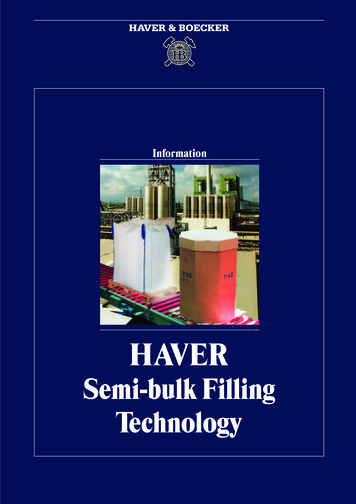
Transcription
HAVER & BOECKERInformationHAVERSemi-bulk FillingTechnology
Semi-bulk containersFIBC – Flexible intermediate bulk containerStable Big-bagsHAVER & BOECKERhave been producingfilling and weighingsystems for flexiblepackaging such asFIBCs, octabins, cartonsand other semi-bulkpackaging units for over20 years. When compared to conventionalbags or other smallpackages, these systemsrepresent a cost effectivealternative within thelogistical supply chainfor handling bulk prod-2ucts. HAVER technologyis suitable for all applications involving fillingand bagging of solids.Commercially availableFIBCs with 1, 2 or 4loops and a rigid fillingspout or open top sideare easily filled. Specialbig-bag design featuressuch as baffles forimproving stability havebeen fully taken intoaccount during thedesign phases of ourfilling systems.In combination with acarrier frame, barrels andcartons may be filledusing the same weighingsystem. For big-bagswith PE liner, the fillingsystem is equipped witha bag inflation unitwhich expands the bagbefore filling starts. Forthis operation, systemsusing compressed air orblowers are available.Using modular configurations and provencomponents, we deliveroptimized individualsolutions that fulfillspecific technical needs,are economical andenvironmentally sound.
Filling system for FIBC with one loopFIBCs with one loop havepenetrated the market,especially for largequantities of loose, bulkmaterials such as cement,fertilizers, etc. wherehigh filling rates can beachieved using basictechnology. For the mostpart, the technologyinvolves bags that arefilled, weighed andtransported whilehanging, and assuringbag stability forsubsequent transport bya forklift.Big-bag filling and weighing systemDepending on materialflow characteristics,filling rates of up to40 Big-bags per hour arepossible. For filling, thespout is inserted into thebag opening. The bagloop is hooked to thesuspension hook whichin turn is connected tothe suspension eyelet ofthe weigher load cell.Using a START button,the filling cycle startsand the product issimultaneously weighed.A cone valve regulatesproduct feeding into thebag. After the fillingends, the filled bags aretransported away fromthe filling station by thestacker and changeoversuspension hooks. Thechangeover suspensionhooks assure continuous,uninterrupted production.Weighing and fillingparameters are selectedusing the weighingelectronic. By usingoptional suspensionframes, 2-point or4-point FIBCs maybe filled as well.Efficient filling andweighing systems thathave robust, long lastingand precise constructionare the results of ouryears of developmentwork.These filling systemsmay be laid out in pairsfor direct loading oftrucks, or they may bestationed as mobile unitsunder silos.HAVER Big-bag weigher3
Product compaction during fillingThe decisive factorsfor optimum filling andFIBC stability are theappropriate air extractionrates and productcompaction, as to theproduct’s properties.These are the keys toHAVER’s proventechnology.Powder type products,which are filled in afluid state, are preferablyde-aerated by using avacuum probe. For thisoperation, the vacuumprobe is made of HAVERPoroplate wire mesh andused according to thefilling volume. Thepore size of the vacuumprobe is determined bythe smallest graindiameter of the product(min. 1µm). Airextraction from theproduct occurs duringcoarse filling, or afterfilling and is programmable via the control unit.shear angle have beenoptimized for a widevariety of products byemploying a HAVERvibration unit.Depending on theproduct’s properties,an individual vibrationsystem is selected.Agitation motors,controlled by a frequencyinverter, allow selectionof a frequency that bestmatches the product’sproperties. Depending onthe product’s flowcharacteristics, thisassures the selection ofthe optimum compactionparameters.All product-specificadjustment parametersare selected via thecontrol panel.Product compaction andreduction of the productAir extraction from the productusing the HAVER Poroplate vacuum probePhoto left:The vibration unit is integratedwith the roller conveyor4
High performancemachines for powdertype, loose materialsrequire systems thatmatch the product. Forfilling rates of over40 bags per hour, a fillingsystem with two compaction units may beused. The product iscompacted at the fillingstation by a HAVERvibration table. Foroptimizing productivity,the filled but not yet fullycompacted bag is thentransported to a subsequent compaction stationwhere a second vibrationtable further compacts theproduct. This results infully compacted FIBCfilled bags, even at highfilling speeds. Thesuccess of this systemhas been proven,especially when fillinghighly fluid, loosematerials. Thecombination of vacuumair extraction and avibration unit is also aproven systemconfiguration forachieving the highestpossible filling speeds.High performance filling station equipped with two vibration units.5
