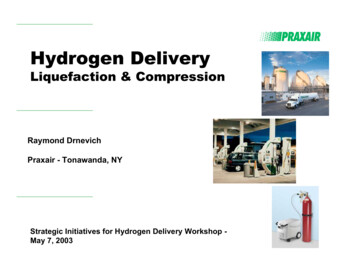
Transcription
Hydrogen DeliveryLiquefaction & CompressionRaymond DrnevichPraxair - Tonawanda, NYStrategic Initiatives for Hydrogen Delivery Workshop May 7, 2003
Agenda¾Introduction to Praxair¾Hydrogen Liquefaction¾Hydrogen Compression2
Praxair at a Glance¾¾The largest industrial gas company in Northand South AmericaOnly U.S. Hydrogen Supplier in All Sizes(Cylinders to Liquid to Pipelines)¾Operations in 40 countries¾Over 23,000 employees¾3,000 active patents¾One million customers worldwide3
Merchant Hydrogen PlantsPraxair Liquid Hydrogen PlantPraxair Tube Trailer Hydrogen PlantPraxair HGS PlantPraxair Cylinder Hydrogen Plant4
Gulf Coast Pipeline EERPARKBAYPORTBATON ALVESTONBAYTEXAS CITYGALVESTONGULF OFMEXICO245 miles of pipeline serving50 major customersHYDROGENNITROGENOXYGENAIR SEPARATIONPLANTSINDUSTRIALAREA5
Hydrogen Liquefaction¾There are 10 hydrogen liquefaction plants in North AmericazTrain size ranges from 6 to 35 TPD (5,400 to 32,000 kg/day)North American Liquid Hydrogen Capacity(TPD)300250200150100500196519701975Air r LiquideIn the 1960’s, liquid hydrogen plants were built to support theApollo program. Today, liquid hydrogen is used to reduce thecost of hydrogen distribution.zzDelivering a full tube trailer of hydrogen to a customer results in adelivery of less than 300 kgA modern liquid hydrogen trailer carries 4000 kg of liquid hydrogen6
Hydrogen LiquefactionH2 SourceH2 yogenicMembraneH2 LiquefactionCryogenic(-423ºF)7
Hydrogen Liquefaction¾The plants are very capital intensivezz¾The process is very energy intensivez¾Praxair has started capacity expansions approximately once every5 years since 1980. The infrequent builds means it’s very difficultto reproduce designs.While larger plants are more capital efficient, it’s hard to take thecapital risk of building the plant too large.Typical unit powers are on the order of 12.5 to 15 kWhe/kgThe cost stack looks like:100%75%50%25%0%CapitalSharePowerO&M8
Hydrogen LiquefactionProcess ReviewH2 Flash CompressorTo FeedH2 Recycle CompressorGN2 to N2LiquefierExternalRefrigerationLN2 Add.To Storage/Fill9
Forms of Liquid HydrogenOrtho-¾¾¾¾¾H -ParaH -H H -Normal Hydrogen is 75% Ortho, 25% ParaLiquid Hydrogen is 0.2% Ortho, 99.8% ParaHeat of Conversion from Normal to Para is 0.146 kWhth/kgHeat of Liquefaction is 0.123 kWhth/kgConversion can cause Vaporization10
Hydrogen LiquefactionIssues for Consideration¾Methods to decrease capital cost:zz¾Methods to decrease energy requirement:z¾Larger scale plants (850 tpd)Plant repeatabilityNew compression and expansion technology High speed centrifugal compressors and possibly expanders Materials development requiredSomething completely different?zNew approaches to low temperature refrigeration Magnetic refrigerators Acoustic refrigerators11
Challenges:¾More cost effective LH2 production systemszzzzz¾System modularization for traditional sized unitsLarger scale equipmentHigher efficiency compressors and expandersMore efficient refrigerationLower cost high-efficiency insulationCost effective small scale hydrogen generationzzzLow cost high pressure compressors and expandersNovel low-temperature refrigerationLow heat leak liquid storage units12
Hydrogen CompressionH2 ProductionSMRByproductGasificationRenewableH2 Purification H2 CompressionPSACryogenicMembraneSmallLarge13
Hydrogen Compression¾Hydrogen is difficult to compresszz¾Hydrogen compressors are expensivezzz¾Very small moleculePositive displacement compressors are usedMaterialsSizeRedundancy required for reliabilityThe process is energy intensivezTypical unit powers are:Inlet-Outlet(psig) Adiabatic Efficiency300 - 1,00070-80%100 - 7,00050-70%Compression Energy0.6 - 0.7 kWhe/kg2.6 - 3.6 kWhe/kg14
Issues Unique to HydrogenCompression¾Compressor Seal and Clearance Tolerancezz¾Hydrogen is the lightest of all the gases and haslower viscosity than NG. Hence, it is easier to migratethrough small spacesSpecial seals and/or tolerance standards need to beestablished to achieve high pressuresHydrogen Embrittlement of MetalszzzAt elevated pressure and temperature, hydrogen canpermeate carbon steel resulting in decarburizationConventional Mild Steel has been used in Germanyand France since 1938 as pipeline material.Alloy steels containing Chromium and Molybdenumhave been suggested for compressor materials.15
Hydrogen Compression for LargeScale Pipeline Delivery (Present)¾State of the Artzzzz¾Multi-Stage Reciprocating Machines- typical to install redundant units inorder to keep on-line time between98-99%.700 - 1000 psig delivery pressuresAdiabatic efficiencies of 78-80%High maintenance costs due towearing components (e.g. valves,rider bands, piston rings)Typical ManufacturerszzzzDresser-RandSulzer BurckhardtArielNeuman-Esser16
Hydrogen Compression for SmallScale Fueling Stations (Present)¾State of the Artzzzz¾V-Belt driven multi-stage reciprocatingHydraulically driven multi-stagereciprocatingV-Belt driven diaphragm5,000 - 10,000 psig delivery pressuresTypical eldRixHydro-PacCompAir17
Hydrogen Compression for SmallScale Fueling Stations (Present)Compressor Cost Comparison(6000 psig) 120,000 100,000 80,000 60,000 40,000 20,000 0Type A - 1Type B - 1Type C - 1Type C - 10018
Hydrogen CompressionIssues for Consideration¾Issue of numbers - what happens if we build 100times the units we build today:zz¾¾¾Cost impact on current technologyPotential for new technologyReliability improvementsMaintenance cost reductionMethods to decrease energy requirement:zzNew mechanical conceptsNon-traditional approaches to compression19
Hydrogen Compression (Future)¾Newer ApproacheszzMechanical Guided Rotor Compressor (GRC) Linear CompressorNon-Traditional Electrically Driven Membranes Hydride Compressors20
6 Hydrogen Liquefaction ¾There are 10 hydrogen liquefaction plants in North America zTrain size ranges from 6 to 35 TPD (5,400 to 32,000 kg/day) ¾In the 1960’s, liquid hydrogen plants were built to support the Apollo program. Today, liquid hydrogen is used to reduce the cost of hydrogen distribution. zDelivering a full tube traile