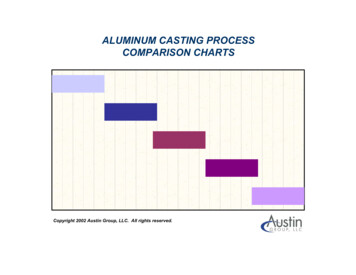
Transcription
ALUMINUM CASTING PROCESSCOMPARISON CHARTSCopyright 2002 Austin Group, LLC. All rights reserved.
A Qualitative Comparison of Several Competing Processes for theProduction of Aluminum CastingsThe following charts are intended to provide a relative guide to compare various aluminum castingmethods. It is important to note that, the actual costs and casting results will vary significantly forany given project. The complexity of the part, the number of cores or pulls, the engineering anddesign time and customer requirements will all have a significant impact on the cost to produce apart with any of the compared methods. An attempt to provide specific comparison data for a givenpart would be highly sensitive to that particular part. Therefore, a composite of existing source dataincluding foundry results, professional society literature, equipment manufacturer comments andpersonal experience was used to generate the comparison charts. Foundries, foam molders andtool builders contributed to the collection of the data.Copyright 2002 Austin Group, LLC. All rights reserved.
ALUMINUM CASTING PROCESSES - COMPARISON ESFINISHRANGELOST FOAMA metal mold is used to produce foam patternsFoam patterns are invested in sand. MoltenOunces upmetal is poured on to the foam patterns throughto 300 lbs.gating. The foam evaporates and is replaced bmetal. .007" to 1" .010 1-3"then add .003"/inchLOST WAXA metal mold is used to produce wax replicas.Wax replicas are placed in an investmentOunces upmaterial. Wax is melted out and molten metal ito 20 lbs.poured into cavity. The mold is broken and thecasting is removed.Treated sand is molded around a wood or metapattern. The mold halves are opened and theOunces upSAND CASTING pattern is removed. Metal is poured into theto tonscavity. The mold is broken and the casting isremovedMINIMUMDRAFTREQUIREDSamples: 3 to 8weeksProduction: 6 to18 weeks63-250 RMS.150"All .004" to ½" .005" to 3"then add .003"/inch63-250 RMSNone.060"Under 1000 4000 to 40000Samples: 6 to10 weeksProduction: 8 to12 weeks .03" to 6"then add .003"/inchAdd .020" to.090" acrossparting line200-550RMS1 to 5 degreesAll 1000 to 10000Samples: 2 to 6weeksProduction: 2 to6 weeks .010" to 1"then add .002"/inch.Add .020"across parting line125-150RMS1/2 to zerodegreesAll 3000 to 30000Samples: 3 to 6weeksProduction: 3 to6 weeks.030" to .060"2500 10000 to 300000Samples: 8 to12 weeksProduction: 10to 18 weeks.070"Prototypes up to250 pcs. 3000 to 15000Samples: 2 to10 weeksProduction: 4 to8 weeks500 12000 to 100000Samples: 6 to 8weeksProduction: 8 to20 weeksDIE CASTING .002"/inchSteel dies, sometimes water cooled, are injecteOunces upAdd .015"32-63 RMSwith molten aluminum. The material solidifies,to 20 lbs.across parting linethe die is opened and the casting ejected.1 to 3 degrees .005 to 2"A plaster slurry is poured into the patternthen addhalves. After setting, the mold is removed fromOunces up63-125 RMS 1/2 to 2 degrees .002"/inchPLASTER MOLD pattern, baked and assembled. Metal is pouredto 50 lbs.Add .010"into the cavity. The mold is broken and theacross parting linecasting removedCopyright 2002 Austin Group, LLC. All rights reserved.NOMINALLEAD TIMES 8000 to 120000Sand is "Vacuum-packed" around patternhalves. The pattern is removed and metal is Ounces uppoured into the cavity. The vacuum is released to 150 lbs.and the casting is removedMolten metal is poured into a steel or iron mold 1 lb. up toThe mold is opened and the casting removed. 100 lbs.TYPICALTOOLINGCOSTS1/4 to ICALSECTIONORDERTHICKNESS QUANTITIES .015" to 1"then add .002"/inchAdd .010" to.030" acrossparting line150-300RMS2 to 5 degrees.25".125".188"
ALUMINUM CASTING PROCESS COMPARISONTOOL LIFELength of tool life is one of the strongest aspects of the Lost Foam process. Life expectancy of Lost Foamtooling is in the hundreds of thousands cycles range with only low-level maintenance requirements. Vprocess and sand casting methods offer intermediate tool life but also require increased dimensionaltolerances due to pattern wear. Permanent mold casting and die casting typically have the shortest tool life.LOST FOAMPROCESSV-PROCESSSANDDIE CASTPERM. MOLDSHORT LIFELONG LIFETOOL LIFE (Based on Expected Cycles)Copyright 2002 Austin Group, LLC. All rights reserved.
