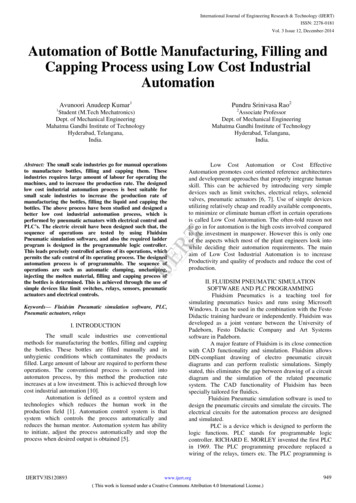
Transcription
International Journal of Engineering Research & Technology (IJERT)ISSN: 2278-0181Vol. 3 Issue 12, December-2014Automation of Bottle Manufacturing, Filling andCapping Process using Low Cost IndustrialAutomationAvunoori Anudeep Kumar1Pundru Srinivasa Rao221Associate ProfessorDept. of Mechanical EngineeringMahatma Gandhi Institute of TechnologyHyderabad, Telangana,India.Abstract: The small scale industries go for manual operationsto manufacture bottles, filling and capping them. Theseindustries requires large amount of labour for operating themachines, and to increase the production rate. The designedlow cost industrial automation process is best suitable forsmall scale industries to increase the production rate ofmanufacturing the bottles, filling the liquid and capping thebottles. The above process have been studied and designed abetter low cost industrial automation process, which isperformed by pneumatic actuators with electrical control andPLC’s. The electric circuit have been designed such that, thesequence of operations are tested by using FluidsimPneumatic simulation software, and also the required ladderprogram is designed in the programmable logic controller.This leads precisely controlled actions of its operations, whichpermits the safe control of its operating process. The designedautomation process is of programmable. The sequence ofoperations are such as automatic clamping, unclamping,injecting the molten material, filling and capping process ofthe bottles is determined. This is achieved through the use ofsimple devices like limit switches, relays, sensors, pneumaticactuators and electrical controls.Low Cost Automation or Cost EffectiveAutomation promotes cost oriented reference architecturesand development approaches that properly integrate humanskill. This can be achieved by introducing very simpledevices such as limit switches, electrical relays, solenoidvalves, pneumatic actuators [6, 7]. Use of simple devicesutilizing relatively cheap and readily available components,to minimize or eliminate human effort in certain operationsis called Low Cost Automation. The often-told reason notto go in for automation is the high costs involved comparedto the investment in manpower. However this is only oneof the aspects which most of the plant engineers look intowhile deciding their automation requirements. The mainaim of Low Cost Industrial Automation is to increaseProductivity and quality of products and reduce the cost ofproduction.IJERTStudent (M.Tech Mechatronics)Dept. of Mechanical EngineeringMahatma Gandhi Institute of TechnologyHyderabad, Telangana,India.Keywords— Fluidsim Pneumatic simulation software, PLC,Pneumatic actuators, relaysI. INTRODUCTIONThe small scale industries use conventionalmethods for manufacturing the bottles, filling and cappingthe bottles. These bottles are filled manually and inunhygienic conditions which contaminates the productsfilled. Large amount of labour are required to perform theseoperations. The conventional process is converted intoautomaton process, by this method the production rateincreases at a low investment. This is achieved through lowcost industrial automation [10].Automation is defined as a control system andtechnologies which reduces the human work in theproduction field [1]. Automation control system is thatsystem which controls the process automatically andreduces the human mentor. Automation system has abilityto initiate, adjust the process automatically and stop theprocess when desired output is obtained [5].IJERTV3IS120893II. FLUIDSIM PNEUMATIC SIMULATIONSOFTWARE AND PLC PROGRAMMINGFluidsim Pneumatics is a teaching tool forsimulating pneumatics basics and runs using MicrosoftWindows. It can be used in the combination with the FestoDidactic training hardware or independently. Fluidsim wasdeveloped as a joint venture between the University ofPadeborn, Festo Didactic Company and Art Systemssoftware in Padeborn.A major feature of Fluidsim is its close connectionwith CAD functionality and simulation. Fluidsim allowsDIN-compliant drawing of electro pneumatic circuitdiagrams and can perform realistic simulations. Simplystated, this eliminates the gap between drawing of a circuitdiagram and the simulation of the related pneumaticsystem. The CAD functionality of Fluidsim has beenspecially tailored for fluidics.Fluidsim Pneumatic simulation software is used todesign the pneumatic circuits and simulate the circuits. Theelectrical circuits for the automation process are designedand simulated.PLC is a device which is designed to perform thelogic functions. PLC stands for programmable logiccontroller. RICHARD E. MORLEY invented the first PLCin 1969. The PLC programming procedure replaced awiring of the relays, timers etc. The PLC programming iswww.ijert.org( This work is licensed under a Creative Commons Attribution 4.0 International License.)949
