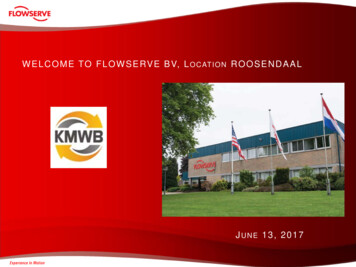
Transcription
W E L C O M E T O F L O W S E RV E B V, L O C AT I O N R O O S E N D A A LJUNE 13, 2017
SPACER Safety Purpose Agenda Conduct Expectations RolesFlowserve Corporation Proprietary and ConfidentialPage 2
Agenda15:00 – 15:20Introductie Flowserve RSD15:20 – 16:25Hoe doen ze dat bij .?a) Control of externally provided b) Internal/supplier audits16:30 – 17:25Rondgang (productie & logistiek)
F LOW S ERVE R OOSEND AAL
Roosendaal plant overview Facility sizeShop floorHeadcountShop CapacityWarehouse: 5,800 m2: 3,600 m2: 215; 72 direct, 143 indirect: 116,000 hours, 3 shifts: 2 shifts Core capabilities:– Knowledge center for pump seals & systems in EMA (technology & logistics)– Test facility completely refurbished in 2013/2014– Hub for all EMA Quick Response Centers (manufacturing & distribution)– QMS certified: ISO 9001 by Lloyd’s Register (since 1989) ASME NQA-1 by AIB Vinḉotte
Scope QMSEngineering and manufacturingofmechanical seals, sealing systems and components forrotating equipmentfor use inpetroleum, chemical, power, pulp and paper, mining andother industries.
High Level ISO Transition RoadmapPreImplementationGap Analysis & StrategyISO 9001:2015ImplementationRenewal Certification1 – Knowledge QA bytrainings, workshops,seminars, etc.2 – Benchmark withother FLS Companies3 – Deploy GAP Analysis tool andexecute GAP analyze (QA), createRAIL and resources.7 – Implement actionsaccording to RAIL and updateQMS documentation.For example Relationship management Risk-based thinking Process approach8 – Review, maintain,develop and improveQMS.Half yearly QMS reviewsandSurveillance Visits LRQA4 – Training InternalISO Audit team5 – Implementation (level off) Process- and Risk Management6 – Align and verifyapproach with LRQA(Focus visit)Frequent Progress / Awareness/ Reporting to Management Team, auditors LRQA and internal ISO Audit Team.Since 2013Start ISO Transition Roadmap.4Q151Q16May 2016Steering team to agree on transition approach, resources and timeline20-22 Sept 2016ISO 9001:2015 certified
GAP Analyze toolSite12345Identified changes or new issued requirements of ISO 9001:2015(compared to ISO 9001:2008)FINDINGSSETTINGRISKRANKING[1 up to 10]REFERENCE: ISO 9001:2015COMPLIANCERANKING [%]NoSECTION(S): xxxxxxxxxxxxISOCLAUSEREF.XXXGAP ANALYSISGAP ANALYSISN.B. Provide references to documentation where necessaryACTUAL QMSAnalysis6ACTIONS tatusFirst Due ActualDateDue DateCloseDateComments / Result / Status / UpdateRAIL78910Notes:Revision: 0Updated: DD-MM-YYDate of execution GAP ANALYZE this section: DD-MMM-YYYYExecuted by: Name(s)Title: xxx & xxxPage 8
ExampleSiteGAP ANALYSISRSDSECTIONS: 1, 2, 3 and 4REFERENCE: ISO 9001:2015SETTINGRISKRANKING[1 up to 10]FINDINGSCOMPLIANCERANKING [%]ISOCLAUSEREF.Section 1: ScopeSection 2: Normative referencesSection 3: Terms and definitionsSection 4: Context of the organization1Section 1Term "product" changed to "Product and or Service" in the scope of theISO9001 standard.7012Section 1 Exclusions of QMS no longer limited within clause 7: Product realization1003Section 2 Fundamentals and vocabulary (ISO 9000) changed to 2015 version1004Section 3 Terms and definitions (ISO 9000) changed to 2015 versionNo54.164.174.2 a)84.2.b)94.2104.3Identified changes or new issued requirements of ISO 9001:2015(compared to ISO 9001:2008)Are external and internal issues determined that are relevant to itspurpose and its strategic direction and that affect its ability to achievethe intended result(s) of its quality management system?Does the organization monitor and review information about theseexternal and internal issues?Are the interested parties that are relevant to the quality managementsystem determined?Are the requirements of these interested parties that are relevant to thequality management system determined?Is the information about these interested parties and their relevantrequirements monitored and reviewed?Are the boundaries and applicability of the quality management systemto establish its scope determined (and available and maintained asdocumented information)?Are the processes and their interactions, needed for the QMS and theirapplication throughout the organization, determined?Are the inputs required and the outputs expected from these processesdetermined?GAP ANALYSISN.B. Provide references to documentation where necessaryStatusFirst Due ActualDateDue DateCloseDateComments / Result / Status / UpdateCheck and or update (text) content of RSD-PR-GEN000E and ISO9001 Certificate on "Product and orService"WG1-Feb-16Open1-Mar-16Ask for impact during transition