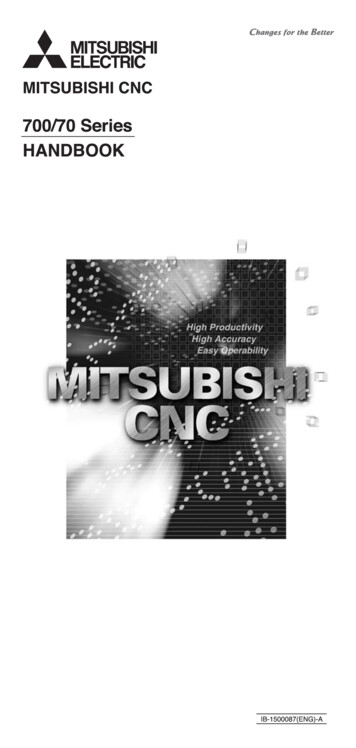
Transcription
ContentsI Alarms1. Operation Alarms (M) .I - 12. Stop Codes (T) .I - 83. Servo/Spindle Alarms .I - 123.1 Servo alarm (S01/S03/S04) .I - 123.2 Initial parameter error (S02) .I - 273.3 Parameter error (S51) .I - 273.4 Servo warning (S52) .I - 284. MCP Alarm (Y) .I - 305. System Alarms (Z) .I - 376. Absolute Position Detection System Alarms (Z7*) .I - 407. Distance-coded Reference Scale Errors (Z8*) .I - 428. Messages during Emergency Stop (EMG) .I - 439. Auxiliary Axis Alarms .I - 459.1 Aux ax servo alarm/warning (S) .I - 459.2 Aux ax abs position error (Z) .I - 489.3 Aux ax operation error (M) .I - 499.4 Auxiliary axis MCP alarms (Y) .I - 5010. Computer Link Errors (L) .I - 5111. User PLC Alarms (U) .I - 5212. Network Service Errors (N) .I - 5413. Program Errors (P) .I - 55II Parameters1. User Parameters .II - 12. Base Specifications Parameters .II - 393. Axis Specifications Parameters .II - 824. Servo Parameters .II - 995. Spindle Parameters .II - 1146. Rotary Axis Configuration Parameters .II - 1487. Machine Error Compensation .II - 1538. PLC Constants .II - 1549. Macro List .II - 15510. Position Switch .II - 16211. Auxiliary Axis Parameter .II - 17212. Open Parameter .II - 18513. CC-Link Parameter .II - 18614. Anshin-net Parameter 2 / MTB-net Parameter 2 .II - 19415. PLC Axis Parameters .II - 202III PLC Devices1. Bit Type Input Signals (CNC- PLC).III - 12. Data Type Input Signals (CNC- PLC) .III - 203. Bit Type Output Signals (PLC- CNC).III - 384. Data Type Output Signals (PLC- CNC) .III - 635. Each Application : Pallet Program Registration .III - 726. Each Application : PLC Axis Indexing .III - 737. Each Application : Tool Life Management Interface.III - 748. Special Relays .III - 77
I Alarms
I Alarms1. Operation Alarms (M)1. Operation Alarms (M)M01 Dog overrun 0001DetailsRemedyWhen returning to the reference position, the near-point detection limit switch did not stopover the dog, but overran the dog.- Increase the length of the near-point dog.- Reduce the reference position return speed.M01 Some ax does not pass Z phase 0002DetailsRemedyOne of the axes did not pass the Z-phase during the initial reference position return after thepower was turned ON.- Move the detector one rotation or more in the opposite direction of the reference position,and repeat reference position return.M01 R-pnt direction illegal 0003DetailsRemedyWhen manually returning to the reference position, the return direction differs from the axismovement direction selected with the AXIS SELECTION key.- The selection of the AXIS SELECTION key's /- direction is incorrect. The error is canceledby feeding the axis in the correct direction.M01 External interlock axis exists 0004DetailsRemedyThe external interlock function has activated (the input signal is "OFF") and one of the axeshas entered the interlock state.- As the interlock function has activated, release it before resuming operation.- Correct the sequence on the machine side.- Check for any broken wires in the "interlock" signal line.M01 Internal interlock axis exists 0005DetailsRemedyThe internal interlock state has been entered.The absolute position detector axis has been removed.A command for the manual/automatic simultaneous valid axis was issued from the automaticmode.The manual speed command was issued while the "tool length measurement 1" signal is ON.- The servo OFF function is valid, so release it first.- An axis that can be removed has been issued, so perform the correct operations.- The command is issued in the same direction as the direction where manual skip turnedON, so perform the correct operations.- During the manual/automatic simultaneous mode, the axis commanded in the automaticmode became the manual operation axis. Turn OFF the "manual/automatic valid" signal forthe commanded axis.- Turn ON the power again, and perform absolute position initialization.