HAVER product dosing and system componentsScrew conveyor dosingforpowder type productsElectro-magnetic feederforcoarse product1. Guide assembly452. Operator’s panel63. Hoisting unit6Cone dosifomicro
ng systemrpelletsFlap-dosingforgranulated products or pelletsBelt conveyor dosingforblended products4. Load cell135. Pneumatically operated hook26. Filling spout with an inflatable sleeve(option)7
OperationThe wide variety ofavailable FIBCs requiresa variable filling headthat can be optimallyoperated when fillingbags of different sizes.The HAVER FIBC fillinghead has been optimizedfor easy operation. Therear hooks are swiveledin position by a pneumatic cylinder and is easilyaccessible by the operator. The filling stationthen swings over to theoperator. Dust-free fillingof the FIBC is assured byan inflatable sleeve and acounter-pressure ringinstalled at the fillingspout.The sturdy filling head isattached to 3 load cells,which are connected tothe HAVER electronicweigher system andassure precisionweighing – even fortechnically difficult, freeflowing materials.The HAVER FIBC fillingsystem has proven itselfto be a high performance,reliable filling system –even when operated inextremely dusty oraggressive environments.Together with theoperator’s terminal,the HAVER electronicweigher system fulfillsall the requirementsfor easy, functionallyappropriate operationof filling stations. Allimportant functions anddata are displayed online.8Diagram above:Diagram of an FIBC fillingstation with an integratedvibration unitPhoto left:Operator’s terminal for theelectronic weighing systemand touchpanel for machineoperation
OptionsTo avoid product leakagefrom the filling spout during bag changes, a fillingspout closure unit maybe installed as an option.After the filling step iscompleted, the closureunit tightly closes off theend of the spout.As a result, contaminationof the outside surface ofbags from residualproduct spillage iseliminated. This closureunit is designed not tointerfere with productflow during filling.The HAVER FIBC fillinghead may be combinedwith an automatic bagclosing unit. For closingof the bag after the fillingoperation, the filling headis decoupled from thecompressed air systemand, by rotating the fillingspout, a so-called “tulip”is formed. The dust-free,wound bag may be theneither manually or automatically closed using ametal clip. Except forhanging empty bags, thisoption assures a complete,functional process thattakes place automatically.Filling spout closure unitBig-bag closing unit9
Pallet transportA complete Big-bag filling system equipped with a pallet unitizer, roller system and filling stationEspecially where highfilling rates and thesubsequent transport ofthe filled bags on palletsare foreseen, it makessense to add a pallettransport system. Rollertracks and pallet dispensers are availablefor achieving this andare customized to meetspecific fillingrequirements. If desired,a slip sheet applicatormay be included as well.If bags with smallerweights are to be stackedover each other, theroller tracks may bereversible and therebyallow, for example, 2 oreven 3 bags to be automatically stacked underthe filling head. Preciselycontrolled conveyorelements assure perfectlycentered FIBC stacking.Perfectly centered, double big-bag stacking10
System variationsThis filling station,which is designed foroctabins and FIBCs witha filling speed of maximum 40 bags per hour, isan example of technology that exactly fulfills theneeds of a specific application. Together with aHAVER net weigher andan integrated HAVERvibration station, plasticpellets are optimallybagged and sealed.Ein Team erfahrenerIngenieure unterstütztund berät Sie von derErstellung desAnlagenkonzeptes biszur Inbetriebnahme.Für die Detailplanung,Abwicklung undDokumentationstehen uns modernsteHilfsmittel zurVerfügung.The entire unit is built onwheels, is fully mobileand may be docked underany silo of choice. Allproduct relevant data aretransmitted via a radiocommunication systemfrom a central controlroom.In addition, this fillingstation is equipped withan automatic watercleaning system thatprovides quick and easycleaning during productchangeovers.Mobile semi-bulk filling station11
HAVER & BOECKERTHE ORIGINALSROTO-PACKERTHE BENJAMININTEGRASILOSI BAU HAMBURGPelletising DiscsLIQUIDSFine-LineFRONTLINET-CLASSHAVER HAVER HAVERTYCAN H-CLASSROTOCEMFILLCEMPM 214FeFeXXX EX2840XXXX0307XXXX1 XMADE BYTHE HAVER GROUPP.O. Box 33 20 D-59282 OELDE, Germany Phone: 49-25 22-30 0 Fax: 49-25 22-30 403 E-mail: mf@haverboecker.comThe machines and plants shown in this leaflet as well as the stated technical parameters are examples of customer-specific technical solutions. Therefore they are subject to modifications.HAVER HAVER HAVER
filling rates of up to Big-bag filling and weighing system 40 Big-bags per hour are HAVER Big-bag weigher possible. For filling, the spout is inserted into the bag opening. The bag loop is hooked to the suspension hook which in turn is connected to the suspension eyelet of the weigher load cell. Using a START button, the filling cycle starts .