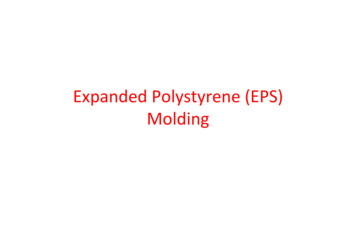
Transcription
Expanded Polystyrene (EPS)Molding
The concept of molten metal vaporizing afoamed polystyrene pattern was first patentedin 1958. In its original form, patterns werefabricated from expandable polystyreneinsulation board and surrounded with bondedsand after which the metal was poured. Withcertain improvements, this process is still in usetoday and is suited for large one‐of‐a‐kindcastings such as dies for stamping of largeautomotive sections and large dimension,heavy‐sectioned castings used by machine toolbuilders. Expanded polysty‐rene is suitable foruse with both ferrous and nonferrous metals.
The basic patent for the "cavity‐less process" (patent#2,830,343)* was issued to inventor H. E. Shroyer whoassigned U.S. Patent rights to Full Mold Process Incorporated.Actually the patent was not based on the production ofcastings, but on its first use — that of art castings. One of thefirst foamed polystyrene castings was the bronze statue"Pegasus" by A. Duca, sculptor and metallurgist at theMassachusetts Institute of Technol‐ogy. Since the originalpatent, several process improvement patents have beenissued. One of the earliest of these was U.S. Patent 3,157,924awarded to T. R. Smith whose development provided for theuse of un‐bonded sand as the medium for surrounding apolystyrene pattern prior to pouring. In this evaporativecasting process, *a pattern refers to the ex‐pandablepolystyrene or foamed polystyrene part that is vaporized bythe molten metal. A pattern is required for each casting.Figure 64 shows a foamed pattern and the casting producedfrom the use of this pattern.
The evaporative casting process is an economicalmethod for producing complex, close‐tolerancecastings using an expandable polystyrene patternand unbonded sand. Expandable polystyrene is athermoplastic material that can be molded into avariety of complex rigid shapes. Common uses forexpandable polystyrene include insulation board,hot drink cups, novelty items, packaging materialsas well as patterns for the foundry in‐dustry. Theexpertise for molding complex, thin‐walledpatterns with rela‐tively smooth surfaces and atthe low densities required for the casting pro‐cesshas also been achieved. With these developments,the evaporative casting process has now made itfeasible to produce high volume productioncastings.
The evaporative casting process involves attachingexpandable polystyrene patterns to an expandablepolystyrene gating system and then applying arefractory coating to the total assembly. After thecoating has been dried, the foam pattern assemblyis positioned on several inches of loose dry sand ina vented flask and additional sand is then addedwhile continuing to vi‐brate the flask until thepattern assembly is completely embedded in sand.A suitable downsprue is located above the gatingsystem and sand is again added until it is level tothe top of the sprue. Molten metal is poured intothe sprue, vaporizing the foam polystyrene andperfectly reproducing the pattern. Gases formedfrom the vaporized pattern permeate through thecoating on the pattern, the sand and finally throughthe flask vents.
The term expandable polystyrene applies todiscrete particles of thermo‐plasticpolystyrene which contains 5‐8% of a volatileliquid expanding agent. The capacity toexpand to a broad range of densities,excellent thermoinsulating efficiency, impactand shock absorbency and the ability to bemolded into simple and complex rigid shapesmakes expandable polysty‐rene uniqueamong thermoplastic materials.
Production of expandable polystyrene beginswith crude oil and natural gas. Benzene, aderivative of crude oil, and ethylene, which isderived from natural gas, are combined to formethylbenzene. By chemical removal of hydrogen,ethylbenzene is converted to styrene. Styrene is aclear water like liquid composed of 92% carbonby weight and 8% hydrogen by weight. Thismaterial is highly reactive and possesses theability to combine with itself to form a long‐chainpolymeric material named polystyrene.Conversion of styrene to polystyrene isaccomplished through a reaction known assuspension polymerization.
