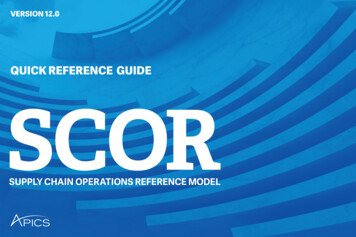
Transcription
VERSION 12.0QUICK REFERENCE GUIDE
SCOR ProcessesPeople—Supply Chain SkillsThe Supply Chain Operations Reference (SCOR) model describes the business activitiesassociated with all phases of satisfying a customer’s demand. The model itself is organizedaround the six primary management processes of Plan, Source, Make, Deliver, Returnand Enable. Using these process building blocks, the SCOR model can be used to describesupply chains that are very simple or very complex using a common set of definitionsacross disparate industries. Today public and private organizations and companies aroundthe world use the model as a foundation for global and site-specific supply chainimprovement projects.The people section introduced in SCOR 10.0 provides a means for managing talent in thesupply chain by incorporating a standard for describing the expertise required to performtasks and manage processes. The SCOR skills management complements the existingprocess, metrics, and practice reference components by aligning people and their skills tothe processes.SCOR spans all customer interactions (quote to cash), all physical material transactions(procure to payment, including equipment, supplies, spare parts, bulk product, software,etc.) and all market interactions (manufacturing, from the understanding of aggregatedemand to the fulfillment of each order).The model is designed and maintained to support supply chains of various complexities andacross multiple industries. The model focuses on three process levels and does not attemptto prescribe how a particular organization should conduct its business or tailor its systemsor information flow.2SCOR 12.0 Quick Reference GuideA Skill in SCOR is the capacity to deliver predetermined results with minimal input of timeand energy, characterized by a standard definition with associated experience, aptitudes,and training.Experience is the knowledge or ability acquired by observation or active participation,obtained by doing the work in a real life environment, and undergoing different situationsthat require different actions.Training develops a skill or type of behavior through instruction.All people skills are coded with a capital letter H followed by a capital letter representing theelement: S for Skills, E for Experience and T for Training. These are followed by a period anda four digit number. Note: The number in the ID is a unique identifier and does NOT indicateany kind of priority, importance, or other meaning.
sP - PlansS - SourcesM - MakesD - DeliversP1Plan Supply ChainsP2Plan SourcesP3Plan MakesP4Plan DeliversP5Plan ReturnsS1Source StockedProductsS2Source Make-toOrder ProductsS3Source Engineerto-Order -to-OrdersD1Deliver StockedProductsD2Deliver Make-toOrder ProductsD3Deliver Engineerto-Order ProductsD4Deliver RetailProductsP1.1:Identify, Prioritizeand AggregateSupply ChainRequirementssP1.2:Identify, Prioritizeand AggregateSupply ChainResourcessP1.3:Balance SupplyChain Resourceswith SCRequirementssP1.4:Establish andCommunicateSupply Chain PlanssP2.1:Identify, Prioritizeand AggregateProductRequirementssP2.2:Identify, Assess andAggregate ProductResourcessP2.3:Balance ProductResourceswith ProductRequirementssP2.4:Establish SourcingPlanssP3.1:Identify, Prioritizeand AggregateProductionRequirementssP3.2:Identify, Assessand AggregateProductionResourcessP3.3:Balance ProductionResourceswith ProductionRequirementssP3.4:EstablishProduction PlanssP4.1:Identify, Prioritizeand AggregateDeliveryRequirementssP4.2:Identify, Assess andAggregate DeliveryResourcessP4.3:Balance DeliveryResources andCapabilitieswith DeliveryRequirementssP4.4:EstablishDelivery PlanssP5.1:Assess andAggregate ReturnRequirementssP5.2:Identify, Assessand AggregateReturn ResourcessP5.3:Balance ReturnResourceswith ReturnRequirementssP5.4:Establish andCommunicateReturn PlanssS1.1:ScheduleProduct DeliveriessS1.2:Receive ProductsS1.3:Verify ProductsS1.4:Transfer ProductsS1.5:AuthorizeSupplier PaymentsS2.1:ScheduleProduct DeliveriessS2.2:Receive ProductsS2.3:Verify ProductsS2.4:Transfer ProductsS2.5:AuthorizeSupplier PaymentsS3.1:Identify Sourcesof SupplysS3.2:Select FinalSupplier andNegotiatesS3.3:ScheduleProduct DeliveriessS3.4:Receive ProductsS3.5:Verify ProductsS3.6:Transfer ProductsS3.7:AuthorizeSupplier ue MaterialsM1.3:Produce and TestsM1.4:PackagesM1.5:Stage ProductsM1.6:Release Product toDeliversM1.7:Waste sue Sourced/InProcess