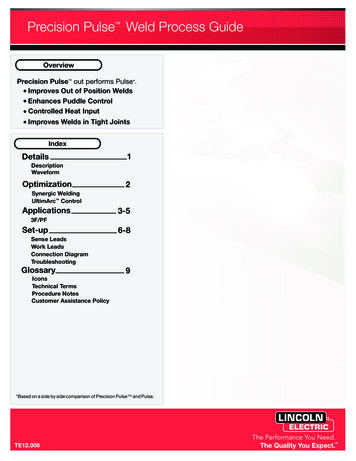
Transcription
TMPrecision Pulse Weld Process GuideOverviewPrecision Pulse out performs Pulse*.Improves Out of Position WeldsEnhances Puddle ControlControlled Heat InputImproves Welds in Tight 2Synergic WeldingUltimArc ControlApplications3-53F/PFSet-up6-8Sense LeadsWork LeadsConnection DiagramTroubleshootingGlossary9IconsTechnical TermsProcedure NotesCustomer Assistance Policy*Based on a side by side comparison of Precision Pulse and Pulse.TE12.008The Performance You Need.The Quality You Expect.SM
TMPrecision Pulse Details1Process DescriptionIdeal for out of position welds, Precision Pulse gives theoperator control over where the droplet transfers and how thepuddle forms. A shorter, more focused arc increases puddlecontrol and improves operator confidence compared toPulse. Frequency adjustment changes the focus and dropletsize increasing control of the weld puddle. The PrecisionPulse waveform is ideally suited for out of position weldswith enhanced puddle control.lsePuFREQUENCY (Hz)Traditional Pulse welding consists of a peak and backgroundcurrent to deposit a molten droplet after each pulse.Precision Pulse functions similarly, but at a fixed frequencyto create a more consistent droplet transfer. The waveform iscapable of producing an extremely focused arc at a lowervoltage.n P u lsecisioPreWFS (in/min)Waveform2 Tailout1Pulse Ramp / PeakReducing current relaxes theplasma force as the dropletapproaches the puddlecreating a clean droplettransfer.A controlled currentincrease creates a moltendroplet without disturbingthe puddle and minimizesthe size of the arc cone.BackgroundLower background helpsm a i n t a i n c o n t ro l b yminimizing the puddleheating.34FrequencyFrequency is a presetvalue. The UltimArc control allows theoperator to fine tune thepulse frequency.The Performance You Need.The Quality You Expect.SM
TMPrecision Pulse Optimization2Synergic Welding1V - Adjust WFS to the desired setting.Refer to the Applications sectionfor the recommended settings.22Based on WFS a pre-programmednominal voltage is selected.Synergic Graph Precision Pulse waveforms aresynergic weld modes. Based on thewire feed speedu, set by the operator,a p re - p ro g r a m m e d v o l t a g e i sautomatically selectedv. Fine tunethe arc length using Voltage.3 -Min.VMax.Synergic Voltage DisplayAbove ideal Voltage(Upper bar displayed)At Ideal Voltage(No bar displayed)Below Ideal Voltage(Lower bar displayed)Adjusting voltage increases ordecreases the arc length, allowingthe user to fine tune arccharacteristics.Synergic Weld modes improve theease of set-up by pre-selecting anideal voltage based on theselected WFS. The user can thenfine tune their Voltage settingbased on their personalpreference and can easily seewhether they are above or belowthe nominal setting.UltimArc ControlThe UltimArc control allows the userto make all the necessary adjustmentsto fine tune the frequency through asingle dial. Increase ( ) or decrease(-)this setting to optimize the focus anddroplet transfer of the arc. 100-10The Performance You Need.The Quality You Expect.SM
TMPrecision Pulse Applications33F / PFoUse a 10 drag angle. 3F45ooUse a 45 work angle. A weave is typically used. TOP10oSIDE90Ar / 10CO21/2 in.VA21.020.019.519.018.0130110958570SuperArc L-560.035”in / min2501/2 in.2103/8 in.1751/4 in.1503/16 in.10 ga125SuperArc L-560.040”1/2 in.3/8 in.1/4 in.3/16 in.10 uperArc L-560.045”1/2 in.3/8 in.1/4 in.3/16 in.1501301109020.019.519.018.01201109570See Customer Assistance Policy and Procedure Notes on page 9.The Performance You Need.The Quality You Expect.SM
TMPrecision Pulse Applications43F / PF Cont.98Ar / 2CO21/2 in.Blue Max 308LSi0.035”in / min2751/2 in.2503/8 in.2251/4 in.2003/16 in.10 ga150Blue Max 308LSi0.045”1/2 in.3/8 in.1/4 in.3/16 in.10 19.018.017.517.016.01401201008065VA90He / 7.5Ar / 2.5CO21/2 in.Max Blue0.035”1/23/81/43/1610gain / /23/81/43/1610gain / 308LSiBlue Max 308LSi0.045”See Customer Assistance Policy and Procedure Notes on page 9.The Performance You Need.The Quality You Expect.SM
TMPrecision Pulse Applications53F / PF Cont.Metric80Ar / 20CO212mmSupraMig 1.0mmSupraMig 1.2mmVAmm1310753m / 570VA98Ar / 2CO212mmLNM 304LSi1.0mmmm1310753m / 008070LNM 17.016.51351151008065See Customer Assistance Policy and Procedure Notes on page 9.The Performance You Need.The Quality You Expect.SM
TMPrecision Pulse Set-Up6Sense Leads A positive ( ) sense lead is required. Thisis a standard connection in an ArcLink cable.A negative sense lead (optional) is highlyrecommended for total welding cablelengths 50 ft. and should be connecteddirectly to the workpiece. -For best performance, connect the worksense lead close to the welding arc.DO NOT connect either sense lead to awelding stud on the power source as thismay result in erratic arc behavior.The negative sense lead should beseparated away from welding cables tominimize interference.-DO NOT route sense lead cable close tohigh current welding cables as this maydistort the sense lead signal.Work Leads --ABCConnect the work lead to the negativestud on the power source and directly tothe workpiece. Maintain the shortestconnection length possible.The total length of the welding currentloop (A B C) should be minimized toreduce inductance.Route cables (A,B) close together tofurther reduce cable inductance.For configurations with excessiveinductance, use Lincoln Electric patented coaxial welding cables.Lincoln Electric coaxial cablescombine the positive and negativewelding leads into one cable to minimizecable inductance.Test cable inductance levels using thePower Wave Manager softwareexclusively from Lincoln Electric Software is available atwww.powerwavesoftware.com.The Performance You Need.The Quality You Expect.SM