International Journal of Engineering Research & Technology (IJERT)ISSN: 2278-0181Vol. 3 Issue 12, December-2014written in high level language, which is easier forunderstandable of the more people [11]. Any machine canbe controlled automatically by use of PLC. For automationof process write the program in the software then transferthe program to the PLC and after that connect the PLC tothe machine [2]. A single PLC can run many machines atsame time. The PLC has capability for handling severalinputs and outputs signal. Allen Bradley PLC and Rslogix500 plc programming software are used for automation ofthe process.III. DESIGN SEQUENCE FOR AUTOMATIONPROCESS OF BOTTLE MANUFACTURING, FILLINGAND CAPPING THE BOTTLESInitially when the power is on the system startsworking the process. The cylinder A. activates and clampsthe die block. Then piston of the cylinder B moves forwardand injects the molten material in to die block and thepiston goes back. Now the piston of cylinder A unclampsthe die block and the bottle ejected on to the conveyor.V. SEQUENCE FOR AUTOMATION OF BOTTLEMANUFACTURING PROCESSFor automation of the bottle manufacturingprocess the sequence consists clamping of the die block,move the ram downwards and inject the molten material into die block, move the ram upwards, wait for a while andunclamp the die the bottle is ejected on to the conveyor.For automation of this process the sequence isA B B-A-.IJERTNow the bottles goes to the filling section and thesensor 1 detects the bottle and activates the cylinder C nowthe piston moves forward clamps the bottle and activatesthe cylinder D and the piston pushes the filler in to thebottle and then the cylinder v activates to open the nozzleand fills the required quantity. When the height of theliquid is sensed by the sensor 2 then cylinder v closes thenozzle, the piston of the cylinder D goes back and filler ismoved up and the bottle gets unclamped and movestowards capping section.IV. SEQUENCE FOR AUTOMATION PROCESS OFMANUFACTURING, FILLING AND CAPPING OFBOTTLESFor automation of bottle manufacturing filling andcapping process the sequence consists of Clamping the dieblock, moving the ram of injection moulding machinedownwards, wait for a while and unclamp the die block,clamp the bottle, move the filler into the bottle, open thenozzle valve, after filling, close the nozzle, unclamp thebottle, clamp the bottle, move the capping motordownwards, after capping, move the capping motorupwards and unclamp the bottle. Thus consists of mainlythree sections bottle manufacturing, filling and capping ofthe bottles.That’s the required sequence for overall process isA B B-A-C D V V-D-C-E F F-E-. The interlocksoccurs between B and B-, similarly in V and V-, F andF- to remove these interlocks relays are used. The totalsequence is divided in to three operations. They areautomation for manufacturing of the bottles by Injectionmoulding machine, automation of filling the bottle,automation of capping the bottles.Now the bottle goes to the capping section whenthe sensor 3 detects the bottle it activates the cylinder E andthe piston moves forward and clamps the bottle. Now thecylinder F activated and the piston comes down and fixesthe cap, the sensor 4 senses whether capping is done andthen activates the piston of the cylinder F to retract, thecylinder E retracts and unclamps the bottle. The man at thelast of the section collects the bottle from the conveyorbelt.The above sequence of operations with inputs andoutputs of the PLC are shown in the below fig.1a)b)c)d)VI. DESIGN OF PNEUMATIC CIRCUIT FORAUTOMATION OF BOTTLE MANUFACTURINGPROCESSConnect the working ports of one directional