training FLSin MarchCheck if ISO9000:2015 is available (contract NEN orTechstreet)WG26-Jan-16Open1-Mar-1627-01-2016: Not in NEN Contract RSD.100Idem 3Idem 3100SWOT executed by MT mid 2015, risksare translated into improvementsprojects and ranked for priorityPeriodical review to be implemented in strategicMT meetingsEK1-Feb-16Open1-Sep-16Periodical review to be implemented in strategicMT meetingsEK1-Feb-16Open1-Sep-16Level of process approach and their in- and outputsto be defined.EK1-Feb-16Open1-Sep-16Assigned by each QMS documentAdd resp and auth per process in QA manualWG1-Feb-16Open1-Mar-16Risk and opp per process not part ofGAP analyse MT.Identify risk and opp per process as defined inISO9001EK1-Feb-16Open1-Sep-16Monitoring by KPI/PI's of processesWhat is definition of -Sep-16707Stakeholderanalyse executed by manassistant with MT mid 201510010010Yearly review of SWOT with MTPart of Stakeholderanalyse7Only annual identified.100Scope QMS in RSD-PR-GEN-000E QAmanual100See appendix A of RSD-PR-GEN-000EQA manual4.4.1124.4.1 a)134.4.1 b)Are the sequence and interaction of these processes determined?100See appendix A of RSD-PR-GEN-000EQA manual144.4.1 c)Are methods (including monitoring, measurements and relatedperformance indicators) needed to ensure the effective operation andcontrol of these processes determined and are the criteria applied?100Outputs of processes by KPI/PImeasurement164.4.1 e)Are the responsibilities and authorities for these processes assigned?100174.4.1 f)1010184.4.1 g)194.4.1 h)Are the processes and the quality management system improved?100204.4.2 a)Is documented information to support the operation of the processesmaintained?104.4.2 b)Is documented information retained to have confidence that theprocesses are being carried out as dualQA Manual and ISO9001 Certificate.Actual Q Policy describes "productsand service".Clause 8.3 Design and developmentfor products and services remainexcluded from scope QMS RSD.Dutch and English ISO9001:2015available11Are the risks and opportunities for these processes addressed?(according 6.1)Are these processes evaluated and are any changes implementedneeded to ensure that these processes achieve their intended results?ACTIONS REQUIREDACTUAL QMS10103Not all in- and outputs determinedSee MoM periodical QMS review,Plant AC and departmental AC's.Process of maintenance is describedImplement periodical review process of (critical)in RSD-PR-QAC-149E, but structuralQMS documents and changes of process ownersperiodical review is missing.DI available as KPI's, Internal Auditreports and MoM Man. ReviewTo be asked in transition training FLSNotes:No 10, 20 & 21 allready identified by section "Documented information".Revision: 0Updated: 01-Feb-16Date of execution GAP ANALYZE this section: 01-Feb-2016Executed by: E. Kepers & W. GeukeTitle: Manager QA/QC/CIP & QA EngineerPage 9
ISO 9001:2015 requirementsfor “Process approach”1) Intended result2) Input and output3) Sequence and interaction4) Performance indicators5) Planning, implementation and control6) Resource management7) Responsibilities/Ownership8) Risk based thinking9) Evaluation, change and improvements10) Trends in process performance(s)
Defined processes of RSD(According RSD-PR-GEN-000E: QA Manual)Core Processes:Supporting FunctionsOrder Entry & BookingOE Customers(Customer Service OrderFulfillment OE)Order Engineering(Seal / SystemEngineering & ATS)Supporting FunctionsOrder Entry & BookingAM Customers(Customer Service OrderFulfillment AM)Order Engineering(Chennai EngineeringCell)Order Scheduling & Inventory Management(MRP Planning)Production Planning(Shopplanning)Project & (Nuclear)Order Management(Seals & Systems)Produce Components(Manufacturing/Tool Crib)PurchaseComponents / Seals /Engineered Systems(Purchasing)NC programming & 3Dmodelling(Chennai Engineering Cell)InspectComponents /Seals / EngineeredSystems(Quality Control)Assemble, testing &InspectionSeals / StandardSystems(Manufacturing,Testlab &Warehouse)Store Components /Seals / Systems(Warehouse)Pick, Pack & ShipComponents /Seals / Systems incl.Documentation(Shipping & mationTechnologySafety, Health mQuality AssuranceProduction Engineering &preparation(Industrial Engineering)Outsource Operations &Component Production(Shop Planning)Human Resources
RSD’s Template for “Process mapping”Process Model QMS RSD
“Process mapping” example
“Risk-based thinking”Five steps of risk management: IdentifyAnalyzeActionMonitorControl
RSD’s Template for “Risks &Opportunities Management”Risico Ernst x Kans x Beersbaarheid
“R & O Management” example
F LOW S ERVE H OEDOEN ZE DAT BIJ .?
