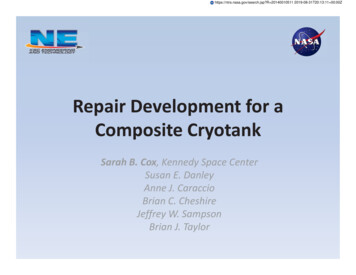
Transcription
https://ntrs.nasa.gov/search.jsp?R 20140010511 2019-08-31T20:13:11 00:00ZRepair Development for aComposite CryotankSarah B. Cox, Kennedy Space CenterSusan E. DanleyAnne J. CaraccioBrian C. CheshireJeffrey W. SampsonBrian J. Taylor
Agenda Background of Composites and CompositeCryotank Project Sandwich Panel Fabrication Repair Development and Testing
What is a Composite? Basic Definition: A material made up of two ormore different materials which keep theirindividual properties Advanced Composite Materials: A fiber reinforcedmatrix Reinforcement Matrix– Polymer/Epoxy– Metal– Ceramic–––––GlassAramid (Kevlar)CarbonCeramicNatural
Strategy for DevelopmentState of the art(SOA)NASA’s experiencewith compositeprimary structuresfor launch vehicles 5-m-dia. drystructures6/12/2014Leapfrogging the SOAputs NASA in aleadership position todrive technologydevelopment 10-m-dia. structures Cryotanks Pressurized habitationmodules Out-of-autoclave processing
Composite Cryotank Technologiesand Demonstration Multi-center team responsible for developing anddemonstrating advanced composite technologies Overall goal of the project is to achieve 30%weight savings 25% cost savings of LH2 compositecryotanks KSC Objectives– Understand the properties of the composites– Perform hands on repair work at KSC– Develop out of autoclave repair cure process
Material Property Testing Void Analysis– Microscopy– Combustion– Compared with Acid Digestionat Glenn32-ply quasi isotropic panel, 100X Mechanical Testing– Tensile 16 ply specimens, all in the samedirection– Short Beam Shear 32 ply specimens, all in the samedirection6
Repair Test Plan1. Fabricate sandwich panel2. Impact with 5.5 ft-lbs force(per ASTM 7136)3. Remove damaged area4. Scarf around damaged area5. Repair with a honeycomb coreplug and a patch6. Edgewise compression test oncontrol and repaired panels
Phase I: Repair Sandwich PanelsFace Sheets HR40/5320-1 Unitape Prepreg 8-ply quasi-layupCore 1.5” Aluminum Honeycomb FM-300 Film AdhesiveRepair Patch HR40/5320-1 Unitape Prepreg FM-300 Film AdhesiveCore Plug 1.5” Aluminum Honeycomb Hysol MA 562 Foaming Adhesive FM-300 Film Adhesive
Composite Panel Fabrication HR40/5320-1 Prepreg Unitape– Fibers preimpregnated with resin– Hand Layup onto flat tool– Out of Autoclave curing[0,90] Composite Microscopy Image
Composite Panel FabricationThe Panels Are Made by Hand Lay-up MethodPrepreg Sheets Hand Lay-upVacuum Debulk ofComposite PanelOven Cure of PanelUnder Vacuum
5320-1 Cure Cycle5320-1 Cure Cycle400Temperature (degrees F)350300250200150100500050100150200Time (minutes)250300350400
Sandwich Panel FabricationBreather ClothFilm AdhesiveVacuum BagPerforated FilmVacuum PortSealantAluminum CoreToolRelease FilmLaminate Face SheetDams (around entire part)
Sandwich Panels after ImpactPanel APanel CPanel BPanel D
Sandwich Panel Scarfing
Patch Preparation Methods Method I: Pre-cured Patch– Patch was cured in an oven with the standard cure cycle– Patch was bonded to the part at 350oF for 1 hour Method II: Co-cured Patch– Patch was cured on the part with a hot bonder– Used cure cycle of the material: 250oF for 3 hours and 350oFfor 2 hours Method III: Partially Cured Patch– Developed a method to determine the cure cycle based onresearch of previous work. Determined the best cure cyclefrom study to be: Patch partially cured at 200oF in an oven for 1 hour Patch fully cured at 350oF with the hot bonder for 2 hours on thepart
Repaired PanelsPanel A: Pre-cured PatchPanel C: Co-cured PatchPanel B: Pre-cured PatchPanel D: Co-cured Patch
Edgewise Compression Testing ASTM C 364: Standard Test Method for Edgewise CompressiveStrength of Sandwich Constructions Provides a load carrying capacity of the construction of thesandwich panels after a repair has been performed. Panels potted into end caps
Edgewise Compression TestingControl (no damage, no repair)MaximumCompressiveCompressivePanel Compressive Load Extension at Max Stress at MaxID(lbf)Load (in)Load (ksi)G517750.08252.4HError During Data Collection
Edgewise Compression TestingPre-cured PatchMaximumPanel Compressive LoadID(lbf)A46608B49494CompressiveExtension at MaxLoad (in)0.0710.075CompressiveStress at MaxLoad (ksi)47.450.0
Edgewise Compression TestingCo-cured PatchMaximumPanel Compressive LoadID(lbf)C38383D38992CompressiveExtension at MaxLoad (in)0.0590.059CompressiveStress at MaxLoad (ksi)42.239.3
