exists, this standard shall take precedence. Where there is conflict betweenreferenced standards, the higher level of standard shall take precedence.3.1.1 Watercare standardsDP - 11 Health and Safety in Facility Design guidelinesDP – 09 Electrical designDP – 12 Architectural design guidelinesME - General mechanical construction standardMS - Material supply standard7363 - Watercare CAD manualAI - Data and Asset Information standard3.1.2 National and international standardsDrinking Water Standards for New Zealand, 2005 (rev. 2018)NZS 1170 Structural design actionsPart 5 Earthquake actions – New ZealandPart 5 Supp 1 Earthquake actions – New Zealand – CommentaryNZS 3106 Code of Practice for concrete structures for the storage of liquidsNZS4219 Seismic performance of engineering systems in buildingsAS/NZS1657 Fixed platforms, walkways, stairways and ladders. Design, construction and installationNZS 4541 Automatic fire sprinkler systemsAS/NZS4024.1601 Design of controls, interlocks and guarding - Guards - General requirements for the designand construction of fixed and movable guardsNZS6801 Acoustics - Measurement of environmental soundVer.1This is an electronic ESF document thatis uncontrolled when copied or printedPage 8 of 37
3.1.3 RegulationsHealth and Safety at Work Act 2015The Hazardous Substances and New Organisms Act 1996 (HSNO)Health and Safety at Work (Hazardous substances) Regulation 2017Resource Management Act 199Building Act 20043.1.4 Other publicationsSeismic Design of Storage Tanks 2009 (New Zealand Society for Earthquake Engineering).API 650 Appendix E 12th Edition, American Petroleum Institute.Engineering NZ practice note 19 “Seismic resistance of pressure equipment and its supports” Jan 2013.4. Material schedules - material selection at designMaterial selection shall be completed by the designer on the following principle:Feasible materials shall be shortlisted based on their limitations of use to ensure reliability, future maintenanceand the cost of repair is kept to a minimum. The consideration of technical advantages shall only be taken on theshortlisted materials. Function and maintainability shall take precedence.The selected material shall be fit for purpose and submitted to Watercare for approval before commencing withdetailed design.As part of the design output, the designer shall complete the procurement schedules for the products andidentify any design specific requirements over and above the minimum requirements stated by Watercare’sMaterial Supply standard.5. Design requirement exemptionsThe following projects are typically excluded from design work:a)Installation or replacements of like-for-like valves, fittings and meter assemblies with componentry that arefully compliant with the Watercare Material Supply standard.b) Repair of a system component or replacing it with a similar Watercare approved component of the sameoperational capacity as described in the original design.c) Maintaining corrosion protection on facilities, unless a new corrosion protection system is proposed.To qualify for the design exemption the works must be reviewed by a Watercare engineer with suitablequalification and experience, completed to Watercare standard design and the asset data, including as-builtdrawings updated to the current standard.Ver.1This is an electronic ESF document thatis uncontrolled when copied or printedPage 9 of 37
Part B – Layout designVer.1This is an electronic ESF document thatis uncontrolled when copied or printedPage 10 of 37
1. Premises access controla)This section shall be read with consultation on the Watercare operational policy document:“Operational Facility/Asset Access and Key/Security Card Control Procedure”. (This document is notpublicly available and must be requested from Watercare).b) Reference shall be made to the Watercare architectural guidelines in relation to design considerationsfor sections on site layout with considerations to crime prevention through environmental design(CPTED) principles.c) Refer to the Health and Safety in Facility guidelines for arrangements between operational and breakout areas.d) Wastewater (resource recovery) plants and water treatment plants for drinking water may requiredifferent consideration to access that could result in contamination or tampering or related publichealth incidents. Treatment facilities are often more remote and therefore may not have visibilitywhere public alarm can be raised, or limited operator attendance due to comprehensive automation.The following table describes access concerns control concerns and possible solutions:Access concernPotential ImpactPlant type impactedSolutionsVandalism and the wilfuldamage of propertyLoss of operationWater treatmentWater qualityWastewater/ResourcerecoverySecurity management,MonitoringAestheticsTerrorismWater qualityWater treatmentLoss of operationMinimise sensitiveinformation withinpublic realmLoss of supplyTheftPerimeter breach: Gate accesscontrolNumber of accessgates and fencesFencesVisitors for workLowered resilienceWater treatmentPublic healthWastewater/ResourcerecoveryPublic healthWater Public healthWater treatmentPublic healthWater treatmentWastewater/ResourcerecoveryAudio-visual breach /Social media:Public healthWater mination/pandemicWater quality/PublichealthWater treatmentVer.1Security managementInspection, digitalmonitoringMinimising access pointsSecurity controlWastewater/ResourcerecoveryPublic site visitsDigital protectionThis is an electronic ESF document thatis uncontrolled when copied or printedInduction and safetypracticesWorks managementManage information andlimiting video and photomaterialPreventing unsolicitedcapture and sharing ofvideo, photos, modelsand operational recordsPerimeter securityMonitoringPage 11 of 37
