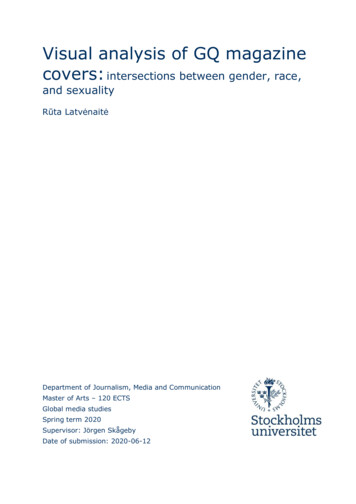
Transcription
Process planning forprecision manufacturingAn approach based on methodologicalstudiesMats BaggeDoctoral Thesis 2014KTH Royal Institute of TechnologyEngineering SciencesDepartment of Production EngineeringSE-100 44 Stockholm, Sweden
TRITA IIP-14-04ISSN 1650-1888ISBN 978-91-7595-172-0Akademisk avhandling som med tillstånd av KTH i Stockholm framlägges till offentliggranskning för avläggande av teknisk doktorsexamen tisdagen den 10 juni 2014 kl. 13:00 isal M311, KTH Industriell Produktion, Brinellvägen 68, StockholmCopyright Mats Bagge 2014Tryck: Universitetsservice US AB
IIIAbstractProcess planning is a task comprising a broad range of activities todesign and develop an appropriate manufacturing process for producinga part. Interpretation of the part design, selection of manufacturingprocesses, definition of operations, operation sequences, machiningdatums, geometrical dimensions and tolerances are some commonactivities associated with the task. Process planning is also “the linkbetween product design and manufacturing” with the supplementarycommission to support design of competitive products.Process planning is of a complex and dynamic nature, often managedby a skilled person with few, or no, explicit methods to solve the task. Thework is heuristic and the result is depending on personal experiences anddecisions. Since decades, there have been plenty of attempts to developsystems for computer-aided process planning (CAPP). CAPP is stillawaiting its breakthrough and one reason is the gap between thefunctionality of the CAPP systems and the industrial process planningpractice.This thesis has an all-embracing aim of finding methods that coveressential activities for process planning, including abilities to predict theoutcome of a proposed manufacturing process. This is realised bygathering supporting methods suitable to manage both qualitative andquantitative characterisation and analyses of a manufacturing process.The production research community has requested systematisationand deeper understanding of industrial process planning. This thesiscontributes with a flow chart describing the process planning process(PPP), in consequence of the methodological studies. The flow chartincludes process planning activities and information flows between theseactivities.The research has been performed in an industrial environment forhigh volume manufacturing of gear parts. Though gear manufacturinghas many distinctive features, the methods and results presented in thisthesis are generally applicable to precision manufacturing of many kindsof mechanical parts.KeywordsProcess planning, precision manufacturing, machining, tolerancechain analysis, process behaviour, process performance, processcapability, in-process workpiece.
VAcknowledgementsThis thesis is a result of my work as an industrial PhD student at theDepartment of Production Engineering IIP, KTH Royal Institute ofTechnology, employed by Scania CV AB, Södertälje. Since the start in2006, I have been involved in several research projects wherecollaborations between Swedish industry, academia and researchinstitutes have been a common denominator. These projects haveprovided many interesting research topics related to my main field ofresearch – process planning – and given many fruitful opportunities toget to know nice and proficient people.Among these people, I would first like to express my specialappreciation and thanks to my supervisors Professor Bengt Lindberg andProfessor Sören Andersson at KTH and Ulf Bjarre at Scania CV AB forinspiring cooperation over the years of studies. The appendedpublications in this thesis have also been written in an invigoratingmanner together with Professor Cornel Mihai Nicolescu, Mats Werke andMikael Hedlind. Thank you!I would also like to thank my colleague and participant in the KUGGproject, Julia Lundberg Gerth for taking time and giving well adviseswhen writing this thesis. My appreciations to the other Ph.D. students inthe KUGG project (where it all begun); Mathias Werner, Ellen Bergseth,Sören Sjöberg and Karin Björkeborn.One important source for inspiration and discussions about crossdisciplinary considerations related to production research has beenparticipating in the seminars lead by Associate Professor Peter Gröndahl.Many persons have contributed to the engaging enthusiasm in theseminar group, especially Robert Gerth, Tord Johansson, Joakim Storck,Jens von Axelson, Richard Lindqvist and Magnus Lundgren.I have in addition had the favour to get to know and spend timetogether with many people at IIP, in front of others; Anders Berglund,Andreas Archenti and Lorenzo Daghini. It has been a pleasure to cadgeyour offices!- Marie, Johan, Maj-Britt and Mona, let me express my sinceregratitude for all your assistance when colloquial duties have not fit intomy business schedule!Finally, all my love goes to Carolin, Hanna and Ellen. You are great!Mats Bagge, Södertälje, May 2014
VIIList of publicationsThis thesis is based on five publications of which one is a licentiatethesis and four are papers. The four papers are appended at the end ofthis doctoral thesis.Licentiate thesis (not appended)Bagge, M., 2009. An approach for systematic process planning of geartransmission parts. Licentiate thesis, Stockholm, Sweden: Royal Instituteof Technology.Paper AWerke, M., Bagge, M., Nicolescu, M. & Lindberg, B., 2014. Processmodelling using upstream analysis of manufacturing sequences.Submitted to: The International Journal of Advanced ManufacturingTechnology (Under review April 2014).Paper BBagge, M. & Lindberg, B., 2012. Analysis of process parameters duringpress quenching of bevel gear parts. In: M. Björkman, ed. Proceedings ofThe 5th International Swedish Production Symposium. Linköping:Produktionsakademien, pp. 251-259.Paper CBagge, M., Hedlind, M. & Lindberg, B., 2013. Tolerance chain design andanalysis of in-process workpiece. In: A. Archenti & A. Maffei, eds.Proceedings of the International Conference on AdvancedManufacturing Engineering and Technologies. Stockholm: KTH RoyalInstitute of Technology, pp. 305-315.Paper DBagge, M., Hedlind, M. & Lindberg, B., 2014. Process chain basedworkpiece variation simulation for performance utilisation analysis.Submitted to: Swedish Production Symposium 2014, Göteborg, Sweden.
