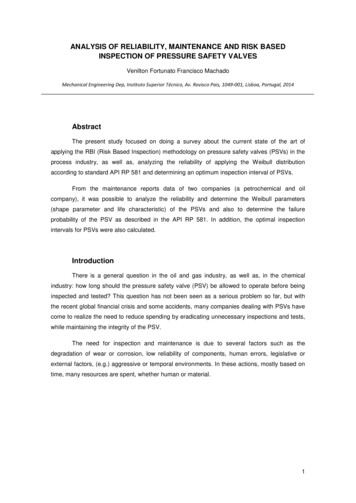
Transcription
ANALYSIS OF RELIABILITY, MAINTENANCE AND RISK BASEDINSPECTION OF PRESSURE SAFETY VALVESVenilton Fortunato Francisco MachadoMechanical Engineering Dep, Instituto Superior Tรฉcnico, Av. Rovisco Pais, 1049-001, Lisboa, Portugal, 2014AbstractThe present study focused on doing a survey about the current state of the art ofapplying the RBI (Risk Based Inspection) methodology on pressure safety valves (PSVs) in theprocess industry, as well as, analyzing the reliability of applying the Weibull distributionaccording to standard API RP 581 and determining an optimum inspection interval of PSVs.From the maintenance reports data of two companies (a petrochemical and oilcompany), it was possible to analyze the reliability and determine the Weibull parameters(shape parameter and life characteristic) of the PSVs and also to determine the failureprobability of the PSV as described in the API RP 581. In addition, the optimal inspectionintervals for PSVs were also calculated.IntroductionThere is a general question in the oil and gas industry, as well as, in the chemicalindustry: how long should the pressure safety valve (PSV) be allowed to operate before beinginspected and tested? This question has not been seen as a serious problem so far, but withthe recent global financial crisis and some accidents, many companies dealing with PSVs havecome to realize the need to reduce spending by eradicating unnecessary inspections and tests,while maintaining the integrity of the PSV.The need for inspection and maintenance is due to several factors such as thedegradation of wear or corrosion, low reliability of components, human errors, legislative orexternal factors, (e.g.) aggressive or temporal environments. In these actions, mostly based ontime, many resources are spent, whether human or material.1
Pressure safety valvesThe pressure safety valve as shown in figure 1, also called PRD (Pressure ReliefValve), pressure relief or simply as safety valve, is an automatic device, moved by a springwhich opens with a pre-established pressure, relieving excess the of pressure and closesproviding good seal when conditions return to normal. It is widely used in the process industry.A PSV is, in many cases, the ultimate protective device for the equipment integrity. It isimportant to ensure that the PSV can operate at all times and all circumstances, and shouldalso be understood as a valve for overpressure protection.Pressure safety valves are subdivided into two groups: conventional PSV figure 1 a)and Balanced PSV figure 1 b).b)a)Figure 1 - a) Convencional PSV; b) Balanced PSVStandard API RP 580 and 581 applied to PSVsThe standard API RP 580 is often used to ensure the smooth operation and properinstallation of PSVs project. This standard provides information on the use of risk analysis todevelop an effective inspection plan.The standard API RP 581 provides quantitative procedures to establish an inspectionprogram using risk-based methods for pressurized fixed equipment, including pressure vessel,piping, tankage, pressure relief devices and heat exchanger tube bundles.2
