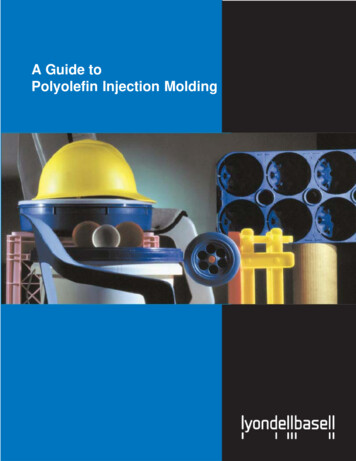
Transcription
A Guide toPolyolefin Injection Molding
A Guide to Polyolefin Injection MoldingTable of ContentsIntroduction .Polyolefins are derived from petrochemicals .Molecular structure and composition affect properties and processability .Chain branching .Density .Molecular weight .Molecular weight distribution .Copolymers .Modifiers and additives .Working closely with molders .How polyolefins are made .Low density polyethylene (LDPE) .High density polyethylene (HDPE) .Linear low density polyethylene (LLDPE) .Polypropylene .Shipping and handling polyolefin resins .Material handling .How to solve material handling problems .Other material handling practices .The injection molding process .Injection units .Plasticator specifications .Screw designs .Nozzles .Clamp mechanisms .Clamp specifications .Injection molds .Types of mold .Sprues and runners .Mold venting .Gating .Mold cooling .Ejection devices .Spiral flow measurement .General injection molding operating procedures .General safety .Heat .Electricity .Machinery motion .The injection molding process and its effect on part performance .The molding cycle .Shrinkage .Warpage .Color dispersion and air entrapment .Part ejection and mold release .Clarity .Gloss .Polypropylene integral hinges .Appendices1. Injection Molding Terms .2. Metric Conversion Guide .3. Abbreviations .4. ASTM test methods applicable to polyolefins .5. Injection molding problems, causes and solutions .6. ASTM and ISO sample preparation and test procedures .7. Compression and injection molded sample preparation for HDPE 21222223232323232929303132323233384041424647
A Guide To Polyolefin Injection MoldingIntroductionPolyolefins are the most widelyused plastics for injectionmolding. This manual, A Guide toPolyolefin Injection Molding,contains general informationconcerning materials, methodsand equipment for producing highquality, injection molded,polyolefin products at optimumproduction rates.Polyolefins that can beinjection molded include: Low density polyethylene(LDPE) Linear low density polyethylene(LLDPE) High density polyethylene(HDPE) Ethylene copolymers, such asethylene vinyl acetate (EVA) Polypropylene and propylenecopolymers (PP) Thermoplastic olefins (TPO)In general, the advantages ofinjection molded polyolefins compared with other plastics are: LightweightOutstanding chemicalresistanceGood toughness at lowertemperaturesExcellent dielectric propertiesNon-hygroscopicThe basic properties of polyolefinscan be modified with a broadrange of fillers, reinforcementsand chemical modifiers.Furthermore, polyolefins areconsidered to be relatively easy toinjection mold.Major application areas for polyolefin injection molding are: AppliancesAutomotive productsConsumer products FurnitureHousewaresIndustrial containersMaterials handling equipmentPackagingSporting goodsToys and noveltiesThis manual contains extensiveinformation on the injection molding of polyolefins. However, itmakes no specificrecommendations for theprocessing of LyondellBasell resinsfor specific applications. For moredetailed information please contactyour LyondellBasell polyolefinssales or technical servicerepresentative.Polyolefins arederived frompetrochemialsPolyolefins are plastic resinspolymerized from petroleum-basedgases. The two principal gases areethylene and propylene. Ethyleneis the principal raw material formak-ing polyethylene (PE andethylene copolymer resins;propylene is the main ingredient formaking polypropylene (PP) andpropylene copolymer resins.Polyolefin resins are classified asthermoplastics, which means thatthey can be melted, solidified andmelted again. This contrasts withthermoset resins, such asphenolics, which, once solidified,can not be reprocessed.Most polyolefin resins for injectionmolding are used in pellet form.The pellets are about 1/8 inch longand 1/8 inch in diameter and usually somewhat translucent to white incolor. Many polyolefin resins contain additives, such as thermalstabi-lizers. They also can be2compounded with colorants, flameretardants, blowing agents, fillers,reinforce-ments, and otherfunctional addi-tives such asantistatic agents and lubricants.Molecular structure andcomposition affectproperties andprocessabilityFour basic molecular propertiesaffect most of the resincharacteris-tics essential toinjection molding high qualitypolyolefin parts. These molecularproperties are: Chain branching Crystallinity or density Average molecular weight Molecular weight distributionThe materials and processes usedto produce the polyolefinsdetermine these molecularproperties.The basic building blocks for thegases from which polyolefins arederived are hydrogen and carbonatoms. For polyethylene, theseatoms are combined to form theethylene monomer, C2H4.In the polymerization process, thedouble bond connecting the carbonatoms is broken. Under the rightconditions, these bonds reformwith other ethylene molecules toform long molecular chains.The resulting product is polyethylene resin.
