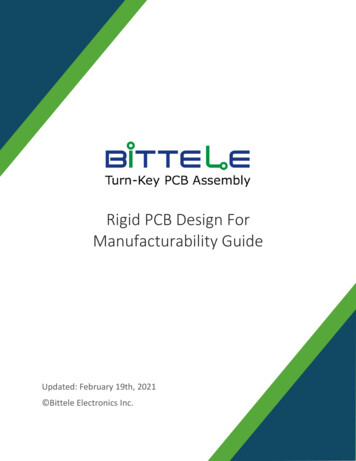
Transcription
Rigid PCB Design ForManufacturability GuideUpdated: February 19th, 2021 Bittele Electronics Inc.
BITTELE ELECTRONICS DFM GUIDE FOR PCB DESIGNERSPAGE 1 OF 68Table of Contents1.0 – Introduction. 51.1 Scope. 52.0 Required Documents . 62.1 Gerber Files – RS-274X Format. 62.2 ODB . 72.3 Drill / Route File . 72.4 Netlist File . 82.5 Centroid File / Pick and Place File . 82.6 Assembly Bill of Materials (BOM) . 82.7 Drawings . 92.8 Standard Manufacturing Specifications . 103.0 Laminate Materials Selection. 113.1 Material Selection & Properties . 113.2 Laminate Material and Thickness . 123.3 Prepreg Designation and Thickness . 123.4 Copper Weight & Heavy Copper for Materials . 133.5 RF Substrates . 143.6 Metal-Core PCBs . 153.7 Multi-Layer Stack-Up . 163.8 Multi-Layer Stack-Up Recommendation . 163.9 Buried Capacitance . 193.10 Material Substitutes (North America vs China) . 204.0 Standard PCB Manufacturing Capabilities . 214.1 PCB Technology Matrix . 214.2 Etch Factor . 234.3 Drill Selection . 244.4 Aspect Ratio . 254.5 Annular Ring . 254.6 Tear Drop Pads . 264.7 Hole Clearance . 264.8 Conductor Clearance . 27Document Contents Bittele Electronics 2021
BITTELE ELECTRONICS DFM GUIDE FOR PCB DESIGNERSPAGE 2 OF 684.9 Via Holes Treatment . 274.10 Finished Board Thickness . 284.11 Overall Finished Profile Tolerance . 284.12 Board Outline . 294.13 Edge Bevel . 295.0 HDI Technology Capabilities. 305.1 Tight Trace Width / Spacing (Trace/Space) . 305.2 BGA . 305.3 Micro-via . 315.4 Multiple Laminations/ Sequential Lamination . 336.0 Surface Finish: Options and Requirements . 356.1 HASL/LF-HASL . 356.2 ENTEK/OSP . 366.3 ENIG . 376.4 Full Body Hard Gold . 386.5 Selective Gold . 386.6 Double Gold (Full-Body Selective Gold) . 396.7 Edge Connector Plating . 396.8 Wire Bonding (Soft Gold) . 396.9 ENEPIG . 406.10 Immersion Tin. 406.11 Immersion Silver . 416.12 Comparison Chart . 427.0 Solder Mask: Options and Requirements . 437.1 – What is a Solder Mask? . 437.2 – Types of Solder Mask . 437.3 – Solder Mask Design Rules. 447.4 – Solder Mask Colours . 457.5 – Substitutes (North America vs China) . 467.6 – Solder Mask Tenting . 467.7 – Solder Mask Plugging . 467.8 – Peel-Able Solder Mask . 468.0 Silkscreen: Options and Requirements . 47Document Contents Bittele Electronics 2021
BITTELE ELECTRONICS DFM GUIDE FOR PCB DESIGNERSPAGE 3 OF 688.1 – What is a Silkscreen?. 478.2 –Silkscreen Requirements . 478.3 – Silkscreen Types . 488.4 – Silkscreen Colours . 488.5 – Substitute (North America vs China). 498.6 – Multiple Colour Silk on One PCB. 498.7 – Serialization . 499.0 Electrical Testing. 509.1 – Electrical Testing Requirements . 509.2 – Flying Probe Test. 519.3 – Fixture (Bed of Nails) Test . 519.4 – Cost . 5110.0 Controlled Impedance PCB . 5310.1 Impedance Calculators. 5510.2 Impedance Models . 5510.3 Impedance Affect Stack-up . 5510.4 Bittele TDR Calculations . 5610.5 TDR Coupons . 5611.0 – Flexible and Rigid-Flex PCBs . 5711.1 Flexible PCB Fabrication Capabilities . 5711.2 Flexible PCB Materials. 5811.3 Rigid-Flex PCBs . 6112.0 Panelization . 6212.1 Fiducials. 6212.2 Tooling Holes . 6212.3 V-Score . 6312.4 Tab Routing . 6313.0 Report Types and Report Writing. 6413.1 Products Final Audit Report . 6413.2 Certificate of Conformance (C of C) . 6413.3 Test Report . 6513.4 Solderability Report . 6513.5 Cross Section Report . 65Document Contents Bittele Electronics 2021
BITTELE ELECTRONICS DFM GUIDE FOR PCB DESIGNERSPAGE 4 OF 6813.6 Impedance Report (TDR) . 6514.0 RoHS Compliance . 6614.1 PCB Raw Material . 6615.0 Assembly Considerations . 6715.1 – Automated Optical Inspection (AOI) . 6715.2 ‒ X-Ray Inspection . 6715.3 – Functional Testing (FCT) . 68Document Contents Bittele Electronics 2021