Estimation of optimum and testing interval for PSV- Case studyIn the three case studies hereby presented, it was analysed the report data of twocompanies, a petrochemical and an oil company. The aim of this study was to estimate anoptimal inspection interval of PSVs. All tables used in the three cases are described in API RP581. The duration of inspection time considered was 5 years.Case 1From the maintenance report of a Petrochemical Industry was possible to obtain thedata as shown in table 1.Table 1 - Data of petrochemical companyTotal of PSVsPSV opens below Set PressurePSVs with leakagePSV opens at (0.9 TP/SP 1.3)PSV opens above set pressure 1.3 SPFluid Temperature3775187T 260 The 37 PSVs operated under the following conditions:-Severity: mild T 500 ( 260 );Types of PSVs: Conventional; from graph 7.6 ๐๐,๐ 0.15 (see API RP 581)Discharge for closed system and the demand rate(๐ท๐ ๐ ): 0.25 (assuming the averagevalues for all overpressure conditions).From table 1, data of leakage PSVs will not be used, since it is intended to establish anoptimum inspection interval of PSVs that fails to open. The results of the 32 PSVs tests areshown in table 2, ranked in increasing order of division on TP/SP where TP is the test pressureand SP is the set ๏ฟฝ๏ฟฝ๏ฟฝ๐ฒ121123102212221Table 2 - Pressure tests results๐๐๐ฅ๐๐ญ๐ข๐ฏ๐ ๐ ๐ซ๐๐ช๐ฎ๐๐ง๐๐ฒ[%] ๐๐ฎ๐ฆ๐ฎ๐ฅ๐๐ญ๐ข๐ฏ๐ ๐ ๐ซ๐๐ช๐ฎ๐๐ง๐๐ฒ 568,757578,12584,37590,62596,8751003
Considering a range of study of 0.7 TP/SP 1.5, with pressure tests results, a graphwas built (TP/SP ratio and the cumulative frequency), as shown in figure 2.TP/SPCumulative distribuition 5%31,3%21,9%15,6%12,5%9,4%3,1%Figure 2 - Ratio TP/SP and cumulative frequencyAccording to fluid severity: mild, T 500 ( 260 ) of the PSVs data, it is determinedthe Weibull parameters from table 7.5 (see API 581), therefore, ๐ฝ 1.837.875years. Table 3 presents the calculations according to standard API RP 581.and ๐๐๐๐ Table 3 โ Calculation according to API RP 581FormulasSee API RP 581๐น๐๐น๐๐๐น๐๐ ๐๐๐ ๐๐๐ ๐ฃ๐๐ ๐ฃ1 ๐๐3.375 ๐๐ด๐๐Results0.75 1.3 e ๐๐ 4 ๐๐ด๐๐0.8Table 7.6๐๐๐๐ ๐น๐ ๐น๐๐ ๐น๐๐๐ฃ ๐๐๐๐๐ฝ๐ก ๐๐ ๐ฃ๐๐๐,๐๐๐๐๐ 1 ๐ ๏ฟฝ๏ฟฝ๏ฟฝ๐๐๐ 1 ๏ฟฝ๏ฟฝ๏ฟฝ๐๐,๐๐๐๐ 1 ๐ถ๐น๐๐๐ ๐ 25 ๏ฟฝ๏ฟฝ๐๐ก ๐๐,๐๐๐๐๐ 0.2 ๐๐,๐๐๐๐๐ 0.2 ๐๐,๐๐๐๐ ๏ฟฝ๏ฟฝ 1๐๐ ๐ฃ๐ฝ ln 1 ๐๐,๐ค๐๐ก ๐ก ๐ฝ ๐๐ข๐๐๐๐๐๐,๐ 1 ๐๐๐ ๐ฃ๐๐,๐ ๐๐๐๐,๐ ๐ท๐ ๐ ๐๐,๐๐ก๐๐๐ ๐ ๐๐ข๐๐ ln 1 1๐๐ ๐ฃ๐๐,๐ ๐ฝ6.69%22.034 [years]6.69%0.25%10 [months]For the first case of study (case1), which is the case of a petrochemical Industry, 32PSVs were studied. The results show that for the current case of the Company, which operatesunder mild conditions in terms of severity of fluid (๐ 260 ), it has small probability of failure at4