TMPrecision Pulse Set-Up7Connection DiagramOptionalThe Performance You Need.The Quality You Expect.SM
TMPrecision Pulse Set-UpTroubleshootingProblem-!!!Burnthrough !Poor Penetration!! - - - -! Concave Bead-!-!Convex Bead-------Contact Tipto WorkDistanceo -Wire FeedSpeed!Under cut-Travel Speed!Porosity- VoltsErratic arc-SpatterV8!!-Push Angle- Tip ?!Gas Coverage!SurfaceContaminants!Proper Feeding Sense Lead Increase-Solution?DecreaseInspect & Replace!ImportantThe Performance You Need.The Quality You Expect.SM
TMPrecision Pulse Glossary9IconsWire TypeGasMaterialThickness Weld StudTorchPositiveSense LeadWire FeedSpeed- NegativeSense LeadVATravel SpeedVoltsAmpsWork ClampFeederTorch NozzleContact Tipto WorkDistanceSpatter (Minimal)Arc LengthSpatterControl KnobDroplet Size(Large)Stop / AvoidDroplet Size(Small)Technical TermsCable InductanceResistance to change in current.GMAWGas metal arc welding including metal inert gas (MIG) and metal active gas (MAG) welding.PorosityGas entrapped in solidifying metal forms spherical or elongated pores in the weld.Push AngleThe angle at which the electrode leads the weld pool relative to the direction of travel.SynergicA mode of control which automatically selects a preprogrammed nominal voltage based on the wirefeed speed (WFS) set by the operator.Work AngleThe angle of the electrode, off perpendicular, relative to the workpiece surface.Procedure NotesAll listed procedures are starting points and may The result of welding at higher travel speeds is arequire some adjustment depending on the specific tendency to produce more spatter, less penetration,application.more undercut, and a less desirable bead shape.Depending on the limitations / requirements of theTorch angle, electrode placement, contamination, actual application, slower travel speeds and highermill scale, joint fit up, and joint consistency are arc voltages may be required.factors that may require special considerationdepending on the specific application.As the travel speed increases in fast followapplications (1/4” to 14 Gauge), a tighter and arcAt higher travel speeds, joint fit up, wire placement, length must be maintained so that the puddleand contamination all become factors that are more properly follows the arc. Operators typically reducesignificant.the arc length control (Trim) to achieve this. At fastertravel speeds, the bead-shape can become veryconvex (or ropy), and the weld will not “wet” well.There is a point at which the arc is set so short thatthe arc will become unstable and stubbing willoccur. This forms a limitation of just how fast thetravel speed can be raised.It is ultimately the responsibility of the end user toensure the proper weld deposition rate, beadprofile, and structural integrity of a given weldapplication.Refer to the included trouble-shooting guide forassistance in overcoming welding issues.Customer Assistance PolicyThe business of The Lincoln Electric Company is manufacturing and selling high quality welding equipment, consumables, and cutting equipment. Our challengeis to meet the needs of our customers and to exceed their expectations. On occasion, purchasers may ask Lincoln Electric for information or advice about theiruse of our products. Our employees respond to inquiries to the best of their ability based on information provided to them by the customers and the knowledgethey may have concerning the application. Our employees, however, are not in a position to verify the information provided or to evaluate the engineeringrequirements for the particular weldment. Accordingly, Lincoln Electric does not warrant or guarantee or assume any liability with respect to such information oradvice. Moreover, the provision of such information or advice does not create, expand, or alter any warranty on our products. Any express or implied warranty thatmight arise from the information or advice, including any implied warranty of merchantability or any warranty of fitness for any customers’ particular purpose isspecifically disclaimed.Lincoln Electric is a responsive manufacturer, but the selection and use of specific products sold by Lincoln Electric is solely within the control of, and remains thesole responsibility of the customer. Many variables beyond the control of Lincoln Electric affect the results obtained in applying these types of fabrication methodsand service requirements.Subject to Change – This information is accurate to the best of our knowledge at the time of printing. Please refer to www.lincolnelectric.com for any updatedinformation.The Performance You Need.The Quality You Expect.SM
135 100 115 85 100 70 80 65 13 13 10 10 7 7 5 5 3 3 5.08 5.72 4.45 5.08 3.81 4.45 3.18 3.81 2.54 3.05 21.5 19.5 21.0 19.0 20.5 18.5 20.0 18.0 19.0 17.5 115 125 105 115 90 100 80 80 65 70 m / min mm m / min V V A A 12mm 12mm 80Ar / 20CO 2 98Ar / 2CO 2 SupraMig 1.0mm LNM 304LSi 1.0mm SupraMig 1.2mm LNM 304LSi 1.2mm Precision Pulse ApplicationsTM 5 The Performance You Need. The