Styrene — and a large volume of water and soap tosuspend the styrene in the water —'is added to asteam‐jacketed agitated vessel. The entire mix‐tureis then heated with proper agitation through aprescribed thermal pro‐gram. At this point, theconversion of styrene into a highly useful thermalplastic polymer, polystyrene, is complete. However,to produce an ex‐pandable polystyrene requiresone additional step. An expanding agent, such asnormal pentane, is added to the vessel and isabsorbed into the po‐lymer through continuedagitation and heat. When the reaction is com‐plete,the pentane bearing beads are subjected to apostreactor processing and are separated intoproduct types according to bead size. The moldingprocess for expandable polystyrene actually followsfive steps:
Pre‐expansionStabilizationMoldingInspectionAging
Expandable polystyrene beads are supplied in an unexpandedform with a bulk density of 40 ln/ft\ Since the blowing agentin the bead will disperse over a period of time, the usual shelflife for unexpanded beads is two months. Beads are first pre‐expanded to the density required for the partic‐ularapplication. Pre‐expansion is accomplished by either steam,vacuum or hot air depending on bead size and ultimatedensity required. In the case of pattern molding for theevaporative casting process, a small bead prod‐uct, pre‐expanded to a density ranging between 1.0 and 1.5 Ib/ft' isre‐quired to produce the highest quality casting. To expand a small bead product at densities below 1.5 lbs percubic foot, a vacuum pre‐expander is required. After pre‐expansion, the beads are allowed to stabilize for at least onehour before molding. This is accomplished by storing thebeads in a fine mesh bag to allow free access of air. After pre‐expansion, the re‐maining blowing agent will continue todisperse. This limits the shelf life of the expanded beads toapproximately 24 hours.
Molding presses specifically designed for expandablepolystyrene are sup‐plied by several companies. Thefoam pattern molds are made of cast aluminum andmachined to finished dimensions. Since polystyrene is notabrasive, tooling wear is minimal. Several hundredthousand patterns can be made before the mold requiresmaintenance. One‐half to one degree draft is sufficient. Mold cavity andcore walls contain small holes or core‐box vents throughwhich steam can enter the mold cavity. Expanded beadsare blown into the mold, completely filling the cavity.Steam heats the ex‐panded beads, causing them tofurther expand filling void areas between the sphericalbeads and fusing them together. Mold and pattern arethen water‐cooled after which the polystyrene pattern isejected. (Fig. 65)
Freshly molded patterns contain 6‐8% by weightinternal moisture. Over‐night aging at ambientconditions will usually dry the patterns to moisturelevel that does not interfere with casting. Ovenaging at 140F (60C) will ac‐celerate the dryingprocess. Molded foam polystyrene patterns shrinkwith age. Patterns will shrink a maximum of about0.100 inches/foot over a peri‐od of 30 days. Theplanned lag time between pattern molding andcasting must be considered when designing apattern mold. Foundries molding their own polystyrene patternswill usually plan to cast within a few days. On theother hand, a foundry purchasing foam patternsfrom an outside source will usually allow for themaximum shrinkage indicated above.
Metal shrinkage in the evaporative castingprocess is generally the same as the liquidmetal shrinkage in conventionally bondedsand molding and must be considered alongwith pattern shrinkage when designing thealuminum mold. Close inspection of themolded polystyrene pattern is critical. Ade‐fect in the pattern, such as an underfilledsection or other cavity in the sur‐face willbecome part of the casting. Therefore, it is farless expensive to scrap a foam pattern than itis to scrap the casting.
Density and Bead Size — Experience with theevaporative casting process has shown thatpatterns molded at a low density using a smallbead ex‐pandable polystyrene product willproduce the highest quality castings. A low densitypattern is required to minimize the amount of gasevolved dur‐ing vaporization of the pattern sincethe gas must permeate through the coating, sandand vent itself to the atmosphere. If the gas formsfaster than it can vent, a defective casting willresult. Gas formation is a function of patterndensity and metal pouring temperature. If patterndensity is in‐creased," more gas will be formed at aconstant pouring temperature.