Internal Audits Each defined process minimum each 3 year; Nuclear process(steps) yearly;Order Entry & BookingOE Customers(Customer Service OrderFulfillment OE)Order Engineering(Seal / SystemEngineering & ATS)Supporting FunctionsOrder Entry & BookingAM Customers(Customer Service OrderFulfillment AM)Order Engineering(Chennai EngineeringCell)Order Scheduling & Inventory Management(MRP Planning)Production Planning(Shopplanning)Project & (Nuclear)Order Management(Seals & Systems)Produce Components(Manufacturing/Tool Crib)PurchaseComponents / Seals /Engineered Systems(Purchasing)NC programming & 3Dmodelling(Chennai Engineering Cell)InspectComponents /Seals / EngineeredSystems(Quality Control)Assemble, testing &InspectionSeals / StandardSystems(Manufacturing,Testlab &Warehouse)Store Components /Seals / Systems(Warehouse)Pick, Pack & ShipComponents /Seals / Systems incl.Documentation(Shipping & mationTechnologySafety, Health mQuality AssuranceProduction Engineering &preparation(Industrial Engineering)Outsource Operations &Component Production(Shop Planning)Human Resources
Internal Audits Each defined process minimum each 3 year; Nuclear process(steps) yearly; Yearly audit plan (approved & priorities by MT);
Internal AuditsEach defined process minimum each 3 year;Nuclear process(steps) yearly;Yearly audit plan (approved & priorities by MT);Feedback/results: Every 6 months by MR;Internal Processes Cost of Poor Quality(as % of Sales LDsCARsFTR Rate MFG partsManagement ReviewQMS Transitie .320.210.060.261096.0010041483
Internal Audits Each defined process minimum each 3 year;Nuclear process(steps) yearly;Yearly audit plan (approved & priorities by MT);Feedback/results: Every 6 months by MR;Qualified auditors;
Internal Audits Each defined process minimum each 3 year;Nuclear process(steps) yearly;Yearly audit plan (approved & priorities by MT);Feedback/results: Every 6 months by MR;Qualified auditors;Corrective/preventive actions of findings;- Best practices: Shared with Process owner(s)- OFI: Input for CIP- NC: Global CAR-System
Internal Audits Each defined process minimum each 3 year;Nuclear process(steps) yearly;Yearly audit plan (approved & priorities by MT);Feedback/results: Every 6 months by MR;Qualified auditors;Corrective/preventive actions of findings;6x year internal audit team meetings;
Questions ?
F LOW S ERVE R ONDLE IDING
Rondleiding Van 16:30 tot 17:30 uur In 4 groepen (met verschillende routes) PBM: brillen en hesjesPage 27
WELCOME TO FLOWSERVE BV, LOCATION ROOSENDAAL . – Knowledge center for pump seals & systems in EMA (technology & logistics) – Test facility completely refurbished in 2013/2014 – Hub for all EMA Quick Response Centers (manufacturing & distribution) – QMS certified: ISO 9001 by Lloyd’s Register (since 1989) ASME NQA-1 by AIB Vinḉotte. Scope QMS Engineering and manufacturing .