Access concernIT/control/automationsystem securityPotential ImpactPlant type impactedSolutionsEnvironmental healthWastewater/ResourcerecoveryStaff isolation andflexibility in skillsPublic healthWater treatmentDigital protectionLoss of operationWastewater/ResourcerecoveryLoss of supplyTerrorism2. Chemical management and storage2.1 GeneralThe design must produce chemical storage and handling solutions that meets the current legislativerequirements under the HSNO and Health and safety at work (Hazardous substances) regulations.2.2 Treatment chemicals2.2.1 Hazardous substance classesSubstance classificationDescriptionClass 1Substance of explosive natureClass 2Flammable gasClass 3Flammable liquidClass 4Flammable solidClass 5Substance with ability to oxidise (to accelerate a fire)Class 6Acute or chronic toxicity – toxic to humansClass 8CorrosivenessClass 9Eco-toxicity with or without bioaccumulation (directlyor indirectly toxic to the environment)2.2.2 Storagea)b)c)d)The design shall comply with the Health and Safety at Work (Hazardous substances) Regulations 2017.Access to class 6 and 8 storage areas must be secured from access by unauthorised persons.The storage area must have appropriate ventilation.The storage area must be designed with appropriate spillage retention measures where tanks or pipework may fail, or where chemicals are transferred or decanted.e) Bund protection from rain whilst allowing air flow or retention as required for the substance (such aslouvered walls to prevent rain but still facilitate air flow.f) Incompatible substances or substances that may react dangerously must not be stored in the samearea.g) Onsite storage should be minimised to reduce hazards.h) Larger volumes require chemicals to be stored in separate areas to public spaces as defined by theregulations.i) The storage area must be prepared for any health-related emergency or spillage that can occur fromthe stored substance.Ver.1This is an electronic ESF document thatis uncontrolled when copied or printedPage 12 of 37
j)k)l)Above ground tanks for must be earthed and bonded to AS/NZS1020:1995 and lightning protected inaccordance with AS/NZS1768:2007 as appropriate for the related classification.Class 2 tanks may not be stacked above one another.Class 3 tanks may not be located end-to-end unless determined by risk assessment that failure of a tankend will not impact other tanks.2.2.3 Labelling and signagea) Containers and storage items must be appropriate for the substance and marked accordinglyb) Containers labels and signage should be such as not to be mistaken for food or beverage i.e. do not usecontainers that can be mistaken for such.c) Tanks must be marked with the design approval number.2.2.4 Waste managementThe plant layout design should consider the practicalities of waste management for the site such as:a)Emptying of bunds: Discharge to waste of naturalised substances into the environment Removing content off-site for disposal Bund cleaning practiceb) Storage of out-of-date substances for collection, its labelling and segregation from other parts of theplant.2.2.5 Record keepinga)b)c)d)e)f)3Inventory records shall be kept up to date.Hazardous substances location plan must be developed and kept up to date.Safety data sheets (SDS) available and linked to inventory.Compliance plans and training material must be prepared.Emergency response plan (ERP) must cover:i.Reasonably foreseeable emergenciesii.Describe location of emergency equipmentiii.Be tested within three months of a change madeiv.Records for testing the ERPAudit methods and frequency must be established.Hazardous areasa) Some areas of the plant may be classified as hazardous areas.b) Any approved safety barriers must be designed for installation to the equipment supplier’s instructionswithout modification.c) All equipment installations within these areas shall employ protection techniques appropriate for the areaof classification as defined by AS/NZS 60079.d) All equipment including cable and glands, shall be certified by a suitably certified testing authority.e) A verification dossier shall be established in accordance with AS/NZS60079.Ver.1This is an electronic ESF document thatis uncontrolled when copied or printedPage 13 of 37
