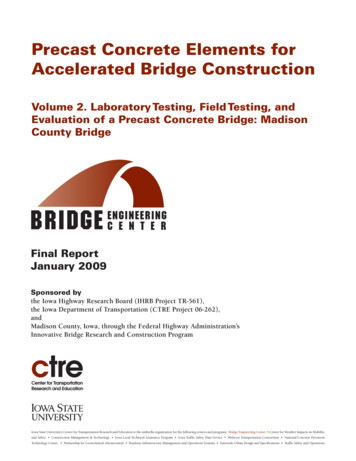
Transcription
Precast Concrete Elements forAccelerated Bridge ConstructionVolume 2. Laboratory Testing, Field Testing, andEvaluation of a Precast Concrete Bridge: MadisonCounty BridgeFinal ReportJanuary 2009Sponsored bythe Iowa Highway Research Board (IHRB Project TR-561),the Iowa Department of Transportation (CTRE Project 06-262),andMadison County, Iowa, through the Federal Highway Administration’sInnovative Bridge Research and Construction ProgramIowa State University’s Center for Transportation Research and Education is the umbrella organization for the following centers and programs: Bridge Engineering Center Center for Weather Impacts on Mobilityand Safety Construction Management & Technology Iowa Local Technical Assistance Program Iowa Traffic Safety Data Service Midwest Transportation Consortium National Concrete PavementTechnology Center Partnership for Geotechnical Advancement Roadway Infrastructure Management and Operations Systems Statewide Urban Design and Specifications Traffic Safety and Operations
About the Bridge Engineering CenterThe mission of the Bridge Engineering Center is to conduct research on bridge technologies tohelp bridge designers/owners design, build, and maintain long-lasting bridges.Disclaimer NoticeThe contents of this report reflect the views of the authors, who are responsible for the factsand the accuracy of the information presented herein. The opinions, findings and conclusionsexpressed in this publication are those of the authors and not necessarily those of the sponsors.The sponsors assume no liability for the contents or use of the information contained in thisdocument. This report does not constitute a standard, specification, or regulation.The sponsors do not endorse products or manufacturers. Trademarks or manufacturers’ namesappear in this report only because they are considered essential to the objective of the document.Nondiscrimination StatementIowa State University does not discriminate on the basis of race, color, age, religion, nationalorigin, sexual orientation, gender identity, sex, marital status, disability, or status as a U.S.veteran. Inquiries can be directed to the Director of Equal Opportunity and Diversity,(515) 294-7612.
GENERAL ABSTRACTPrecast Concrete Elements for Accelerated Bridge ConstructionPrecast concrete elements and accelerated bridge construction techniques have the potential toimprove the health of the U.S. highway system. In precast bridge construction, the individualcomponents are manufactured off-site and assembled on-site. This method usually increases thecomponents’ durability, reduces on-site work and construction time, minimizes traffic disruption,and lowers life-cycle costs. Before widespread implementation, however, the benefits of precastelements and accelerated bridge construction must be verified in the laboratory and field.For this project, precast bridge elements and accelerated bridge construction techniques wereinvestigated in the laboratory and at three bridge projects in Iowa: in Boone County, MadisonCounty, and Black Hawk County. The objectives were to evaluate the precast bridge elements,monitor the long-term performance of the completed bridges, and evaluate accelerated bridgeconstruction techniques.The results of these investigations are presented in three volumes, as described below; thisvolume is Volume 2.Vol. 1-1. Laboratory Testing of Precast Substructure Components: Boone County Bridge1-2. Laboratory Testing of Full-Depth Precast, Prestressed Concrete Deck Panels:Boone County Bridge1-3. Field Testing of a Precast Concrete Bridge: Boone County BridgeIn 2006, a continuous four-girder, three-span bridge was constructed that included precastabutments, pier cap elements, prestressed beams, and precast full-depth deck panels. All ofthe precast elements performed well during strength testing and were set quickly andsmoothly during construction, and the completed bridge experienced very smalldisplacements and strains when subjected to live loads.Vol. 2. Laboratory Testing, Field Testing, and Evaluation of a Precast Concrete Bridge:Madison County BridgeIn 2007, a two-lane single-span bridge was constructed that had precast box girders withprecast abutments. The elements performed well during laboratory load transfer andstrength testing, and the completed bridge performed well in terms of maximum deflectionsand differential displacements between longitudinal girder joints.Vol. 3. Laboratory Testing, Field Testing, and Evaluation of a Precast Concrete Bridge:Black Hawk CountyIn 2007, two precast modified beam-in-slab bridge (PMBISB) systems were constructed,each of which included precast abutment caps, backwalls, and deck panels. Various deckpanel configurations transferred load effectively during laboratory testing, and all precastelements met expectations. The completed bridges experienced very low induced stressesand met AASHTO deflection criteria, while the PMBSIB system effectively transferredload transversely.