ProductsM2.3:Produce and TestsM2.4:PackagesM2.5:StageFinished ProductsM2.6:Release FinishedProduct to DeliversM2.7:Waste DisposalsM3.1:Finalize itiessM3.3:Issue Sourced/InProcess ProductsM3.4:Produce and TestsM3.5:PackagesM3.6:StageFinished ProductsM3.7:Release Productto DeliversM3.8:Waste DisposalsD1.1:Process Inquiryand QuotesD1.2:Receive, Enter,and Validate OrdersD1.3:Reserve Inventoryand DetermineDelivery DatesD1.4:Consolidate OrderssD1.5:Build LoadssD1.6:Route ShipmentssD1.7:Select Carriers andRate ShipmentssD1.8:Receive Productfrom Sourceor MakesD1.9:Pick ProductsD1.10:Pack ProductsD1.11:Load Vehicle& GenerateShipping DocssD1.12:Ship ProductsD1.13:Receive andVerify Productby CustomersD1.14:Install ProductsD1.15:InvoicesD2.1:Process Inquiryand QuotesD2.2:Receive, Configure,Enter andValidate OrdersD2.3:Reserve Inventoryand DetermineDelivery DatesD2.4:Consolidate OrderssD2.5:Build LoadssD2.6:Route ShipmentssD2.7:Select Carriers andRate ShipmentssD2.8:Receive Productfrom Sourceor MakesD2.9:Pick ProductsD2.10:Pack ProductsD2.11:Load Product& GenerateShipping DocssD2.12:Ship ProductsD2.13:Receive andVerify Productby CustomersD2.14:Install ProductsD2.15:InvoicesD3.1:Obtain andRespond to RFP/RFQsD3.2:Negotiate andReceive ContractsD3.3:Enter Order,Commit Resources& Launch ProgramsD3.4:ScheduleInstallationsD3.5:Build LoadssD3.6:Route ShipmentssD3.7:Select Carriers &Rate ShipmentssD3.8:Receive Productfrom Sourceor MakesD3.9:Pick ProductsD3.10:Pack ProductsD3.11:Load Product& GenerateShipping DocssD3.12:Ship ProductsD3.13:Receive andVerify Productby CustomersD3.14:Install ProductsD3.15:InvoicesD4.1:GenerateStocking SchedulesD4.2:Receive Productat StoresD4.3:Pick Productfrom backroomsD4.4:Stock ShelfsD4.5:Fill Shopping CartsD4.6:CheckoutsD4.7:Deliver and/orinstallsR - ReturnsE - EnablesSR1Source ReturnDefective ProductsSR2Source ReturnMRO ProductsSR3Source ReturnExcess ProductsDR1Deliver ReturnDefective ProductsDR2Deliver ReturnMRO ProductsDR3Deliver ReturnExcess ProductsE1Manage SupplyChain BusinessRulessE2ManageSupply ChainPerformancesE3ManageSupply Chain Dataand InformationsE4ManageSupply ChainHuman ResourcessE5ManageSupply ChainAssetssE6ManageSupply ChainContractssE7ManageSupply ChainNetworksE8Manage SupplyChain RegulatoryCompliancesE9ManageSupply Chain RisksE10ManageSupply ChainProcurementsE11ManageSupply ChainTechnologysSR1.1:Identify DefectiveProduct ConditionsSR1.2:DispositionDefective ProductsSR1.3:Request DefectiveProduct ReturnAuthorizationsSR1.4:Schedule DefectiveProduct ShipmentsSR1.5:ReturnDefective ProductsSR2.1:Identify MROProduct ConditionsSR2.2:DispositionMRO ProductsSR2.3:RequestMRO ReturnAuthorizationsSR2.4:ScheduleMRO ShipmentsSR2.5:ReturnMRO ProductsSR3.1:Identify ExcessProduct ConditionsSR3.2:DispositionExcess ProductsSR3.3:Request ExcessProduct ReturnAuthorizationsSR3.4:Schedule ExcessProduct ShipmentsSR3.5:ReturnExcess ProductsDR1.1:Authorize DefectiveProduct ReturnsDR1.2:Schedule DefectiveReturn ReceiptsDR1.3:Receive DefectiveProduct(includes verify)sDR1.4:TransferDefective ProductsDR2.1:Authorize MROProduct ReturnsDR2.2:Schedule MROReturn ReceiptsDR2.3:ReceiveMRO ProductsDR2.4:TransferMRO ProductsDR3.1:Authorize ExcessProduct ReturnsDR3.2:Schedule ExcessReturn ReceiptsDR3.3:ReceiveExcess ProductsDR3.4:TransferExcess ProductsE1.1:Gather BusinessRule RequirementssE1.2:Interpret BusinessRule RequirementsE1.3:DocumentBusiness RulesE1.4:CommunicateBusiness RulesE1.5:Release/PublishBusiness RulesE1.6:Retire BusinessRulesE2.1:Initiate ReportingsE2.2:Analyze ReportssE2.3:Find Root CausessE2.4:PrioritizeRoot CausessE2.5:DevelopCorrective ActionssE2.6:Approve & in AccesssE3.5:Publish InformationsE3.6:Verify InformationsE4.1:Identify Skills/ResourceRequirementsE4.2:Identify AvailableSkills/ResourcessE4.3:Match Skills/ResourcessE4.4:Determine onsE4.6:Approve, Prioritizeand LaunchsE5.1:Schedule AssetManagementActivitiessE5.2:Take Asset Off-linesE5.3:Inspect andTroubleshootsE5.4:Install andConfiguresE5.5:Clean, Maintainand RepairsE5.6:Decommissionand DisposesE5.7:InspectMaintenancesE5.8:Reinstate AssetsE6.1:Receive Contract/Contract UpdatessE6.2:Enter andDistribute ContractsE6.3:Activate/ArchiveContractsE6.4:Review ContractualPerformancesE6.5:IdentifyPerformance ovementssE6.7:Select, Prioritizeand DistributeResolutionssE7.1:Select Scopeand OrganizationsE7.2:Gather Inputand DatasE7.3:Develop t ImpactsE7.6:Select and ApprovesE7.7:Develop ChangeProgramsE7.8:LaunchChange