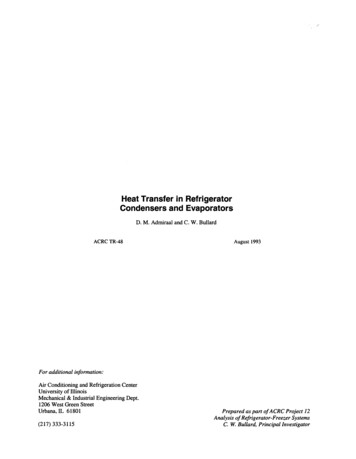
Transcription
,.'Heat Transfer in RefrigeratorCondensers and EvaporatorsD. M. Admiraal and C. W. BullardACRCTR-48August 1993For additional information:Air Conditioning and Refrigeration CenterUniversity of IllinoisMechanical & Industrial Engineering Dept.1206 West Green StreetUrbana, IL 61801(217) 333-3115Prepared as part ofACRC Project 12Analysis of Refrigerator-Freezer SystemsC. W. Bullard, Principal Investigator
The Air Conditioning and RefrigerationCenter was founded in 1988 with a grantfrom the estate of Richard W. Kritzer, thefounder of Peerless of America Inc. A Stateof Illinois Technology Challenge Granthelped build the laboratory facilities. TheACRC receives continuing support from theRichard W. Kritzer Endowment and theNational Science Foundation. Thefollowingorganizations have also become sponsors ofthe Center.Acustar Division of ChryslerAllied-Signal, Inc.Amana Refrigeration, Inc.Brazeway, Inc.Carrier CorporationCaterpillar, Inc.E. I. du Pont de Nemours & Co.Electric Power Research InstituteFord Motor CompanyFrigidaire CompanyGeneral Electric CompanyHarrison Division of GMICI Americas, Inc.Modine Manufacturing Co.Peerless of America, Inc.Environmental Protection AgencyU. S. Army CERLWhirlpool CorporationFor additional information:Air Conditioning & Refrigeration CenterMechanical & Industrial Engineering Dept.University of Illinois1206 West Green StreetUrbana IL 618012173333115
Table of ContentsPageList of Tables . vList of Figures . viNomenclature . viiChapter1. Introduction . 11.1 Purpose . 11.2 Development of the variable conductance model . 21.3 Heat transfer correlations . 31.3.1 Two-phase correlations . 31.3.2 Single-phase correlations . 62. Evaporator Model . 92.1 The two zone model . 92.2 The one zone model . 162.3 Comparison with constant conductance models . 182.4 Summary . 193. Condenser Model . 203.1 Air-side complexities . 203.2 Recirculation fraction . 213.3 Volumetric air flow rate and leak fraction . 233.4 Condenser inlet air temperature . 233.5 Governing equations . 263.6 Summary . 314. Conclusions and Suggestions for Future Research . 334.1 Conclusions . 334.2 Suggestions for future research . . 35References . 37AppendixA. Objective Functions for Parameter Estimation . 38B. Evaporator and Condenser Geometric Complexities . 42B.l Evaporator . 42B.2 Condenser . 43C. Split Fraction and Volumetric Air Flow Rate in the Evaporator . 45D. Possible Improvements In Condenser Performance . 49D.l Improving air flow . . 49D.2 Eliminating recirculation . 50111
E. Calculation of Refrigerant Mass Flow Rate . 52F. Comparison of Measured and Calculated Data . 56IV
List of Tables ThWe2.12.22.33.13.2C.1C.2Results of evaporator model . 14Calculation of air split fraction and volumetric flow rate . 15Two-zone constant conductance results . 18Recirculation fraction . 22Summary of condenser results . 29Independent calculation of air split fraction and volume flow rate . 47Simultaneous calculation of air split fraction and volume flow rate . 48v
List of Figures .1E.2F.1F.2F.3F.4F.5F.6Comparison of BoPierre and ChatolWattelet heat transfer coefficients . 5Evaporator heat exchanger geometry . 9Comparison of calculated and measured evaporator loads for data set I . 12Comparison of calculated and measured evaporator loads for data set 11. 12Heat load confidence interval vs. volumetric air flow rate . 13Air flow through refrigerator compartment . 15Comparison of ChatolWattelet and BoPierre parameter estimation . 17Condenser heat exchanger geometry . 20Comparison of calculated and measured values of grille inlet temperature . 22Front view of condenser air inlet . 24Condenser inlet air temperature distribution . 24Average air inlet temperatures . 25Comparison of calculated and measured condenser loads . 30Contributions to overall heat transfer resistance . 35Air mixture control volume . 45Data set I refrigerant mass flow measurements . 53Data set II refrigerant mass flow measurements . 54Evaporator exit temperature comparison, data set 1. . 56Evaporator exit temperature comparison, data set II . 56Single-zone evaporator load comparison, data set II . 57Condenser load comparison, Reeves (1992) . 57Condenser load comparison, data set I. . 58Condenser load comparison, data set II . 58vi
Nomenclature[ft2]AareaCheat capacity (rbcp)cpspecific heatDinternal tube diameterffractionGmass fluxgacceleration of gravityhheat transfer coefficienthfgheat of vaporizationJmechanical equivalent of heatkthermal conductivityLlength of tubeeft]Ihmass flow rate[lbm/h]Qheat transfer[Btu/h]q"heat flux through tube wallRheat transfer resistancerradius of tubeeft]swall thicknesseft]TtemperatureUheat transfer conductanceVvolumetric air flow h·ft2)][ft/s2][Btu/(h·ft2. oP)][Btu/lbm][778.3 .OP/Btu][OP][Btu/(h·ft2. oP)][cfm]Greek symbolsexratio of external area to internal area6hchange in enthalpyEeffectiveness[Btu/lbm]VB
