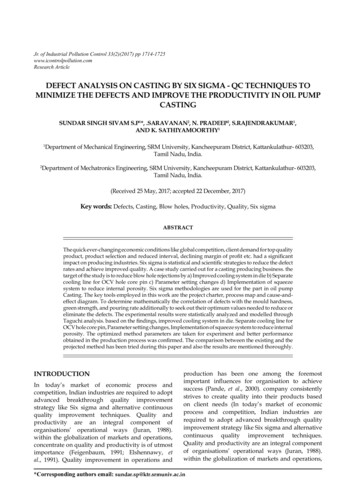
Transcription
Jr. of Industrial Pollution Control 33(2)(2017) pp 1714-1725www.icontrolpollution.comResearch ArticleDEFECT ANALYSIS ON CASTING BY SIX SIGMA - QC TECHNIQUES TOMINIMIZE THE DEFECTS AND IMPROVE THE PRODUCTIVITY IN OIL PUMPCASTINGSUNDAR SINGH SIVAM S.P1*, .SARAVANAN2, N. PRADEEP2, S.RAJENDRAKUMAR1,AND K. SATHIYAMOORTHY1Department of Mechanical Engineering, SRM University, Kancheepuram District, Kattankulathur- 603203,Tamil Nadu, India.1Department of Mechatronics Engineering, SRM University, Kancheepuram District, Kattankulathur- 603203,Tamil Nadu, India.2(Received 25 May, 2017; accepted 22 December, 2017)Key words: Defects, Casting, Blow holes, Productivity, Quality, Six sigmaABSTRACTThe quick ever-changing economic conditions like global competition, client demand for top qualityproduct, product selection and reduced interval, declining margin of profit etc. had a significantimpact on producing industries. Six sigma is statistical and scientific strategies to reduce the defectrates and achieve improved quality. A case study carried out for a casting producing business. thetarget of the study is to reduce blow hole rejections by a) Improved cooling system in die b) Separatecooling line for OCV hole core pin c) Parameter setting changes d) Implementation of squeezesystem to reduce internal porosity. Six sigma methodologies are used for the part in oil pumpCasting. The key tools employed in this work are the project charter, process map and cause-andeffect diagram. To determine mathematically the correlation of defects with the mould hardness,green strength, and pouring rate additionally to seek out their optimum values needed to reduce oreliminate the defects. The experimental results were statistically analyzed and modelled throughTaguchi analysis. based on the findings, improved cooling system in die. Separate cooling line forOCV hole core pin, Parameter setting changes, Implementation of squeeze system to reduce internalporosity. The optimized method parameters are taken for experiment and better performanceobtained in the production process was confirmed. The comparison between the existing and theprojected method has been tried during this paper and also the results are mentioned thoroughly.INTRODUCTIONIn today’s market of economic process andcompetition, Indian industries are required to adoptadvanced breakthrough quality improvementstrategy like Six sigma and alternative continuousquality improvement techniques. Quality andproductivity are an integral component oforganisations’ operational ways (Juran, 1988).within the globalization of markets and operations,concentrate on quality and productivity is of utmostimportance (Feigenbaum, 1991; Elshennawy, etal., 1991). Quality improvement in operations andproduction has been one among the foremostimportant influences for organisation to achievesuccess (Pande, et al., 2000). company consistentlystrives to create quality into their products basedon client needs (In today’s market of economicprocess and competition, Indian industries arerequired to adopt advanced breakthrough qualityimprovement strategy like Six sigma and alternativecontinuous quality improvement techniques.Quality and productivity are an integral componentof organisations’ operational ways (Juran, 1988).within the globalization of markets and operations,*Corresponding authors email: sundar.sp@ktr.srmuniv.ac.in
1715SIVAM ET AL.concentrate on quality and productivity is of utmostimportance (Feigenbaum, 1991; Elshennawy, etal., 1991). Quality improvement in operations andproduction has been one among the foremostimportant influences for organisation to achievesuccess (Pande, et al., 2000). company consistentlystrives to create quality into their products basedon client needs (Juran, 1988). For manufacturingquality products, continuous improvement (CI)methodologies are developed to induce higherproductivity of the operations (Hobbs, 2004; Nave,2002). throughout the past 20 years, the standardprogress has provided a broad collection of CImethods to accelerate the method of rising qualityand productivity that supports the business growth(Cox, et al., 2003). Six sigma is one of the recent CIapproaches that are applied within the best-in-classfirms (Bessant and Francis, 1999). Six sigma could bea highly structured process improvement frameworkthat uses each applied math and non-statistical toolsand techniques to eliminate method variation andthereby improve method performance and capability(Antony and Banuelas, 2002). Minimising defects tothe amount of 3.4 defects per Million opportunities(DPMO) is at the guts of this technique (Harry, 1998;McAdam and Lafferty, 2004). to realize target, thisapproach seeks to identify and eliminate