BITTELE ELECTRONICS DFM GUIDE FOR PCB DESIGNERSPAGE 5 OF 681.0 – IntroductionThe purpose of this Design for Manufacturability (DFM) guide is to assist Bittele’s customers in designingprinted circuit boards (PCBs) that can be manufactured quickly and efficiently. These DFM guidelines definethe various tolerances, rules, and testing procedures to which Bittele adheres during PCB manufacturing.It is beneficial to all parties involved, in terms of both cost and efficiency, if these issues can be addressedduring the design stage, rather than during production. By providing this guide, we hope to avoid the potentialscenario where our client has finished designing a board, but must later revise their design due to facilitylimitations.DFM guidelines are essential to promote a client’s understanding of the various options that we offer, thereasons for each of these options, and the limitations of Bittele’s production facilities. At Bittele we specializein turn-key production rigid multi-layer PCBs with part procurement and placement.For a quick overview of our manufacturing specifications please see our other document on our website titled“PCB Fabrication Specifications”.1.1 ScopeConsulting these DFM guidelines during your design process will allow you to plan a PCB that conforms to thecapabilities of Bittele’s facilities. A strong understanding of our manufacturing ability enables our clients toachieve the special features that their designs require, while maximizing efficiency with regard to both timeand money.Listed below are a few of the more notable benefits found in designing for manufacturability: Higher quality results by working within facility capabilitiesReduced lead times by avoiding unnecessary delaysLower labor and material costs from correcting errorsHigher first-pass yieldsMinimized environmental impact by avoiding waste from re-making boardsIn order to fully reap the benefits listed above, our clients must understand our abilities concerning the specifictype of PCB option(s) that they require. This guide is therefore divided into sections according to the differenttypes of options and features that we offer at Bittele. Those sections are as follows: Required DocumentsLaminate Materials SelectionPCB Manufacturing CapabilitiesHDI Technology CapabilitiesSurface Finish: Options and RequirementsSolder Mask: Options and RequirementsDocument Contents Bittele Electronics 2021 Silkscreen: Options and RequirementsElectrical TestingControlled Impedance PCBPanelizationReport Types and Report WritingRoHS Compliance
BITTELE ELECTRONICS DFM GUIDE FOR PCB DESIGNERSPAGE 6 OF 682.0 Required DocumentsVarious PCB design files and other forms of documentation are required for Bittele to fabricate a printed circuitboard and populate the components onto that board. There are two file formats we can translate and acceptfor manufacturing: ODB and Gerber version RS-274X.In the OBD format, all data required for PCB fabrication and assembly are included within the .TGZcompressed archive. Should you choose to use this format, you will just need to provide the .TGZ archive alongwith a Bill of Materials (BOM) for assembly.If you choose to use the Gerber file format, please ensure that you are using the RS-274X version. This formatspecifies a set of files, where each individual file represents one type of design drawing, such as top copper,bottom solder mask, or top silk screen. Please ensure that you provide a Gerber file for each design element inyour PCB layout, as well as any other relevant documentation for fabrication and assembly. When using thegerber format, additional files are required for board assembly, a centroid file for pick and place as well as aBill of Materials with part numbers.2.1 Gerber Files – RS-2
Feb 19, 2021 · the printed circuit board (PCB) design information, can be sent directly to a PCB Fabrication and Assembly company, such as Bittele. ODB stands for Open Data Base, with the ‘ ’ suffix added in 1997, when component descriptions were enabled. O