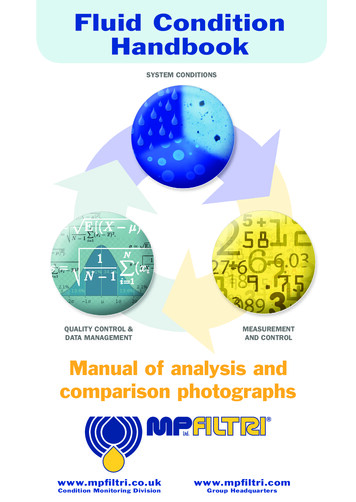
Transcription
Fluid ConditionHandbookSYSTEM CONDITIONSQUALITY CONTROL &DATA MANAGEMENTMEASUREMENTAND CONTROLManual of analysis andcomparison photographsLtd.www.mpfiltri.co.ukCondition Monitoring Divisionwww.mpfiltri.comGroup Headquarters
IndexIntroductionGeneral InformationPg’sIntroduction2General Information3-6Sampling Procedures7-9Cleanliness ReportingFormats10-15Micron Rating SizeComparisons16-17Comparison Photographsfor Contamination Classes18-29Hydraulic ulic System TargetCleanliness Levels32Filter Element BetaRatio Information33Information onReynolds Numbers34Information onPressure Changes35Viscosity Conversion Chart36Cleanliness Code Comparison37Measuring Water in Hydraulicand Lubricating fluids38-39Contamination MonitoringProducts40-41In hydraulic fluid power systems, power istransmitted and controlled through a liquidunder pressure within an enclosed circuit.The liquid is both a lubricant and a powertransmitting medium.The presence of solid contaminant particlesin the liquid interferes with the ability of thehydraulic fluid to lubricate and causes wear tothe components. The extent of contaminationin the fluid has a direct bearing on theperformance and reliability of the system andit is necessary to control solid contaminantparticles to levels that are consideredappropriate for the system concerned.A quantitative determination of particulatecontamination requires precision in obtainingthe sample and in determining the extentof contamination. Liquid Automatic ParticleCounters (APC) (MP Filtri Products), work on thelight-extinction principle. This has become anaccepted means of determining the extent ofcontamination. The accuracy of particle countdata can be affected by the techniques used toobtain such data.IMPORTANT. For definitive and comprehensive guidance on condition monitoring and the content held within thisdocument, always refer to the relevant standard.MP Filtri UK Ltd has created this document based on related current standards dated as such. The document isintended as a guide only and MP Filtri UK Ltd reserves the right to alter content, specifications, artwork and relatedinformation without prior written notice.To ensure that you always have the latest revision of this document, please go to www.mpfiltri.co.uk2www.mpfiltri.co.ukCondition Monitoring Divisionwww.mpfiltri.comGroup HeadquartersThe NAS 1638 reporting format was developed for use where the principlemeans of counting particles was the optical microscope, with particlessized by the longest dimension per ARP598. When APC’s came in touse this provided a method of analysing a sample much faster than theARP598 method. A method of calibrating APC’s was developed, althoughthey measured area and not length, such that comparable results to thatof ARP598 could be obtained from the same sample. Now, APC’s are theprimary method used to count particles and the projected area of a particledetermines size. Because of the way particles are sized with the twomethods, APC’s and optical microscopes do not always provide the sameresults. NAS 1638 has now been made inactive for new design and hasbeen revised to indicate it does not apply to use of APC’s.Prior to ISO 11171, the previous APC calibration method most widelyutilised was ISO 4402, which used Air Cleaner Fine Test Dust (ACFTD) as thereference calibration material. ACFTD is no longer manufactured and theISO 4402 method using this dust has been made obsolete. The industrydeveloped the method ISO 11171, which supersedes ISO 4402, with acalibration standard based on NIST-certified samples of ISO 12103-1 A3medium test dust suspended in hydraulic oil. There is a difference betweenthe particle measurements by ISO 4402 and ISO 11171. To retain the samecleanliness measure, calibrations using ISO 11171 are conducted to acorrected particle count scale. For example, particles reported as 5 um withthe ISO 4402 method are reported as 6 um (c) by the ISO 11171 method. Infact 5 um corresponds to 6.4 um (c), and some round off was conducted forsimplification.www.mpfiltri.co.ukCondition Monitoring Divisionwww.mpfiltri.comGroup Headquarters3
