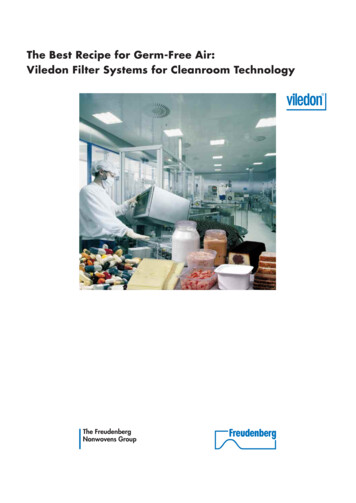
Transcription
The Best Recipe for Germ-Free Air:Viledon Filter Systems for Cleanroom Technology
Where every single germ counts.The pharmaceutical industry bears an unusually high degree of responsibility to bothmankind and the natural environment duringthe entire production cycle for solid or liquidmedicines. Beginning with research and development, continuing through the productionprocess all the way to final packaging, ultrastringent safety regulations have to be complied with, designed to minimise the risk ofcontamination with micro-organisms, particlesand pyrogens.The table below shows the classification ofclean areas under the GMP (Good Manufacturing Practice) Guidelines drawn up by theAmerican FDA (Food & Drug Administration)and also by the EC, combined with a recommendation for the filter classes to be installedin the final stage. Detailed definitions of theroom classes concerned can be found in thespecialised literature. Careful attention mustbe paid to the production line’s operatingmodes (at rest, production).Equally stringent safety regulations apply inthe related fields of biotechnics and medicaltechnology, as well as the production of foodstuffs and cosmetics free of preservatives, allof which necessitate assured safety zonesduring particular stages of the process.To attain the clean air quality required, airfilters of different filter classes and designsare combined to form multi-stage systems.A crucial element in this context is the qualityof the air, whose maximised purity is essentialfor monitored chemical/pharmaceutical processes and numerous others as well.A prefiltration unit, usually comprising twostages, collects coarse to fine particles, so asto store the principal mass of air contaminants.This reduces the loading on the final HEPA/ULPAfilters, which by collecting ultra-fine particlesdetermine the actual quality of the clean airinvolved.The high degree of air purity required forproducing and packaging sterile medicines,the handling of hazardous substances, and theprocessing of products not amenable to finalsterilisation, or of highly perishable foodstuffs,can be created only in faultlessly functioningclean areas (cleanrooms, safety workbenches,isolators, etc.).In order to achieve maximised clean air quality directly at the sterile product, the air is delivered in a low-turbulence displacement flow.In the adjoining areas, the number of air changes per hours should be chosen to suit theparticular room, the equipment and the staffconcerned. The supply of filtered air to anyzone must be dimensioned so as to ensureEC Recommendations(GMP Guidelines)GMP Guidelines of the FDAAir flowRecommended filterclasses for thefinal HEPA/ULPAfiltersRoom ClassMaximum numberof particles 0.5 µmMaximum numberof germs (CFUs*)A100 per ft 33,531 per m30.1 per ft33 per m3low-turbulent/„laminar“H 13 / H 14B——turbulentH 13 / H 14C100,000 per ft 33,531,467 per m32.5 per ft 388 per m3turbulentH 13D——turbulentH 11 / H 13* CFUs Colony-Forming Units
. it pays to be well on the safe sidethat no matter what the operating conditionsare, effective air flow is guaranteed and anoverpressure is maintained against adjoiningareas with a lesser risk.The air flows are carefully routed so that particles generated by a person, a process or amachine are not carried into zones with ahigher risk.When handling hazardous substances, theexhaust air has to be cleaned by HEPA/ULPAfilters too.A typical cleanroom concept for pharmaceutical processes is illustrated diagrammaticallyon the right.The absolute reliability of the filters used, interms of collection efficiency, leakproof construction and secure mounting in the supportsystem, is crucial for the safe manufacture ofsterile products. Choosing a concomitantlyhigh-quality filter system will always pay off,not least in terms of cleanroom validation andmonitoring.For cleanroom installations, Freudenberg offers a complete range of filters in the ClassesG 3 to U 17, meeting even the toughest of requirements for efficient and dependable operation. The choice available also includes ournewly developed combination filters for reducing pollutant gases and unwanted odours.Pharmaceutical cleanroom with Viledon HEPA filtersIntake airH13/ H14FiltersH13/ H14 FiltersF5 FiltersF7/F9 FiltersTurbulentareaLaminar-flowareaF9 FiltersH13 FiltersExhaust airTypical cleanroom concept for pharmaceutical processesTheir unique media structure provides ClassF 7 particle filtration plus effective gas adsorptionwith activated carbon in a single filter stage.So they can be used as replacements both forparticle filters and for activated-carbon filters,offering high additional utility compactly designed in.Vertical-flow cleanroom module with Viledon HEPA filters