Like‐wise, if pattern density is held constant and pouringtemperature is in‐creased, more gas will be evolved sincethe polystyrene molecule will break down into more basicmolecules at the higher temperature. As a result, steelcastings generally require a lower density pattern thangray, malleable or ductile iron. Ferrous castings generallyrequire a lower density than cop‐per alloys, which in turnrequire a lower density than when casting alumi‐num. Theratio of surface area to volume should also be considered. All of the gas that is formed must pass through the coatingon the surface of the pattern. Patterns with wallthicknesses between 1/8 inch and 1/4 inch can usually bepoured in iron at densities between 1.4 and 1.5 Ib/ft3.Thicker patterns will require densities of 1.25 pounds percubic foot or lower. As a general rule, the required patterndensity will range between 1.0 and 1.5 lb/ ft3 dependingupon the part geometry and the metal being poured.
Regarding bead size, a small bead is required toobtain a relatively smooth surface on moldedpatterns. In addition, the small bead will alsoenable fill‐ing of the thin‐wall section (e.g. 1/4inch and less). Gating — Proper gating is critical and is usually atrial‐and‐error approach by the foundry untilexperience is gained with the evaporative castingpro‐cess. The trial gating system is cut from lowdensity foam board and glued to the pattern ormultipattern assembly. Once the proper gatinghas been determined for a particular application,it is usually molded sometimes even as an integralpart of the pattern.
Venting is a major problem due to the enormousquantity of decomposi‐tion products which are the directresult of the vaporization of the polysty‐rene. Venting isbest accomplished simply by using the combination of an"open" sand and adequate vents placed at strategic pre‐planned exit points in the total molding concept.Inadequate venting will contribute‐materially to grosscasting defects. Gluing — Multicomponent polystyrene patterns alongwith gating systems can be assembled with any contactcement provided the solvent is not an aromatichydrocarbon. Rubber cement maybe satisfactory for theinitial casting evaluations, and other proprietary cementsfor polystyrenes may be obtained in model or hobbyshops. Other contacts may be made with ma‐joradhesive manufacturers.
Coating — Pattern assembly, with the gatingsystem attached is coated, us‐ually by dippingwith a permeable refractory coating which hasbeen spec‐ially formulated for expandablepolystyrene and then air or oven dried at 140F(60C or less). The coating prevents sandcollapse during pouring. The portion of thegating system where the downsprue will beattached is not coated. The refractory coatingis important since it actually is part of themold. The contact line between the coatingand the pattern is the actual mold wall surface.(Fig. 66)
Sand — A coarse (e.g. 25‐30 AFS GFN) rounded orangular sand is gener‐ally used. This type of sand isrecommended for its maximum permeability so that thegases evolved during pouring and the vaporization ofthe poly‐styrene can freely exit from the mold cavity. Flasks — Mating cope and drag flasks are not requiredfor unbonded sand castings. Instead, a flask can be anycontainer that is rigid enough to with‐stand vibrationand the weight of the sand. The flask must be ventedwith slots in the side walls to allow rapid escape of thegases formed by vaporiza‐tion of the pattern. A finemeshed screen should line the inside walls of the flask inorder to prevent sand loss through the vents.
Casting Procedure — Several inches of sand arefirst placed in the bottom of the flask to form abase for the pattern. The coated patternassembly is then positioned on the sand base andsand is added while vibrating the flask until thesand reaches a level point with the gating system.A suitable downsprue should be located abovethe gating system and additional sand is addeduntil it is level with the top of the downsprue.Care should be taken to prevent any sand grainsfrom dropping into the downsprue. Pour‐ingprocedures and methods are the same as inbonded sand casting.