Particle size analysisDifferences between NAS 1638 and AS4059E.Several methods and instruments based on different physical principlesare used to determine the size distribution of the particles suspended inaeronautical fluids. The numbers of particles found in the different sizeranges characterize this distribution. A single particle therefore has asmany equivalent diameters as the number of counting methods used.AS4059E was developed as a replacement/equivalent to the obsolete NAS1638 format, where table 2 relates to the old AS4059D standard and table1 is the equivalent NAS1638 standard. However, there are differences.Particularly in Table 2, (Cumulative Particle Counts).Figure 1 shows the size given to the particle being analysed (shading) by amicroscope as its longest chord and an APC calibrated in accordance withISO 11171 using the Standard Reference Material NIST SRM 2806 sizedby the equivalent projected area.AS4059E allows the analysis and reporting of smaller particle sizes thanNAS 1638.Particle to be analyzedSized by microscope“longest dimension”“diam. of equiv. proj.surface”13μmArea 78.5 μm2Equivalent sized 13 μm4Sized by APC calibrated asper ISO 11171 (new NIST)www.mpfiltri.co.ukCondition Monitoring DivisionEquivalent sized 10 μmwww.mpfiltri.comGroup HeadquartersCounting of Smaller Particles.Counting Large Particles and Fibres.In some samples, it has been observed that many of the particles largerthan 100 micrometers are fibres. However, APC’s size particles basedon projected area rather than longest dimension and do not differentiatebetween fibres and particles. Therefore, fibres will be reported as particleswith dimensions considerably less than the length of the fibres. A problemwith fibres is that they may not be present in fluid in the system but ratherhave been introduced as the result of poor sampling techniques or poorhandling during analysis.Determining AS4059E Class Using Differential Particle Counts:This method is applicable to those currently using NAS 1638 classes anddesiring to maintain the methods/format, and results equivalent to thosespecified in NAS 1638.Table 1 applies to acceptance criteria based on differential particle counts,and provides a definition of particulate limits for Classes 00 through 12. Aclass shall be determined for each particle size range. The reported classof the sample is the highest class in any given particle range size.NOTE: The classes and particle count limits in Table 1 are identical to NAS 1638.Measurements of particle counts are allowed by use of an automatic particlecounter (calibrated per ISO 11171 or ISO 4402:1991), or an optical or electronmicroscope. The size ranges measured and reported should be determinedfrom Table 1 based on the measurement method.www.mpfiltri.co.ukCondition Monitoring Divisionwww.mpfiltri.comGroup Headquarters5
Determing AS4059E Class Using Cumulative Particle Counts:This method is applicable to those using the methods of previous revisionsof ÅS4059 and/or cumulative particle counts. The cleanliness levels forthis method shall be specified by the appropriate class from Table 2. Toprovide versatility, the applicable cleanliness class can be identified in thefollowing ways:a. Basing the class on the highest class of multiple size ranges .b. Total number of particles larger than a specific size.c. Designating a class for each size range.Designating a Class for Each Size Range:APC’s can count the number of particles in several size ranges. Today,a different class of cleanliness is often desired for each of several sizeranges. Requirements can be stated and cleanliness can easily bereported for a number of size ranges. A class may be designated for eachsize from A through F*. An example is provided below:7B/6C/5D is a numeric-alpha representation in which the numberdesignates the cleanliness class and the alphabetical letter designatesthe particle size range to which the class applies. It also indicates thatthe number of particles for each size range do not exceed the followingmaximum number of particles:Size B: 38,924 per 100 mlSampling ProceduresMethods oftaking samplesfrom hydraulicapplicationsusing appropriatereceptaclesENSURE THAT ALL DANGERS AREASSESSED AND THE NECESSARYPRECAUTIONS ARE TAKEN DURINGTHE SAMPLING PROCESS.DISPOSAL OF FLUID SAMPLESMUST FOLLOW PROCEDURESRELATING TO COSHH.Size C: 3462 per 100 mlSize D: 306 per 100 mlSampling procedures are defined in ISO4021. Extraction of fluid samplesfrom lines of an operating system.*Please check standard for definition of size/classesReceptacles should be cleaned in accordance with DIN/1505884.The degree of cleanliness should be verified to ISO3722.6www.mpfiltri.co.ukCondition Monitoring Divisionwww.mpfiltri.comGroup Headquarterswww.mpfiltri.co.ukCondition Monitoring Divisionwww.mpfiltri.comGroup Headquarters7