opening of 0.25 % in a range of 5 years of inspection, and the optimum inspection time for thiscase is once every 10 months.Case 2From the maintenance report of the oil company, it was possible to obtain the datashown in table 4.Table 4 - Data of PSVs from an Oil CompanyTotal de PSVsPSV Opens at (0.9 TP/SP 1.3)Opens above set pressure 1.3 SPPSVs with leakageFluid Temperature342626T 260 The 28 PSVs operated under the following conditions:-Severity service: severe T 500 ( 260 );-Types of PSVs: Conventional-Discharge for closed system and the demand rate (๐ท๐ ๐ ): 0.25 (average overpressure).From table 4, data of leakage PSVs will not be used, since it is intended to establish anoptimum inspection interval of PSVs that fails to open. The results of the 28 PSVs tests areshown in table 5, ranked in increasing order of division on TP/SP.TP/SPTable 5 - Pressure test resultsFrequency%FrequencyCumulative ,01313,5792,861,30213,5796,431,35213,57100,005
Considering a range of study of 0.92 TP/SP 1.35, with pressure test results a graphCumulative frequency[%]was built (TP/SP ratio and the cumulative frequency), as shown in figure 3.100,080,060,040,020,00,00,811,21,4TP/SPFigure 3 - Ratio TP/SP and cumulative frequency.According to fluid severity service: severe T 500 ( 260 ) of the PSVs data, it isdetermined the Weibull parameters from table 7.5 (see API 581), therefore, ๐ฝ 1.8and๐๐๐๐ 13.2 years. From graph 7.6 (see API 581) ๐๐,๐ 0.15 and table 6 presents thecalculations according to API RP ๏ฟฝ๏ฟฝ 3.375 ๐๐ด๐๐ 1.3 e ๐๐ 4 ๏ฟฝ๏ฟฝ๐๐ ๐ฃ๐๐,๐ค๐๐ก ๏ฟฝ๏ฟฝ๏ฟฝTable 7.6 ๐น๐ ๐น๐๐ ๐น๐๐๐ฃ ๐๐๐๐๐ฝ๐ก ๏ฟฝ๏ฟฝ๏ฟฝ๐ 1 ๏ฟฝ๏ฟฝ๏ฟฝ๐ 1 ๏ฟฝ๏ฟฝ๏ฟฝ๐๐,๐๐๐๐ 1 ๐ถ๐น๐๐๐ ๐ ๐๐,๐๐๐๐๐ 0.2 ๏ฟฝ๏ฟฝ๏ฟฝ๐ ๐ก 0.2 ๐๐๐๐๐ก๐๐ ๐ฃ1๐ฝ ln 1 ๐๐,๐ค๐๐ก ๐ก ๐ฝ ๐๐ข๐๐๐๐๐๐,๐ 1 ๐๐๐ ๐ฃ๐๐,๐ ๐๐๐๐,๐ ๐ท๐ ๐ ๐๐,๐๐ก๐๐๐ ๐ ๐๐ข๐๐ ln 1 1๐๐ ๐ฃ๐๐,๐ ๐ฝ17.920 ๏ฟฝ๏ฟฝ๐๐ ๐ก๐๐๐๐ 31.2%8.631 [years]31.20%1.2%9 [months]For the second case of study (case 2), which is the case of the oil industry, 28 PSVswere studied. The results show that for the current case of the company, which operates undersevere conditions in terms of severity of fluid (๐ 260 ), it has a probability of failure at6
opening of 1.2% in a range of 5 years of inspection, and the optimum inspection time for thiscase is once every 9 months.Case 3In this case, data from oil company (see table 4) is hereby analysed. 6 PSVs failed dueto leakage, and therefore, it is estimated and analysed the growth of the probability of failurewith the inspection time duration.The 6 PSVs operated in a severe condition in terms of fluid severity (๐ 500 ( 260 )), from table 7.12 (see API 581) have ๐ฝ 1.6 and ๐๐๐๐ 13.1 years. Since the PSVhas a metal seat, the adjustment factor is ๐น๐ Table 7.6 (API 581)๐๐๐๐ ๐น๐ ๐น๐๐๐ฃ ๏ฟฝ๐,๐ค๐๐ก๐๐ข๐๐Results10.67.86 [years]-๐๐ ๐ฃ๐๐,๐ค๐๐ก ๏ฟฝ๏ฟฝ๏ฟฝ๐๐๐ฝ๐ก ๏ฟฝ๏ฟฝ๏ฟฝ๐ 1 ๏ฟฝ๏ฟฝ๏ฟฝ๐ 1 ๏ฟฝ๏ฟฝ๏ฟฝ๐๐,๐๐๐๐ 1 ๐ถ๐น๐๐๐ ๐ ๐๐,๐๐๐๐๐ 0.2 ๏ฟฝ๏ฟฝ๏ฟฝ๐ 0.2 ๏ฟฝ๏ฟฝ๐ ๐ฃ๐๐,๐๐๐๐ ln 1 ๐๐,๐ค๐๐ก ๐๐ ๐ฃ๐๐๐ก๐๐๐ ๐๐ก38.43% 1 ๐๐ก ๐ฝ ๐๐ข๐๐๐๐ ๐ฃ๐ก๐๐๐ ๐ ๐๐ข๐๐ ln 1 ๐๐๐ก ๐๐๐๐34.32%8.59 [years]34.32%1 ๐ฝ4.9 yearsFor a better understanding of the results obtained, figure 4 shows the growth of theprobability of failure due to leakage with the optimal inspection time.Probability of failure due toleakage vs Inspection timeInspection time %34,32%26,57%18,42%10,51%3,78%1,32%Figure 4 - growth of the probability of failure due to leakage7