ALUMINUM CASTING PROCESS COMPARISONTOOL COSTConventional sand casting offers the lowest cost tool with the V-process having comparable costs for simpletools but varying with complexity. The Lost Foam process allows a wide range of simple to very complexparts resulting in the wide tool cost range. Permanent mold and die cast tools are comparable on simpletooling. Cast iron and steel are more expensive to work with than aluminum, which accounts for the higherstarting costs for permanent mold and die casting tools. Die cast tools increase sharply in cost withcomplexity.140000COST (US CESSPERM. MOLDPROCESSCopyright 2002 Austin Group, LLC. All rights reserved.LOST FOAMDIE CAST
ALUMINUM CASTING PROCESS COMPARISONCOMPLEXITY OF DESIGNThe Lost Foam process will allow the most complex part designs of all the methods. Foams can be assembledand glued together to produce exceptionally complicated castings, often combining two or more castings intoone piece. Die casting with the use of core pulls can produce complex one piece parts. V-process castingstypically do not use cores and are simpler. Sand casting and permanent mold methods with their use of coresallow the next highest level of complexity.LOST FOAMPROCESSDIESANDPERM. MOLDV-PROCESSSIMPLECOMPLEXCOMPLEXITY OF DESIGNCopyright 2002 Austin Group, LLC. All rights reserved.
ALUMINUM CASTING PROCESS COMPARISONRELATIVE SURFACE FINISHA wide range of surface finishes are produced by the various casting methods. Green sand casting willproduce the worst surface finish while die casting typically produces the best results when dies are new. TheLost Foam casting surface is usually better than all of the processes with the exception of die casting. Inaddition, the surface finish in the Lost Foam process should be consistent throughout the tool life cycle. Diecast and permanent mold surface finish will deteriorate as more cycles are run.DIE CASTPROCESSLOST FOAMV-PROCESSPERM. THRMS VALUECopyright 2002 Austin Group, LLC. All rights reserved.350
ALUMINUM CASTING PROCESS COMPARISONDIMENSIONAL TOLERANCESDie casting is expected to result in the highest level of dimensional accuracy. Lost Foam and V-processmethods are typically better than permanent mold casting. Green sand casting yields the least accurateresults .002" / 1"DIE CAST .007" / 1"PROCESSLOST FOAM .010" / 1"V-PROCESS .015" / 1"01 " / 1"PERM. MOLD .030" / 1"SANDLEAST ACCURATEMOST ACCURATEDIMENSIONAL TOLERANCESCopyright 2002 Austin Group, LLC. All rights reserved.
ALUMINUM CASTING PROCESS COMPARISONEASE OF ENGINEERING CHANGESEngineering or tooling changes are expected to be easiest to implement on sand casting equipment, wherealuminum or even wood patterns are used. The V-process also allows relatively easy changes due to patternmaterial. The Lost Foam process use of aluminum tooling makes tool changes the next easiest to change.Cast iron permanent molds and steel dies are the most difficult to change.SANDPROCESSV-PROCESSLOST FOAMPERM. MOLDDIE CASTDIFFICULTEASYEASE OF ENGINEERING CHANGESCopyright 2002 Austin Group, LLC. All rights reserved.
ALUMINUM CASTING PROCESS COMPARISONNEAR NET SHAPE CAPABILITYDie casting will produce the best near-net-shape casting. The combination of a good surface finish,dimensional accuracy and added features make the Lost Foam process a close second to die casting. Vprocess patterns are subject to wear but produce good results in low volumes. Permanent mold and greensand methods have the least potential for producing near-net-shape castings.DIE CASTPROCESSLOST FOAMV-PROCESSPERM. MOLDSANDLEAST POTENTIALHIGHEST POTENTIALNEAR NET SHAPE CAPABILITYCopyright 2002 Austin Group, LLC. All rights reserved.
ALUMINUM CASTING PROCESS COMPARISONINTERNAL METAL SOUNDNESSPermanent mold has demonstrated the best internal metal soundness. The Lost Foam process has smoothmetal flow characteristics resulting in less gas entrapment during pouring and producing results comparableto Permanent Mold. The lack of cores or sand bonding media in the Lost Foam process eliminates gasabsorption from the mold during solidification. By contrast, die castings are noted for air and gas entrapmentand can be expected to demonstrate the most porous metal characteristics.PERM. MOLDPROCESSLOST FOAMV-PROCESSSANDDIE CASTPOROUSSOLIDINTERNAL METAL SOUNDNESSCopyright 2002 Austin Group, LLC. All rights reserved.
A wide range of surface finishes are produced by the various casting methods. Green sand casting will produce the worst surface finish while die casting typically produces the best results when dies are new. The Lost Foam casting surface is usually better than all of File Size: 687KBPage Count: 11