ProgramsE8.1:MonitorRegulatory EntitiessE8.2:Assess RegulatoryPublicationssE8.3:Identify RegulatoryDeficienciessE8.4:Define RemediationsE9.1:Establish ContextsE9.2:Identify Risk EventssE9.3:Quantify RiskssE9.4:Evaluate RiskssE9.5:Mitigate RisksE10.1:Develop Strategyand PlansE10.2:Pre-Procurement/ Market Test andMarket 10.4:Supplier Selectionto ParticipatesE10.5:Issue ITT / RFQsE10.6:Bid / TenderEvaluation andValidationsE10.7:Contract Award andImplementationsE11.1:Define SupplyChain TechnologyRequirementssE11.2:Identify Supply ChainTechnologyRoadmapsE11.4:Select TechnologySolutionsE11.5:Define and DeployTechnologySolutionsE11.6:Maintain andImprove TechnologySolutionsE11.7:Retire TechnologySolution
SCOR PracticesSCOR PerformanceA practice is a unique way to configure a process or a set of processes. The uniqueness canbe related to the automation of the process, a technology applied in the process, special skillsapplied to the process, a unique sequence for performing the process, or a unique methodfor distributing and connecting processes between organizations. All practices have links toone or more processes, one or more metrics and, where available, one or more skills.The performance or metrics section of SCOR focuses on understanding the outcomes of thesupply chain and consists of two types of elements: Performance Attributes and Metrics., andintroduces the concept of Process/Practice Maturities.SCOR Practices are classified to simplify identification of practices by areaof interest:nnnnnnnnnnBusiness Process Analysis/ImprovementCustomer SupportDistribution ManagementInformation ManagementInventory ManagementMaterial HandlingNew Product IntroductionOrder Engineering (ETO)Order ManagementPeople Management (Training)nnnnnnnnnPlanning and ForecastingProduction ExecutionProduct Lifecycle ManagementPurchasing /ProcurementReverse LogisticsRisk/Security ManagementSustainable Supply Chain ManagementTransportation ManagementWarehousingSpecial ApplicationsSustainableSCOR is based upon The GRI Sustainability Reporting Standards (GRI Standards)that are within scope of the SCOR model. GRI Standards are free to use and are available atwww.globalreporting.org/standards. The following strategic environmental metrics allowthe SCOR model to be used as a framework for environmental accounting:nnMaterials Used(Weight or Volume)Energy Consumed(Joules,Watt-hours or Multiples)Water Volume Withdrawn(Gallons, Liters or Multiples)nnAir Emissions(Metric Tons or Equivalents)Liquid and Solid Wastes(Gallons, Liters or Multiples, Weightor Volume)The SCOR framework ties emissions to the originating processes, providing a structure formeasuring environmental performance and identifying where performance can beimproved. The hierarchical nature of the model allows strategic environmental footprintgoals to be translated to specific targets and activities.4SCOR 12.0 Quick Reference t Management Efficiency (Assets)A metric is a standard for measurement of the performance of a supply chain or process.SCOR metrics are diagnostic metrics (compare to how diagnosis is used in a medical office).SCOR recognizes three levels of pre-defined metrics:Level-1 metrics are diagnostics for the overall health of the supply chain. These metrics arealso known as strategic metrics and key performance indicators (KPI). Benchmarking level-1metrics helps establishing realistic targets to support strategic directions.Level-2 metrics serve as diagnostics for the level-1 metrics. The diagnostic relationshiphelps to identify the root cause or causes of a performance gap for a level-1 metric.SustainableSCORnA performance attribute is a grouping or categorization of metrics used to express a specificstrategy. An attribute itself cannot be measured; it is used to set strategic direction. Forexample: “The LX product needs to be leading the competition in reliability“ and “The XY-marketrequires us to be among the top 10 agile manufacturers“. Metrics measure the ability toachieve these strategic directions. SCOR recognizes 5 performance attributes:Level-3 metrics serve as diagnostics for level-2 metrics.The analysis of performance of metrics from level-1 through 3 is referred to as metricsdecomposition, performance diagnosis or metrics root cause analysis. Metricsdecomposition is a first step in identifying the processes that need further investigation.(Processes are linked to level-1, level-2 and level-3 metrics).