For the present case, if the company performs inspections once every 0.5 years (6months), the probability of failure of PSV due to leakage is 1.32%, and if the company conductsinspections once every 5 years, the probability of failure is 34.32%.ConclusionPressure safety valves play an important daily role in the process industry by protectingfacilities, human lives and invested capital. The only way to know if the PSV is operating well isto develop an effective inspection plan. This plan must guarantee the reliability of the PSV andensure that the PSV can operate at all times and all circumstances.The three cases studies analyzed in this article were used to determine the probabilityof failure of the PSVs and to estimate the optimal inspection intervals according to standard API581.In the first case (petrochemical industry), according to pressures test results and theseverity of the service (mild) it was possible to determine the probability of failure of the PSVand the optimal inspection time (once every 10 months).In the second case (oil company), according to pressure test results of the maintenancereports and the serviceโs severity (severe), the probability of failure is great than 35.40%. it isadvised that inspection has to be performed twice a year, or once every 9 months for bettercontrol of the failure.In the third case (the same oil company), 6 PSVs failed due to leakage and the optimalinspection time estimated is once every 6 months.The results show that the proposed solution, despite some limitations, is feasible for thedevelopment of this work, thus leaving a solid basis for a better risk analysis according tostandard API RP 581BibliographyAmerican Petroleum Institute, Risk-Based Inspection, API RP 580, November 2009American Petroleum Institute, Risk-Based Inspection Technology, API RP 581,September 2008.American Petroleum Institute, Seat Tightness of Pressure Relief Valves, API 527, July,1991.American Petroleum Institute, Pressure Vessel Inspection, code: In-Service Inspection,Rating, Repair, and Alteration, API 510-Downstream segment, June, 20068
Leser, LESER GmbH &Co.KG, 2013. [Online].Available:www.leser.com. Acedido [29setembro 2013].M.S.Jones Inspeรงรฃo Baseada no Risco โ Vรกlvulas de seguranรงa de Equipamentos sobpressรฃo, Lisboa, 2009.R. Assis, Apoio ร Decisรฃo em gestรฃo da Manutenรงรฃo โ fiabilidade e manutibilidade,Lisboa, Lidel, 2004R.B.Abertnethy, The new Weibull handbook, north Palm Beach, Florida, 2000.9
Standard API RP 580 and 581 applied to PSVs . The standard API RP 580 is often used to ensure the smooth operation and proper installation of PSVs project. This provides information on the use of risk analysis to standard develop an effective inspection plan. The standard API RP 581 provides quantitative procedures to establish an inspection program using risk-based methods for pressurized .File Size: 262KBPage Count: 9