defects,mistakes or failures in business processes by focusingon process performance characteristics (Snee, 2004).Six sigma approach are found to be vital profit driversin a style of industries (Caulcutt, 2001), highlightingthe economic dimension of quality improvement. Byusing DMAIC methodology, most of the Six sigmaefforts are centered on taking variability out of theexisting processes (Park, 2003; Bhote, 2002). DMAICis anagram of the most important phases at intervalsthe methodology particularly, outline measure,analyse, improve and management (Breyfogle,1999a). The outline part entails the definition of thematter and critical-to-quality (CTQ) characteristic.The measure phase selects most applicable qualitycharacteristic to be improved and establishes metrics.In analysis part, the foundation causes of defect areanalysed. In improve part, simple however powerfulstatistical tools/techniques are accustomed reducethe defect or method variations. in control part, theapproach of sustaining the advance is developedand place effective (Pyzdek, 2001; Montgomery,1998). The DMAIC frame work utilises numeroustools and techniques like management charts,quality perform preparation (QFD), failure modeand impact analysis (FMEA), style of experiments(DoE) and statistical method control (SPC) forvariation management to drive out defects inoperations. Among the offered collection of toolsand techniques, application of DoE is at the guts ofDMAIC cycle (Breyfogle, 1999a). Casting is that theopening move within the manufacture of metalliccomponent in which the material is liquefied byheating and poured into previous ready mouldcavity wherever it's allowed to solidify. Removingthe solidified component from the mould cavity andcleansed to form. In casting method there are severaldefects occur, these defects reduced by differentresearchers as (Bhupinder, 2014) in a manufactorybusiness. The business make submersible pumpselements like higher housing Motor pulley, higherhousing, mini Chaff cutter wheel in large scale andrejection comes within the type of slag inclusions inforged iron casting. These parameters were chosenfor complete analysis. to minimize the rejection useDMAIC approach. the idea of six letter (Satish, 2014)which is disciplined, data-driven methodology thatwas developed to boost producing quality, companyprofit and business method. several organizationshave tried to use Six-Sigma DMAIC approach andits tools to induce optimized structure achievements.The producing business is explores the amount ofissue and level of usage of various tools of DMAICapproach. (Abidakun, et al., 2014) paper explainsSix sigma DMAIC analysis in an aluminium millin order to identify sources and causes of wastewith offer veritable solutions. DMAIC approachesare justified (Vikas, et al., 2015) and minimize sandcasting defects once root reason behind defect isn'ttraceable. Business strategy accustomed improve(Virender, et al., 2014) business and potency to satisfyclient desires and expectations. The sand castingsmanagement the varied parameters with DMAICtechnique. The results show that the sand castingrejection due has been reduced from 6.98% to 3.10 tryto the defects because of Blow holes were reducedfrom 2.74% to 0.11% by increasing the permeabilityand reducing the moisture of sand. (Suraj, et al., 2015)Use of design of experiments (DOE) and analysisof variance (ANOVA) techniques each squaremeasure combined to see statistically the correlationof defects with the inexperienced strength, mouldhardness, and running rate conjointly to searchout their optimum values required to reduce thedefects. Indian manufactory rejection rate (Binu andAnilkumar, 2013) is one among major issues, thuscut back this rejection by modifying methodologyand style the tool to offers higher forgeding qualityand increase the production cast. (Kumaravadivel,et al., 2011; Sundar, et al., 2015; Sundar, et al., 2015;Sundar, et al., 2016; Sundar, et al., 2016) implementthe DMAIC primarily based Six letter Approach so
DEFECT ANALYSIS ON CASTING BY SIX SIGMA - QC TECHNIQUES TO MINIMIZE THEDEFECTS AND IMPROVE THE PRODUCTIVITY IN OIL PUMP CASTINGas to attenuate the prevalence of defects and increasethe letter level of sand casting method. In today’schallenging market, each organization is trying torealize higher quality and productivity. this may besimply achieved if you concentrate on the reductionin numerous defects that inflicting rejection of theelements. this is often the foremost viable strategyand it'll conjointly lead the organization towardseffectiveness in competitive market. the firstobjective of this Study is concentrated on RejectionReduction in case oil pump Blow Hole Rejectionthrough Six sigma – QC Techniques. The objectiveshere are improved cooling