The pouring rate is determined by the rate atwhich the pattern vaporizes. A constant head ofmetal must be maintained. As soon as the castingshave solidified they are ready for shakeout. Theusual method is to empty the flask onto a steelgrating. The sand will fall through the grating tobe col‐lected and returned to a storage bin by aconveyor system. The sand is ready for reuse assoon as it has cooled to approximately 14')F (60C)or less. If the sand is not properly cooled, the heatcan cause the next patt ;rn around which it is tobe used to distort. Castings may then beprocessed in keeping with the usual procedures.(Fig. 67)
Using the Polystyrene Casting Process for MakingPatterns The polystyrene or expandable pattern process has been inuse for a number of years and is still being used almostexclusively for castings such as automotive dies. A typicalprocedure for the casting of an automotive die would consistof the following steps: standard polystyrene board shapesare used to fabricate the patterns. The foam board isavailable in blocks or sheets in sizes from 4 feet wide to 18inches long and with thickness vari‐ations from 1 inch to 18inches making it adaptable to all design require‐ments. Itsease of handling is best illustrated by comparing one cubicfoot of polystyrene at approximately 1‐1/2 lbs. to 1 cubicfoot of mahogany at 50 lbs. (Fig. 68) The woodworking tools found in modern pattern shops canbe used for all cutting and shaping processes. Patterns arecut out of board stock with a band saw or hot wire.
If duplicate sections of segments are needed multiplepieces of polystyrene board may be stacked and cut tothe full capacity of the saw. Shaping can be done with arouter, spindle sander or sharp knife. Although standardshrink allowances are used in pattern construction, draftconsiderations on patterns is eliminated so thatcon‐struction is simplified. Board sections are joinedtogether by commercial glues or adhesives madeexpressly for use with the polystyrene foam, as well aswire brads in order to reinforce the cemented bond. Usually sharp inside corners are broken with fillets. Thesefillets are an aid to casting soundness and generally willbe accomplished by using a wax fillet mate‐rial. Beeswaxis the material used and paraffin waxes are notrecom‐mended. Pattern job numbers for identification,etc. are stamped into zinc tapes which are then fastenedto the pattern.
The pattern is weighed to estimate the castingweight. One pound of poly‐strene requiresapproximately 350 to 370 pounds of metal. Theweight of the wax, glue, etc. must be estimated.If the polystyrene pattern as it is re‐ceived froman outside source or the company pattern shophas any open joints, these must be taped in orderto prevent these openings (cracks) fromappearing in the casting. A gummed masking tapeor plastic type tape may be used. When the finalpattern is complete, a thick coating of refrac‐torywash is necessary in order to obtain a satisfactorycasting surface.
The special refractory coatings for use with polystyrenepatterns have been developed by coatingmanufacturers, and the instructions for applicationshould be followed closely. Usually, a first coat isapplied, and after it has been dried, a second coat isapplied, generally with a high pressure hydrau‐lic airlesstype spraygun where very little over‐spray isencountered. Many of the successful polystyrenecasting producers use as many as three coats of therefractory coating, making sure that there is a specifictime interval allowed for complete and thorough dryingof each of the coats. A coating thickness of 1/32 to 1/16 inch minimum isnecessary for heavy sections (6 to 10 inches crosssection). Refractory coating runs and brush marks onthe wash coat are not important since the surfaceadjacent to the polystyrene actually forms the finalmetal finish.
Because polystyrene patterns are structurally flexible,the cope plate must be flat and true to prevent bentcastings. Usually it is necessary to level with a dry sandbed, plywood sheets or sheets of polystyrene. The copeboards must be dry in order for the molding sand toharden properly as it is rammed in about thepolystyrene pattern. The gate areas for the gating of the metal to thepolystyrene pattern are figured at about twice that usedfor wood molded patterns. In the pouring ofpolystyrene, as it vaporizes, there is a slight backpressure which is generated when the metal vaporizesthe polystyrene. Bottom gating into all of the lowestpoints appears to do the best job of producing cleanercope surfaces, which has been a general problem withpolystyrene patterns.
Gates can be bridged from one part of a casting toanother simply with a strip of 1 x 2 inch polystyrene.Runners are constructed of 2 x 4 inch pieces ofpolystyrene which are laid on the cope board and thedown gates are attached with nails or glue. A refractorywash coating on the gating system is not necessary. The sand mixture usually used is of the air‐hardeningchemically bonded sands and consists of a base washedand dried silica sand of approximately AFS GFN 55. Theair‐hardening sand is applied to the pattern and the gatesto a depth of 2 inches minimum. Any of the air‐hardenedchemically bonded sand mixtures may be used for themolding, ramming and venting in of the polystyrenepattern.