For polypropylene, the hydrogenand carbon atoms are combinedto form the propylene monomer,CH3CH:CH2.or degradation may cause crosslinking in polyethylenes and chainscission in polypropylenes.3range of 0.895 to 0.905 g/cm ,which is the lowest for acommodity thermo-plastic anddoes not vary appreciably frommanufacturer to manufacturer.The third carbon atom forms aside branch which causes thebackbone chain to take on a spiralshape.Ethylene copolymers, such asethylene vinyl acetate (EVA), aremade by the polymerization ofethylene units with randomlydistributed vinyl acetate (VA)comonomer groups.Chain branchingPolymer chains may be fairlylinear, as in high densitypolyethylene, or highly branchedas in low density polyethylene. Forevery 100-ethylene units in thepolyethylene molecular chain,there can be one to ten short orlong branches that radiate threedimensionally (Figure 1). Thedegree and type of branching arecontrolled by the process (reactor),catalyst, and/or any comonomersused.Chain branching affects many ofthe properties of polyethylenesincluding density, hardness,flexibility and transparency, toname a few. Chain branches alsobecome points in the molecularstructure where oxidation mayoccur. If excessively hightemperatures are reached duringprocessing, oxidation can occurwhich may adversely affect thepolymer’s properties. This oxidationPolypropylene, on the other hand,can be described as being linear(no branching) or very highlybranched. Although the suspendedcarbon forms a short branch onevery repeat unit, it is alsoresponsible for the unique spiraland linear configuration of thepolypropylene molecule.DensityPolyolefins are semi-crystallinepolymers which means they arecomposed of molecules which arearranged in a very orderly(crystalline) structure andmolecules which are randomlyoriented (amorphous). This mixtureof crystalline and amorphousregions (Figure 2) is essential inproviding the desired properties toinjection molded parts. A totallyamorphous polyolefin would begrease-like and have poor physicalproperties. A totally crystalline polyolefin would be very hard andbrittle.HDPE resins have linear molecularchains with comparatively few sidechain branches. Therefore, thechains are packed more closelytogether (Figure 3). The result iscrystallinity up to 95 percent. LDPEresins generally have crystallinityfrom 60 percent to 75 percent.LLDPE resins have crystallinityfrom 60 percent to 85 percent. PPresins are highly crystalline, butthey are not very dense. PP resinshave a nominal specific gravity3For polyethylene, the density andcrystallinity are directly related, thehigher the degree of crystallinity,the higher the resin density. Higherdensity, in turn, influencesnumerous properties. As densityincreases, heat softening point,resistance to gas and moisturevapor permeation and stiffnessincrease. However, increaseddensity generally results in areduction of stress crackingresistance and low temperaturetoughness. LDPE resins have densitiesranging from 0.910 to 0.930grams per cubic centimeter(g/cm3)LLDPE resins range from0.915 to 0.940 g/cm3HDPE resins range from 0.940 to 0.960 g/cm3As can be seen, all naturalpolyolefin resins, i.e, those withoutany fillers or reinforcements, havedensities less than 1.00 g/cm3. Thislight weight is one of the key