- Turn OFF the "tool length measurement 1" signal to start the program by the manual speedcommand.M01 H/W stroke end axis exists 0006DetailsRemedyThe stroke end function has activated (the input signal is "OFF") and one of the axes is in thestroke end status.- Move the machine manually.- Check for any broken wires in the "stroke end" signal line.- Check for any limit switch failure.M01 S/W stroke end axis exists 0007DetailsRemedyThe stored stroke limit I, II, IIB or IB function has activated.- Move the machine manually.- Correct any setting error of the parameters for the stored stroke limit.M01 Chuck/tailstock stroke end ax 0008DetailsRemedyThe chuck/tail-stock barrier function turned ON, and an axis entered the stroke end state.- Reset the alarm with reset, and move the machine in the reverse direction.M01 Ref point return No. invalid 0009DetailsRemedy2nd reference position return was performed before 1st reference position return has beencompleted.- Execute 1st reference position return.M01 Sensor signal illegal ON 0019DetailsThe sensor signal was already ON when the "tool length measurement 1" signal wasvalidated.The sensor signal turned ON when there was no axis movement after the "tool lengthmeasurement 1" signal was validated.The sensor signal turned ON at a position within 100?m from the final entry start position.Remedy- Disable the "tool length measurement 1" signal and move the axis in a safe direction.- Disabling the sensor signal also clears the operation alarm.(Note) When the "tool length measurement 1" signal is disabled, the axis can be moved ineither direction. Pay attention to the movement direction.M01 Ref point retract invalid 0020DetailsRemedyReference position retract was performed while the coordinates had not been established.- Execute reference position return.I-1
I Alarms1. Operation Alarms (M)M01 Tool ofs invld after R-pnt 0021DetailsRemedyReference position return had been performed during the tool escape and return, whichinvalidated the tool compensation amount after the reference position return.- The error is cleared if the operation mode is changed to other than reference positionreturn before the axis performs reference position return.- The error is cleared when the tool return is completed.- The error is cleared if reset 1 is input or the emergency stop button is pushed.M01 R-pnt ret invld at abs pos alm 0024DetailsRemedyA reference position return signal was enabled during an absolute position detection alarm.- Reset the absolute position detection alarm, and then perform the reference positionreturn.M01 R-pnt ret invld at zero pt ini 0025DetailsRemedyA reference position return signal was input during zero point initialization of the absoluteposition detection system.- Complete the zero point initialization, and then perform reference position return.M01 Now skip on 0030DetailsRemedyThe "skip input" signal remains enabled when the operation has shifted from skip retract tomeasurement.- Increase the skip retract amount.M01 No skip 0031DetailsRemedyEven though the 1st skip was to the correct position, the 2nd skip could not be found.- Check whether the measurement target has moved.M01 Operation error 0035DetailsMovement prohibited during tool retractAn axis movement was attempted from the tool retract position.The movement was attempted by a manual command in the tool return.RemedyIt is not allowed to move an axis arbitrarily from the tool retract position. Take the followingsteps to move the axis.- Cancel the program execution by reset.- Use the tool escape and retract function and let the axis escape from the tool retractposition.The interruption by a manual command is not allowed in a tool return. Take the following stepto move the axis.