Technical Report Documentation Page1. Report No.IHRB Project TR-5612. Government Accession No.3. Recipient’s Catalog No.4. Title and SubtitlePrecast Concrete Elements for Accelerated Bridge Construction: LaboratoryTesting, Field Testing, Evaluation of a Precast Concrete Bridge, Madison CountyBridge5. Report DateJanuary 20097. Author(s)Brent Phares, Terry Wipf, Jake Bigelow, Ryan Bowers, and F. Wayne Klaiber8. Performing Organization Report No.CTRE Project 06-2629. Performing Organization Name and AddressBridge Engineering CenterIowa State University2711 South Loop Drive, Suite 4700Ames, IA 50010-866410. Work Unit No. (TRAIS)12. Sponsoring Organization Name and AddressIowa Highway Research BoardIowa Department of Transportation800 Lincoln WayAmes, IA 500106. Performing Organization Code11. Contract or Grant No.13. Type of Report and Period CoveredFinal Report14. Sponsoring Agency Code15. Supplementary NotesVisit www.ctre.iastate.edu for color PDF files of this and other research reports.16. AbstractThe importance of rapid construction technologies has been recognized by the Federal Highway Administration (FHWA) and the IowaDOT Office of Bridges and Structures. Recognizing this a two-lane single-span precast box girder bridge was constructed in 2007 overa stream. The bridge’s precast elements included precast cap beams and precast box girders. Precast element fabrication and bridgeconstruction were observed, two precast box girders were tested in the laboratory, and the completed bridge was field tested in 2007 and2008.17. Key Wordsaccelerated bridge construction—Boone County, Iowa—field testing—laboratorystrength testing—precast concrete box girders and abutments18. Distribution StatementNo restrictions.19. Security Classification (of thisreport)Unclassified.21. No. of Pages22. Price96NA20. Security Classification (of thispage)Unclassified.
PRECAST CONCRETE ELEMENTS FORACCELERATED BRIDGE CONSTRUCTION:LABORATORY TESTING, FIELD TESTING, EVALUATION OF APRECAST CONCRETE BRIDGE, MADISON COUNTY BRIDGEFinal ReportJanuary 2009Co-Principal InvestigatorsTerry J. Wipf, Director, Bridge Engineering CenterCenter for Transportation Research and Education, Iowa State UniversityBrent M. Phares, Associate Director, Bridge Engineering CenterCenter for Transportation Research and Education, Iowa State UniversityF. Wayne Klaiber, Professor, Department of Civil, Construction, and Environmental EngineeringIowa State UniversityResearch AssistantRyan P. BowersAuthorsBrent Phares, Terry Wipf, Jake Bigelow, Ryan P. Bowers, and F. Wayne KlaiberSponsored bythe Iowa Highway Research Board (IHRB Project TR-561)and Madison County, Iowa,through the Federal Highway Administration’sInnovative Bridge Research and Construction ProgramPreparation of this report was financed in partthrough funds provided by the Iowa Department of Transportationthrough its research management agreement with theCenter for Transportation Research and Education (CTRE Project 06-262).Center for Transportation Research and EducationIowa State University2711 South Loop Drive, Suite 4700Ames, IA 50010-8664Phone: 515-294-8103Fax: 515-294-0467www.ctre.iastate.edu
TABLE OF CONTENTSACKNOWLEDGMENTS . XIEXECUTIVE SUMMARY .XIII1 . GENERAL INFORMATION .11.1 Introduction .11.2 Background .11.3 Objectives and Scope .22 . BRIDGE DESCRIPTION .32.1 Box Girder Properties .52.2 Fabrication Observations .92.3 Field Construction Observations .123 . LABORATORY TESTING.153.1 Concrete Strength Test.153.2 Variable Post-Tensioning Force Test .163.3 Flexural Strength Test .183.4 Shear Strength Test .193.5 Guardrail Connection Test .224 . LABORATORY TEST RESULTS .244.1 Concrete Strength Test Results .244.2 Variable Post-Tensioning Force Test Results .244.3 Flexural Strength Test Results .284.4 Shear Strength Test Results .334.5 Guardrail Connection Test Results .365 . FIELD TESTING.435.1 Evaluation methodology and instrumentation .436 . FIELD TEST RESULTS .476.1 Static Loading .476.2 Dynamic Loading.606.3 Corrosion Monitoring .647 . CONCLUSIONS AND RECOMMENDATIONS .66REFERENCES .68APPENDIX A. MADISON COUNTY BOX GIRDER BRIDGE PLANS . A-1v