ReliabilityResponsivenessAgilityCostRL.1.1 - Perfect Order FulfillmentRS.1.1 - Order Fulfillment Cycle TimeAG.1.1 - Upside Supply Chain AdaptabilityCO.1.1 - Total Supply Chain Management CostsAM.1.1 - Cash-to-Cash Cycle TimeRL.2.1 - % of Orders Delivered In FullRS.2.1 - Source Cycle TimeAG.2.1 - Upside Adaptability (Source)CO.2.1 - Cost to PlanAM.2.1 - Days Sales OutstandingRL.3.33 - Delivery Item AccuracyRS.3.8 - Authorize Supplier Payment Cycle TimeAG.2.2 - Upside Adaptability (Make)CO.3.1 - Cost to Plan Supply ChainAM.2.2 - Inventory Days of SupplyRL.3.35 - Delivery Quantity AccuracyRS.3.35 - Identify Sources of Supply Cycle TimeAG.2.3 - Upside Adaptability (Deliver)CO.3.2 - Cost to Plan (Source)AM.3.16 - Inventory Days of Supply ( Raw Material )RL.2.2 - Delivery Performance to Customer Commit DateRS.3.107 - Receive Product Cycle TimeAG.2.4 - Upside Return Adaptability (Source)CO.3.3 - Cost to Plan (Make)AM.3.17 - Inventory Days of Supply ( WIP )RL.3.32 - Customer Commit Date Achievement TimeCustomer ReceivingRS.3.122 - Schedule Product Deliveries Cycle TimeAM.3.23 - Recycle Days of SupplyRL.3.34 - Delivery Location AccuracyRL.2.3 - Documentation AccuracyRL.3.31 - Compliance Documentation AccuracyRL.3.43 - Other Required Documentation AccuracyRL.3.45 - Payment Documentation AccuracyRL.3.50 - Shipping Documentation AccuracyRL.2.4 - Perfect ConditionRL.3.12 - % Of Faultless InstallationsRL.3.24 - % Orders/Lines Received Damage FreeRL.3.41 - Orders Delivered Damage Free ConformanceRL.3.42 - Orders Delivered Defect Free ConformanceRL.3.55 - Warranty and ReturnsAG.2.5 - Upside Return Adaptability (Deliver)CO.3.4 - Cost to Plan (Deliver)RS.3.125 - Select Supplier and Negotiate Cycle TimeAG.1.2 - Downside Supply Chain AdaptabilityCO.3.5 - Cost to Plan (Return)AM.3.28 - Percentage Defective InventoryRS.3.139 - Transfer Product Cycle TimeAG.2.6 - Downside Adaptability (Source)CO.2.2 - Cost to SourceAM.3.37 - Percentage Excess InventoryAG.2.7 - Downside Adaptability (Make)CO.3.6 - Cost to Authorize Supplier PaymentAM.3.44 - Percentage Unserviceable MRO InventoryCO.3.7 - Cost to Receive ProductAM.3.45 - Inventory Days of Supply ( Finished Goods )CO.3.8 - Cost to Schedule Product DeliveriesAM.2.3 - Days Payable OutstandingCO.3.9 - Cost to Transfer ProductAM.1.2 - Return on Supply Chain Fixed AssetsCO.3.10 - Cost to Verify ProductAM.2.4 - Supply Chain RevenueCO.2.3 - Cost to MakeAM.2.5 - Supply Chain Fixed AssetsCO.3.11 - Direct Material CostAM.3.11 - Fixed Asset Value (Deliver)CO.3.12 - Indirect Cost Related to ProductionAM.3.18 - Fixed Asset Value (Make)CO.3.13 - Direct Labor CostAM.3.20 - Fixed Asset Value (Plan)CO.2.4 - Cost to DeliverAM.3.24 - Fixed Asset Value (Return)RS.3.140 - Verify Product Cycle TimeRS.2.2 - Make Cycle TimeRS.3.33 - Finalize Production Engineering Cycle TimeRS.3.49 - Issue Material Cycle TimeRS.3.101 - Produce and Test Cycle TimeRS.3.114 - Release Finished Product to Deliver Cycle TimeRS.3.123 - Schedule Production Activities Cycle TimeRS.3.128 - Stage Finished Product Cycle