Economical top performance in the first place:Viledon Compact pocket filtersViledon Compact pocket filters are depthloading filters. The particles are arrested inthe filter medium at the fiber surface.Viledon Compact pocket filters are predominantly used in prefiltration and have givencost-efficient, dependable service in a widerange of different applications. Their particular design features offer numerous advantages:The filter media of synthetic/organic fibersare progressive or triple-layered in structureand provide high dust holding capacity inconjunction with a slow rise in pressure dropand thus long lifetimes.Inherently rigid design of the filter pocketsensures uniform dust storage. The pocketswill neither sag nor collapse, precluding anypossibility of dust penetration at shutdowns orload changes. Even with high dust loads anddamp conditions the inherent rigidity and thefiltration efficiency are fully maintained.The filter pockets are welded to preventleaks and securely foamed into the polyurethane front frame; dust penetration is thusreliably precluded even at high pressure drops.The welded-in spacers ensure optimumshaping of the filter pockets during operation,preventing any loss of active filtering area dueto pocket surface contact.500 µm3-layer nonwoven filter medium, inner layer electrostaticallyspun microfibersThe polyurethane front frame is corrosionproof and reinforced by a foamed-in profilefor maximum mechanical strength.The entire filter element is moistureresistant up to 100% relative humidity, thermally stable up to 70 C, stands up well tomost chemicals, and can be incinerated completely.Low maintenance and servicing costs.High-quality accessories, like a mountingframe made of stainless steel or galvanizedsheeting, with a positive spring-lock systemand a plug-in rubber seal.Viledon Compact pocket filters – the design assets
Safety in the last instance:Viledon MaxiPleat and HEPA/ULPA filtersViledon MaxiPleat and HEPA/ULPA filtersconstitute a technological quantum leap in thefield of rigid/cassette filters. Their innovativedesign ensures a performance profile that paysoff all along the line:A patented thermal embossing processguarantees optimum pleat geometry with equidistant spacing, as well as homogeneous airpassage at a very low pressure drop.The V-shaped pleat configuration ensuresfull utilisation of the filter area with uniformdust deposition. This in turn means long usefullifetimes and exceptionally cost-efficient, reliable operation.The filter’s entire face area is evenly utilised without being impeded by vertical supports, i.e. superfluous air turbulence with resultant high pressure drops is precluded.Maximised operational reliability, thanksto interaction of the various material characteristics and process steps: high-strength filtermedium, optimum dimensional stability ofthe pleat pack, leakproof integration in adistortion-resistant frame.500 µmHigh-strength glassfiber filter medium with a special bondersystemLow-turbulence downstream air flow thanksto equidistant, geometrically precise pleats.The frames of the MaxiPleat filters aremade of halogen-free plastic. HEPA/ULPA filters are available in a wide range of framevariants, like MDF, anodised aluminium, galvanised steel sheeting, stainless steel or aluminium sheeting, plus complete filter/hood modules for single-flow configuration. All filterscan be fitted with protection grids on request.Leakproof mounting of the HEPA/ULPAfilters is assured by a continuous, foamed-onPU seal or a gel-channel/knife-edge configuration for fluid sealing systems.The filter elements are light in weight anddisposal-friendly, as the innovative conversiontechnology minimizes the use of sealing andpleat-fixing agents. All filters with non-metalframe versions are completely incinerable.All MaxiPleat and HEPA/ULPA filters aremoisture-resistant up to 100% relative humidity and thermally stable up to 70 C, withpeaks up to 80 C.Low maintenance and servicing costs.Optimum pleat geometry and equidistance due to patented embossing process
Technical data overviewFilter classto EN 779G 35 SF 45 SG 35 SLF 40G3G4G3G4F 50T 60F5F6MF 70MF 90MX 75MX 85MX 95MX 98F6F7F6F7F8F9Front dimensions595x 595 mm 595x 595 mm 595x 595 mm 595x 595 mm 595 x 595 mm 592 x 592 mm 592x 592 mmstandard elementOverall depthNominalvolume flow rateInitial pressuredrop at nominalvolume flow rateRecommendedfinal pressuredrop*Averagearrestance/ASHRAE dustAverageefficiencyDust holdingcapacity/ASHRAE dustMoistureresistance/rel. humidityThermalstability/temporarypeaks330 mm650 mm650 mm650 mm650 mm292 mm292 mm3,400 m3/h4,250 m3/h4,250 m3/h4,250 m3/h4,250 m3/h4,250 m3/h4,250 m3/h20 Pa20 Pa100 Pa120 Pa30 Pa65 Pa65 Pa40 Pa45 Pa120 Pa110 Pa150 Pa200 Pa200 Pa250 Pa400 Pa400 Pa400 Pa400 Pa86 %87 %95 %95 %97 %99 % 99 %––51 %63 %75 %85 %75 %86 %92 %96 %1,180 g2,300 g690 g510 g1,425 g1,585 g700 g590 g1,380 g550 g570 g450 g100 %100 %100 %100 %100 %100 %100 %70 C70 C70 C70 C70 C70 C70 C80 C80 C80 C80 C80 C80 C80 C99 % 99 % 99 %* This figure is recommended out of cost-efficiency considerations. It can be exceeded in certain applications without problems.Further technical data and available sizes of Viledon filters can be found in the corresponding data sheets.