- Cancel the program execution by reset.M01 Chopping axis R-pnt incomplete 0050DetailsRemedyChopping mode has been entered while the chopping axis has not completed referenceposition return.All axes interlock has been applied.- Reset the NC or disable the "chopping" signal, and then carry out the reference positionreturn.M01 Synchronous error excessive 0051DetailsRemedyThe synchronization error of the master and slave axes exceeded the allowable value undersynchronous control.A deviation exceeding the synchronization error limit value was found with thesynchronization deviation detection.- Select the correction mode and move one of the axes in the direction in which the errorsare reduced.- Set a larger value or "0" for "#2024 synerr (Allowable error)" to disable the error check.- When using simple C-axis synchronous control, set "0" for "synchronous control operationmethod".M01 No spindle select signal 0053DetailsRemedySynchronous tapping command was issued when the "spindle selection" signals for allspindles were OFF in the multiple-spindle control II.- Turn ON the "spindle selection" signal for the tapping spindle before performing thesynchronous tapping command.M01 No spindle serial connection 0054DetailsRemedySynchronous tapping command was issued in the multiple-spindle control II, while thespindle with the "spindle selection" signal ON was not serially connected.- Make sure the "spindle selection" signal for the spindle is ON.- Consider the machine construction when issuing the command.M01 Spindle fwd/rvs run para err 0055DetailsRemedyAsynchronous tapping command was issued when M code of the spindle forward/reverse runcommand, set by "#3028 sprcmm", was one of the followings in the multiple-spindle control II.- M0, M1, M2, M30, M98, M99, or M198- M code No. that commands to enable/disable the "macro interrupt" signal- Correct the "#3028 sprcmm (Tap cycle spindle forward run/reverse run M command)"setting.I-2
I Alarms1. Operation Alarms (M)M01 Tap pitch/thread number error 0056DetailsRemedyThe command for the pitch or the number of threads is not correct in the synchronoustapping command of the multiple-spindle control II.The pitch is too small for the spindle rotation speed.Thread number is too large for the spindle rotation speed.- Correct the pitch, number of threads or rotation speed of the tapping spindle.M01 Handle ratio too large 0060DetailsRemedyHandle ratio is too large for the rapid traverse rate (or external deceleration speed whenexternal deceleration is valid).- Set a smaller ratio.M01 R-pos offset value illegal 0065DetailsRemedyAt the start of reference position initial setting, "#2034 rfpofs (Distance-coded referenceposition detection offset) is not set to "0".- Set "#2034 rfpofs" to "0", then turn the power ON again to perform the reference positioninitial setting.M01 R-pos scan distance exceeded 0066DetailsRemedyReference position could not be established within the maximum scan distance.- Check the scale to see if it has dirt or damage.- Check if the servo drive unit supports this function.M01 No operation mode 0101DetailsRemedy- Check for any broken wires in the input mode signal line.- Check for any failure of the MODE SELECT switch.- Correct the sequence program.M01 Cutting override zero 0102DetailsRemedyThe "cutting feed override" switch on the machine operation panel is set to"0".The override was set to "0" during a single block stop.- Set the "cutting feed override" switch to a value other than "0" to clear the error.- If the "cutting feed override" switch has been set to a value other than "0", check for anyshort circuit in the signal line.- Correct the sequence program.M01 External feed rate zero 0103DetailsRemedyMANUAL FEED
I Alarms 1. Operation Alarms (M) I - 1 1. Operation Alarms (M) M01 Dog overrun 0001 Details When returning to the reference position, the near-point detection limit switch did not stop over the dog, but overran the dog. Remedy - Increase the length of the near-point dog. -