Problem areas, where burn‐in might occur can befaced with either zircon or chromite sand. It isessential that the sand be compacted against thepattern by hand packing or tapping. This willprevent excessive burn‐in and metal penetrationinto the void areas. In deep pockets and sideopenings, it is important to use reenforcing rods. In supporting a deep horizontal pocket, tabletsshould be hung through the polystyrene from thecope surfaces. If the chemically bonded air‐hardening sand is to be used only as a facing, thenafter the facing sand has hardened, the mold maybe finished‐rammed with regular backup sand. Thisprocedure, as well as variations, is totallydependent upon the individual facility's processingsystem.
After the mold has been rammed, the bottom board is boltedor fastened and the drag rolled over. This must be donecarefully to prevent cracking of the facing sand which canresult in runouts. The molding board is removed and loosesand removed from the cope surfaces. An interesting aspect ofthis casting process is that very few risers are required oncastings containing ribs and pockets. For heavy chunkycastings, conventionally sized side risers are required. It is bestto use polystyrene blind‐type risers in order to prevent theneed for removing the cope after ramming. Blind risers help prevent excessive flames and heat byexcluding air from the vaporization process of the polystyreneas the metal is poured. Risers are placed in the requiredlocations and cores or ceramic tile are placed on the runner toform the downsprue. Downsprues are arranged for pouringwith one or two ladles depending on the equipment availableas well as the size of the casting. Each riser and the ends of therunner are vented with a number 10 wire to help removesome of the gas pressure which is generated
during the pouring. A safety core or plug can also beplanned to be placed in the cope to be used in case thegating system fails at the beginning of pouring or thiscore may be removed at the end of the pouring to makecer‐tain that the mold cavity is full of metal. One‐halfinch vent rods may also be used in risers in order toprovide a "flow‐off" indication. The cope is sanded in a manner similar to the drag. Rodand "gaggers" can be used if the flush bar spacingexceeds 12 inches. Normally, an 8 to 10 inch cope iscompletely filled with the air‐hardening chemicallybonded sand. The cope flask is clamped in theconventional manner to the drag flask and a pouring boxmay then be set. In all cases where air‐hardenedchemically bonded sands are used, it is essential toinsure enough time for the chemi‐cally bonded sands tothoroughly cure.
The extensive development of the polystyrene patternsindicates that the measurable savings are in patternconstruction costs and machining advan‐tage. Thepolystyrene material is priced less than wood, easilyfabricated and is easier to work with than when workingwith wood. Since the polystyrene pattern is lost for each castingmade and must be re‐. newed for the production ofanother one, the economics of the process are,therefore, influenced to a great extent by the quantityof castings required. Estimates indicate that for smallbatches, the average cost for handmade polystyrenefoam patterns is between 20 and 25% of the productioncost of corresponding wooden patterns including coreboxes.
This means that small batches of up to five castings can bepr6duced economically by the polystyrene process. Patternsfor large quantities must be produced in au‐tomaticpolystyrene molding machines. Since this would be asignificant cost factor, it is generally necessary to haveorders for 5,000 and up to 20,000 castings in order to makequantity production a really economical proposition. Castings weighing from 100 to 200,000 pounds have beenproduced in a variety of grades of steel. The onlymetallurgical limitation experienced to date concerns steelswith low carbon contents. Vaporization of the polysty‐renefoam pattern results in a carbon‐rich atmosphere which maycreate a slight carbon pickup of approximately 0.03%. Thiscarbon pickup is con‐sidered negligible for alloy steels havinga carbon content in excess of 0.1%. The process is notrecommended for steel castings with very low car‐boncontents.