advantages for parts injectionmolded from polyolefins. A generalguide to the effects of density onthe properties for various types ofpolyethylene resins is shown inTable 1.Table 1. General guide to the effects of polyethylene physical properties onprperties and processingMolecular weightAtoms of different elements, suchas carbon, hydrogen, etc., havedifferent atomic weights. Forcarbon, the atomic weight is 12and for hydrogen it is one. Thus,the molecular weight of theethylene unit is the sum of theweight of its six atoms (two carbonatoms x 12 four hydrogen x 1) or28.Unlike simple compounds, likeethylene or propylene, everypolyolefin resin consists of amixture of large and small chains,i.e., chains of high and lowmolecular weights. The molecularweight of the polymer chaingenerally is in the thousands andmay go up to over one million. Theaverage of these is called, quiteappropriately, the averagemolecular weight.As average molecular weightincreases, resin toughnessincreases. The same holds true fortensile strength and environmentalstress crack resistance (ESCR) –cracking brought on when moldedparts are subjected to stresses inthe pres-ence of materials such assolvents, oils, detergents, etc.However, high-er molecular weightresults in an increase in meltviscosity and greater resistance toflow making injection molding moredifficult as the average molecularweight increases.Melt flow rate (MFR) is a simplemeasure of a polymer’s meltviscosity under standard conditionsof temperature and static load(pressure). For polyethylenes, it isoften referred to as melt index (MI).MFR is the weight in grams of amelted resin that flows through astandard-sized orifice in 10minutes (g/10 min). Melt flow rateis inversely related to the resin’saverage molecular weight: as theaverage molecular weightincreases, MFR decreases andvice versa.Melt viscosity, or the resistance ofa resin to flow, is an extremelyimportant property since it affectsthe flow of the molten polymerfilling a mold cavity. Polyolefinswith higher melt flow rates requirelower injection molding processingpressures, temperatures andshorter molding cycles (less timeneeded for part cooling prior toejection from the mold). Resinswith high viscosities and, therefore,lower melt indices, require theopposite conditions for injectionmolding.It should be remembered thatpressure influences flowproperties. Two resins may havethe same melt index, but differenthigh-pressure flow properties.Therefore, MFR or MI must beused in conjunction with othercharacteristics, such as molecular4weight distribution, to measure theflow and other properties of resins.Generally, injection molding resinsare characterized as havingmedium, high or very high flow.For injection molding grades, theMFR (MI) values for polyethylenesare generally determined at 190 C(374 F) using a static load of 2,160g. MFR values for polypropylenesare determined at the same loadbut at a higher temperature 230 C(446 F). The MFR of otherthermoplastics may be determinedusing different combinations oftemperatures and static load. Forthis reason, the accurate predictionof the relative processability ofdifferent materials using MFR datais not possible.Molecular weightdistributionDuring polymerization, a mixture ofmolecular chains of widely varyinglengths is produced. Some may beshort; others may be extremelylong containing several thousandmonomer units.