Phase IA: Partially Cured Patches Partially curing the patch in the oven allowsthe patch to have some rigidity and hold itsshape but still have some flexibility to fullyconform to the part Beneficial for curves and complex shapes Decreases repair time by having commonlydamaged area shapes, and patch sizesavailable Decreases the cure time on the vehicle
Phase IA: Partially Cured PatchesIn order to determinethe optimal degree ofpartial cure, laminatepanels were repairedwith patches which sawa range of cureconditions
Patch Cures Patches cured in oven undervacuum at the temperatureand time given All patches were de-bulkedon the part for 30 minutesprior to hot bond cure Repairs cured on hot bonderat 250oF for time shown andthen at 350oF for 2 ure in OvenTemp Time(deg F) Hot BonderCure Time at250F (min)165150120165150120165150120
Tensile Testing Test panels were cut into 1” stripsand tested as a comparative ure in OvenTemp Time(deg F) Hot BonderCure Time at250F rvations After Oven CureStrength (psi)Patch was still tacky, pliable38107Patch was still tacky and pliable38689Patch was not very tacky or pliable43624Not very tacky or pliable32660Patch was not very tacky or pliable39209Patch was not very tacky or pliable54811Very Stiff31728Very Stiff, like it was fully cured49254Very stiff42049
Phase II: NDE during RepairProcess Three additional sandwich panels werefabricated with the same materials The panels received IR Thermography scansafter each event:– Fabrication– Impact (to 5 ft-lbs)– Repair Three patch methods: pre-cured, co-cured,and partially cured patches used on the panels
Initial IR Thermography ScanPlanned for Co-cured patchPlanned for partially cured patch Planned for pre-curedpatch
After Impact
After Impact
After Impact
After Repair – Co-cured Patch
After Repair – Partially CuredPatch
After Repair – Pre-cured Patch
Edgewise CompressionCo-cured PatchMaximumPanel Compressive LoadID(lbf)L34111CompressiveExtension at MaxLoad (in)0.054CompressiveStress at MaxLoad (ksi)34.6
Edgewise CompressionPartially Precured PatchMaximumPanel Compressive LoadID(lbf)M36117CompressiveExtension at MaxLoad (in)0.056CompressiveStress at MaxLoad (ksi)36.6
Edgewise CompressionPrecured PatchMaximumPanel Compressive LoadID(lbf)N38934CompressiveExtension at MaxLoad (in)0.059CompressiveStress at MaxLoad (ksi)39.5
Summary of ResultsPatchMaximumPanelCure Compressive y36117N Precured38934CompressiveExtension at MaxLoad ssiveStress at MaxLoad (ksi)52.447.450.042.239.334.636.639.5
Conclusions A comparative study of edgewise compressiontesting on repaired sandwich panels wascompleted Repairs with precured patches had higherloads than partially cured or cocured patches– This may be due to variations in hot bond curing– Need more data on partially cured patches
Future Work Test more panels with partial cure patches,incorporating lessons learned from previouswork Take a closer look at the heating profile of thehot bonder Perform repairs on curved panels
Questions?
References1.Mark J. Shuart, “Composites for Exploration.” SAMPE Conference and ExhibitionPresentation, PowerPoint. May 21-24, 20122.Douglas A. McCarville, et. al. (2013) “Manufacturing Overview of a 2.4 MeterComposite Cryotank.” SAMPE Conference Proceedings, Long Beach, CA, May 6-9,2013.3.Keller, R.L., Owen, W.S. “Process method to repair bismaleimide (BMI) compositestructures.” (2004). US Patent Number eller, R.L. and Spalding, J.F. “Process development protocol and vacuum bagprocess for carbon-epoxy prepreg.” US Patent Number 7857925.https://www.google.com/patents/US7857925
Backup
Impactor
Composites for Exploration ProjectVehicleHeavy LiftAtlas VDelta IVDia10 m5.4 m5.1 mArea 561 m2 311 m2 277 m2 A Multi-center team with the goal ofdeveloping a 10 m diameter payload fairingDemonstrate 25-30 percent weight savingsand 20-25 percent cost savings for compositecompared to metallic payload fairingstructuresCoEx ThrustSOAPanels for 10m-dia. barrelsNo compositesexperience at thisscaleAutomatedmanufacturingLimited to 7-mdia. barrelsOoA*technologiesMaturing foraerospace qualityDesigndatabaseNotdemonstrated for10-m-dia. barrels*out of autoclave
1/6th – Arc Panel Fabrication10 mAutomated Fiber Placement System1/6th Tool Fabrication
Panels Not CompletedPanel EPanel F
FM-300 Film Adhesive Core Plug 1.5" Aluminum Honeycomb Hysol MA 562 Foaming Adhesive FM-300 Film Adhesive . Composite Panel Fabrication HR40/5320-1 Prepreg Unitape - Fibers preimpregnated with resin - Hand Layup onto flat tool - Out of Autoclave curing [0,90] Composite Microscopy Image . Composite Panel Fabrication The Panels Are Made by Hand Lay-up Method Prepreg .