Filter classto EN 1822SF 11SF 13SF 13SF 13SF 14Filter/HoodmoduleH 11H 13H 13H 13H 14H 14Front dimensions610x 610 mm 610x 610 mm 610 x 610 mm 610x 610 mm 610x 610 mmstandard element610 x1220 mmOverall depth292 mm78 mm150 mm292 mm71 mm92 mm140 mmPleat depth200 mm280 mm50 mm100 mm200 mm280 mm50 mm70 mm50 mm70 mm1,000 m3/h1,500 m3/h600 m3/h1,200 m3/h125 Pa145 Pa100 Pa120 PaNominal volume 3,000 m 3/hflow rate for3standard element 3,400 m /h2,500 m3/h3,400 m3/hInitial pressuredrop at nominalvolume flow rate160 Pa250 Pa250 Pa250 PaRecommendedfinal pressuredrop*600 Pa600 Pa600 Pa600 Pa600 Pa600 PaInitial efficiencyfor MPPS** 95 % 99.95 % 99.95 % 99.95 % 99.995 % 99.995 %Initial efficiencyto DIN 24184 98 % 99.97 % 99.97 % 99.97 %––Utilizationcategoryto ZH/1/487(BIA test)–K 1, K 2K 1, K 2K 1, K 2––Moistureresistance/rel. humidity100 %100 %100 %100 %100 %100 %Thermalstability80 C80 C80 C80 C80 C80 C** MPPS Most Penetrating Particle Size Efficiency minimum)( The figures given are mean values subject to tolerancesdue to the normal production variations.
Quality probed to perfectionReg. Nr. 1420Freudenberg Vliesstoffe KGFilter DivisionWeinheim/GermanyMulti-scanner for HEPA and ULPA filtersConsistently high quality of the filter mediaused is essential if the completed filter elements are to perform properly.For quality assurance of HEPA and ULPA filters, the corresponding filter media are testedby means of a newly developed 18-channelCNC (Condensation Nuclei Counter) test standto measure pressure drop and collection efficiency. This enables the specific minimumcurve with the MPPS (Most Penetrating Particle Size / efficiency minimum) to be determined for the medium under test.The MPPS concerned will later be used as thetest particle size in the multi-scan test for finalinspection of the completed filter elements.In accordance with the relevant standard,every single HEPA filter of the H13 class issubjected to the approved oil-mist-test to ensure there are no leaks.The multi-scan test stand has been developedspecifically for certification testing of highquality cleanroom filters. The multi-scannerdetermines the pressure drop at nominalvolume flow, the clean-air-side velocity profile,the efficiency for MPPS, and any leak pointsat the horizontally inserted filter element.During the scan operation to determine theindividual filter efficiency, up to 30 infeednozzle/probe pairs in a comb configuration(connected to a corresponding number ofCNCs) move across the filter’s surface.The test reports generated by the multiscanner are an important constituent of thequalification and validation documents required for submission to supervising authorities.You will find more detailed information on ourrange of filters in our product-specific literature.Give us a call, we’re here to help you!Numbersof particle825586604649534407old l:Threshold:15 Filter DivisionD - 69465 WeinheimTel. 49 (0) 62 01- 80-62 65 Fax 49 (0) 62 01- 88-62 99ack /trScan99.997% for MPPS181,628,000 Part/100 ms45,407 Part/100 msMulti-scan test report for a H14 filterFreudenberg Vliesstoffe KG10Filter5width1LR 072 05/99. Printed on paper bleached without chlorine.At Freudenberg, quality is an across-the-boardcommitment, which starts off with full comprehension of the customer’s requirements, before translating these into products, processesand services. A modern quality managementsystem to ISO 9001 monitors all operations,from the very beginning of development workand application-engineering consultancy all theway through to delivery of the finished product.
Viledon Compact pocket filters Viledon Compact pocket filters - the design assets Viledon Compact pocket filters are depth-loading filters. The particles are arrested in the filter medium at the fiber surface. Viledon Compact pocket filters are predomi-nantly used in prefiltration and have given cost-efficient, dependable service in a wide