The relative distribution of large,medium and small molecularchains in the polyolefin resin isimportant to its properties. Whenthe distribu-tion is made up ofchains close to the average length,the resin is said to have a “narrowmolecular weight distribution.”Polyolefins with “broad molecularweight distribution” are resins witha wider variety of chain lengths. Ingeneral, resins with narrowmolecular weight distributions havegood low-temperature impactstrength and low warpage. Resinswith broad molecular weightdistributions generally have greaterstress cracking resistance andgreater ease of processing (Figure4).copolymer ethylene ethyl acrylate(EEA) and vinyl acetate toproduce ethylene vinyl acetate(EVA).Ethylene is used as a comonomerwith propylene to producepolypropylene randomcopolymers. Polypropylene can bemade more impact resistant byproducing a high ethylenepropylene copolymer in a secondreactor forming a finely dispersedsecondary phase of ethylenepropylene rubber. Products madein this manner are commonlyreferred to as impact copolymers. Working closelywith moldersLyondellBasell offers a wide rangeof polyolefin resins for injectionmold-ing, including Alathon andPetrothene HDPE,Petrothene LDPE, LLDPE, and PP, UltratheneEVA copolymers and Flexathene TPOs. These resins are tailored tomeet the requirements of manyareas of application. LyondellBasell polyolefins technicalservice representatives are alsoavailable to assist injection moldersand end-users by providingguidance for tool and part designand the development of specialtyproducts to fulfill the requirementsof new, demanding applications.CopolymersThe comonomers most often usedwith LLDPE and HDPE are calledalpha olefins. They includebutene, hexene and octene. Othercomonomers used with ethyleneto make injection molding gradesare ethyl acrylate to make the NucleatorsClarifiersLubricantsPolyolefin resins with distinctly different properties can be made bycontrolling the four basic molecularproperties during resin productionand by the use of modifiers andadditives. Injection molders canwork closely with theirLyondellBasell polyolefins sales ortechnical service representative todetermine the resin that best meetstheir needs.The type of catalyst and thepolymerization process used toproduce a polyolefin determines itsmolecular weight distribution. Themolecular weight distribution(MWD) of PP resins can also bealtered during production by controlled rheology additives thatselec-tively fracture long PPmolecular chains. This results in anarrower molecular weightdistribution and a higher melt flowrate.Polyolefins made with one basictype of monomer are calledhomopolymers. There are,however, many polyolefins, calledcopolymers, that are made of twoor more monomers. Many injectionmolding grades of LLDPE, LDPE,HDPE and PP are made withcomonomers that are used toprovide specific propertyimprovements. Modifiers andadditivesNumerous chemical modifiers andadditives may be compounded withpolyolefin injection molding resins.In some grades, the chemicalmodifiers are added during resinmanufacture. Some of theseadditives include: AntioxidantsAcid scavengersProcess stabilizersAnti-static agentsMold release additivesUltraviolet (UV) light stabilizers5How polyolefinsare madeHigh-purity ethylene and propylenegases are the basic feedstocks formaking polyolefins (Figure 5).These gases can be petroleumrefinery by-products or they can beextracted from an ethane/propaneliquified gas mix coming throughpipelines from a gas field. Highefficiency in the ethane/propanecracking and purification results invery pure ethylene and propylene,which are critical in the productionof high quality polyolefins.
LyondellBasell can producepolyolefins by morepolymerization technologies andwith a greater range of catalyststhan any other supplier can. Twoof LyondellBasell’s plants arepictured in Figure 6.Low densitypolyethylene (LDPE)To make LDPE resins,LyondellBasell uses highpressure, high temperaturetubular and autoclavepolymerization reactors (Figures7 and 8). Ethylene is pumpedinto the reactors and combinedwith a catalyst or initiator tomake LDPE. The LDPE meltformed flows to a separatorwhere unused gas is removed,recovered, and recycled backinto the process. The LDPE isthen fed to an extruder forpelletization. Additives, ifrequired for specific applications,are incorporated at this point.High densitypolyethylene (HDPE)Figure 7. LDPE high temperature tubular process diagram6There are a number of basicprocesses used byLyondellBasell for mak-ingHDPE for injection moldingapplications —including thesolution process and the slurryprocess. In the multi-reactorslurry process used byLyondellBasell (Figure 9),ethylene and a comonomer (ifused), together with an inerthydrocarbon carrier, are pumpedinto reactors where they arecombined with a catalyst.However, in contrast to LDPEproduction, relatively lowpressures and temperatures areused to produce HDPE. Thegranular polymer leaves thereactor system in a liquid slurryand is separated and dried. It isthen conveyed to an extruderwhere additives are incorporatedprior to pelletizing.