controlvalve to cylinder A and the working ports of otherdirectional control valve to the cylinder BThe input port of each directional valve which isresponsible for the motion of the piston is connected tothe compressor.The port of the directional valve which is responsibleof moving out the pressure from the other side of thepiston is connected to the exhaust.The compressor is connected to the pressure source.The circuit is shown in below fig 2.Fig 1: Inputs and Outputs connected to the PLC.Fig 2: Design of Pneumatic circuit for automation of bottle manufacturingprocessIJERTV3IS120893www.ijert.org( This work is licensed under a Creative Commons Attribution 4.0 International License.)950
International Journal of Engineering Research & Technology (IJERT)ISSN: 2278-0181Vol. 3 Issue 12, December-2014VII. DESIGN OF ELECTRIC CIRCUIT FORAUTOMATION OF BOTTLE MANUFACTURINGPROCESSa) Connect the start button and solenoid valves A ,B to the NC (Normally Closed) of the relay K.b) Connect the solenoid valves B-, to the NO(Normally Opened) of relay K.c) Connect TB- NO with timer T as shown in circuit.d) Connect the timer switch to the solenoid valve A-.e) Connect the TB to relay K.f) Hold the relay K with K and TA- NC.g) The circuit is designed as per the circuit shown infig 3 below.X. Design of Electric Circuit for Automation Process ofFilling the Bottlesa) The sensors have three terminals one is connected to ve, -ve and the other is output.b) The output of sensor 1 is connected to the relay K2 andthe output of the sensor s2 is connected to relay K3.c) The relay K2 is hold with K2 NO and TV NC.d) The relay K3 is hold with K3 NO and TC- NCe) The solenoid C is connected to K2f) TC NO and the solenoid D are connected to K2g) TD NO and solenoid V are connected to K2.h) The solenoid V- is connected to K3.i) TV- NO and the solenoid D- are connected to K3.j) TD- and the solenoid C- are connected to K3, asshown in below fig 5.IJERT.Fig 4: Pneumatic circuit design for automation process of filling theBottles.Fig 3: Design of Electric circuit for automation of Bottle manufacturingprocess.VIII. SEQUENCE FOR AUTOMATION OF FILLINGTHE BOTTLESFor automation of the filling process the sequenceconsists of clamp the bottle, inject the filler in to the bottle,open the valve, fill the bottle up to required quantity, closethe nozzle valve, eject the filler from the bottle, andunclamp the bottle. The sequence for this process isC D V V-D-CCylinders C, D, V are used for clamping of thebottle, movement of the filler, and nozzle valve open orclose respectively.IX. DESIGN OF PNEUMATIC CIRCUIT FORAUTOMATION PROCESS OF FILLING THE BOTTLESa) Working ports of each cylinder C, D, V are connectedto working ports of each directional control valve.b) The input port of each directional valve which isresponsible for the motion of the piston is connected tothe compressor.c) The port of the directional valve which is responsibleof moving out the pressure from the other side of thepiston is connected to the exhaust.d) The compressor is connected to the pressure source, asshown in fig 4.IJERTV3IS120893Fig 5: Design of Electric circuit for automation process of filling thebottles.XI. SEQUENCE FOR AUTOMATION OF CAPPINGTHE BOTTLESFor automation of capping process the designedsequence is clamp the bottle, movement of the cappingmotor, unclamp the bottle. For automation of this processthe designed sequence is E F F-ETwo double acting pneumatic cylinders E and Fare used for clamp the bottle and to the capping motorrespectively.www.ijert.org( This work is licensed under a Creative Commons Attribution 4.0 International License.)951
International Journal of Engineering Research & Technology (IJERT)ISSN: 2278-0181Vol. 3 Issue 12, December-2014XII. DESIGN OF PNEUMATIC CIRCUIT FORAUTOMATION PROCESS OF CAPPING THEBOTTLES.a) Each double acting pneumatic cylinder’s workingports are connected to working ports of eachdouble solenoid directional control valves.b) The input port of each directional valve which isresponsible for the motion of the piston isconnected to the compressor.c) The port of the directional valve which isresponsible of moving out the pressure from theother side of the piston is connected to theexhaust.d) The compressor is connected to the pressuresource, as shown in fig 6.Fig 7: Design of electric circuit for automation process of capping thebottles.IJERTXIV. SIMULATION FOR AUTOMATION PROCESS OFMANUFACTURING, FILLING AND CAPPING OF THEBOTTLESThe electric circuit that designed is drawn in theFluidsim Pneumatic simulation software by choosing therequired components from the components library and thedrawn circuit is shown in below fig 8.After drawing the circuit press the simulationbutton and circuit is ready for simulation then press thestart button the injection moulding process starts, when thesensors are activated assigned operation is done.Fig 6: Pneumatic circuit Design for automation process of capping thebottles.XIII. DESIGN OF ELECTRIC CIRCUIT FORAUTOMATION PROCESS OF CAPPING THEBOTTLESa) The ve and –ve terminals of the sensor 3 andsensor 4 are connected to power supply andground as shown in below fig 7.b) The output terminals of the sensor 3 is connectedto relay K4 and the output of the sensor 4 isconnected to relay k5.c) The relay K4 is hold with k4 and TF NC.d) The relay K5 is hold with K5snd TE- NC.e) The solenoid E is connected to K4.f) TE and solenoid F is connected to K4g) The solenoid F- is connected to Fh) The solenoid E- and TF- are connected to K5.IJERTV3IS120893www.ijert.org( This work is licensed under a Creative Commons Attribution 4.0 International License.)952
International Journal of Engineering Research & Technology (IJERT)ISSN: 2278-0181IJERTVol. 3 Issue 12, December-2014Fig 8: Design of Electric circuit for entire automation process in Fluidsimpneumatic simulation softwareIJERTV3IS120893www.ijert.org( This work is licensed under a Creative Commons Attribution 4.0 International License.)953
International Journal of Engineering Research & Technology (IJERT)ISSN: 2278-0181Vol. 3 Issue 12, December-2014XV. LADDER PROGRAMMING IN RSLOGIX 500SOFTWAREThe ladder program for the automation of bottlemanufacturing, filling and capping process is shown belowand the following tables show inputs and outputs that areassigned to the Allen Bradley PLC.The connections of inputs and outputs of PLC are shown inbelowTable 1: Inputs assigned in Allen Bradley /18I:0/19I:0/20Fig 9: Inputs and Outputs of PLC for automation of Injection MouldingprocessIJERTSTART BUTTONForward position sensor of cylinder A is TA Retract position sensor of cylinder A is TAForward position sensor of cylinder B is TB Retract position sensor of cylinder B is TBRetract position sensor of cylinder C is TCMotor start SensorForward position sensor of cylinder C is TC Sensor 1Forward position sensor of cylinder D is TD Forward position sensor of cylinder V is TV Sensor 2Retract position sensor of cylinder D is TDRetract position sensor of cylinder E is TESensor 3Forward position sensor of cylinder E is TE Retract position sensor of cylinder F is TFForward position sensor of cylinder F is TF Sensor 4Retract position sensor of cylinder V is TV-Table 2: Outputs assigned in Allen Bradley PLCSolenoid valve of clamping cylinder A to moveO:0/0forward is A Solenoid valve of ram cylinder B to moveO:0/1forward is B Solenoid valve of ram cylinder B to moveO:0/2Reverse is BSolenoid valve of clamping cylinder A to moveO:0/3reverse is ADC motor onO:0/4Solenoid valve of clamping cylinder C to moveO:0/5forwards is C Solenoid valve of filler cylinder D to moveO:0/6forwards is D Solenoid valve of cylinder V for valve openingO:0/7is V Solenoid valve of cylinder V for valve closing isO:0/8VSolenoid valve of filler cylinder D to moveO:0/9reverse is DSolenoid valve of clamping cylinder C to moveO:0/10reverse is CSolenoid valve of clamping cylinder E to moveO:0/11forwards is E Solenoid valve of capping cylinder F to moveO:0/12forwards is F Solenoid valve of capping cylinder F to moveO:0/13reverse is FSolenoid valve of clamping cylinder E to moveO:0/14reverse is E-IJERTV3IS120893Fig 10: Inputs and Outputs of PLC for automation of filling the bottlesFig 11: Inputs and Outputs of PLC for automation of capping the bottleswww.ijert.org( This work is licensed under a Creative Commons Attribution 4.0 International License.)954
