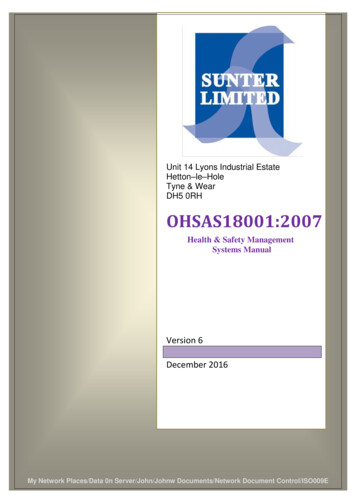
Transcription
Unit 14 Lyons Industrial EstateHetton–le–HoleTyne & WearDH5 0RHOHSAS18001:2007Health & Safety ManagementSystems ManualVersion 6December 2016My Network Places/Data on Server/John/John Documents/Network Document Control/ISO009CMy Network Places/Data 0n Server/John/Johnw Documents/Network Document Control/ISO009E
Health & Safety ManagementSystem ManualDateVersion 0.201502.12.2016123456DevelopedbyJohn WalkerJohn WalkerJohn WalkerJohn WalkerJohn WalkerJohn WalkerIssuedbyJohn WalkerJohn WalkerJohn WalkerJohn WalkerJohn WalkerJohn WalkerINTRODUCTIONThis Manual has been written in accordance with the OHSAS18001:2007 Standard. Theaim of the manual is to outline the internal procedures in place to effectively carry outthe requirements of the Standard.The OHSAS18001:2007 Standard will be implemented on all Company undertakings.This manual will be adapted and new revisions will be made once identified or if andwhen new legislation and/or work procedures demand it, any revision will overwrite anyprevious versions.The OHSAS18001:2007 Health & Safety Management Standard is overseen for theCompany by the Health, Safety & Environmental Manager. Any questions and/orqueries on this manual and/or on any Health & Safety Issue should be directed too:Mr John WalkerHealth, Safety & Environmental ManagerUnit 14Hetton Lyons Industrial EstateHetton-le-HoleTyne & WearDH5 0RHTel 0191 526 8106Mobile 07891 289 235Email john@sunters.comDecember 20161Version 6
Health & Safety ManagementSystem ManualHS.1OHSAS18001Clause Number 4.1GENERAL REQUIREMENTSDecember 20162Version 6
Health & Safety ManagementSystem ManualSUNTER LTD GENERAL HEALTH & SAFETY STATEMENTSunter limited subscribes to the Health & Safety Policy in place and is committed toimplementing and maintaining a Health & Safety System conforming to OHSAS18001:2007throughout the whole of the company’s undertaking and at all of its premises and work sites.SUNTER LTD HEALTH & SAFETY DIRECTIONOur aim is to monitor and continuously improve on our health & safety performance, and thecompany is committed to achieving this by: Complying with all relevant health & safety regulations, ACOPS and other legislativedocuments and/or requirements, codes of practice, corporate policies and protocols,as a minimum. Co-operating with Client, Local Authority and Housing Associations with regards to allaspects that could or have an adverse effect on the health & safety and the protectionof individuals, groups and property. Develop and implement Safe Working Practices in all undertakings, by the provision ofInformation, Instruction & Supervision to ALL Employees as well as Contractors taskedto carry out undertakings on the company’s behalf, this is achieved by the provision of:o Generic Risk Assessmentso Site Specific Risk Assessmentso Work Method Statementso COSHH Assessmentso Any Other Training: Provide suitable and sufficient training to enable employees and contractorsto carry out their work activities without hazard and/or risk, including:o Initial Company Inductiono Site Inductiono Tool Box Talkso Safety Presentationso Trade Specific Industry Standard trainingo CSCS Cards and Health & Safety Testingo Any Other Develop and maintain continuous improvement of our health & safety performance,addressing all aspects of works, which include:o Site Supervision & Managemento Plumbing & Heating Operationso Joinery Operationso Plastering & Wall Tiling Operationso General Operative Operationso Stores Operationso Trainees & Apprentice Supervision & Managemento Any other Fully integrate health & safety considerations into all aspects of the company’sundertakings to minimise any adverse effects, as far as is reasonably practicable.Internal audit and review of the health & safety management system shall ensure that thesystem remains effective and meets OHSAS18001:2007 standards throughout the Company.This Health & Safety System Manual will be made known to all our employees and tomembers of the public and interested parties upon request.December 20163Version 6
Health & Safety ManagementSystem ManualINDEX OF BUSINESS 1HS.11HS.12General RequirementsHealth & Safety PolicyPlanningImplementation & OperationCheckingManagement ReviewORGANISATION CHART & HEALTH & SAFETY MANAGEMENT RESPONSIBILITESManaging Director(Mr Terry Sunter)Directors(Mr Lee Sunter)(Mrs Maureen Sunter)(Mr Kevin Stubbs)Internal Auditor(s)Safety ManagerLead ISO/OHSAS Auditor(Mr John Walker)Site ManagersOffice ManagerStores ManagerSite StaffOffice StaffStores StaffDecember 20164Version 6