Linear low densitypolyethylene (LLDPE)Figure 8. High temperature autoclave process diagramLyondellBasell uses a gas phaseprocess for making LLDPE (Figure11). This process is quite differentfrom the LDPE process, butsomewhat similar to the HDPEprocess. The major differencesfrom the LDPE process are thatrelatively low pressure and lowtemperature polymerization reactorsare used. Another difference is thatthe ethylene is copolymerized withbutene or hexene comonomers inthe reactor. Unlike HDPE, thepolymer exits the reactor in a drygranular form, which issubsequently compounded withadditives in an extruder.With changes in catalysts andoperating conditions, HDPE resinsalso can be produced in some ofthese LLDPE reactors.Figure 9. HDPE parallel reactors — slurry processPolypropyleneTo make PP, LyondellBasell uses avertical, stirred, fluidized-bed, gasphase process (Figure 12).LyondellBasell was the firstpolypropylene supplier in the UnitedStates to use gas-phase technologyto produce PP. Impact copolymersare produced using two, fluidizedbed, gas phase reactors operatingin series.LyondellBasell’s polyolefinproduction facilities are describedinShipping andhandling ofpolyolefin resinsLyondellBasell also utilizes a multireactor solution process for theproduction of HDPE (Figure 10). Inthis process, the HDPE formed isdissolved in the solvent carrier andthen precipitated in a downstreamprocess. An additional adsorptionstep results in a very clean productwith virtually no catalyst residues.Because both of these processesutilize multiple reactors,LyondellBasell has the capabilityof tailoring and optimizing themolecular weight distribution ofthe various product grades toprovide a unique range ofprocessability and physicalproperties.7It is of utmost importance to keeppolyolefin resins clean.LyondellBasell ships polyolefinresins to molders in hopper cars,hopper trucks, corrugated boxes,and 50-pound plastic bags. Strictquality control throughout resinmanufacture and subsequenthandling, right through delivery tothe molder, ensures the cleanlinessof the products.
Table 2. LYB polyolefinproduction facilitiesFigure 10. HDPE solution processBAYPORT, TXFigure 11. LLDPE fluidized bed processvirgin resin. In all cases, theproportion of regrind used shouldbe carefully controlled to assureconsistency of processing andpart performance.Material handlingLyondellBasell utilizes materialhandling systems and inspectionprocedures that are designed toprevent external contamination andproduct cross-contamination duringproduction, storage, loading andshipment.Since polyolefin resins are nonhygroscopic (do not absorb water)they do not require drying prior tobeing molded. However, undercertain conditions, condensationmay form on the pellet surfaces.When bulk containers aredelivered, the molder must useappropriate procedures forunloading the resin. Maintenanceof the in-plant material handlingsystem is also essential. Whenbags and boxes are used, specialcare is necessary in opening thecontainers, as well as coveringthem, as they are unloaded.Reground resin, whether used asa blend or as is, should also bestringently protected to keep itfree of contamination. Wheneverpossible, the regrind materialshould be used as it is generated.When this is not possible, thescrap should be collected in aclosed system and recycled withthe same precautions taken for8When cartons of resin aremoved from a cold warehouseenvironment to a warmmolding area or when transferringcold pellets from a silo to an indoorstoragesystem, the temperature of thematerial should be allowed toequilibrate, for up to eighthours to drive off any condensation before molding.