CI:PLM:PPAP:P-FMEA:PPM:PPP:PUR:R&D:RE:ReVer:SE:T1, T2. :TE:VW:Artificial IntelligenceAutomotive Industry Action GroupAdvanced Product QualityComputer Aided DesignComputer Aided ManufacturingComputer Aided Process PlanningCost of Poor QualityDimension Dependency ChartDimension Dependency Chart 2Design of ExperimentsDefects per Million OpportunitiesFinal DimensionFordonsstrategisk Forskning och InnovationIntegrated Computer Aided ManufacturingIntegration DEFfinitionIn Process WorkpieceKey Performance IndexNumerical ControlOperation ElementOriginal Equipment ManufacturerProcess Capability IndexProduct Lifecycle ManagementProduction Part Approval ProcessProcess Failure Mode and Effects AnalysisParts Per MillionProcess Planning ProcessPerformance Utilisation RatioResearch and DevelopmentRandom ErrorRealistic VerificationSystematic ErrorTool number 1, 2 et ceteraTotal ErrorVirtual Workshop
XIContentsList of publications.VIIAbbreviations.IX1 Introduction . 11.1 Process planning for manufacturing . 11.2 Structure of the thesis . 42 Frame of reference . 52.1 PPP - the process planning process . 52.2 Process capability – a boundary condition for process planning . 72.3 Conceptions of process characterisation . 82.4 The beam balance . 82.5 The beam balance versus process capability . 92.6 Transmission part manufacturing . 122.6.1 The transmission parts . 122.6.2 The workshop . 122.6.3 The process planning . 133 Problems to solve and research objectives . 153.1 Industrial problem to solve . 153.2 Related process planning research . 163.3 Research objectives . 203.4 Delimitations . 204 Research approach . 214.1 R&D of systematic process planning methods . 214.2 Positioning of appended publications . 24
XII5 Performed research and synthesis of results . 255.1 Schematic process planning . 265.1.1 An approach for systematic process planning of geartransmission parts . 275.2 Capture of process behaviour . 285.2.1 Paper A: Process modelling using upstream analysis ofmanufacturing sequences. 305.2.2 Paper B: Analysis of process parameters during pressquenching of bevel gear parts . 335.2.3 Multivariate data analysis . 385.3 Tolerance synthesis and analysis . 395.3.1 Paper C: Tolerance chain design and analysis of in-processworkpiece . 415.3.2 Paper D: Process chain based workpiece variation simulationfor performance utilisation analysis . 445.4 Synthesis of results . 495.4.1 Information flows . 495.4.2 Refining the PPP with information flows . 526 Discussion and conclusions . 556.1 Coverage of the research results . 556.2 Follow-up of research objective 1 . 566.3 Follow-up of research objective 2 . 586.4 The relation between the PPP and PPAP . 586.5 Process capability index . 596.6 Relevance of the chosen problems to solve . 616.7 Scientific contribution . 62
XIII6.8 General application of the research results . 626.9 Conclusions . 637 Future work. 657.1 Economic aspects . 657.2 Representation of the PPP and information flows . 657.3 The model driven approach . 667.4 A new approach for P-FMEA . 668 References . 67
11 Introduction1.1 Process planning for manufacturingProcess planning for manufacturing covers a wide range of activitiesneeded to specify the manufacturing process for a part. Unfortunately,the process planning terminology “is somewhat fuzzy” (Anderberg, 2012)and there is no commonly adopted or standardised definition of what isincluded or not, nor for the activities whatever they may be.Marri, et al. (1998) gives a definition that seems to be applicable inmost cases where process planning is considered:“Process planning is defined as the activity of deciding whichmanufacturing processes and machines should be used to perform thevarious operations necessary to produce a component, and the sequencethat the processes should follow.”A more comprehensive definition of the aim of process planning formanufacturing is that by ElMaraghy and Nassehi (2013):“Process planning, in the manufacturing context, is the determinationof processes and resources needed for completing any of themanufacturing processes required for converting raw materials into afinal product to satisfy the design requirements and intent and respectthe geometric and technological constraints.”An important addition to these constraints is that the manufacturingmust be cost-effective for a business to be successful. This is realised by awell-running manufacturing process in addition to efficient processplanning to meet agreed deadlines (Scallan, 2003). The integration ofmanufacturing cost is essential and has been discussed by many authors(Gupta, et al., 2011; Xu, et al., 2009; Mayer & Nusswald, 2001).Process planning is also described to be the interface between productdesign and manufacturing (Scallan, 2003) and the work often includescoordination of product design
Manufacturing Engineering and Technologies. Stockholm: KTH Royal Institute of Technology, pp. 305-315. Paper D Bagge, M., Hedlind, M. & Lindberg, B., 2014. Process chain based workpiece variation simulation for performance utilisation analysis. Submitted to: Swedish Production Symposium 2014, Göteborg, Sweden. IX Abbreviations AI: Artificial Intelligence AIAG: Automotive Industry Action Group .