Health & Safety ManagementSystem ManualRESPONSIBILITIESManaging Director – Acting as Safety Director - To provide funding and “Top Management”responsibilities to ensure that the Health & Safety System is implemented.Directors – To assist the Managing Director in his “Top Management” responsibilities and toensure all Managers and other Staff are aware that they must co-operate in Internal andExternal Audits and implement and manage any other aspects of the Standard.Safety Manager – To devise, manage, maintain and implement the Health & Safety Systemand to inform the Directors/Managing Director of their responsibilities in ensuring the system isfully complied with. To act as the Lead Auditor and schedule Internal Audits and liaise with theExternal Auditor in his/her Audit requirements.Internal Auditors – To carry out Internal Audits to ensure that the Standard is implementedand up-to date. Report any non-conformities or non-co-operation to the Lead Auditor orCompany Director.Site Managers – To ensure that any site under their control implements all requirements ofthe standard and any non-conformity are acted upon and reported to the Safety Manager.Site Staff – To implement all aspects of the standard during their daily work duties, reportingto the Site Manager and item(s) that they feel may need attention or alteration.Stores Manager – To ensure that all materials are stores in a safe manner and that all health& safety requirements are implemented within the stores and all stores procedures.Stores Staff – To comply with the requirements and instructions given on Health & Safetyissues by the Stores Manager or any Senior Member of Staff.Office Manager – To ensure that all requirements of the Standard are implemented within theoffice environment.Office Staff – To comply with the requirements and instructions given on health & safetyissues by the Office Manager or any Senior Member of Staff.Others (Visitors etc) – To comply with any information given with regards to health & safetymatters whilst on company premises.December 20165Version 6
Health & Safety ManagementSystem ManualHS.2OHSAS18001Clause Number 4.2HEALTH & SAFETY POLICYSTATEMENTDecember 20166Version 6
Health & Safety ManagementSystem ManualDate08.08.201116.08.2013Health & SafetyProcedureNumberHS1HS1ISO 13JWJWJWJWGENERAL POLICY STATEMENTOur policy is to provide and maintain safe and healthy working conditions, equipment andsystems of work for all employees. We also accept our responsibility for the health and safetyof other people who may be affected by our activities.Therefore the company accepts the responsibility:i)To provide and maintain safe and healthy working conditions on their premises andsites of clients, taking account of relevant statutory requirements.ii)To provide such training and instruction as may be relevant to their particularoperations to assist employees to perform their work safely and efficiently.iii)To make available such safety devices and protective equipment as may beappropriate and to secure the supervision of there use.iv)To maintain a continuing interest in health and safety matters applicable to theactivities in which they are involved and for management to set an example in safebehaviour.v)The company will actively carry out risk assessments of all aspects of thebusiness.vi)To ensure that all employees are aware of their responsibilities with regards toenvironmental matters.Employees of the company have a duty to co-operate in this objective:i)By working safely and efficiently.ii)By properly using safety devices and protective equipment provided and by meetingstatutory obligations.iii)By reporting incidents which have led or may lead to injury or damage.iv)By adhering to company procedures and observing instructions designed to contributeto the protection of health and safety.v)By co-operating in the investigation of accidents with the object of introducingmeasures to minimise the possibility of recurrence.vi)By ensuring that all environmental issues are addressed i.e. recycling etcT. SunterManaging DirectorDecember 2106Documents Produced within this ProcedureDescriptionDecember 2016Date & Revision NoDocument Author7Where RetainedVersion 6
Health & Safety ManagementSystem ManualHS.3OHSAS 18001Clause Number 4.34.3.1 Health & Safety Aspects4.3.2 Legal & Other Requirements4.3.3 Objectives, Targets & Programme(s)PLANNINGDecember 20168Version 6