the pellets. Proper design of thetransfer lines is also critical interms of utilizing the optimum bendradii, blind tees, and proper angles.Consult your LyondellBaselltechnical service engineer forguidance in this area.Figure 12. PP dual reactors – gas-phase processHow to solve materialhandling problemsSince smooth piping is a leadingcontributor to angel hair andstreamers, one solution is toroughen the interior wall of thepiping. This causes the pellets totumble instead of sliding along thepipe, minimizing streamerformation. However, as the rapidlymoving polyolefin pellets contact anextremely rough surface, smallparticles may be broken off thepellets creating fines or dust.The best way to improve resinutilization is to eliminatecontaminants from transfersystems. If bulk handling systemsare not dedicated to one materialor are not adequately purged,there is always the possibility ofcontamination resulting fromremnants of materials previouslytransferred.Occasionally, clumps of “angelhair” or “streamers” mayaccumulate in a silo and plug theexit port. Contaminants of this typecan also cause plugging of transfersystem filters and/or problems thataffect the molding machine. All ofthese problems can result inmolding machine downtime,excessive scrap and the time andcosts of cleaning silos, transferlines and filters. Polyolefin dust,fines, streamers and angel haircontamination may be generatedduring the transfer of polymerthrough smoothbore piping. Thesetransfer systems also may containlong radius bends to convey theresin from a hopper car to the siloor holding bin. A polyolefin pelletconveyed through a transfer linetravels at a very high velocity. Asthe pellet contacts the smooth pipewall, it slides and friction isgenerated. The friction, in turn,creates sufficient heat to raise thetemperature of the pellet surface tothe resin’s softening point. As thishappens, a small amount of moltenpolyolefin is deposited on the pipewall and freezes almost instantly.Over time, this results in depositsdescribed as angel hair orstreamers.As the pellets meet the pipe wall,along the interior surface of a longradius bend, the deposits becomealmost continuous and streamersare formed. Eventually, the angelhair and streamers are dislodgedfrom the pipe wall and find theirway into the molding process, thestorage silo or the transfer filters.The amount of streamers formedincreases with increased transferair temperature and velocity.Other good practices of materialhandling include control (cooling)of the transfer air temperature tominimize softening and melting of9Two pipe finishes, in particular,have proven to be effective inminimizing buildup and giving thelongest life in transfer systems.One is a sand-blasted finish of 600to 700 RMS roughness. This finishis probably the easiest to obtain.However, due to its sharp edges, itwill initially create dust and finesuntil the edges become rounded.The other finish is achieved withshot blasting using a #55 shot with55-60 Rockwell hardness toproduce a 900 RMS roughness.Variations of this finish arecommonly known as “hammerfinished” surfaces. The shotblasting allows deeper penetrationand increases hardness, which inturn leads to longer surface life.The rounded edges obtainedminimize the initial problemsencountered with dust andfines. They also reduce metalcontamination possibly associatedwith thesandblasted finish.Whenever a new transfersystem is installed or when aportion of an existing system isreplaced, the interior surfacesshould be treated by either
sand or shot blasting. Theinitial cost of having this doneis far outweighed by theprevention of future problems.Elimination of long-radiusbends where possible is alsoimportant as they are probablythe leading contributor tostreamer formation. When thistype of bend is used, it iscritical that the interior surfaceshould be either sand- or shotblasted.The use of self-cleaning,stainless steel “tees” in placeof long bends prevents theformation of streamers alongthe curvature of the bend,causing the resin to tumbleinstead of slide (Figure 13).However, there is a loss ofefficiency within the transfersystem when this method isused. Precautions should betaken to ensure that sufficientblower capacity is available toprevent clogging of the transferlines and maintain the requiredtransfer rate.Figure 13. Eliminate long-radiusbends where possible. The useof stainless steel "tees"prevents the formation ofstreamers along the curvatureof the bend.To extend the life of the transferpiping, it should be rotated 90 atperiodic intervals. Resin pelletstend to wear grooves in thebottom of the piping as they aretransferred which not onlycontributes to fines and streamerformation but also acceleratedwear due to non-uniform abrasion.Regardless of the type ofequipment used or the materialstransferred, a transfer systemshould be maintained and keptclean in the same manner as anyother piece of productionequipment. Periodic washing anddrying of silos and holding binsreduces the problem of fines anddust build-up due to staticcharges.Other steps to eliminatecontamination include: Inspect the entire transfersystem on a regular basisClean all filters in the transfersystem periodicallyEnsure that the suction line isnot lying on the ground duringstorage or when the system isstarted to prevent debris fromentering t
A Guide To Polyolefin Injection Molding Introduction Polyolefins are the most widely used plastics for injection molding. This manual, A Guide to Polyolefin Injection Molding, contains general information concerning materials, methods and equipment for producing high quality, injection