International Journal of Engineering Research & Technology (IJERT)ISSN: 2278-0181Vol. 3 Issue 12, December-2014XVI. CONCLUSIONThe designed low cost industrial automationprocess is of programmable. The automation process haspreciseness and accuracy in their operations, which iscontrolled through its controllers. The sequence ofoperations are such as automatic clamping, de-clamping,injecting the molten material, filling and capping process ofthe bottles are essential in industries to increase itsproduction rate. Therefore, the required ladder program isdesigned in the programmable logic controller to itsoperating process. This is achieved through the use ofsimple devices like limit switches, relays, sensors,pneumatic actuators and electrical controls. The electriccircuits are designed and the sequence of operations aretested by using Fluidsim Pneumatic simulation software.The Automation process helps in reducing thetime taken for the process to be completed. TheImplementation of Low Cost Industrial Automation ,particularly in small scale industries with simple usage ofdevices like pneumatic, actuators with electrical control tothe existing conventional methods will make theautomation at low cost to yield higher productivity.IJERTXVII. FUTURE SCOPEA scope for automation process to reduce the timerequired for testing the quality of Bottles. There is also ascope for automation process to measure the quality of theliquid filled in the bottles. The production rate is to bestored in the PLC. A record of the data like materialavailability, machines availability should be integrated withPLC for optimum utilization of machines to increase theproduction rate.XVIII. REFERENCESMallaradhyah M, K.R.Prakash “Automatic Liquid Filling to Bottlesof Different Height Using Programmable Logic Controller.”International Journal of Mechanical and Production Engineering,ISSN: 2320-2092, Volume- 1, Issue- 4, Oct-2013.2. Savita, Lokeshwar “Implementation and Performance Analysis ofBottle Filling Plant Using Ladder Language.” (IJSR) ISSN(Online): 2319-7064 Impact Factor: 3.358 Paper ID: 0201516(2012).3. Ahmed Ullah Abu Saeed, Md. Al-Mamun and A.H.M. ZadidulKarim “Industrial Application of PLCs in Bangladesh.” InternationalJournal of Scientific & Engineering Research, ISSN 2229-5518,Volume 3, Issue 6, June-2012.4. Kelvin T Erickson, “A Programmable logic controllers”, IEEEpotentials, pp.14-17, march-1996.5. Nabil Shaukat, “A PLC Based Automatic Liquid Filling Process”,IEEE, publication page No. 226-233, 2002.6. J. Swider, G. Wszolek, W. Carvalho “Programmable controllerdesigned for electropneumatic systems” 13th International ScientificConference on Achievements in Mechanical and MaterialsEngineering, 16 th-19 th May 2005,Gliwice-Wisla, Poland.7. Zeliko Situm, Tihomir Zilic and Mario Essert “High Speed SolenoidValves in Pneumatic Servo Applications” 15th MediterraneanConference on Control and Automation, July 27th-29th 2007, AthensGreece.8. Chengwen Chai, Jifie Cai, Yiming Wang and Shuqin Wu “Researchon PLC-Based Pneumatic Controlling System of Flying Splicer ofWeb-Fed Offset Presses”. The open Mechanical EngineeringJournal, Volume 5, 2011.9. Darshan P, H.V. Ramakrishna, Vijayavithal Bongale “PLC BasedAutomatic Powder Coating Machine Controller” ,InternationalJournal of Applied Engineering Research ,ISSN 0973-4562, pp.755763,Volume 9, Number 7 (2014).10. Munstaser Momani, Mohammed Abuzalata, Igried Khadwaldch andHisham Mujafet “Pneumatic, PLC Controlled, Automotive Gear1.Fig 12: Ladder Program for Automation ProcessIJERTV3IS120893www.ijert.org( This work is licensed under a Creative Commons Attribution 4.0 International License.)955
International Journal of Engineering Research & Technology (IJERT)ISSN: 2278-0181Vol. 3 Issue 12, December-2014IJERTShifting Mechanism”, Research Journal of Applied Sciences,Engineering and Technology, ISSN: 2040-7467, Publication Date:May 10, 2010.11. Sadegh vosough and Amir vosough “PLC and its Applications”International Journal of Multidisciplinary Sciences and Engineering,vol. 2, no. 8, November 2011.IJERTV3IS120893www.ijert.org( This work is licensed under a Creative Commons Attribution 4.0 International License.)956
understandable of the more people [11]. Any machine can be controlled automatically by use of PLC. For automation of process write the program in the software then transfer the program to the PLC and after that connect the PLC to the machine [2]. A single PLC can run many machines at same time. The PLC has capability for handling several