TimeRS.3.142 - Package Cycle TimeRS.2.3 - Deliver Cycle TimeRS.3.16 - Build Loads Cycle TimeAG.1.3 - Overall Value at Risk (VAR)AG.2.9 - Supplier’s/Customer’s/ Product’s Risk RatingAG.2.10 - Value at Risk (Plan)AG.2.11 - Value at Risk (Source)AG.2.12 - Value at Risk (Make)AG.2.13 - Value at Risk (Deliver)AG.2.14 - Value at Risk (Return)AG.2.15 - Time to Recovery (TTR)CO.3.14 - Order Management CostsAM.3.27 - Fixed Asset Value (Source)CO.3.15 - Order Delivery and / or Install CostsAM.1.3 - Return on Working CapitalRS.3.46 - Install Product Cycle TimeCO.2.5 - Cost to ReturnAM.2.6 - Accounts Payable (Payables Outstanding)RS.3.51 - Load Product & Generate Shipping DocumentationCycle TimeCO.3.16 - Cost to Source ReturnAM.2.7 - Accounts Receivable (Sales Outstanding)CO.3.17 - Cost to Deliver ReturnAM.2.8 - InventoryRS.3.110 - Receive Product from Source or Make Cycle TimeRS.3.111 - Receive, Configure, Enter, & Validate Order Cycle TimeRS.3.116 - Reserve Resources and Determine Delivery DateCycle TimeCO.2.6 - Mitigation CostsCO.3.18 - Risk Mitigation Costs (Plan)CO.3.19 - Risk Mitigation Costs (Source)CO.3.20 - Risk Mitigation Costs (Make)RS.3.117 - Route Shipments Cycle TimeCO.3.21 - Risk Mitigation Costs (Deliver)RS.3.120 - Schedule Installation Cycle TimeCO.3.22 - Risk Mitigation Costs (Return)RS.3.124 - Select Carriers & Rate Shipments Cycle TimeCO.1.2 - Costs of Goods SoldRS.3.126 - Ship Product Cycle TimeCO.2.7 - Direct Labor CostRS.2.4 - Delivery Retail Cycle TimeCO.2.8 - Direct Material CostRS.3.17 - Checkout Cycle TimeCO.2.9 - Indirect Cost Related to ProductionRS.3.32 - Fill Shopping Cart Cycle TimeRS.3.34 - Generate Stocking Schedule Cycle TimeRS.3.97 - Pick Product from Backroom Cycle TimeRS.3.109 - Receive Product at Store Cycle TimeRS.3.129 - Stock Shelf Cycle TimeRS.2.5 - Return Cycle TimeSCOR 12.0 Quick Reference GuideAG.2.8 - Downside Adaptability (Deliver)RS.3.18 - Consolidate Orders Cycle TimeRS.3.102 - Receive & Verify Product by Customer Cycle Time5Asset Management Efficiency
About APICSAPICS is the association for supply chain management and the leading providerof research, education and certification programs that elevate supply chainexcellence, innovation and resilience. The APICS Certified in Production andInventory Management (CPIM); APICS Certified Supply Chain Professional(CSCP); APICS Certified in Logistics, Transportation and Distribution (CLTD);and APICS Supply Chain Operations Reference-Professional (SCOR-P)designations set the industry standard. With more than 45,000 members andapproximately 300 channel partners, APICS is transforming the way people dobusiness, drive growth and reach global customers.For more information, visit apics.org/scor. APICS 2017. All rights reserved. SCOR is a registered trademark in the United States and Europe.
People—Supply Chain Skills The people section introduced in SCOR 10.0 provides a means for managing talent in the supply chain by incorporating a standard for describing the expertise required to perform tasks and manage processes. The