Health & Safety ManagementSystem ManualDate08.08.201116.08.201322.10.2015Health & SafetyProcedureNumberHS3HS3HS3ISO 4.3123JWJWJWJWJWJW1. PURPOSEThe aim of this procedure is to identify the health & safety aspects, legal and otherrequirements of its activities, products and services within the defined scope of the health &safety system, taking into account planned and new developments, or new or modifiedactivities, products and services. Also to determine those aspects that has significantimpact(s) on the health & safety of any person(s) or organisations that come into contact withthe company.2. SCOPEThe scope of the procedure is to identify and plan the activities that the company have, andproduce a detailed action plan that can be implemented and maintained to ensure that thecompany attains and maintains the OHSAS18001;2007 Accreditation. An Action Plan will beproduced to determine the way forward in the implementation of the Standard. Objectives,targets and programme(s) will be implemented where required3. PROCESSPlanning of the Health & Safety Management System will be overseen by the ManagingDirector in conjunction with the Company Directors. The daily running and managing of thesystem will be overseen by the Health & Safety Manager.4.3. HEALTH & SAFETY ASPECTSThe company has various areas that will need to be managed in accordance with theStandard. The main areas are: Risk Assessment & Control (Risk Assessments and Work Method Statements) Information, Instruction, Training & Supervision Auditing and Inspection (Internal & External) Implementation & OperationRISK ASSESSMENT & CONTROLThe company takes assessment of risk and hazards that may be evident during itsundertakings as a priority.To accommodate and facilitate risks and hazards that may be evident either on site or at thehead office facility, risk assessments and work method statements are carried out on workactivities. These risk assessments and work method statements form a part of the system thatas a whole encompasses all health & safety control measures.These risk assessments, work method statements and other documents are formulated in amethodical way by the Health & Safety Manager to ensure that a safe working environment isin place at all times.The assessment and control of risk is a major factor in ensuring that a safe workingenvironment is achieved. The procedure for the formulation of risk assessments and workmethod statements is as shown in the flowcharts as follows.December 20169Version 6
Health & Safety ManagementSystem ManualRisk Assessment & Work Method Statement Formulation & Amendment ProceduresThe process/job or task is identifiedIt is determined who within the workforce has previousexperience in carrying out the taskThis person is evaluated to see if they are competentto give practical advice on the task.The competent person is asked to discuss with theH&S Manager the best way (in his/her opinion) to carryout the task.These findings are evaluated by the H&S Manager andadapted (if required) to comply with safe workingpractices and current legislation.The draft RA and/or WMS is written and a discussionbetween the competent person, Site Manager and theH&S Manager takes place to discuss the draftassessment.Assessmentdeemedsuitable fortrialAssessmentdeemed notsuitable fortrialThe competent person then carries out the taskfollowing the requirements of the RA and/or WMSto establish if any changes are required prior topassing the RA and/or WMS as a live documentAssessment passed and tobe implementedAssessment notpassed andrequires furtherreviewOnce all are happy that the RA and/or WMS can be implemented andthat it covers the task safely, a RA and/or WMS number is allocated tothe document(s) and the document(s) becomes live and is passed ontoall who will carry out the task.December 201610Version 6
Health & Safety ManagementSystem ManualOnce the procedure shown has been carried out and the risk assessment becomes a livedocument, the following procedure is carried out to ensure that the risk assessment is currentand up to dateRA and/or WMS is in place and is datedReasons for reviewNew ProcessNew EquipmentNew PersonnelOtherNew LegislationReview takes placeReview findsamendmentsnot neededReview findsamendmentsneededAmendmentsput into placeRA and/or WMS passed and redated before being put back asa live documentThe flow charts within this procedure details the process that Sunter Ltd carry out whenassessing the requirements for Risk Assessments and Work Method Statements. Thisprocedure takes into consideration all tasks, jobs and processes carried out by Sunter Ltdemployees and/or contractors.December 201611Version 6
Health & Safety ManagementSystem Manual4.3.2 LEGAL & OTHER REQUIRMENTS.Legal and other requirements that need to be in place to adhere
Lead ISO/OHSAS Auditor (Mr John Walker) Directors (Mr Lee Sunter) (Mrs Maureen Sunter) (Mr Kevin Stubbs) Internal Auditor(s) Site Managers Stores Staff Site Staff Office Staff Stores Manager Office Manager . Health & Safety Management System Manual December 2016 5 Version 6 RESPONSIBILITIES Managing Director – Acting as Safety Director - To provide funding and “Top