ffriction factorJ.LviscositypdensityXttLockhart-Martinelli parameter[lb·s/ft 2][lb/ft3][( r( rC:xrlSubscriptsairair-side parameterair, indspair, inlet of desuperheating region (evaporator)air, inspair, inlet of superheating region (evaporator)air, intpair, inlet of two-phase region (evaporator)air,middownstream inlet air (condenser)air, sgisubcooled region inlet air (condenser)air, tpgiupstream two-phase region inlet air (condenser)air!air-side parameter of two-phase region upstream of condenser fanair2air-side parameter of two-phase region downstream of condenser fancalccalculated valuecondentire condenserdas a function of tube diameterdspdesuperheating regioneairevaporator air-side calculationeoevaporator exit parameterevapentire evaporatorevaploadmeasurement of evaporator loadfrefrigeratorfsfin-side parameteriinternal tube parameter1liquidmmean tube parameterVlll
" 'rnamixed air before evaporator inletmeasmeasured valuerateas described by rate equationsrefrefrigerant-side parameterref, indsprefrigerant, inlet of desuperheating region (evaporator)ref, insprefrigerant, inlet of superheating region (evaporator)ref,intprefrigerant, inlet of two-phase region (evaporator)ref, 1compressor exit refrigerantref,2two-phase refrigerant (condenser)sbsubcooled regionspsuperheating regionttheoretical parametertptwo-phase regiontpitwo-phase refrigerant parameter upstream of condenser fantp2two-phase refrigerant parameter downstream of condenser fanvvaporzfreezerDimensionless groupsBoBoiling number[q/(G·hfg)]FrFroude number[G2/(p2. g .D)]NuNusselt number[h·DIk]PrPrandtl number[cp·JlIk]ReReynolds number[G·D/Il]IX
.'
Chapter 1Introduction1.1 PurposeThe phase-out of CFCs by the year 1995 and the impending phase-out of HCFCs in thefuture has created a need for redesigning new refrigerators and retrofitting old ones with newrefrigerants. This report describes an extensive experimental and analytical effort aimed atpredicting the performance of evaporators and condensers using alternative refrigerants. Heatexchanger models are also expressed in a form where heat exchanger tube diameters and lengthsare explicitly specified to help analyze new configurations.Existing refrigerator models often use a constant conductance modeling approach (e.g.ADL (Merriam et. aI., 1992), Porter and Bullard (1993)). These models are better than thesingle-zone constant-VA model used by the V.S. Department of Energy to set the 1993 energystandards (ADL, 1982). However, they fail to account for changes in heat transfer resistance dueto changes in refrigerant flow characteristics. Characteristics that may affect the resistance toheat transfer include refrigerant mass flow rate and refrigerant properties. For instance, in ourrefrigerator overall heat transfer resistance may change more than 10 percent in the two-phaseregion of the evaporator and more than 20 percent in the superheated region.In addition to being more accurate than the constant conductance model, the variableconductance model is also more flexible. When the constant conductance model is used aconductance is determined for each zone of both the evaporator and the condenser. Theconductances that are determined are only useful for the refrigerant that was used in the system atthe time when the conductances were determined. This is because conductances are dependenton the properties of the refrigerant in the system. The variable conductance model takes theproperties of the refrigerant into account. The coefficients of the variable conductance modelneed to be determined once; after that the model can be used for different operating conditions,tube diameters, and refrigerants.I
Finally, the model will be useful for assessing the applicability of refrigerant heat transfercorrelations to refrigerator models. The correlations that are used in our models were developedunder ideal conditions in long straight tubes. The accuracy of our models will provide insightinto how well the heat transfer correlations work in actual modeling applications.1.2 Development of the variable conductance modelThe overall heat transfer equation for a heat exchanger must be written so that thevariable conductance model can be invest
The overall heat transfer equation for a heat exchanger must be written so that the variable conductance model can be investigated. The equation is developed by identifying each component of the resistance to heat transfer between the two working fluids of the heat exchanger. For the case of an evaporator or a condenser there are three .