system in die, Separatecooling line for OCV hole core pin, Parameter settingchanges, Implementation of squeeze system toreduce internal porosity.MATERIALS AND METHODSPareto chartThe diagram is a graphical representation of the law.The various categories are listed across the bottomof a graph, then the cumulative totals are plottedas percentages. Starting with the largest numberto the left, the diagram is formed. It is clearly seenthat a small portion of activities are more importantand contribute most towards the objective. A largeproportion is trivial in their contribution. It canbe shown quickly which category is clearly moreimportant. Thus, the chart helps to identify the ‘VitalFew from Trivial Many’ and to concentrate on thevital few for improvement. Six-pack charts includedifferent six different packs and are provided in theformat of one diagram.Control chartsAmong seven SPC tools, control diagram is themost important part. Control chart based uponmeasurements of quality characteristics such asSqueeze Time, Weld Time, Hold Time and Pressureare called as control charts for variables. The processvariations are controlled using control diagrams, anddefective products are avoided by some preventiveactions. Here, it means controls diagrams R, and Xare the most popular control charts.Control charts R, XX charts control the process average whereas Rcharts control the process dispersion or variability.If X1, X2 Xn is a sample with n members for givenquantitative attributes, and then the mean for thesesamples are as follows:x1 x 2 x3 . xn Xn1716According to the central limit theorem, selectingappropriate sample size, distribution X tends tonormal distribution. Thus, 99.72% of data is placedwithin the following control limits.ucl µ x 3σ xcl µ xlcl µ x 3σ xHence, control limits for X diagram can bedetermined, having the mean and standard deviationfor Xs society [14].Statistical principles for R (range) control chartsR is applied as an estimate for standard deviation. Theprocess variability are controlled, depicting R valueson the control diagram. This control diagram is calledR diagram. Limits calculations for these diagramsare performed as easily as X diagram calculations,assuming that Ri refer to variations between themaximum and minimum data in i-th sample. Whenthe control limits of diagrams are calculated usinginitial samples, it is necessary to depict the mean andrange oversamples on X , R Diagrams and connectthe points to each other on diagrams for studyingthem. If the points on diagrams show an out ofcontrol state or a non-random pattern, causes mustbe studied. Other on diagrams for studying them. Ifthe points on diagrams show an out of control stateor a non-random pattern, causes must be studied.Dispersion chartClearly, sampling must be performed during variousperiods with few numbers so that data would havethe most important attribute for comprehensiveness.Random sampling in long period of time is requiredto obtain better results. It is recommended that thenumber of data in each group not to exceed fromfive. Dispersion diagram shows data by the formatof its group as well as the data in each group whichis in vertical line. Dispersion diagram indicates thequantitative level of data in each group. It also showshow far data is quantitatively close to each other. Itallows us to compare different groups with eachother to identify the relationships among them interms of their component numbers. Finally, it helpsto compare process performance during variousperiods and evaluate it implicitly.HistogramHistogram represents variation in sets of datagraphically. Histograms are bar graph displayi.e., vertical rectangles drawn side by side. Themost generally used graph for showing frequencydistributions, in a set of data occurs. Many data
SIVAM ET AL.1717are categorized in a specific format in order thatthe problem can be understood and analysed moresimply. It is obvious that data grouping and graphicdisplay help us significantly to decide logically andeffectively. It provides an image for data, by whichthree following attributes can be understood andobserved more simply: a) Form of data frequencydistribution b) Location with central tendencyfor distribution c) Dispersion by distributiondevelopment. Usually, in the best situation, acommon pattern is the bell-shaped curve known asthe “normal distribution.” In a normal distribution,points are as likely to occur on one side of the averag
DEFECT ANALYSIS ON CASTING BY SIX SIGMA - QC TECHNIQUES TO MINIMIZE THE DEFECTS AND IMPROVE THE PRODUCTIVITY IN OIL PUMP CASTING SUNDAR SINGH SIVAM S.P 1*, .SARAVANAN2, N. PRADEEP2, S.RAJENDRAKUMAR , AND K. SATHIYAMOORTHY1 1Department of Mechanical Engineering, SRM University, Kancheepuram District, Kattankulathur- 603203,