LIST OF FIGURESFigure 2.1. Location of Madison Co. precast bridge .3Figure 2.2. Photographs of Madison Co. precast bridge .3Figure 2.3. Plan and section of bridge .4Figure 2.4. Photograph of bridge guardrail system .5Figure 2.5. Box girder dimensions.6Figure 2.5. Box girder reinforcement layout .7Figure 2.6. Box girder guardrail properties .9Figure 2.7. Photograph of box girder form with bottom pretension strands .10Figure 2.8. Photograph of top of beam reinforcing and foam core.10Figure 2.9. Photograph of end reinforcing and lift points .11Figure 2.10. Photograph of midspan transverse tie duct.11Figure 2.11. Photograph of crew lifting girder out of forms .12Figure 2.12. Photographs of precast pile cap beam installation .12Figure 2.13. Photographs of box girder placement sequence .14Figure 3.1. Photograph of a precast box girder used for laboratory testing .15Figure 3.2. Box girder concrete core locations .15Figure 3.3. Photographs of laboratory setup for variable post-tensioning force tests .16Figure 3.4. Variable post-tensioning loading locations .17Figure 3.5. Photograph of tandem wheel footprint used during the variable post-tensioning forcetests .18Figure 3.6. Instrumentation grid for variable post-tensioning force tests.18Figure 3.7. Laboratory setup to test flexural strength of a box girder .19Figure 3.8. Instrumentation locations .19Figure 3.9. Shear strength test setup .20Figure 3.10. Transducer and concrete strain gage grid for shear strength test .21Figure 3.11. Rosette layout for shear strength test .21Figure 3.12. Guardrail connection test load locations .22Figure 3.13. Guardrail connection test setup .22Figure 3.14. Guardrail post instrumentation .23Figure 4.1. Total strain at midspan with load at D1 and a post-tensioning force of 17 kips .24Figure 4.2. Deflection results at point D1 with a 17 kip post-tensioning force .25Figure 4.3. Load fractions at midspan for various post-tensioning forces and load at D1 .26Figure 4.4. Load fractions at quarterspan for various post-tensioning forces and load at D1 .27Figure 4.5. Load fractions at midspan for various post-tensioning forces and load at B1 .27Figure 4.6. Load fractions at quarterspan for various post-tensioning forces and load at B1 .28Figure 4.7. Photograph of flexural cracking after flexure test .29Figure 4.8. Moment at midspan of the box girder .30Figure 4.9. Tensile stress at midspan of the box girder .30Figure 4.10. Total compressive stress at midspan of the box girder .31Figure 4.11. Compressive stress due to applied load and one-half the dead load and prestressingforce at midspan of the box girder .32Figure 4.12. Deflection versus load plot for box girder flexural strength test.32Figure 4.13. Photographs of box girder after shear failure .33Figure 4.14. Shear force in the box girder .34Figure 4.15. Principle strains due to applied load at rosette 2N during shear strength testing .34vii
Figure 4.16. Principal stresses due to the total load at rosette 2N .35Figure 4.17. Theoretical and experimental deflections at quarterspan during shear test .36Figure 4.18. Photographs of failed guardrail connection elements .36Figure 4.19. Post deflections during test 1.38Figure 4.20. Deflected shape of the top of the guardrail at failure .39Figure 4.21. Post strains during test 1 .39Figure 4.22. Post displacements for test 2 .40Figure 4.23. Deflected shape of the guardrail during test 2 .41Figure 4.24. Photograph of deflected guardrail during test 4 .41Figure 4.25. Post strains during test 2 .42Figure 5.1. Instrumentation layout .43Figure 5.2. Transverse load positions: Vehicle traveled west into page .45Figure 5.3. Madison County load truck .46Figure 5.4. Vehicle configuration and axle loads .46Figure 6.1. Representative time history deflections .48Figure 6.2. 2007 and 2008 transverse deflected shape at midspan and quarterspan .49Figure 6.3. 2007 and 2008 differential deflections .52Figure 6.4. 2007 Experimental strains; LC 7 .55Figure 6.5. 2008 Experimental strains; LC 7 .55Figure 6.6. 2007 Experimental and analytical strain comparison; LC 3 .56Figure 6.7. 2008 Experimental and analytical strain comparison; LC 3 .57Figure 6.8. Experimentally obtain load fraction .
Precast Concrete Elements for Accelerated Bridge Construction Precast concrete elements and accelerated bridge construction techniques have the potential to improve the health of the U.S. highway system. In precast bridge construction, the individual components are manufactured off-site