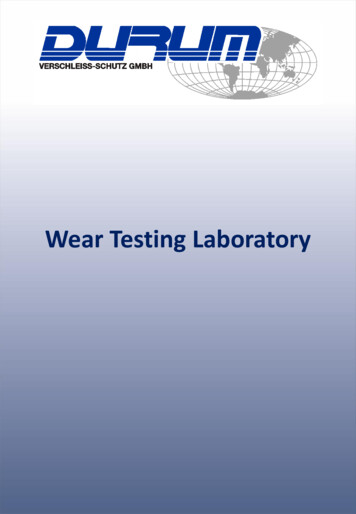
Transcription
Wear Testing Laboratory
Friction wheel testASTM G65-04(dry sand/ rubber wheel test)Principle of dry sand/ rubber wheel test:Test parameters(Mod A):wear distance:4,309 mabrasive:quartz sand (F50/70)abrasive flow:320 – 370 g/mincontact force:130 Ndiamater wheel:214.9 – 228.6 mmRotational speed:200 rpm standardized test procedure offers a broad spectrum of materials to testModificationA (materials with medium and high hardness)B (short Version of A)C (thin coatings)D (materials with low wear resistance)E (short version of A)contact force [N] wear distance [m]130130130451304,3091,43671.84,309718The specimens are weighed before and after the testand the wear is reported in mm³.
Friction wheel testASTM G65-04(dry sand/ rubber wheel test)Abstract/ Scope*:„This test method covers laboratory procedures for determining the resistance ofmetallic materials to scratching abrasion by means of the dry sand/rubber wheeltest. It is the intent of this test method to produce data that will reproducibly rankmaterials in their resistance to scratching abrasion under a specified set ofconditions.”„Abrasion test results are reported as volume loss in cubic millimetres for theparticular test procedure specified. Materials of higher abrasion resistance willhave a lower volume loss.“„The dry sand/rubber wheel abrasion test involves the abrading of a standard testspecimen with a grit of controlled size and composition. The abrasive isintroduced between the test specimen and a rotating wheel with a chlorobutylrubber tire or rim of a specified hardness. This test specimen is pressed againstthe rotating wheel at a specified force by means of a lever arm while a controlledflow of grit abrades the test surface. The rotation of the wheel is such that itscontact face moves in the direction of the sand flow. Note that the pivot axis ofthe lever arm lies within a plane which is approximately tangent to the rubberwheel surface, and normal to the horizontal diameter along which the load isapplied. The test duration and force applied by the lever arm is varied as noted inProcedure A through E. Specimens are weighed before and after the test and theloss in mass recorded. It is necessary to convert the mass loss to volume loss incubic millimetres, due to the wide differences in the density of materials.Abrasion is reported as volume loss per specified procedure.”* extracts of ASTM G65 - 00
Miller testASTM G75- comparable worldwide- high amount of variations of solid-fluid-mixturePrinciple and test parameters:motor-driven rotor causes the oscillating movement ofthe specimen by an eccentric fitted connecting rodTwo ways to run the test:1) standardized slurry abrasiv resistance of the material2) standardized specimen abrasiveness of the slurryThe specimens are weighed before and after the testand the wear is reported in mm³.
Miller testASTM G75Abstract/ Scope*:“This test method covers a single laboratory procedure that can be used todevelop data from which either the relative abrasivity of any slurry (MillerNumber) or the response of different materials to the abrasivity of differentslurries (SAR number), can be determined.”“The test data obtained by this procedure is used to calculate either a numberrelated to the rate of mass loss of duplicate standard-shaped 27% chromium ironwear blocks when run for a period of time in the slurry of interest (MillerNumber), or calculate a number related to the rate of mass loss (converted tovolume loss) of duplicate standard-shaped wear specimens of any material ofinterest when run a period of time in any slurry of interest (SAR number).”“The requirement for a finished flat wearing surface on the test specimen for aSAR Number test may preclude application of the procedure where thin (0.051 to0.127 mm), hard, wear-resistant coatings will not allow for surface finishing. The 6hours total duration of the SAR Number Test may not allow establishment of aconsistent rate-of-mass-loss of the unfinished surface.”“The relative effect of slurry abrasivity in both the Miller Number and the SARNumber is determined by using the measured mass loss of a standard-shaped 27%chromium iron metal wear block (Miller Number); or a metal, ceramic, composite,plastic, or elastomer wear specimen (SAR Number), driven in a reciprocatingmotion by a rotating crank, riding in the bottom of a trough containing the slurry.A direct load is applied to the wear block or wear specimen. For each test, thebottom of the trough is equipped with a new piece of a sheet of Neoprene to actas a lap. The interior of the trough has a flat-bottomed or truncated “V” shapetrough that confines the slurry particles to the path taken by the wear block orwear specimen. At one end of each stroke, the wear block or wear specimen islifted off the lap by a cam action for sufficient time to allow fresh slurry materialto flow under the wear block or wear specimen.”* extracts of ASTM G75 - 07
Miller testASTM G75Friction wheel testASTM G65-04(dry sand/ rubber wheel test)
ASTM G65-04 (dry sand/ rubber wheel test) Abstract/ Scope*: „This test method covers laboratory procedures for determining the resistance of metallic materials to scratching abrasion by means of the dry sand/rubber wheel test. It is the intent of thi