The mere handling of ligntweight polystyrenematerial in the pattern shops is far easier thanhandling wood. Polystyrene foam is worked withmetal cutting tools, but the power requirement isfar less. Smooth casting sur‐faces are obtained byselecting high speed tools for cutting the patternand by applying suitable refractory coatings whichare specially formulated for use with polystyrenepatterns. Advantages of the evaporative casting process, ascompared to the conven‐tional bonded‐sandcasting techniques, are numerous. Undoubtedlythe most important advantage is that no cores arerequired. Other immediate advantages of theprocess:
Castings can be made to closer tolerances as wallsas thin as 0.120 inches have been cast. * No binders or other additives are required forthe sand which is reusa‐ble. Flasks for containing the mold assembly areinexpensive. Shakeout of the castings in unbonded sand issimplified‐not requiring the heavy shakeoutmachinery. The need for skilled labor is greatly reduced. Casting cleaning is minimized since there are noparting lines or core fins.
Polystyrene Advantages Advantages of the evaporative casting process,when compared to conven‐tional bonded‐sandtechniques, other than the prime advantages ofno cores, reusable sand, no binders or additivesand inexpensive flasks, indi‐cate a cost analysisproduction savings of 20‐25% on reasonablysimple cored items, and as much as 45‐50% oncomplex castings. The benefits of the evaporativecasting process can be better appreciated ifviewed in terms of actual savings as analyzed bystudying the following major cost centers.
Reduced operating costs are chiefly the result oftwo factors. First, since the sand is reusable andcores are eliminated, sand consumption is greatlyreduced along.with elimination of binders andother additives. Secondly, skilled laborrequirements are considerably reduced. Skilledsand molders are replaced by semi‐skilled laborer,who merely position a foam pattern assembly andpour sand around it into a vibrating flask. There isno need for the skilled patternmaker, coremakerand coresetter. In addition, labor savings may beobtained in the areas of maintenance and cleaningroom personnel since less complex equipment isrequired and grinding e.g. core fins, parting lineflash are eliminated.
There is a great savings in equipment and equipmentcosts. Equipment costs for an evaporative casting plantincluding in‐house production of foam‐patternmolding equipment has been estimated at 1/2 thecost of the conventional green sand foundry. Ifpolystyrene patterns are purchased from an outsidesource, equipment savings can be even greater andac‐counting costs much more accurate. More specifically, core machines, core dryers, sandmolding machines and sand mullers are eliminated.Sand han‐dling and shakeout equipment is simplifiedand much less equipment is needed for the abrasivecleaning as well as grinding of the castings forship‐ment.
Building costs are also materially reduced because of thelack of need for heavy equipment foundations. Coremolds, metal patterns and mating cope and drag flasksare also eliminated. In their place are the sim‐ple flasksand foam‐pattern tooling which can last indefinitely,because of the lack of actual sand abrasion where metalpatterns are involved in nor‐mal production. In addition,the use of polystyrene as a pattern material may alsomake it possible that storage of seldom used patternsmay be eliminated. Since castings are consistently poured at closer toleranceswith less grinding finishing stock, the dimensionalvariability usually associated with core setting, etc. iseliminated. This overall casting quality achieve‐mentreflects savings from amount of metal poured to castingprocessing costs.
Polystyrene‐ Disadvantages Pattern coating process is time‐consuming, andpattern handling requires great care. Greater molding skill is required to compact theair‐hardened chemically bonded sands withoutpattern damage and to properly place vents. Pouring is more hazardous. There is less room for mistakes in the process. (Ascrapped casting means replacement not only ofthe mold but the pattern as well.)
The continued and future use of polystyrene patterns inthe metalcasting industry is bright. Its versatility has beenfully recognized and has been used to advantage issolving many problems. Further developments can beanticipated as time goes on. Improvements inpolystyrene board stock will in turn improve castingfinishes. Economical reproduction of large patterns inquantity is already a reality. Mass production of small patterns has be‐come anaccepted practice and continued future developments aswell as experience with the use of this material wiil opennew areas for its use in actual casting where intricatecored passages are part of the casting design as well asfor the continued use of polystyrene for patterns.
One‐half to one degree draft is sufficient. Mold cavity and core walls contain small holes or core‐box vents through which steam can enter the mold cavity. Expanded beads are blown into the mold, completely filling the cavity. Steam heats the ex‐panded beads, causing them to