4Cross-connection controlRecommended cross-connection protection at equipment is listed below:Description of equipment / installationRecommended minimum protectionLiquid chemical tanksi)ii)iii)Provide air gap on dilution water supplyAir gap to overflow and drainProvide day-tanksDry chemical feeder tanksi)ii)Provide air gap on fill supplyAir gap to overflow and drainChemical feed pumpsi)ii)iii)Discharge at point of positive pressureProvide vacuum relief or similar anti-siphon deviceNo pump priming or flushing lineChemical carrier linesProvide a reduced pressure zone (RPZ) backflow device at thesupplyChemical injection point to carrier lineProvide a reduced pressure zone (RPZ)Chemical injection line in common withpotable water / non-potable waterProvide a reduced pressure zone (RPZ), eliminate crossconnection (separate injectors for raw or filtered water)Surface washersi)ii)iii)Filter backwashProvide air gap to overflow and drainFilter-to-wasteProvide air gap to overflow and drain, or air gap to processstream ahead of filtersMembrane cleaning (in-place)Physical disconnectSample lines to monitoring equipmenti)ii)Air gapAtmospheric vacuum breakerMonitoring equipment for raw andpotable wateri)ii)Air gapPhysical disconnectAtmospheric vacuum breakPressure vacuum breakers assemblyDouble check valve assembly4 Process and potable water in plant pipinga)Potable water for consumption shall be completely separated from process water supplies. Due to thecomplexity of process water reticulation system layouts the probability of interconnection of process waterpiping is high.b) Best practice is to take process water from discreet points for individual processes.c) A reduced pressure zone (RPZ) backflow device shall be installed at these take-off points.d) Potable water for process uses in the facility shall be from no more than two discrete points with backflowprevention at the supply point.e) Refer to Part C, section 4 for piping layout and section 10 of this part for colour coding of pipework.5 Common wall constructionThe design shall consider cross contamination that may occur because of shared or common walls betweenwater being treated and finished water. Either double walls with an adequate separation to allow inspection ormonitoring of the wall integrity, or basins should be arranged to be well separated for prevention.Ver.1This is an electronic ESF document thatis uncontrolled when copied or printedPage 14 of 37
6 Confined spacesConfined space shall be minimised. There are dangers and difficulties associated with conducting maintenancework in confined spaces. The design shall seek to limit confined spaces and place infrastructure above ground,not restrict entry or exit, and not cause engulfment or poor air quality.7 Equipment general positioningThis section must be read with Part C.EquipmentPositioningValvesSize 50mm positioned 600mm to 1000mm from the operator platformto the top of the operating mechanism. This includes any valve of anysize that is required to be disabled for r3gular maintenance such ascheck valves.Size 50mm positioned not higher than 1500mm from the operatorplatform (excludes regularly maintainable valves)PumpsMounted on a pump skid with surface level minimum 200mm above theground level. (excludes submersible pumps)Horizontal clearance of minimum 1000mmVertical space above pumps over 25kg shall be clear and provided withaccess for lifting equipment.Process (dosing) pumpsMounted on a dosing skid positioned at a height of 600mm clear frompipework that could leak onto the pump and positioned to allowclearances for maintenance of pump componentsSensorsIn reach of platforms and other access means and removable such thatequipment or parts cannot be dropped into process containersMetersClearances and pipe runs must be observed as described by themanufacturer’s installation requirementsMonitoring stationsSuitable for human interaction not requiring leaning over otherequipment and at a height from standing surface of 1.2m to 1.5mCable runsShort as possible, either mounted above 2000mm overhead on cabletrays or in cable ducts. Ducting should not be in areas that can flood orhave poor ventilation and prone to high temperatures.Ver.1This is an electronic ESF document thatis uncontrolled when copied or printedPage 15 of 37
Part C – Mechanical designVer.1This is an electronic ESF document thatis uncontrolled when copied or printedPage 16 of 37
1. Guardsa)All rotating, moving or oscillating items shall be fully guarded to comply with the relevant standardsand WorkSafe requirements.b) All drive mechanism, rotating and reciprocating parts and drive belts shall be securely shrouded toprovide protection and safety for both maintenance and operating personnel.c) All such guards shall be of adequate material and coverage but shall also be readily removable forgaining access to the plant without the need for first removing or displacing any major item of plant.d) Guard design shall allow inspection ports or with expanded metal sections to allow inspection withouthaving to remove the guards in compliance with AS/NZS4024.1601.e) All guards shall be designed and fitted with location pins or other suitable devices to ensure the correctpositioning of the guard and provide positive fixing.f) Guards shall require the use of engineering tools for removal and shall not be able to be simply liftedon and off.g) Grilles, bars or mesh shall be provided behind inspection ports where moving equipment may bereached. Interlocks shall be provided to stop equipment if covers are opened.2. Maximum equipment noise levelsa)The sound pressure level (L10) for all equipment operating at full load shall not exceed 80 dB(A) at adistance not greater than three metres radius from the equipment or sound enclosure.b) Noise levels shall be reduced by the enclosure, or lagg
This document is to describe the general considerations for process plant layout and material selection in conjunction with the Health and Safety in Facility design guidelines and particular plant design