Methods of taking sample from hydraulicapplications, using appropriate recepticlesMethods of taking sample from hydraulicapplications, using appropriate recepticlesMethods One & TwoMethods Three & FourMethod One –Preferred methodMethod Two –Preferred methodMethod Three Reservoir samplingMethod Four –Bottle Dipping(Using a suitable sampling valve with PTFEseating method)(Using an unspecifiedsampling valve)(Use only if methods One &Two cannot be used)(Least preferred method due to possiblehigh ingression of contaminationInstall sampling valve in pressure orreturn line (in closed condition) at anappropriate point under constant flowor turbulent conditionsInstall valve in return line or anappropriate point where flow isconstant and does not exceed 14 barOperate system for at least 30 minutesbefore taking a sampleOperate system for at least 30 minutesbefore taking a sampleClean outside of sampling valveFlush sampling valve by passing atleast 45 litres through valve back toreservoirOpen the sampling valve to give appropriate flow rate and flush at least onelitre of fluid through the valveDo Not Close Valve After FlushingDisconnect line from valve to reservoirwith valve open and fluid flowingThoroughly clean area around the pointof entry to the reservoir where samplebottle is to be insertedAttach sample bottle to the samplingdeviceCarefully insert sampling hose intothe midway point of the reservoir. Trynot to touch sides or baffles within thereservoirClean outside of ultra clean samplebottle using filtered solvent, allow toevaporate dryDip sample bottle into reservoir, capand wipeRe-seal reservoir accessLabel the bottle with the necessaryinformation for analysis e.g. Oil type, runninghours, system description etc.Repeat the above three steps three timesto ensure flushing of the equipmentClose the sampling valveAttach ultra cleaned sample bottle tosampling device – collect final fluid sampleLabel the bottle with the necessaryinformation for analysis e.g. Oil type,running hours, system description etc.Condition Monitoring DivisionThoroughly clean area around the pointof entry to the reservoirRelease vacuum, disconnect bottle anddiscard fluidPlace bottle under sampling valve.Fill bottle to neck. Cap bottle & wipe.www.mpfiltri.co.ukOperate system for at least one hourbefore taking a sampleExtract sample using the vacuum pumpand fill to approx 75% volumeRemove cap from sampling bottle.Ensure cap is retained in hand facedownwards8Operate system for at least one hourbefore taking a sampleRemove bottle from sampling device &cap - label with appropriate informationwww.mpfiltri.comGroup Headquarterswww.mpfiltri.co.ukCondition Monitoring Divisionwww.mpfiltri.comGroup Headquarters9
Cleanliness Reporting FormatsISO 4406:1999 Cleanliness Code SystemThe International StandardsOrganisation standardISO 4406:1999 is the preferredmethod of quoting the numberof solid contaminant particles ina sample.The code is constructed fromthe combination of three scalenumbers selected from thefollowing table.The first scale numberrepresents the number ofparticles in a millilitre sample ofthe fluid that are larger than4 μm(c).The second number representsthe number of particles largerthan 6 μm(c).The third number representsthe number of particles that arelarger than 14 μm(c).10www.mpfiltri.co.ukCondition Monitoring Divisionwww.mpfiltri.comGroup Headquarterswww.mpfiltri.co.ukCondition Monitoring Divisionwww.mpfiltri.comGroup Headquarters11
Cleanliness Reporting FormatsClasses of Contamination According to NAS 1638The NAS system was originally developed in 1964 to define contaminationclasses for the contamination contained within aircraft components. Theapplication of this standard was extended to industrial hydraulic systemssimply because nothing else existed at the time.Classes of ContaminationAccording to NAS 1638The coding system defines the maximum numbers permitted of 100mlvolume at various size intervals (differential counts) rather than usingcumulative counts as in ISO 4406:1999.Although there is no guidance given in the standard on how to quote thelevels, most industrial users quote a single code which is the highestrecorded in all sizes and this convention is used on MP Filtri’s APC’s.CONTAMINATION LEVEL CLASSES according to NAS 1638(January 1964)The contamination classes are defined by a number (from 00 to 12) whichindicates the maximum number of particles per 100 ml, counted on adifferential basis, in a given size bracket.12www.mpfiltri.co.ukCondition Monitoring Divisionwww.mpfiltri.comGroup Headquarterswww.mpfiltri.co.ukCondition Monitoring Divisionwww.mpfiltri.comGroup Headquarters13
Cleanliness Reporting FormatsCleanliness Reporting FormatsSAE AS 4059 REV.E**SAE AS 4059 REV.E**Cleanliness Classification for Hydraulic Fluids (SAE Aerospace Standard)Cleanliness Classification for Hydraulic Fluids (SAE Aerospace Standard)This SAE Aerospace Standard (AS) defines cleanliness levels for particulatecontamination of
Handbook Ltd. SYSTEM CONDITIONS QUALITY CONTROL & DATA MANAGEMENT MEASUREMENT AND CONTROL. www.mpfiltri.co.uk www.mpfiltri.com Condition Monitoring Division Group Headquarters www.mpfiltri.co.uk www.mpfiltri.com 2 Condition Monitoring Division Group Headquarters 3 Index Introduction Pg’s Introduction 2 General Information 3-6 Sampling Procedures 7